PET is one of the most widely used plastic packaging materials worldwide. Additionally, it is among the most common forms of garbage found in the water. However, because PET bottles are 100% recyclable, they should be viewed as resources rather than waste after use. Heating and molding techniques are used to form PET into a variety of shapes, making it a convenient, safe, and hygienic packing process. PET exhibits a low melting temperature in contrast to glass and aluminum substitutes. This property enables converting PET packaging into a closed loop, or in other words, creating a circular economy that is simple and sustainable.
Read more: PET vs HDPE: Which one is better?
1. Why should you recycle PET bottles?
PET bottle recycling should be done to support the circular economy. The concept of the circular economy is, in essence, to extend the life of goods and maintain the highest potential value of the resource's attributes for an extended period of time, thus allowing resources to remain inside the economic cycle for a longer time. The plastic may still be used as fuel after it loses its recyclable status since it has the same calorific value as virgin material.
The growing number of people (including PET bottle suppliers and users) who identify as environmentally conscious drives up demand for items made from recycled materials. The demand for resources rises in tandem with the growth of the world's population. We become less reliant on the finite raw materials of Earth by recycling the resources that have previously been exploited.
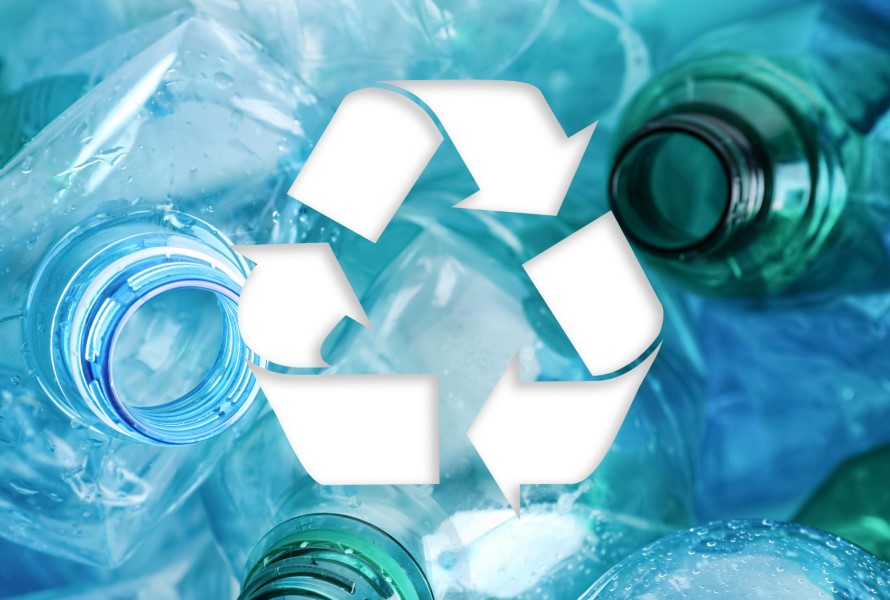
Due to the exceptional performance characteristics and high degree of recyclable nature, PET plastic bottles have a wide range of possible post-consumption applications, making them one of the most widely used plastic packaging materials worldwide. PET packaging is also easily identifiable. Simply check for the #1 sign to confirm that all of the plastic in your item is recyclable.PET can be heated and molded into many different forms, but the most recognizable are the plastic water and beverage bottles, which offer hygienic, secure, and convenient methods of storing beverages. Because PET melts at a lower temperature than materials like glass and aluminum, recycling PET packaging into more PET packaging in a closed loop is simple and environmentally friendly.
2. Steps of PET bottle recycling
2.1. Bottle collection
The PET bottle could simply be thrown away with the rest of the trash after use. But, it is not a long-term solution. Most countries now have recycling policies in place to promote plastic recycling, including PET. The consumer is advised to place the PET bottles in the recycling bin rather than discarding them. The recyclables will then be gathered and delivered to a sorting place. Businesses will also generate PET waste, so they should ensure the plastic collection and recycling process to help save our planet.
2.2. Sorting process
At the recycling plant, high-value recyclable plastics like PET are separated automatically or manually to ensure no non-plastic waste is left and mixed together. It is due to the fact that the recycling of PET would be contaminated by the presence of other plastics, which would lower the quality of the material for reuse, decrease efficiency, and increase waste.
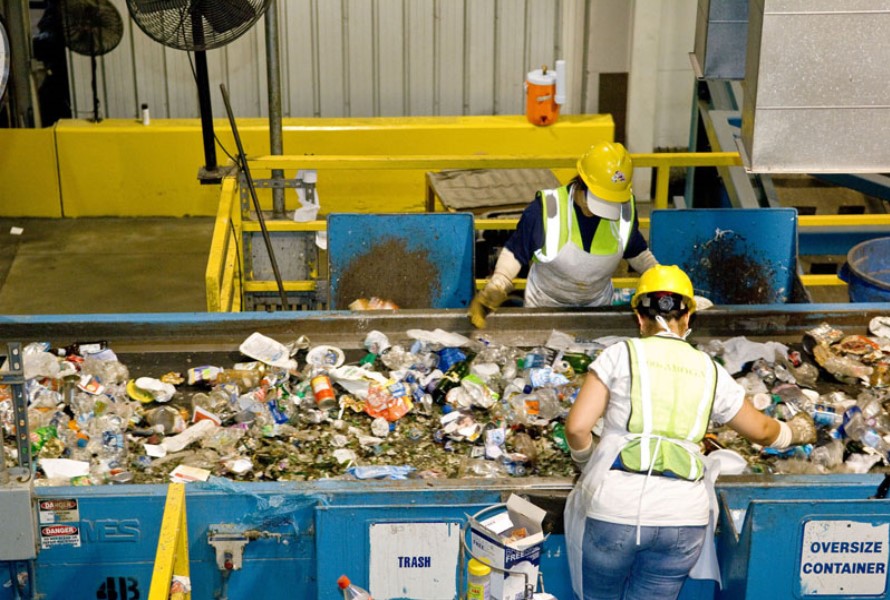
2.3. Bottle compaction
The screw compactor compacts and drains the PET bottles in a continuous process. The process is simple, in which the machine operator feeds the machine manually, using a forklift or a conveyor. Following the material's descent into the screw, the PET is compressed and the liquid is squeezed out. The compacted and drained PET bottles typically land in a container. PET bottles that have been drained and compacted are easier to transport to a recycling facility.
2.4. Transportation
After the collecting and compressing process, the PET is transported to the recycling places. PET is superior to other recyclable packaging materials because it is incredibly lightweight and easily forms tiny bales. As a result, there are less emissions related to transportation.
2.5. Recycling process
There are two methods for PET bottle recycling: chemical recycling and mechanical recycling. The most popular method is the mechanical one since it doesn't release harmful substances from chemical agents that could endanger the environment.
The objective of mechanical PET recycling is to obtain clean PET flakes, which can be combined with virgin polymer or used directly to create new products.
2.6. Transformation into pellets
Upon arrival at a recycling facility, the compacted PET bottles undergo sorting and washing in order to remove any remaining materials, metals, labels, and adhesive. Then, they will go to the grinding process.
After cleaning , the PET bottles are placed in a grinder. To make the bottles suitable for recycling, the grinder reduces them to tiny PET flakes. After that, the PET bottles are fed into a machine that separates the flakes based on color and material. The purpose of this process is to ensure no non-PET materials continue through the recycling process.
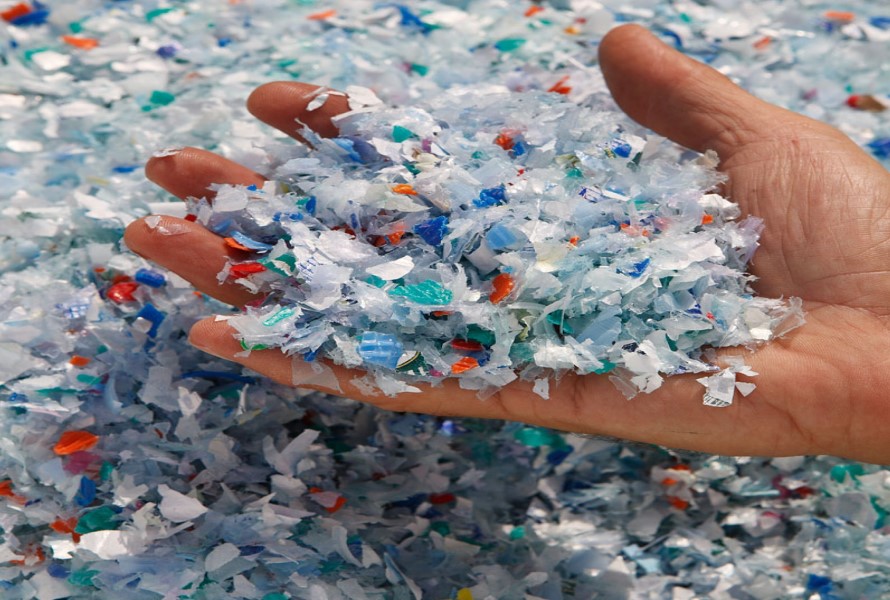
2.7. Washing and decontamination
The PET flakes will be cleaned, ground, and dried before being melted and formed into long PET plastic lines that will subsequently be divided into tiny pellets. Nitrogen is used to decontaminate the pellets so they are suitable for food packaging. It is feasible to repurpose PET for food and beverage packaging due to the decontamination process. It could also be applied to other kinds of bottle packaging, such as supplies for cleaning. This procedure is crucial since it ensures the safety of using PET in the bottle-to-bottle loop. It must function incredibly well to make it safe for food and drink once more.
2.8. Reformation and reuse
Manufacturers then send this recycled PET to be used in the packaging sector. Initially, the PET pellets are formed into preforms, which are then shipped to bottle manufacturers in preparation for being turned into new bottles. These manufacturers do not currently make their own preforms.
After being heated, these PET preforms are shaped and sized correctly. By doing this, the bottle-to-bottle loop is closed, guaranteeing packaging's continued sustainability.
3. EuroPlas - A trustworthy green material manufacturer
EuroPlas is the world's No. 1 filler masterbatch manufacturer, providing customers with unique plastic raw material solutions to help their factories optimize production costs and improve their competitiveness in the market. Moreover, we understand the importance of eco-friendly materials to contribute to the green world and encourage sustainable lifestyles. Therefore, we've created a series of biodegradable products used in different industries to help reduce the bad effects of plastics on the environment.
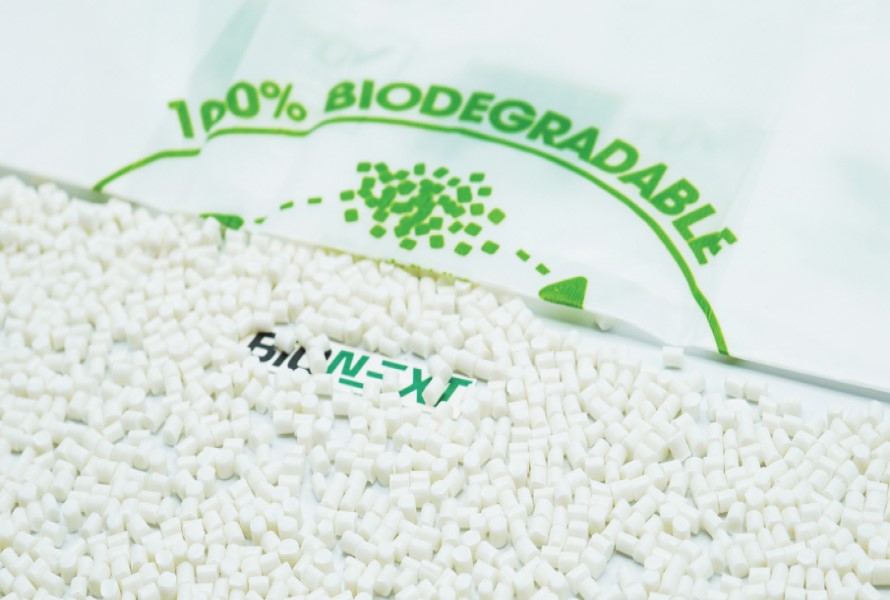
3.1. Bioplastic compound
Bioplastic compounds have many advantages. Unlike conventional petrochemical-based plastics, which are made from costly petroleum or natural gas, bioplastic compound is produced from renewable biomass sources, including polylactic acid (PLA) and Polyhydroxyalkanoate (PHA), plants and vegetables (corn, palm oil, potatoes), or fossil fuels like aliphatic-aromatic co-polyester (PBAT).
Using biodegradable and compostable compounds means you'll be less dependent on fossil fuels. Its life cycle assessment shows that it can decrease the carbon footprint in the manufacturing process. Furthermore, the bioplastic compound has better mechanical properties than unprocessed plastics, fewer toxins, and decomposes faster.
The material is widely used in different industrial sectors such as electronics, automotive & transport, household appliances, construction, fibers, and especially food packaging.
Acknowledging this fact, EuroPlas has introduced the Bioplastic compound, a green material solution with outstanding mechanical properties that enables end-products to be biodegradable within 12 months. We ensure your final products will meet all strict quality control criteria. With our bioplastic compound, you can have a full function in one material, which can be tailor-made based on your end-product requirements.
3.2. Bio filler
EuroPlas has more than 16 years of experience in providing sustainable solutions for the plastic industry. Bio filler (including BioMates 01, BioMates 02, and BioMates 03) is another cost-effective material solution for bioplastic end-products. It's a popular choice in the international market, including Europe and the USA. Our biodegradable materials not only save your production cost for bioplastic end-products but also improve their properties such as gloss, stiffness, etc. They can also act as anti-block and slipping agents in blown film, making them ideal for different applications.
If you’re looking for a green solution for your products, EuroPlas is ready to help. Contact us right now for the best price!