Plastic is one of the most common and useful materials used all over the world. Around 300 million tons of plastic are produced on Earth per year, and it's crucial to extend its lifespan as long as possible. And one of the ways to do so is recycling.
So, how is plastic recycled? Let's find out!
1. Why Should We Recycle Plastic?
Plastic is a popular, versatile material. The more we reuse and recycle it, the less demand for creating a new one will be. It means recycling can help us:
- Reduce energy and fossil fuel consumption as recycling uses less energy and fossil fuel than producing new.
- Reduce CO2 and other greenhouse gas emissions and the air pollution resulting from waste burning.
- Reduce the need for extracting new and raw materials from the Earth, thus, saving natural resources, eliminating heat-trapping gasses' emissions, and decreasing rubbish.
- Reduce the landfills used for producing new plastic.
- Acknowledge and promote a sustainable lifestyle. Knowing the process of plastic recycling will help us change our habit of overconsumption to contribute to a healthy environment.
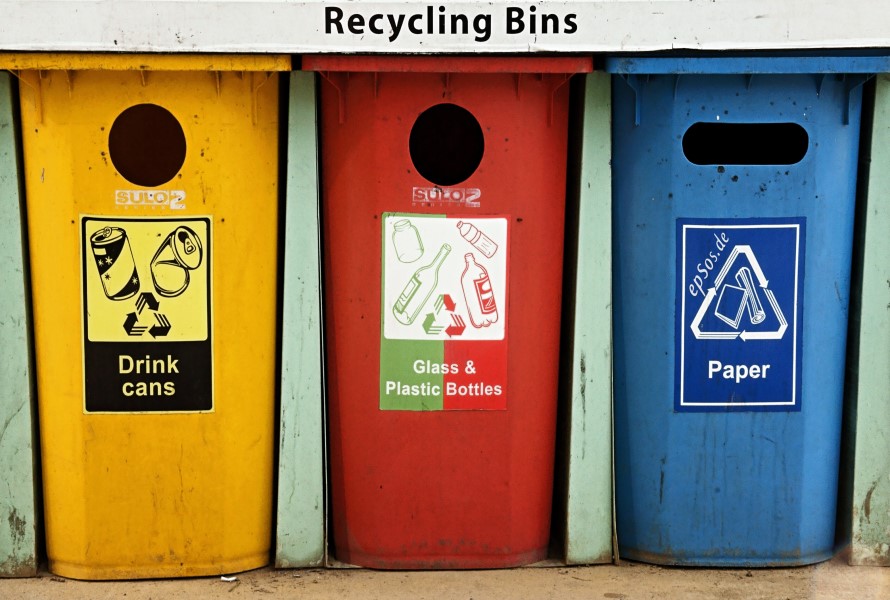
2. How Is Plastic Recycled?
The process can be summarized into two stages:
- First, the plastic is sorted by polymer type. Automatic and manual methods are both applied to ensure no contaminants are left.
- After sorting and cleaning, the next step will be: shredding into flakes or melting to form pellets, depending on the technology and purpose of using recycled plastic. Then, it will be molded into new products.
Recycled plastic can be used in various industries, such as:
- Automobiles: For example, bumpers and wheel arch liners.
- Construction: For instance, reusable crates and pallets, damp-proof membranes, etc.
- Gardening: seed trays, flower pots, watering butts, water cans, etc.
- Clothing: polyester fabric for clothing
- Others: food trays, drink bottles, refuse sacks and carrier bags, etc.
3. Which Plastic Can Be Recycled?
The process of plastic recycling can be applied to a list of plastics below:
3.1. PET
PET, or Polyethylene Terephthalate, is the most widely recycled plastic in the world. In general, PET bottles are quite easy to recycle. It's mixed between the virgin and the recycled version to strengthen the product and form a new PET bottle again.
You may be surprised that most PET plastic is recycled into clothes and textile garments—some of your fashion items, such as T-shirts, carpets, and backpacks. The process of plastic recycling includes turning PET into flakes, then spinning it as a yarn.
Another amazing application of recycled PET is to fill plastic bottles with sand, stack them and add cement or mud to become a wall for houses. It's mostly seen in third-world countries.
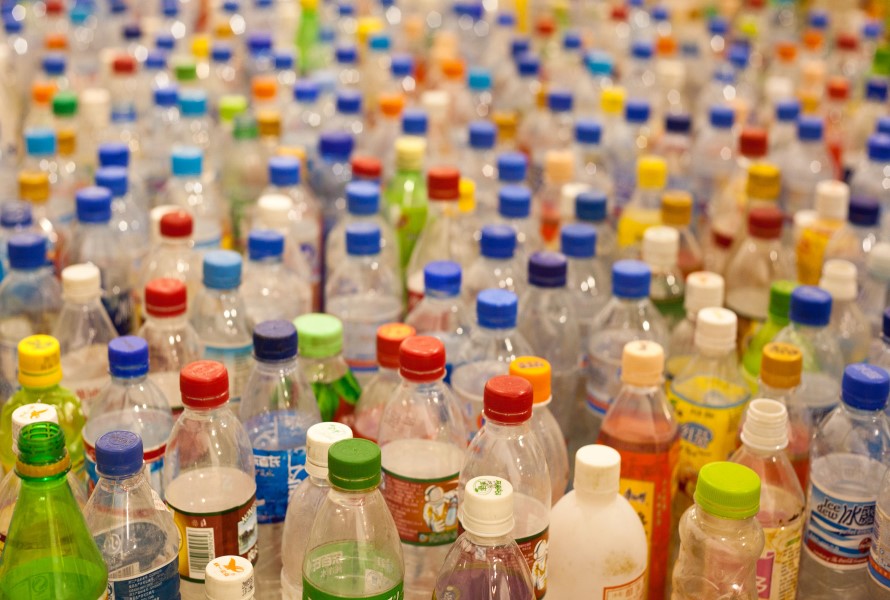
3.2. HDPE
According to most recycling centers in the world, HDPE is one of the easiest plastic polymers to recycle. You can find both transparent and colored HDPE.
The post-consumer recycled natural HDPE is usually used in non-food application bottles, including bottles for household cleaners, detergent, motor oil, and also fil packaging. Meanwhile, some other non-food application bottles, lawn products, or pipes are made from pigmented HDPE post-consumer recycled resin.
Downcycling is also applicable for HDPE (recycling it to become material for lower-value products. This kind of market includes plastic lumber, benches, tables, and road curbs.
3.3. PVC
PVC or polyvinyl chloride can actually be recycled. However, the process is harder compared to other plastics. You should consult with local authorities for the information.
3.4. LDPE
LDPE, also known as low-density polyethylene, is the material for the infamous plastic bags, including those you usually find in grocery stores and other retailers. LDPE is recyclable, yet it does not mean you can always do so. For example, plastic bags are easy to get stuck inside the recycling machine, creating danger while processing.
This material is also cheap and low-quality; thus, recycling is not really worth it (in terms of financial cost). However, if LDPE is recycled, it can be used as packaging films or bin liners.
3.5. PP
PP or Polypropylene is a good plastic and is one of the most popular plastic packaging materials in the world. Once you throw the plastic away, it will degrade slowly, and the complete decomposition may take around 20 to 30 years, meaning after-using PP may take lots of landfill.
Despite this fact, recycling PP is not easy and expensive. It's also difficult to eliminate the smell of what was contained inside the plastic before. Plus, after recycling, the product is usually gray or black, which can not be used in packaging. That's why Polypropylene is more widely included in speed bumps, auto parts, park benches, plastic lumbers, and other industrial applications.
3.6. PS
PS, Polystyrene or Styrofoam is a common material for packing foam (or peanuts), disposable plastic cutlery, and coffee cups. However, if you can't reuse it, you'd better avoid it as the plastic is hard and can not be recycled.
3.7. Others
This category refers to a blend of various plastic types. Since it's a mixed product, it's difficult for recycling companies to separate, making recycling impossible.
4. Eco-friendly Products from EuroPlas - Build Your Green World
As a professional in the masterbatch industry, EuroPlas understands the demand for biodegradable plastic for sustainable development and the environment. Therefore, we've developed Bioplastic Compound and Bio Filler.
BioNEXT is a bio compound that can be decomposable within a year after use. Our products are environment-friendly and possess many outstanding features. We've made it through strict quality control management to meet all the requirements.
Here is the list of
Bioplastic Compound from EuroPlas:
Product |
Outstanding features |
BiONext 102 - a bio-compound made of bioplastic and CaCO3 |
- Biodegradable within 12 months after use
- Full functions in one material
- High stiffness
- Low melt flow index
- High impact strength
- Easy for processing
|
BiONext 152 - a bio-compound made of bioplastic and CaCO3 |
- Biodegradable within 12 months after use
- Full functions in one material
- High stiffness
- High impact strength
- Great gloss
- Easy for processing
|
BiONext 400 - a bio-compound based on bioplastic and modified starch powder |
- Biodegradable within 12 months after use
- Full functions in one material
- Keep moisture on the surface, resulting in longer food preservation
|
BiONext 500 - a bio-compound based on bioplastic and reinforced CaCO3 powder |
- Biodegradable within 12 months after use
- Full functions in one material
- High stiffness
- Good elongation
- Easy for processing
- Great dispersion
|
BiONext 600 - a bio-compound based on bioplastic, talc and other specific additives |
- Biodegradable within 12 months after use
- Full functions in one material
- Anti UV, oxidation, and moisture
|
BiONext 700 - a bio-compound based on bioplastic and specific plasticizers |
- Biodegradable within 12 months after use
- Full functions in one material
- Prevent oxidation, thus resulting in longer food preservation
|
Bio Filler from EuroPlas is a cost-effective material solution for bioplastic products. It's a biodegradable material that improves several properties of end-products, such as stiffness, gloss, etc. It can act as an anti-block and slipping agent in blown film.
List of Bio Fillers from EuroPlas:
Products |
Description |
Outstanding Features |
BiOMates 01 |
A mixture of bio resin, modified CaCO3 and dispersion additives. |
- Optimize cost for bioplastic end-products processing
- Biodegradability
- Play as anti-blocking and slipping agent for PBAT films
|
BiOMates 02 |
A blend of bio resin, modified BaSO4 and dispersion additives. |
- Optimize cost when mixing with several types of bio resins, such as: PBAT, PBAT compound, PBAT & PLA blend
- Increase the film glossiness
- Films are more transparent than when using CaCO3
|
BiOMates 03 |
A combination of bio resin, modified talc and dispersion additives. |
- Optimize cost for bioplastic end-products processing
- Increase the stiffness for films
Films are more transparent than when using CaCO3
- Play as anti-blocking and slipping agent for PBAT films
- Technical specifications
|