Metallic masterbatches are transforming the automotive industry in a more advanced and sustainable way. They offer the perfect combination of style, durability, and performance for a wide range of vehicle applications. From enhancing the aesthetics of a vehicle with a premium metallic finish to reducing weight for better fuel economy, this innovative material is a game changer in the industry’s evolution. Understanding the benefits and trends of metallic masterbatches in the automotive industry can go a long way in optimizing the cost of your next project. Let’s explore right away!
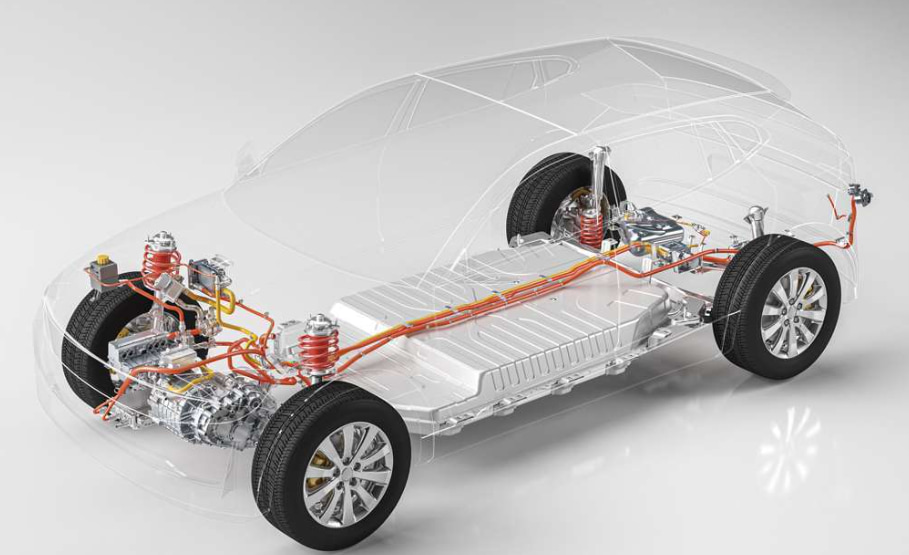
Metallic masterbatch in plastic compounds can be used in various important car parts
1. Benefits of Metallic Masterbatch in Automotive Applications
Metallic masterbatch is popular in many automotive applications due to their excellent benefits. Understanding the typical benefits of metallic masterbatches will help lay the foundation for the success of your upcoming project. Here are some benefits that cannot be missed:
1.1. Enhanced Aesthetic Appeal
Metallic masterbatch is commonly used in automotive applications to achieve a premium finish for a car. The material shines with a special metallic luster, giving the interior and exterior an elegant, high-end appearance.
Moreover, aesthetic improvement is essential for creating stunning car interiors and exteriors, as almost all manufacturers pursue a sleek and contemporary design. The metallic effect in the masterbatch lends a sort of depth to it as well as a richness that is not achievable with traditional colorants.
One illustration is many expensive cars that have clear coat painted pieces on the dashboard, door parts, or the gear panel with a shiny finish, which brings in a vibe of luxury without using metal compositions.
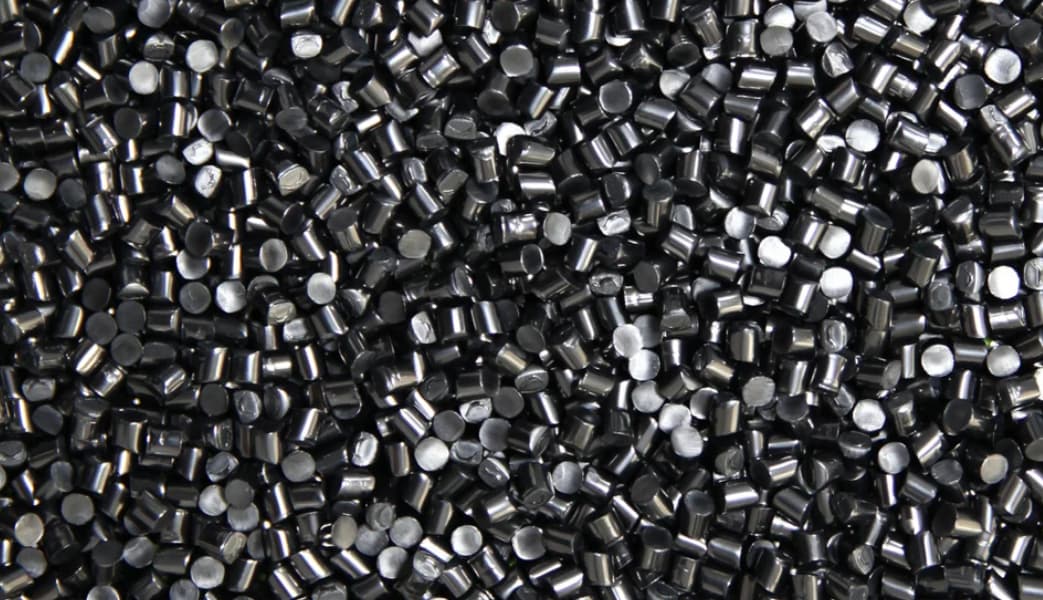
Metallic masterbatch is commonly used in automotive applications to achieve a premium finish for a car
1.2. Cost-Effective Alternative to Metal Parts
Metallic masterbatch can be used with significantly less virgin metal powder to produce nearly metal-free parts. This technique helps manufacturers operate smoother processes, saving a large amount of cost. For example, vent covers with metallic masterbatch reduced aluminium oxide to nanosize which gets the products to the list of the green materials.
The particular advantage is that these are cost-saving measures which metallic masterbatch offers to the manufacturer worldwide. The metallic masterbatch of plastic parts can replace their metal counterparts in automobile interiors. Metallic masterbatch in plastic compounds can be used in various important car parts, such as knobs, vent covers, and decorative trims, while retaining the metallic look needed for automotive design.
By using metallic masterbatch, the aluminum appearance of a plastic component one can create the identical impression as of a component made from actual aluminum.
1.3. Lightweight Design for Fuel Efficiency
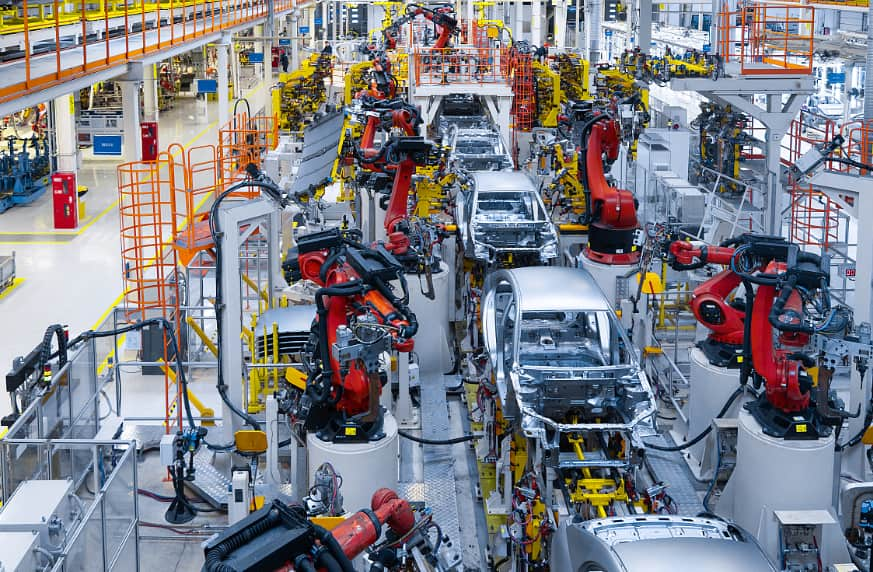
Replacing metal parts with metallic masterbatch in plastic components will offer better fuel economy
Among all other challenges facing the automotive industry today, reducing vehicle weight for the improvement of fuel efficiency and minimization of emissions becomes one of the most important. Metallic masterbatch enables manufacturers to achieve a metallic look while keeping components lightweight, as plastic is much lighter than metal.
A lighter vehicle consumes a lesser amount of energy for movement, particularly for EVs that monitor battery efficiency. Replacing metal parts with metallic masterbatch in plastic components will offer better fuel economy and maneuverability to the carmakers.
For example, metallic plastic door handles and mirror housings can help reduce overall vehicle weight without compromising appearance.
1.4. Endurance and Resilience Towards Weather Conditions
As outdoor materials, automotive components must endure critical parameters of environmental conditions that include UV exposure, temperature fluctuations, and moisture. Metallic masterbatch formulations are designed to augment the durability of plastic parts so that they can meet requirements of harsh weather while most people do not even know they are plastic.
The importance of durability is for all exterior applications such as bumpers, grilles, and even side molding applications where they're constantly exposed to the outer environment. The ultimate metallic masterbatch formulation has UV stabilizers and weather resistance additives that will prevent fading, cracking, or surface degradation.
For instance, a bumper made of metallic masterbatch that resembles a metallic finish keeps shining and has integrity even at sun exposure and temperature changes after hundreds of years.
1.5. Brand Differentiation
Metallic masterbatch gives automakers the ability to create unique designs that embody their brands and differentiate their vehicles from the competition. By varying the pigment concentration and formulation, manufacturers create different metallic effects ranging from subtle shimmer to deep mirror-like gloss.
This customization level is necessary for brand identity and customer appeal. Manufacturers of luxury vehicles, for example, often use exclusive interior metallic color schemes that enhance a premium image.
An excellent example is the application of bronze or gunmetal metallic plastic trims in sports cars, which elevate the dynamic and high-performance appeal while being cost-effective.
1.6. Enhanced Efficiency in Production
With the incorporation of metallic masterbatch into plastic parts, it reduces the need of post-processing like painting or electroplating as its virgin metallic applies. There will be no necessity of any coating outside, resulting in saving of time and labor costs.
This is a very important process in high-volume automotive production, where speed and consistency determine the end product. Moreover, there is no risk of cases such as paint chipping from surfaces that have metallic effects.
Like injection-molded dashboard panels, which contain built-in metallic pigments that are ready for installation as they come out of the mold.
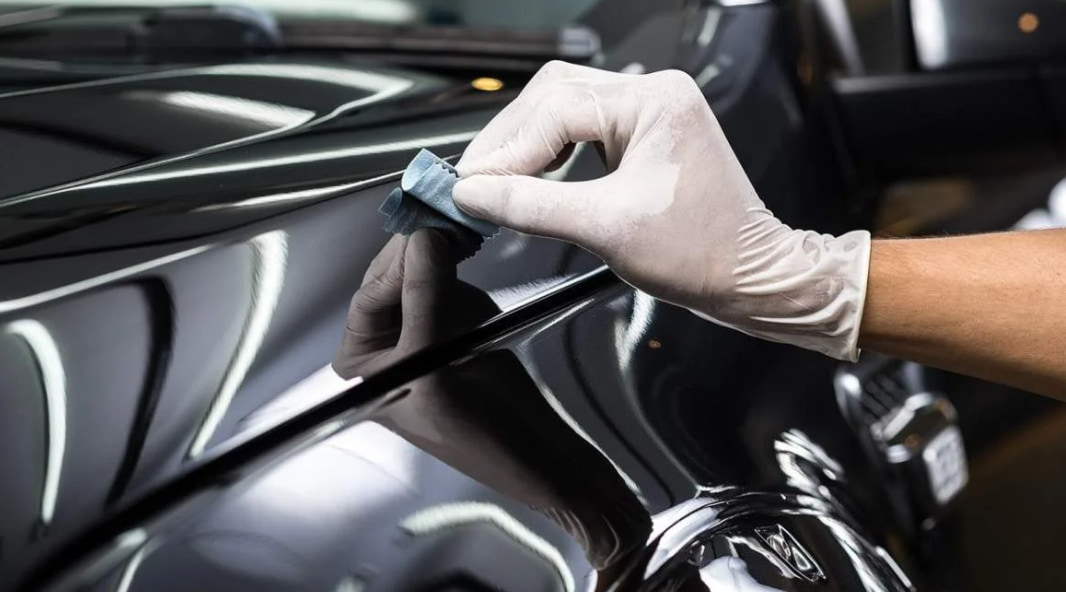
Metallic masterbatch reduces the need of post-processing like painting or electroplating as its virgin metallic applies
1.7. Sustainability
Sustainability is a main concern of almost all stakeholders of the automotive sector. Here, they must consider that metallic masterbatch contributes towards the environment by manufacturing waste minimisation and reduction in energy consumption. As production of plastic products involves the direct incorporation of metallic masterbatch into it, environmental hazards of chrome plating and spray painting can be eliminated altogether.
Many formulations of metallic masterbatch are suitable for integration with recycled plastics in the same process. That is to ensure compatibility with recyclability. Thus, the metallic-finished recyclable plastic components make lesser environmental effects on all environmental aspects but still maintain high aesthetics from a quality standpoint.
For example, metallic plastic produced from recycled polypropylene can add to the sustainability of the vehicle in the future without compromising design aesthetic functions.
1.8. Enhanced resiliency
Automotive components frequently require contact with interchanges and can take a lot of wear and tear. Metallic masterbatch can make scratches and abrasions on plastic parts much less damaging in appearance which helps to keep the appearance intact over the years.
Metallic masterbatch makes the surface harder and imparts properties that help prevent minor scratches and scuffs to the parts. Important applications to this feature would be the high-contact areas like center consoles, door handles, and trims on steering wheels exposed to everyday use.
For example, the plastic center console coated with metallic paint would not be so visible even after years of tussle with keys, mobile phones, and others.
2. Current Trends in Metallic Masterbatch for Automotive Industry
2.1. Sustainable and Eco-Friendly Metallic Masterbatch
As sustainable standards become paramount in the automotive industry, an increasing number of manufacturers are switching toward environmentally friendly solutions. Some of them are biodegradable materials, recycled plastics, and non-toxic metallic masterbatch. The express intention is to achieve further reduction of any negative environmental impact while achieving the utmost quality aesthetics.
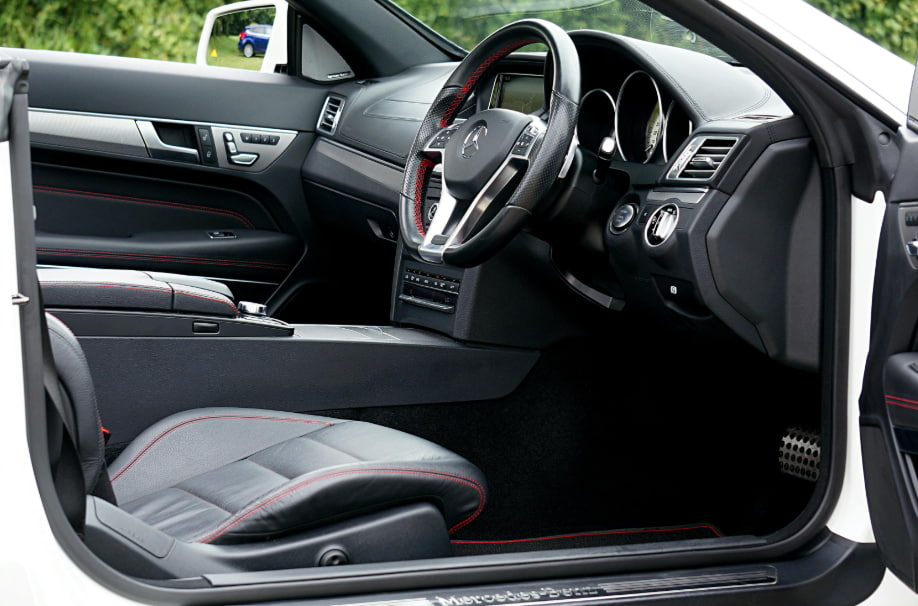
Sustainable metallic masterbatch becomes part of the green manufacturing initiative
This is amongst the core and long-term trends in the automotive industry. Pressures on the automobile manufacturers to cut carbon emissions are increasing, along with adoption of stringent environmental policies. Sustainable metallic masterbatch becomes part of the green manufacturing initiative for the brands to appeal to their environmentally conscious customers. Some of the important benefits of this trend are:
Environmentally-friendly: The use of recycled and bio-based plastics contribute to the reduction of plastic waste.
Low VOC emissions: Due to metal masterbatches, the alternative of solvent-based coatings as finishes was totally avoided.
Regulatory compliance: Stricter legislation on plastic waste and emissions are coming into effect in many countries, thus making sustainable materials a valid necessity.
Some recycled plastic formulations play as a carrier resin, so that metal-finished automotive components become both fashionable and environmentally friendly. The automakers' goal is also to use bio-based polymers as an alternative to fossil fuel reliance. Some luxury brands are beginning to use recycled polypropylene (PP) or ABS for metal-finished interior trim, adding an appeal and supporting their own sustainability goals.
2.2. High-Performance Metallic Masterbatch for Electric Vehicles (EVs)
With rapid development in the electric vehicle (EV) markets, metallic masterbatch solutions are in high demand. High-performance metallic masterbatch has been developed so that it also meets requirements specific to the interiors and exteriors of electric vehicles.
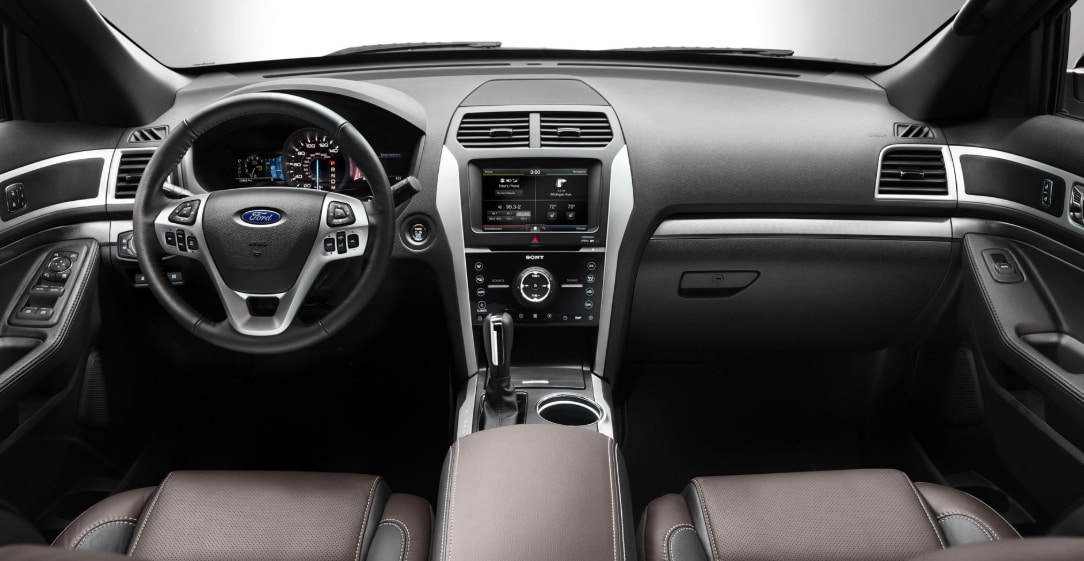
Metallic masterbatch offers excellent alternatives to metal parts and saves weight on the vehicle
This is being considered a very lucrative trend from a cost point of view. Electric vehicles are being promoted as a green development trend with futuristic design and high-tech interiors; therefore, metallic masterbatch finishes are also becoming an ever-attractive option. This is basically because metallic masterbatch offers excellent alternatives to metal parts and saves weight on the vehicle. For its lightweight properties, it can provide various advantages for electric vehicles, such as smooth maneuvering, energy and cost savings. Below are some of the other advantages of this material:
Improved aesthetics: Metallic finishes give a sleek, contemporary appearance, elevated with the futuristic image of electric cars.
Lightweight: Reduces the burden of metal parts that would be detrimental to batteries' performance.
Thermal and electrical insulation: Some formulations of metallic masterbatch are specifically made to minimize the heat within the electronic components.
EV manufacturers are utilizing metallic masterbatch plastic components in dashboards, panels, and external trims to create a clean, high-tech design. Some metallic masterbatch formulations also exhibit improved heat dissipation critical for EV battery cases and electronics enclosures.
3. Conclusion
Metallic masterbatch is the solution for making a perfect balance between aesthetics and functionality, cost-effectiveness, and much more in the automobile sector. It would create extremely high-end metallic finishes without the weight and cost of real metal. It creates the perfect fusion from enhancing the visual appeal, durability, fuel efficiency, and sustainability of the vehicle.
The market trends prevailing today, like eco-friendly formulations and high-performance solutions for electric vehicles, reflect how the automotive industry is progressing with sustainability. Metallic masterbatch will be soon employed as an advanced functional additive in the near future. Whether for traditional cars or electric ones, this material is going to be part of the generation of cars still to come.
4. About EuroPlas’ Grey Masterbatch
EuroPlas is proud to be a world-leading filler masterbatch supplier with many years of experience. We bring high-quality products manufactured through the most advanced techniques and machinery. EuroPlas's color masterbatch is meticulously designed to achieve the most accurate properties in plastic products.
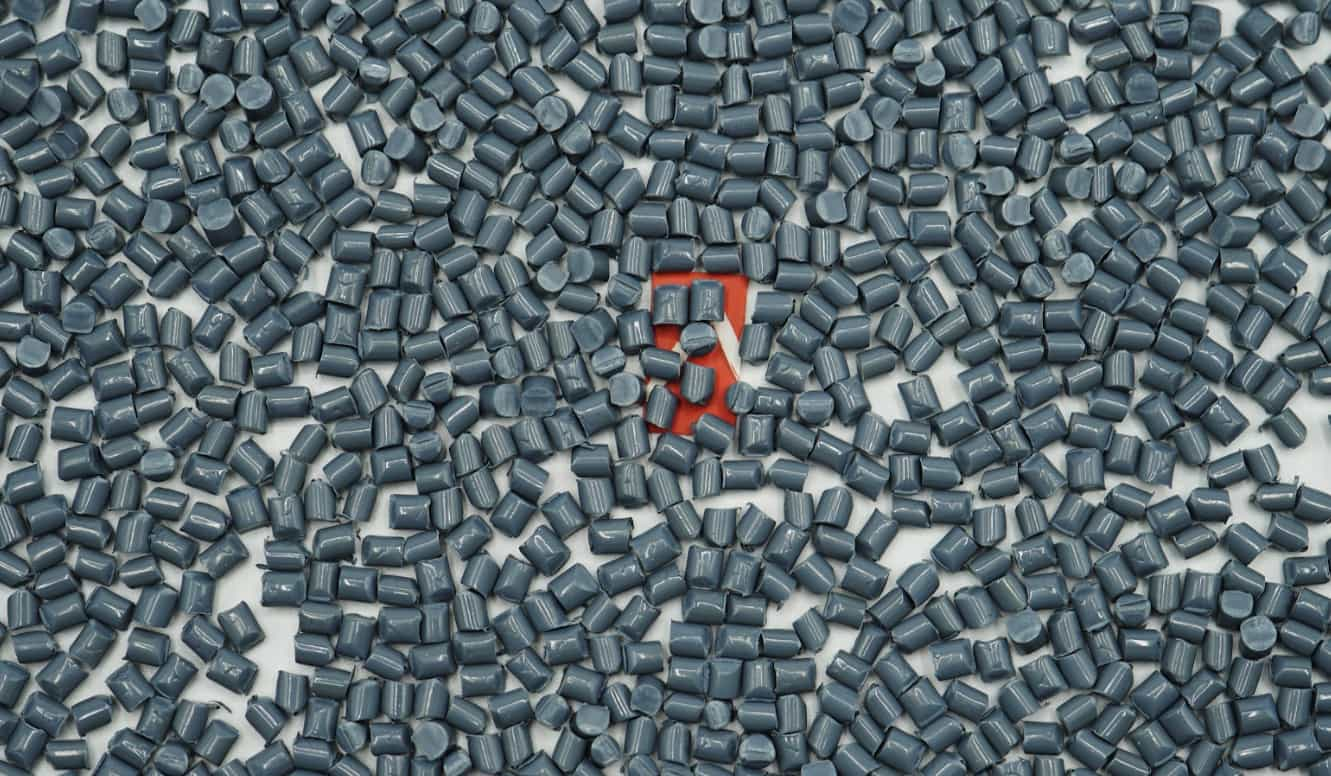
EuroPlas's grey masterbatch is one of impressive materials
Among them, EuroPlas's grey masterbatch is one of impressive materials. This color masterbatch adds vibrant gray color and advanced properties according to the additives to the initial raw material. Our grey masterbatch has excellent dispersibility, high heat resistance, and perfect color fastness. This material helps manufacturers create end products with desired colors, characteristics, and mechanical strength at the lowest cost.
We commit to offer grey masterbatch with various tones and properties suitable to customers' production requirements. Our technical staff will consult and help you customize a masterbatch that adds an even, rigid gray color for the products. Contact us now!