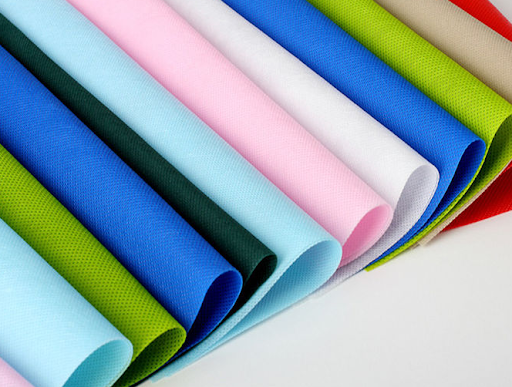
Nonwoven fabric has been contributing greatly to various industries from medical, health care, agriculture, etc.
Nonwoven fabric is considered one of the most flexible and extremely creative materials. Unlike traditional fabrics, they are produced without weaving or knitting. Nonwoven fabric has been contributing greatly to various industries from medical, health care, agriculture, etc. Depending on the different types of nonwoven fabric, it will have its own properties and advantages. Immediately update the following 8 typical types of nonwoven fabric to better understand their applications and great benefits.
1. Overview Of Nonwoven Fabric
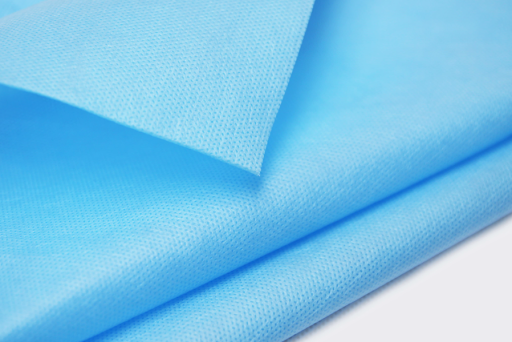
Nonwoven fabric is made by linking fabric fibers by wrapping, pressing or binding with a special needle instead of knitting or weaving
Nonwoven fabric is a quite unique fabric in structure and properties. Nonwoven fabric is made by linking fabric fibers by wrapping, pressing or binding with a special needle instead of knitting or weaving. Strengthening the network bonds between fabric fibers can be done mechanically (through needle punching), chemically (using adhesives) or thermally (using heat). They possess countless great advantages such as light weight, softness, sturdiness, good water resistance and are extremely breathable. Nonwoven fabric can be produced quickly in large quantities at a very reasonable cost.
2. Eight Types Of Nonwoven Fabric
2.1. Spunlace nonwovens
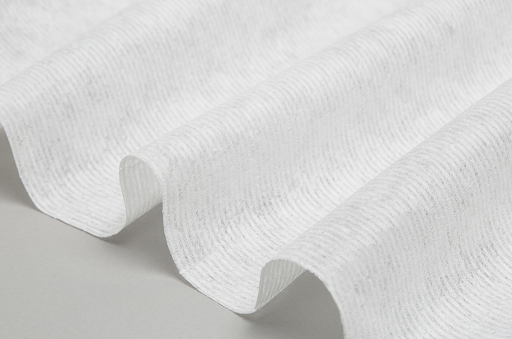
Spunlace nonwoven fabric possesses softness and drape, so it is very suitable for applications that require smoothness
Spunlace nonwoven fabric is one of the most popular fabrics today. They are produced by winding loose fabric fibers together through high-pressure water jets. The basic steps to produce spunlace nonwoven fabric can be summarized as follows:
-
Arrange fiber network: Arrange a fiber network on the conveyor belt.
- Start the water jet system: High pressure water jets are directly sprayed into the fiber network, causing them to intertwine and bond into fabric.
- Drying:The drying system will be started to remove remaining moisture on the fabric.
Spunlace nonwoven fabric possesses softness and drape, so it is very suitable for applications that require smoothness. In addition, this type of nonwoven fabric also possesses good tensile strength, high absorbency and flexibility in production. Some typical applications of spunlace nonwoven fabric include industrial wipes, baby towels, surgical gowns, wound dressings, diapers, and some air and liquid filters.
2.2. Heat-bonded nonwoven fabric
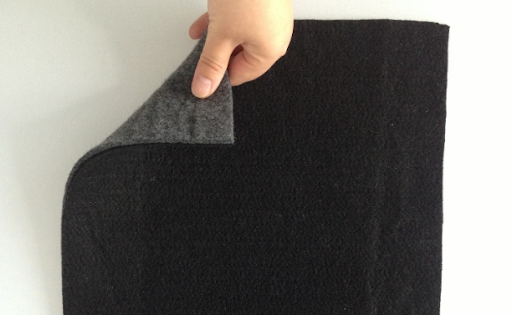
Heat-bonded nonwoven fabric is one of the very durable materials suitable for many different applications
Heat-bonded nonwoven fabric is also one of the ideal choices in production. Heat-bonded nonwoven fabric is created in the form of bonding fabric fibers together using heat and pressure without weaving or knitting. The production process of this nonwoven fabric is described with the following basic steps:
-
Fiber network arrangement: The fibers are arranged in a mesh or mat form.
- Heat-bonded: The fiber web is passed through heated rollers or presses. High temperatures melt the fabric fibers, causing them to stick together into fabric.
- Cooling: After cooling, the fabric will cool down and solidify into a strong, compact material.
Heat-bonded nonwoven fabric is one of the very durable materials suitable for many different applications. They provide an even texture throughout the fabric. Fabric properties can be adjusted by varying temperature, pressure and bonding time. Some common applications of nonwoven fabric include sound/heat insulation in cars, disposable protective clothing and some roofing and insulation applications in the home. In particular, they can also be used as geotextiles to help stabilize soil and prevent erosion.
2.3. Pulp air-laid nonwovens
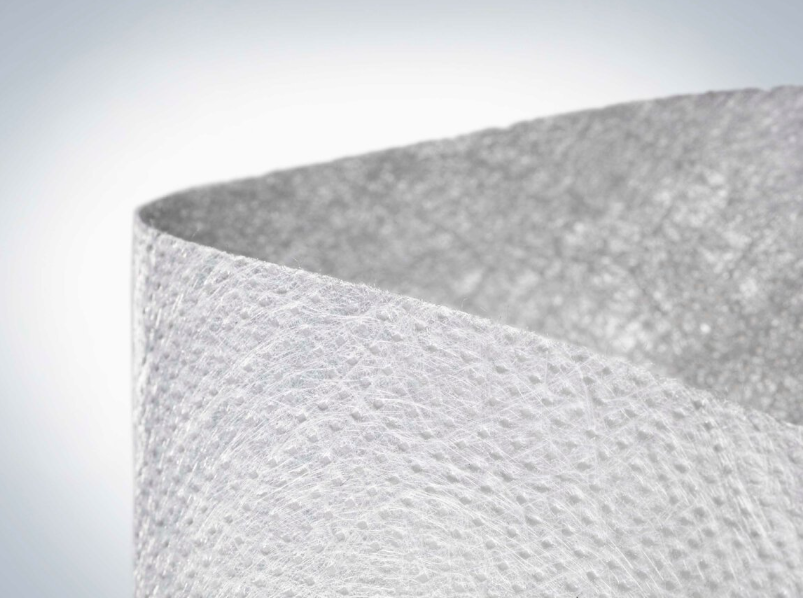
Pulp air-laid nonwoven fabric is often biodegradable and environmentally friendly
Pulp air-laid nonwoven fabric is also known as air-laid paper or pulp fabric. They are bonded from cellulose fibers derived from wood pulp. This process includes the following steps:
-
Preparation of pulp: Wood pulp is mixed with water to form a thick mixture.
- Hanging the yarn: The mixture is pumped into the air spreader. Here, air is used to transport and evenly distribute the fibers into a network.
- Bonding: The fiber mats are then dried and or bonded with adhesives to create the finished fabric.
- Product finishing: Fabric can be laminated (pressed) to improve texture and appearance.
With its softness and high absorbency, pulp air-laid nonwoven fabric is well suited for applications requiring a gentle touch and good moisture balance. They often have a thicker texture than other nonwoven fabrics, making them suitable for cushioning or support applications. In particular, this type of fabric is often biodegradable and environmentally friendly. Some applications of this type of nonwoven fabric include disposable diapers, feminine hygiene products, wipes and some medical and health care products that require absorbency and softness.
2.4. Wet-laid nonwovens
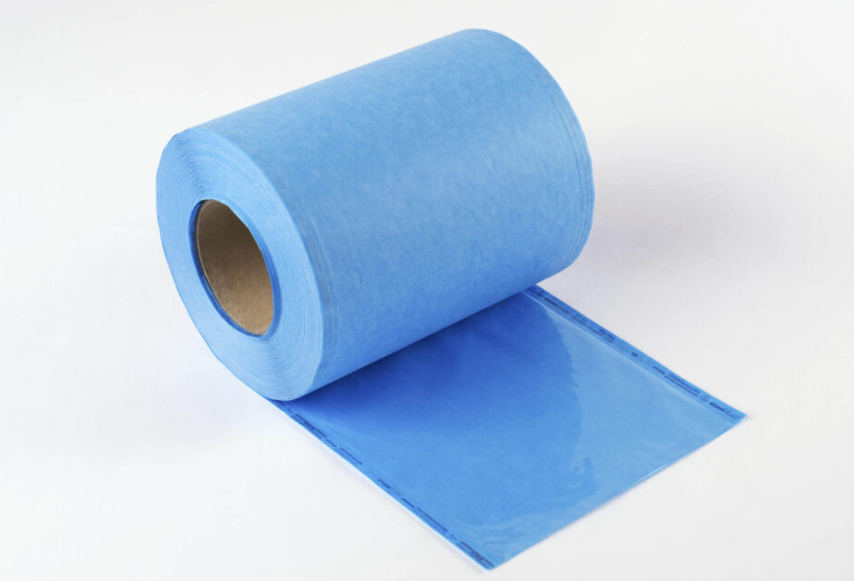
Wet-laid nonwoven fabric possesses a consistent and uniform fabric structure, similar to paper
Wet-laid nonwoven fabric is a type of nonwoven material produced using a process similar to traditional papermaking. The process description is as follows:
-
Fiber preparation: These fibers are usually cellulose from wood pulp or synthetic fibers. They will be mixed with water to form a paste.
- Fiber formation: The mixture is poured and evenly distributed on the conveyor belt. At this step, water is drained out and separated from the fiber network.
- Pressing and drying: Wet fabrics are pressed to remove excess water and strengthen the fabric structure. They are then dried using heated rollers or some other drying method.
- Finishing: Fabrics may undergo additional processes such as calendering or coating to achieve final properties.
Wet-laid nonwoven fabric possesses a consistent and uniform fabric structure, similar to paper. They are very flexible in adjusting fiber type and processing conditions. Some applications of nonwoven fabric include medical drapes and wound dressings, air and liquid filtration systems, tea bags, wipes, etc.
2.5. Spunbond nonwovens

Spunbond nonwoven fabric is known for its extremely good breathability
Spunbond nonwoven fabric is a type of nonwoven material created by spinning thermoplastic fibers. They are then bonded together to form fabric. This process includes the following steps:
-
Spinning: Thermoplastic fibers are melted and extruded through a spinning machine to form fibers.
- Fiber formation: The fibers are cooled and solidified. Then, they are pulled and distributed into a grid or carpet form.
- Fiber bonding: The fiber network is then bonded using heat, pressure, or both. This process causes thermoplastic fibers to fuse together to create fabric.
- Finishing: Fabrics may undergo additional finishing processes such as calendering (pressing) to enhance the fabric's properties, texture and durability.
Spunbond nonwoven fabric is known for its extremely good breathability. They also possess commendable light weight and durability. Some applications of this nonwoven fabric include masks, weed barrier coatings, geotextiles, shopping bags, etc.
2.6. Meltblown nonwovens
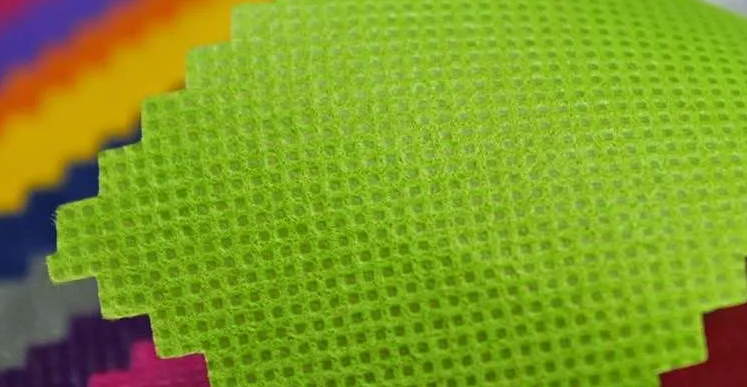
Meltblown nonwoven fabric possesses an extremely fine fiber structure that makes them one of the fabrics with high density
One of the very popular types of nonwoven fabric is meltblown. This is a nonwoven fabric created by extruding thermoplastic polymers. First, the process causes the material to melt through nozzles or spinning machines. The system then blows them with high-speed air to form a network of interwoven fibers. The main steps in this process are:
-
Melting: Thermoplastic polymers are melted in an extruder.
- Extrusion: The molten material is forced through small nozzles or spinning machines to produce continuous very fine fibers.
- Blowing: High-speed hot air or gas blows the extruded fibers onto the conveyor belt to form a web. This step also helps spread the fibers randomly.
- Bonding: The fiber web is then cooled or heat treated so that it sticks together tightly.
- Finishing: The fabric may undergo further processes such as pressing or drying to improve its texture and durability.
Meltblown nonwoven fabric possesses an extremely fine fiber structure that makes them one of the fabrics with high density. Thanks to this, meltblown nonwoven fabric is known for its excellent filtration properties that help remove most small particles. Besides, this nonwoven fabric is also very soft and highly absorbent. Some applications of this fabric include medical masks, diapers, air and liquid filtration systems, protective clothing, etc.
2.7. Acupuncture nonwovens
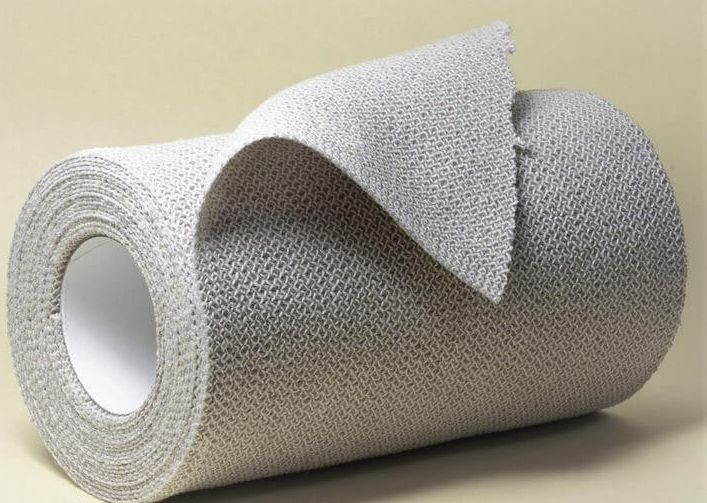
Acupuncture nonwoven fabric possesses suitable features and properties to serve acupuncture processes
Acupuncture nonwoven fabric is a specialized nonwoven material designed for use in acupuncture-related applications. This nonwoven fabric possesses suitable features and properties to serve acupuncture processes. They are very soft, helping to create comfort for the patient during use. In addition, this nonwoven fabric has good antibacterial properties to help ensure hygiene and reduce cross-infection.
Some applications of acupuncture nonwoven fabric include acupuncture mats, acupuncture needle covers, and some bed sheets and pads for medical use.
2.8. Stitch nonwovens
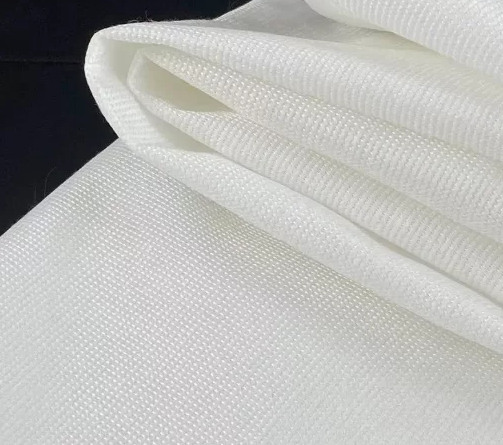
Stitch nonwoven fabric is a type of nonwoven material created by stitching layers of fibers together to form a bonded fabric
Stitch nonwoven fabric is a type of nonwoven material created by stitching layers of fibers together to form a bonded fabric. This method combines elements of both nonwoven and woven fabrics. Production process includes:
-
Prepare the yarn: The yarn will be laid in layers to form a mesh or carpet.
- Stitching: Layers of fabric are sewn together using a sewing machine or specialized sewing equipment. This process helps hold the fibers in place and form the fabric.
- Bonding: In some cases, additional bonding methods such as heat treatment or glue are used to enhance the stability and durability of the fabric.
Stitch fabric's stitching provides greater strength and durability than some other nonwoven fabrics. In addition, they are very flexible in production. The drape, softness and density of the fabric can be changed flexibly by adjusting the stitches.
3. Conclusion
In conclusion, the appearance of nonwoven fabric is considered a creative innovation in production. A better understanding of the different types of nonwoven fabrics will help manufacturers flexibly adjust the properties of each type to suit each production need. In fact, thanks to its excellent properties, the potential use of nonwoven fabric will continue to expand in the near future. The future of nonwovens promises even greater contributions to efficiency, sustainability and everyday convenience.
4. About EuroPlas
EuroPlas is proud to be one of the most reputable and trustworthy material suppliers worldwide. You can easily find and buy bio-filler, color masterbatch, plastic, and bioplastic compounds, etc., for your nonwoven applications with just a click of the mouse. Besides, come to EuroPlas' blog today to update more useful materials information. We are a provider of optimal material solutions with a series of high quality plastic lines. Our solutions meet the diverse needs of the world's industries, not only in terms of high standards and reliability but also in terms of environmental obligations.