Nylon blocks are sturdy and versatile pieces of nylon. It has the exceptional properties of the main resin, a synthetic polymer used in many different sectors.
Since it features strength, flexibility, low friction, and resistance to chemical wear and tear, it's a popular choice in the engineering, electronics, and automotive industries. Let's dig into the details of this material right now!
1. What Are Nylon Blocks?
Nylon blocks are large, solid pieces of plastic made from nylon resin. They're used in a wide range of commercial, industrial, and technical applications due to their strength, durability, and adaptability. The synthetic polymer used to make these blocks, nylon resin, is renowned for its ability to withstand chemicals, wear, and abrasion.
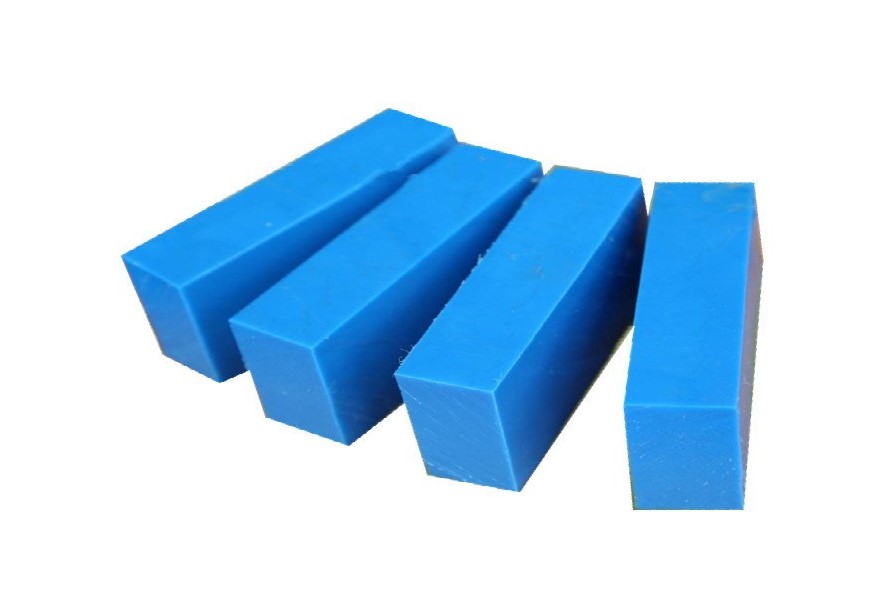
Nylon blocks
Nylon blocks' strength and wear resistance make them perfect for heavy-duty applications. They are also helpful in mechanical parts that need to move smoothly, thanks to their low coefficient of friction. Under typical circumstances, they can tolerate mild heat and keep their structural integrity. Besides, the material is beneficial in electrical components due to its insulating qualities.
2. Applications of Nylon Blocks
Due to their strength, durability, and versatile properties, nylon blocks are used in many industries, including:
- Engineering and manufacturing: Nylon blocks are frequently used for custom machining of parts, including gears, bearings, bushings, pulleys, washers, and spacers, since they offer exceptional durability and wear resistance.
- Automotive industry: Automotive components, including gears, bearings, bushings, and cam followers, are made of nylon, a robust and low-friction material. It helps minimize wear and boost system performance. Other applications also include under-the-hood parts that need high temperatures and stress, such as brackets and pulley wheels.
- Electronics and electrical: Because of its longevity and resilience to high temperatures, nylon blocks are used in the manufacturing of electrical insulators, wire components, and connections. They are also frequently found in electronic device housings, relays, and electrical switch components.
- Food processing: Nylon blocks offer resistance to moisture and chemicals, allowing them to be used in food processing and manufacturing for conveyor systems.
- Marine industry: Because they are resistant to chemicals, moisture, and salt, nylon blocks are essential for marine boat parts including pulleys, bushings, and bearings.
- Medical and pharmaceutical: Their robustness, biocompatibility, and resistance to moisture and chemicals make them ideal for medical equipment parts and pharmaceutical processing.
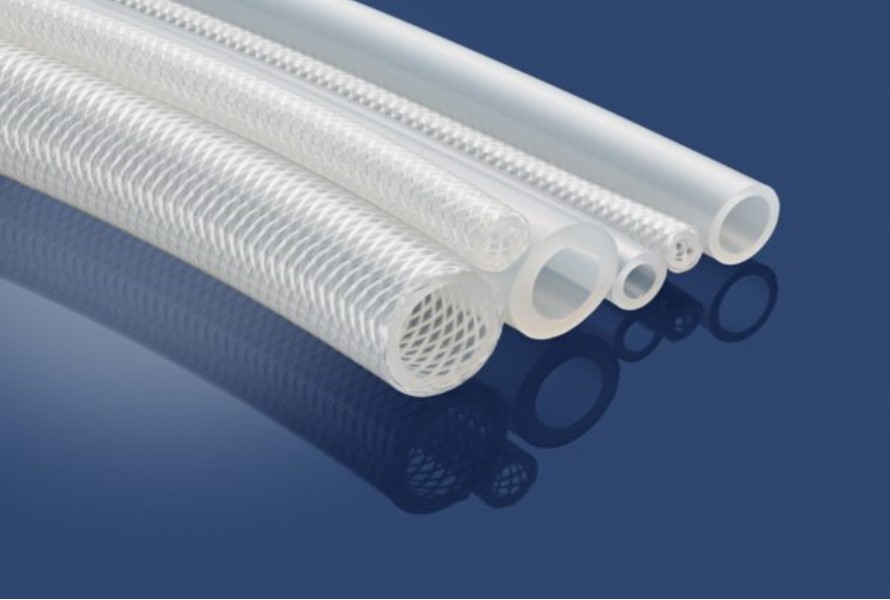
Customized tubing for medical applications
3. Why Are Nylon Blocks Used By Industries In Real Life?
Because of their special qualities enabling them to withstand a variety of demanding conditions, nylon blocks are widely used in industries for a wide range of applications. They have:
- Durability and strength: Their strength and ability to tolerate mechanical stress without breaking or deforming make them suitable for parts like gears, bearings, and bushings that survive wear and severe loads. It guarantees a long service life and lowers the need for frequent replacements.
- Low Friction and wear resistance: Nylon's low coefficient of friction enables its components to slide smoothly against other materials. This characteristic is essential for sectors including industrial, automotive, and aerospace because it lowers maintenance costs and boosts productivity by reducing friction in moving components.
- Electrical insulation: Nylon's exceptional insulating qualities make it a useful material in the electrical and electronics sectors. Its ability to tolerate electrical current without degrading is essential for safe device operation.
- Chemical, moisture, and weather resistance: Because of their exceptional resistance to a wide range of chemicals, oils, and fuels, nylon blocks are ideal for applications in the food processing, automotive, and chemical production sectors. They are appropriate for outdoor and maritime applications due to their exceptional resistance to weather and moisture. The nylon components are dependable in a range of weather conditions because they can resist water, salt, and environmental factors without deteriorating.
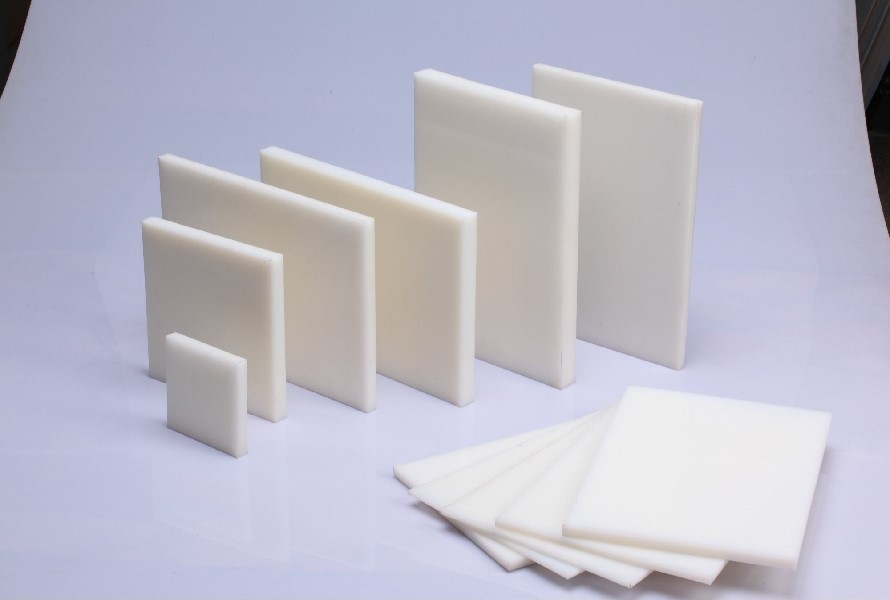
Nylon blocks offers many benefits
4. Challenges and Limitations
Though nylon blocks offer many good properties, we can't say they don’t have any disadvantages. Before using the material, manufacturers should consider:
- Strength: Nylon is less strong than metals or reinforced composites, which makes it less appropriate for uses where significant mechanical strength is needed, including heavy-duty structural components. Nylon might not be the best material unless strengthened with glass fibers.
- Temperature and UV sensitivity: Nylon may disintegrate at temperatures exceeding 180°C (356°F), which is lower than certain other technical polymers or metals. Therefore, even though it is heat resistant, it has limitations in high-temperature situations, making it less appropriate for high-temperature uses, such as some industrial equipment components or automobiles. Furthermore, unless nylon is specifically treated or coated to withstand UV radiation (for example, by adding chemicals to increase UV stability), it is less appropriate for outdoor applications due to its susceptibility to UV light damage.
- Wear and tear in high-load applications: Nylon may not be suitable for high-load or high-stress applications because of its propensity to wear or fail under continuous strain. Additives like glass fiber or carbon may be necessary to strengthen nylon in high-velocity, high-friction settings, such as heavy-duty equipment.
- Processing challenges: Despite being simple to process, nylon's high melt viscosity makes it difficult to mold into intricate geometries. Uneven material flow and flaws, including voids, warping, and varying component quality, can happen during the manufacturing process.
5. Conclusion
Nylon blocks are an essential material for many modern industrial applications. It offers minimal friction, necessary strength, and good resistance to chemicals and wear, making it suitable for both heavy machinery and small details. Though there are some disadvantages, nylon remains an economical and reliable choice for many applications that demand durability and high performance.
6. About EuroPlas' PA Products
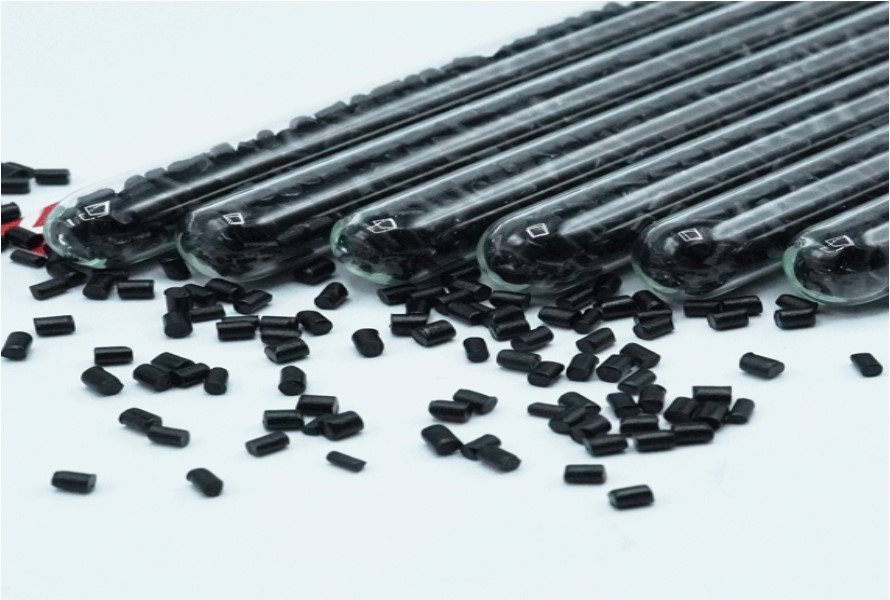
PA compound from EuroPlas
As a leader in the masterbatch world, EuroPlas always updates its technology to provide the best products for customers. To enhance the quality of PA, we created excellent compounds: PA6, PA66 blend compound and PA66, PA6 Glass fiber compound. These all-functions-in-one solutions will assist you in producing final products that are highly precise, mechanically strong, and have improved usability and durability.
Contact us now for a stable and quality source of raw materials!