In the plastic industry, color masterbatch plays a vital role in defining product aesthetics, brand identity, and surface appeal. To ensure precise, stable, and process-friendly coloration, the production process of color masterbatch must adhere to rigorous technical standards.
So how exactly is color masterbatch manufactured? Let’s explore each stage in detail below.
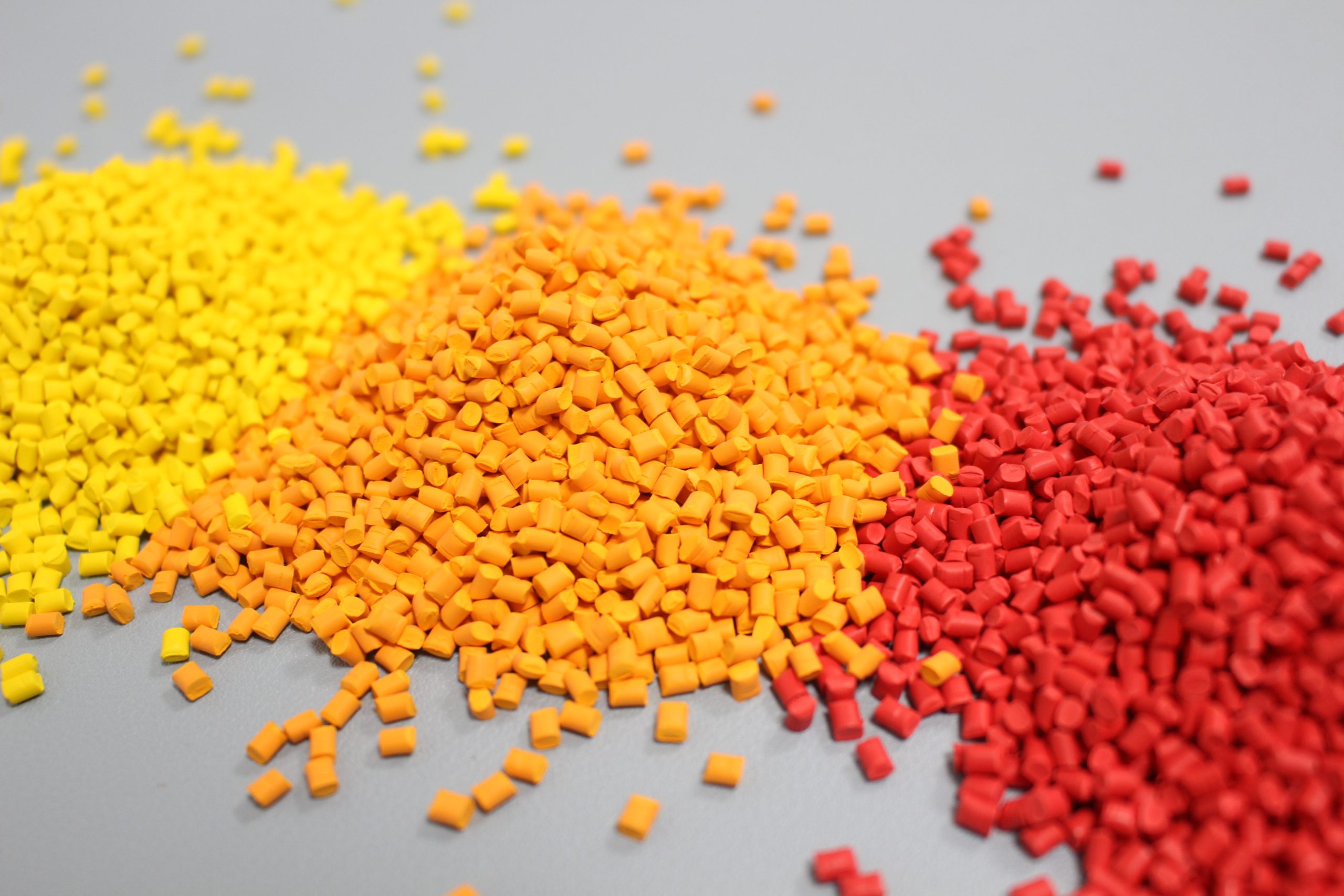
How exactly is color masterbatch manufactured?
1. Raw material selection
The first step in producing color masterbatch is selecting the right ingredients. The main components include:
- Pigments or dyes: These may be inorganic (e.g., oxides, carbon black, titanium dioxide) or organic (e.g., azo, phthalocyanine, quinacridone). The pigment must be heat-resistant, lightfast, and compatible with the base resin.
- Carrier resin: A thermoplastic polymer that matches the final product’s base resin, such as PE, PP, PS, or ABS. It ensures optimal dispersion and processing compatibility.
- Additives: Dispersants, heat stabilizers, antioxidants, or processing aids are added to enhance performance and color durability.
2. Precise weighing and premixing
Once the color formula is determined based on standard samples or customer requests, the raw materials are weighed with precision using electronic scales. Strict control of these ratios ensures consistency in color output across production batches.
Next, materials are fed into a high-speed mixer for dry blending. This helps the pigment particles distribute evenly throughout the carrier resin before extrusion. Some manufacturers use heated or forced mixers with temperature control to further improve dispersion and batch uniformity.
3. Melting and extrusion
The blended mixture is fed into a single or twin-screw extruder, where it is heated, mixed, and melted into a homogeneous compound.
Key parameters to control include:
- Proper temperature suited to both pigment and resin type
- Screw speed ensuring fine dispersion without pigment degradation
- Stable pressure and flow throughout the process
4. Pelletizing and cooling
After exiting the extruder, the molten compound passes through a cooling system—either water or air—to quickly lower its temperature to a safe level for pelletizing.
The cooled strand is then cut into uniform color masterbatch pellets using a high-speed cutting system. Depending on application, manufacturers may adjust pellet shape and size to meet specific equipment or processing requirements, such as cylindrical pellets, flat shapes, or micro-pellets.
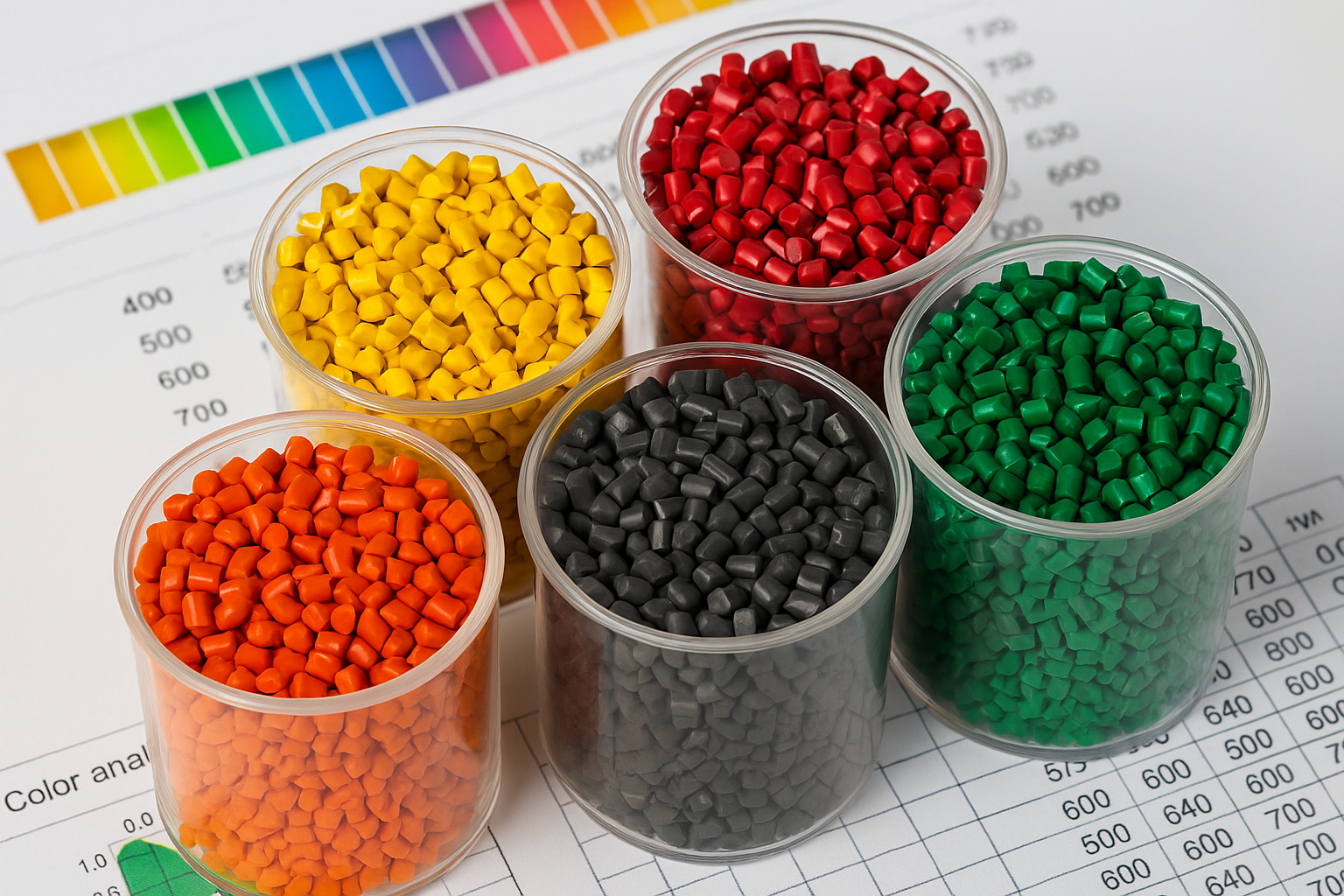
In the plastic industry, color masterbatch plays a vital role
5. Drying and packaging
The pellets are dried to remove residual moisture, preventing quality issues during further processing.
Products are then quality-checked based on criteria such as:
- Dispersion quality
- Color accuracy (measured with a spectrophotometer)
- Pellet shape and size
Finally, the color masterbatch is packed in PE bags or multi-layer moisture-resistant sacks and stored under controlled conditions.
6. Color matching and custom formulation
Besides standard formulations, manufacturers offer custom color matching based on customer samples. Color technicians use spectrophotometers and color matching software to create tailored formulas and produce test samples to verify Delta E (color deviation) remains within acceptable limits.
Regular color checks ensure consistency across all batches delivered to clients.
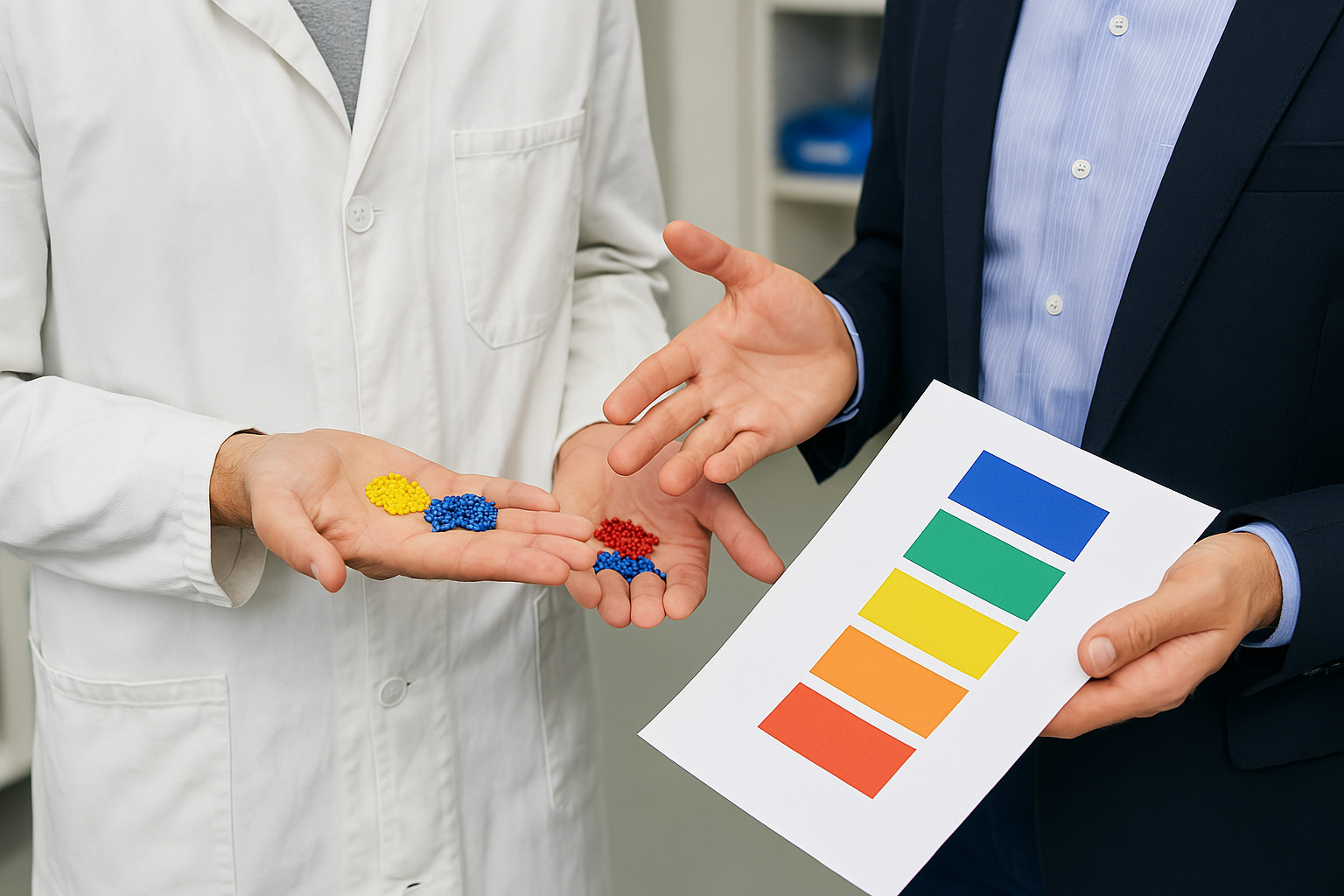
Besides standard formulations, manufacturers offer custom color matching based on customer samples.
7. Conclusion
Color masterbatch is a high-precision material that requires tight control from raw material selection and mixing to pelletizing and quality assurance. Each step is critical to achieving uniform, durable, and compatible coloration for plastic applications.
Understanding how color masterbatch is produced empowers plastic manufacturers to choose the right supplier and optimize production efficiency and end-product quality.
8. About EuroPlas
EuroPlas is one of the world’s leading masterbatch manufacturers, operating seven factories in Vietnam and Egypt with a total capacity of 800,000 tons per year, distributing to more than 95 countries.
EuroPlas’ color masterbatch line is developed using advanced color-matching technology and premium pigments tailored to customer needs. Our solutions deliver precise color performance, excellent dispersion, high heat and light stability, environmental friendliness, and a wide range of customizable shades.
Explore more at the EuroPlas Blog or get in touch via our Contact Page.