When it comes to advanced engineering thermoplastics, PEEK (Polyether Ether Ketone) and PEKK (Polyetherketoneketone) stand out. Understanding the differences between these two materials is critical for many manufacturing applications, including additives and 3D printing.
PEKK and PEEK, like twins with different personalities, have distinguishing properties that make them suited for certain uses. Let us go deeper into their qualities to discover the nuances that define each of them.
1. PEKK vs PEEK: Definitions
PEKK (Polyetherketoneketone) and PEEK (Polyetheretherketone) are both high-performance thermoplastic polymers that belong to the polyaryletherketone (PAEK) family.
1.1. Polyetherketoneketone (PEKK)
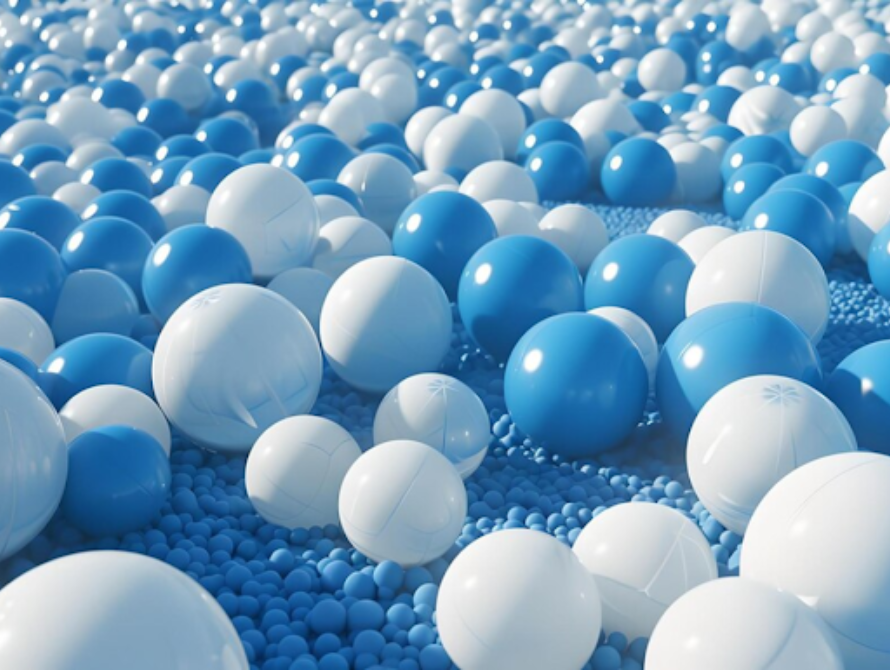
Both polymers have excellent qualities; nonetheless, their chemical structures show considerable discrepancies.
Polyetherketoneketone, or PEKK, is a high-performance thermoplastic that is well-known for its remarkable chemical and mechanical resistance. PEKK is composed of a distinct molecular structure with two ketone groups in each repeating unit, which sets it apart from other plastics. The unique arrangement that provides PEKK its exceptional qualities.
Its qualities can be greatly influenced by the exact ratios of the ingredients, or in this case, the molecular structure's constituent parts.
High-temperature, chemically aggressive, and mechanically demanding plastics are needed in industries such as aerospace, automotive, and medical. Hexcel Corporation, previously Oxford Performance Materials, makes PEKK-based parts for Boeing's Starliner space transports utilizing 3D printing. These parts, which have the same strength as aluminum but weigh 40% less, are fire and radiation resistant, making them perfect for aerospace applications.
Gain a deeper comprehension of PEKK's capabilities at: All you need to know about PEKK plastic
1.2. Polyetheretherketone (PEEK)
On November 19, 1978, ICI, a renowned chemical company, produced the first batch of Polyether Ether Ketone (PEEK), marking a momentous occasion in the field of high-performance polymers.
Polyether Ether Ketone, or PEEK, is a type of molecular structure that alternates between ether and ketone groups. PEEK's exceptional mechanical strength, thermal stability, and chemical resistance are made possible by this special arrangement, which makes it a highly sought-after material in a variety of sectors.
The US Food and Drug Administration (FDA) recently approved PEEK for safe human contact under acceptable preparation conditions. This advancement has paved the way for PEEK's incorporation into the food and beverage industry, where it is increasingly used in a variety of components including cookware, beverage dispensers and nozzles, and processing applications. This regulatory approval reinforces PEEK's dependability and suitability for important applications in food handling and processing, cementing its position as a versatile material in a wide range of industrial contexts.
PEEK is easy to integrate into intricate designs and applications since it can be used with a variety of manufacturing methods, such as injection molding, extrusion, and machining.
PEEK was chosen to manufacture two crucial components for the Jovian Auroral Distributions Experiment on NASA's Juno Space Probe. The Southwest Research Institute of San Antonio developed the JADE sensors for electrons and ions, which were critical to the probe's purpose. This demonstrated the material's viability for aeronautical applications and its role in boosting space exploration efforts.
Learn about the most recent advancements in PEKK technology at: PEEK plastic: Definitions and Application
2. PEKK vs PEEK: What are the differences?
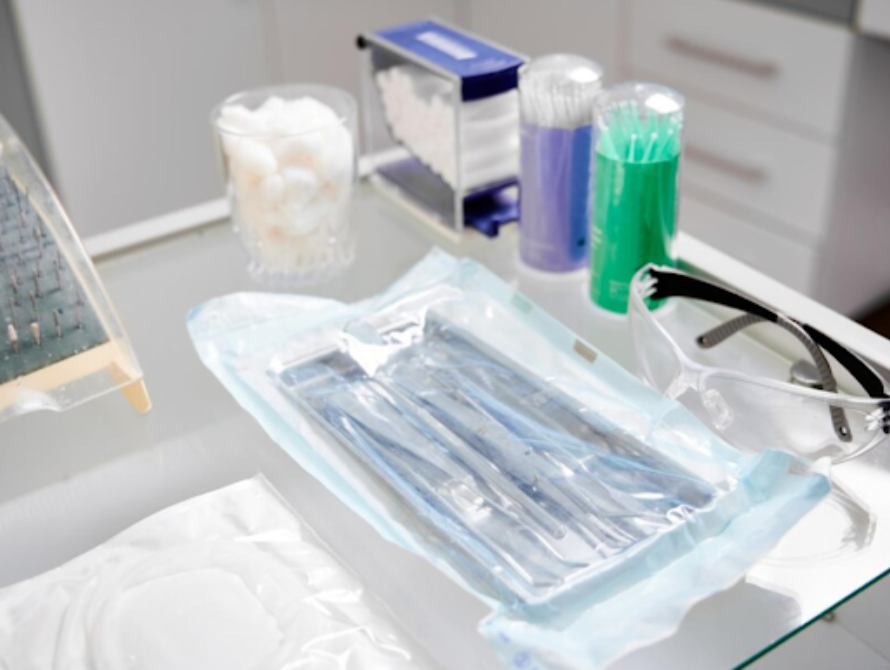
PEKK and PEEK are at the forefront of medical technology, providing unprecedented improvements in implanted devices.
2.1. Chemical Structure:
The molecular structure of PEKK consists of repeating units, with each unit containing two ketone groups (-CO-). PEKK exhibits remarkable mechanical strength, thermal stability, and chemical resistance due to its structure, which yields a polymer chain with alternating ketone and ether groups.
On the other hand, PEEK is made up of repeating units, each of which has one ether group (-O-) and one ketone group (-CO-). With ketone and ether functions alternated, this molecular configuration forms a polymer chain. Because each repeating unit of PEEK has a single ketone group, all of its qualities may change significantly, even though it is mechanically stronger, more stable at high temperatures, and more chemically resistant than PEKK.
2.2. Mechanical Strength:
PEKK:
- Tensile strength ranges between 70 and 150 MPa.
- The range of a flexural modulus can range from 2,800–4,000 MPa.
PEEK:
- Tensile strength usually falls between 90 and 100 MPa.
- The variety of flexural modulus is typically 3,500–4,000 MPa.
The main causes of the mechanical strength differences between PEEK (Polyether Ether Ketone) and PEKK (Polyetherketoneketone) are changes in their molecular makeup and architectures.
However, processing parameters like temperature, pressure, and cooling rate during manufacture can also have an impact on the mechanical properties of PEKK and PEEK. Changes in the parameters of the processing can have an impact on the degree of crystallinity and molecular alignment, which in turn affects mechanical strength.
For instance, in injection molding, the rate of crystallization is influenced by the temperature of the polymer melt as it flows into the mold cavity. Adjusting the temperature profile makes it possible to maximize crystallinity and, in turn, mechanical qualities. Higher molding temperatures for PEKK and PEEK may encourage greater crystallinity and, thus, higher mechanical strength.
2.3. Thermal Stability:

By exposing these materials to temperatures, researchers ensure their endurance in demanding applications.
PEKK: Withstands temperatures ranging from -70°C to 260°C without batting an eye, making it a top choice for extreme temperature environments.
PEEK: Although it might not reach as high of temperatures as PEKK, PEEK is not far behind and can withstand temperatures ranging from -70°C to 250°C with ease.
By adding additives or fillers, like carbon or glass fibers, PEKK and PEEK's thermal stability can be further increased. This can also improve the materials' mechanical performance and heat resistance.
2.4. Chemical Resistance:
PEKK: Highly resistant to acids, bases, solvents, and oils – it's like the superhero of chemical resistance.
PEEK: Equally impressive in its chemical resistance, standing up to acids, bases, solvents, and hydrocarbons with ease.
Enhancing chemical resistance in the polymer matrix can be achieved by adding fillers and additives. Fillers have the ability to provide a physical barrier that stops chemicals from penetrating and breaking down the polymer matrix.
2.5. Biocompatibility:
PEEK and PEKK's chemical compositions are well-tolerated by biological systems, ensuring they do not release harmful substances. Both materials exhibit inert behavior, reducing the risk of adverse reactions or toxicity when implanted.
Their surface properties can be modified to enhance interaction with biological tissues, promoting integration and reducing rejection.
In orthopedics, PEEK is used in joint replacements and bone plates, while PEKK finds applications in spinal fusion cages. Additionally, they are utilized in surgical instruments for precise procedures and in drug delivery systems for controlled release of pharmaceuticals.
2.6. Applications:
PEKK and PEEK play crucial roles in the field of advanced materials, leading to innovative solutions across a wide range of industries.
Application
|
PEEK Solution/Product
|
PEKK Solution/Product
|
Structural components
|
Lightweight brackets, clips, and panels
|
Structural brackets, ducts, and interior panels
|
Engine components
|
Piston parts, valve seals
|
Gaskets, seals
|
Orthopedic implants
|
Joint replacements, spinal fusion cages
|
Spinal fusion cages, interbody devices
|
Prosthetics
|
Dental implants, abutments
|
Dental implants, bridges
|
Manufacturing components
|
Gears, bearings, bushings
|
Pump parts, valve seats, seals
|
Electrical insulation
|
Connectors, housings
|
Electrical connectors, device housings
|
Injection molding parts
|
Injection molding components such as molds and nozzles
|
Extrusion dies, injection molding tooling and fixtures
|
3. PEKK vs PEEK: Differences in how it’s made
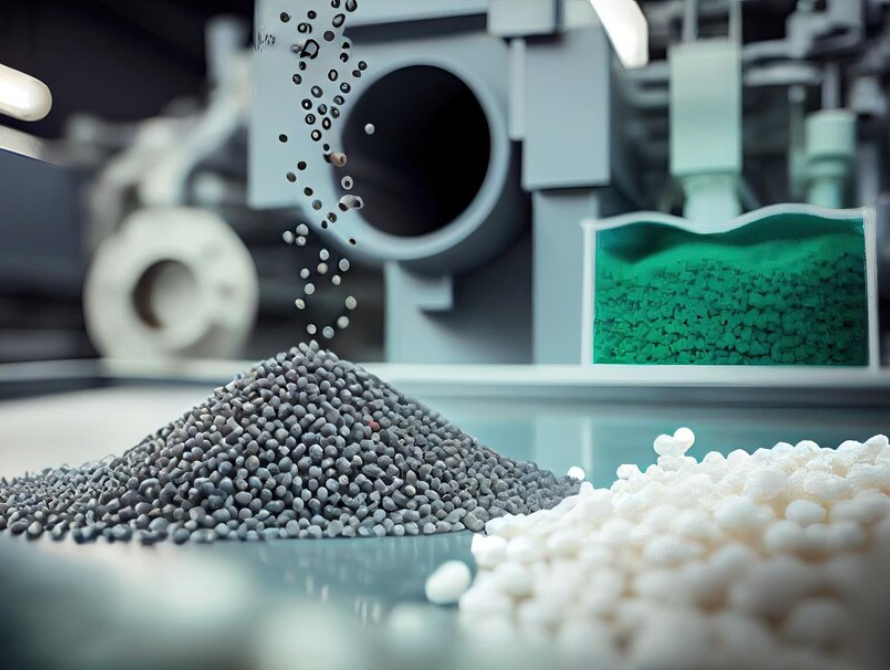
Changes in monomer composition and reaction circumstances result in unique characteristics for each material.
3.1. PEKK Manufacturing Process:
Usually, step-growth polymerization—also referred to as polycondensation—is used to create PEKK. Long polymer chains are created in this procedure by a sequence of chemical reactions involving monomers that include ether and ketone groups. In particular, aromatic diacid chlorides and aromatic bisphenols react under carefully regulated circumstances in the presence of a catalyst to create PEKK.
The resultant PEKK polymer is purified and processed into different forms, including pellets or powder, for further usage after the polymerization operation is finished. To create completed goods, these forms can then be 3D printed, molded, or extruded.
3.2. PEEK Manufacturing Process::
PEEK is mostly made by nucleophilic aromatic substitution, often known as polycondensation, a step-growth polymerization technique. This method creates PEEK polymer chains by reacting aromatic dihalides and aromatic bisphenols with an acid or base catalyst.
To promote chain development and cross-linking, the polymerization reaction happens at high pressures and temperatures, usually in a molten or solvent state. After reaching the required molecular weight, contaminants and leftover solvents are eliminated from the PEEK polymer by precipitating, washing, and drying it.
Extrusion or other molding techniques are then used to transform the pure PEEK resin into different forms, such as pellets, granules, or powders. Using techniques like injection molding, compression molding, or machining, these forms can be further processed into final products.
3.3. Key Differences in Manufacturing:
Monomer composition: The monomers used in PEKK synthesis contain ketone and ether groups, while those used in PEEK synthesis contain ketone and halide groups, leading to differences in chemical structure and properties.
Reaction conditions: The temperature, pressure, and catalysts used in the polymerization reactions of PEKK and PEEK vary, which has an impact on the polymerization kinetics and overall structure.
Cost: Because there are variations in raw material availability, reaction conditions, and purification techniques, the manufacturing processes for PEKK and PEEK may be more expensive than one another. In comparison to PEEK, the production of PEKK might require more intricate synthesis procedures and specialized catalysts, which could raise manufacturing costs.
4. PEKK vs PEEK: Which one is better?
Criteria
|
PEKK
|
PEEK
|
Decision
|
Mechanical Strength
|
- Higher tensile strength (70-150 MPa)
- Higher flexural modulus (2,800-4,000 MPa)
|
- Lower tensile strength (90-100 MPa)
- Similar flexural modulus (3,500-4,000 MPa)
|
PEKK: Suitable for applications requiring higher mechanical strength.
|
Thermal Stability
|
- Can withstand temperatures (-70°C to 260°C)
- Higher thermal stability
|
- Can withstand temperatures (-50°C to 250°C)
- Slightly lower thermal stability
|
PEKK: Preferred for high-temperature applications due to its wider temperature range.
|
Chemical Resistance
|
- Highly resistant to acids, bases, solvents, oils
|
- Highly resistant to acids, bases, solvents, hydrocarbons
|
Equal: Both materials offer exceptional chemical resistance.
|
Biocompatibility
|
- Extensively tested for biocompatibility, suitable for medical implants and devices
|
- Widely used in medical implants and devices
|
Equal: Both materials are suitable for medical applications requiring biocompatibility.
|
Manufacturing Versatility
|
- May involve more complex synthesis steps and specialized catalysts, potentially resulting in higher manufacturing costs
|
- Generally easier to process and more cost-effective
|
PEEK: Offers better manufacturing versatility and cost-effectiveness.
|
Cost
|
- Potentially higher manufacturing costs due to complexity of synthesis steps and specialized catalysts
|
- Generally lower manufacturing costs
|
PEEK: Offers better cost-effective
|
Neither PEKK nor PEEK can be definitively labeled as "better" than the other. Instead, the choice depends on the specific requirements and priorities of your application. PEKK excels in high-temperature environments and offers superior mechanical properties, while PEEK is widely recognized for its versatility, toughness, and cost-effectiveness.
Consider factors such as temperature resistance, mechanical strength, chemical resistance, biocompatibility, and cost when selecting the most suitable material for your project.
5. About EuroPlas
EuroPlas (EuP) stands out as a global leader in the plastic materials industry, renowned for its commitment to innovation, customer satisfaction, and sustainable development.
Utilizing cutting-edge technology, a skilled workforce, and an international perspective, EuroPlas provides customized plastic material solutions that satisfy the various demands of global industry.
Explore a wide choice of plastic material solutions and find out more about how EuroPlas may help your business by visiting our website.
Check out the blog for EuroPlas right now to stay up to date on the most recent information, analysis, and advancements in the plastic materials sector.