Nylon vs. Teflon: What Are The Differences?
When selecting materials for industrial or mechanical applications, Nylon vs Teflon frequently come into consideration due to their distinct advantages. Understanding the differences between Teflon vs Nylon is crucial for producers, engineers and designers when selecting the right component for their projects.
1. Overview Of Nylon & Teflon
Nylon vs Teflon, both essential synthetic polymers, are widely used across various industries due to their unique properties.
Nylon, first developed by Wallace Carothers in 1935, is known for its mechanical strength and wear resistance. This thermoplastic material has found applications in countless products, from fabrics like carpets and bridal veils to industrial components such as gears, bearings, and machine screws. However, its hydrophilic nature, meaning it absorbs water, can limit its functionality in environments where moisture resistance is needed.
Teflon, or PTFE (Polytetrafluoroethylene), discovered accidentally by Dr. Roy Plunkett in 1960, when he was working on finding an alternative material for cooling purposes. After that, Teflon has become a go-to material in applications requiring non-stick, heat-resistant, and chemically inert properties. One of its most popular uses is in non-stick cookware, but Teflon also excels in industrial environments, serving as a lubricant due to its low friction and water-repellent surface.
Both Nylon vs Teflon are commonly used as washers due to their superior mechanical strength and friction resistance compared to traditional materials like aluminum, steel, and bronze. Nylon washers are valued for their durability and ability to withstand wear, making them ideal for parts subjected to high stress and movement. However, in applications where water or chemical exposure is an issue, Teflon is the better choice.
.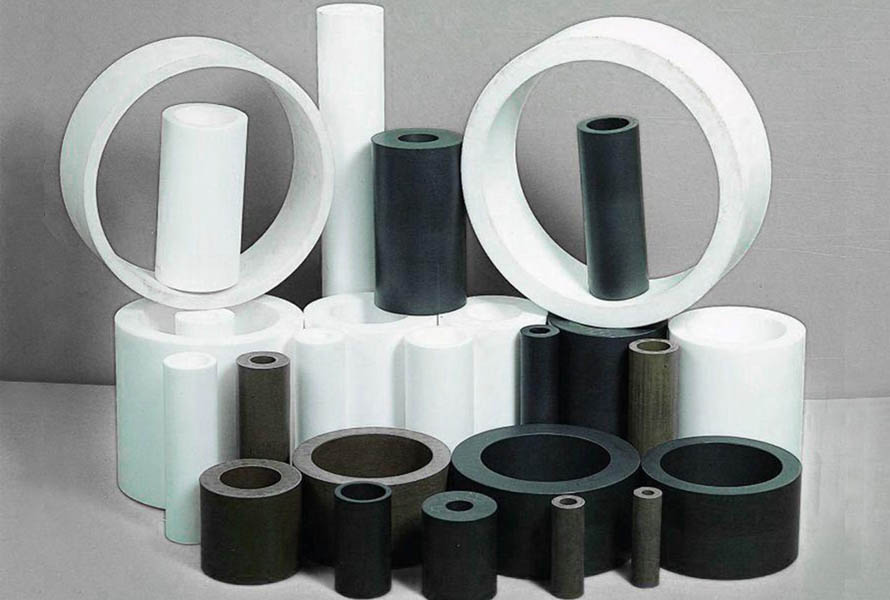
Nylon vs Teflon, both essential synthetic polymers, are widely used across various industries thanks to their unique properties.
2. Nylon vs. Teflon: Comparing Properties
Here's a table comparing Nylon vs Teflon properties and highlights the key differences between them.
Property |
Nylon |
Teflon (PTFE) |
Chemical Composition |
Polyamide polymer made from repeating units of amides. |
Polytetrafluoroethylene (PTFE), a fluoropolymer made from tetrafluoroethylene. |
Temperature Resistance |
Handles moderate heat, typically up to 200°C (392°F). |
Excellent heat resistance, up to 260°C (500°F). |
Friction Coefficient |
Moderate friction, often used in applications requiring durability. |
Extremely low friction, ideal for applications needing slipperiness and wear resistance. |
Flexibility |
Good flexibility and elasticity, making it suitable for a range of mechanical applications. |
Less flexible, but highly durable under stress and deformation. |
Impact Resistance |
High impact resistance, maintaining strength under stress. |
Lower impact resistance compared to Nylon, may crack under sudden impact. |
Wear Resistance |
Good wear resistance but degrades over time with high friction. |
Outstanding wear resistance, maintains properties even with continuous friction. |
Water Absorption |
Absorbs water, which can affect its mechanical properties (up to 3-4%). |
Non-absorbent, maintaining stable performance in wet environments. |
Chemical Resistance |
Resistant to oils, greases, and some chemicals, but not as chemically inert as Teflon. |
Highly resistant to most chemicals, acids, and solvents. |
Electrical Insulation |
Good electrical insulation, often used in electronics. |
Excellent electrical insulation, superior to Nylon. |
Cost |
More cost-effective, widely available. |
More expensive due to specialized manufacturing and material properties. |
3. Nylon vs. Teflon: Pros & Cons
Nylon vs Teflon, both offer distinct advantages and disadvantages, making them suitable for different applications. For example, Nylon’s durability, flexibility, and affordability make it a versatile option for mechanical parts, but its water absorption and lower chemical resistance limit its use in certain environments. Teflon, with its superior chemical resistance, high-temperature tolerance, and low friction, excels in extreme conditions but comes at a higher cost and with reduced flexibility.
Nylon
- Pros: Strong, durable, flexible, affordable, abrasion-resistant
- Cons: Absorbs moisture, susceptible to some chemicals
Teflon
- Pros: Non-stick, heat-resistant, chemically resistant, reduces wear
- Cons: Expensive, potential environmental concerns
Selecting between Nylon vs Teflon depends on the specific requirements of the application, balancing cost, durability, and environmental factors. Both materials offer distinct properties that can influence their suitability for various industrial and consumer uses. Understanding these differences is key to making the right choice.
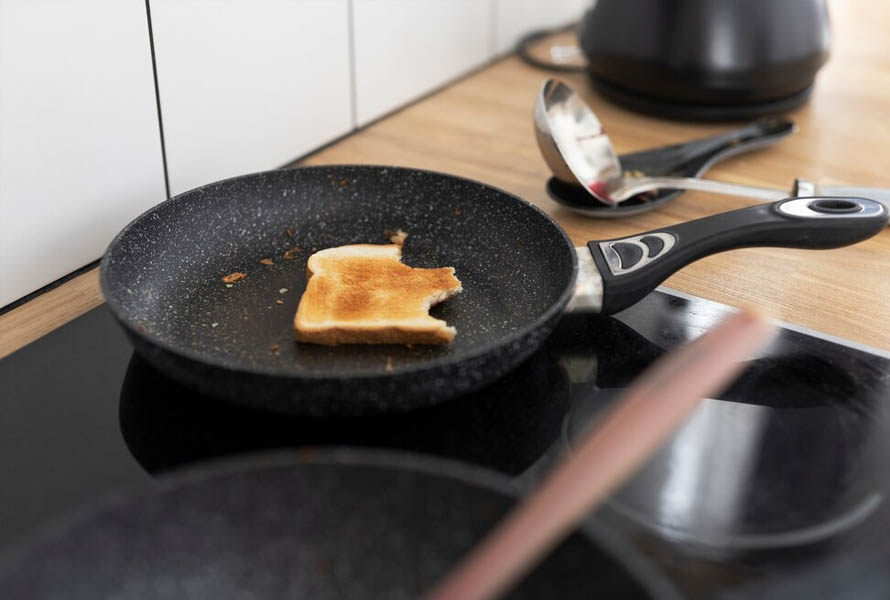
Teflon, with its superior chemical resistance, high-temperature tolerance, and low friction, excels in extreme conditions
4. Nylon vs. Teflon: Comparing Applications
Nylon vs Teflon is a common comparison when evaluating materials for engineering applications. Both materials have unique properties. When choosing between nylon vs teflon, understanding their strengths helps in selecting the most suitable material for specific industrial uses.
Nylon's strength and flexibility make it a popular choice for:
- Clothing and textiles: From stockings and backpacks to sportswear and carpets, nylon's durability and versatility come in handy.
- Ropes and cords: Used for tasks requiring strong, flexible lines, like mooring lines, climbing ropes, and cargo straps.
- Automotive parts: Nylon's toughness makes it suitable for gears, bearings, and other components needing reliable performance under stress.
- Industrial applications: Nylon's strength and abrasion resistance make it a good fit for gears, washers, and conveyor belts.
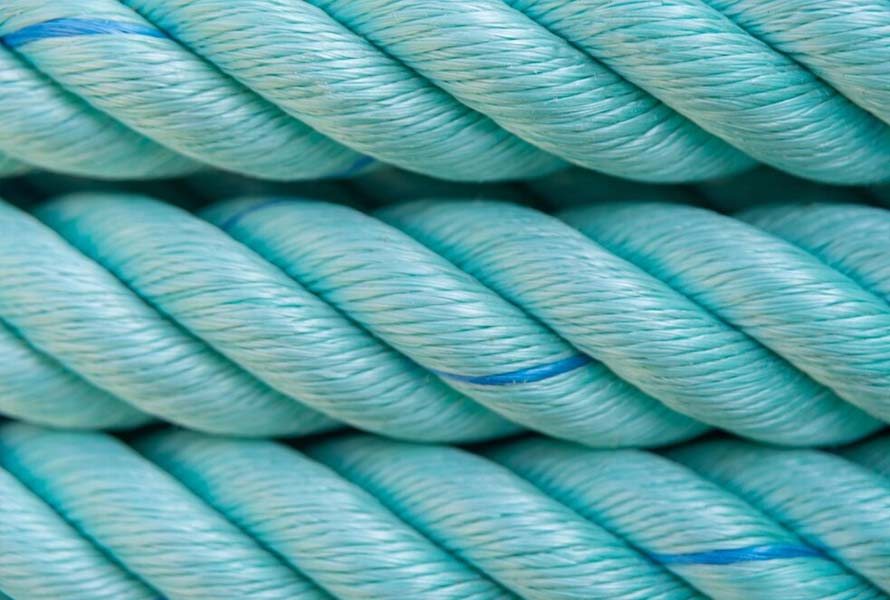
The strength and flexibility of nylon make it a popular choice for textile applications, ropes, gears, washers, and more.
Teflon's non-stick and heat-resistant properties make it ideal for:
- Non-stick cookware: Frying pans, griddles, and waffle irons all benefit from Teflon's ability to prevent food from sticking and ease cleaning.
- Industrial coatings: Used on pipes, molds, and other equipment where materials need to flow smoothly and withstand high temperatures.
- Medical devices: Teflon's non-reactive nature and low friction make it suitable for catheters, implants, and other medical equipment.
- Electrical insulation: Teflon's ability to resist electrical current makes it useful for wires, cables, and other electrical components.
- Aerospace components: Teflon's heat resistance and low friction make it suitable for use in aircraft and spacecraft components.
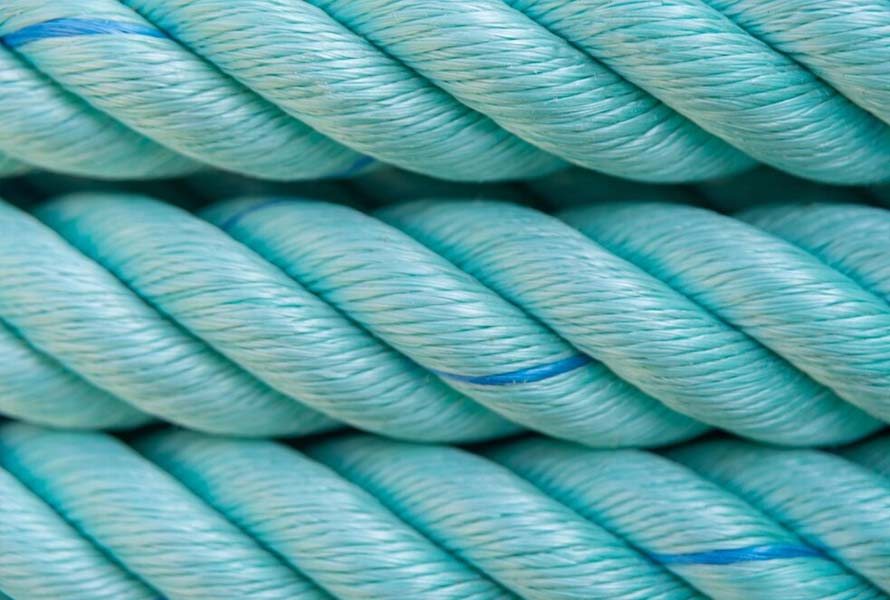
Nylon vs Teflon offer distinct advantages for a wide range of applications.
5. What Should You Choose? Nylon Or Teflon?
Choosing between Nylon vs Teflon ultimately depends on the specific requirements of your application. If you need a material that offers strength, flexibility, and durability for mechanical components, Nylon is an excellent choice. However, if your application involves exposure to harsh chemicals, high temperatures, or requires low friction properties, Teflon is the better option, despite its higher cost.
Assessing factors such as environmental conditions, mechanical stresses, and budget will guide you in making the right choice between Nylon vs Teflon for your needs.
6. Conclusion
In conclusion, Nylon vs Teflon are both valuable materials, each offering unique benefits suited to different applications. Nylon, with its robustness and flexibility, is well-suited for a variety of applications that require mechanical strength and durability, making it a staple in many industrial settings. Teflon, while not as strong, compensates with its unparalleled resistance to chemicals and high temperatures, making it essential in applications where these factors are critical.
By understanding Nylon vs Teflon’s distinct properties, you can make an informed choice to ensure the best performance and durability for your projects.
7. About EuroPlas’ PA Products
With over 17 years of experience and a global reach spanning over 95 countries, EuroPlas has become a trusted resource for PA (polyamide) products. Our PA products cater to various unique applications, going beyond traditional nylon uses by offering PA compounds designed for a wide array of industries, such as automotive, electronics, and textiles, etc. Specialized applications of EuroPlas PA include:
- PA 6 and PA 66: EuroPlas offers high-quality PA6 and PA66 products, both known for their outstanding mechanical properties and heat resistance. PA6 is ideal for applications requiring flexibility and impact resistance, while PA66 offers superior stiffness and thermal stability, making it suitable for more demanding engineering tasks.
- Bioplastics: Bio-based PA compounds from EuroPlas offer a sustainable solution for packaging, agriculture, and disposable products.
- Filler Masterbatches: EuroPlas offers PA compounds with added fillers that improve specific properties like strength, heat resistance, or flame retardancy. This allows for tailored material solutions for diverse applications.
- Color Masterbatches: Pre-colored PA compounds from EuroPlas simplify production, offer a solution to the hassle of separate coloring processes and ensure color consistency.
EuroPlas PA products offer versatility beyond traditional nylon applications. If you’re looking for top-quality PA materials to meet your industrial needs, contact us for expert advice and product solutions tailored to your requirements.