PET vs. PP: What Are The Differences?
PET vs. PP are two of the most widely used materials. Understanding their differences is crucial for selecting the right plastic for various applications. This article explores the in-depth comparison of PET vs. PP, helping you make informed decisions for your projects.
1. Overview Of PET And PP Plastic
PET stands for Polyethylene Terephthalate and is a thermoplastic polymer employed in the packaging of beverages and food. It is famous for being strong, clear, and recyclable, making it an eco-friendly choice.
Read more: What is Polyethylene terephthalate (PET)?
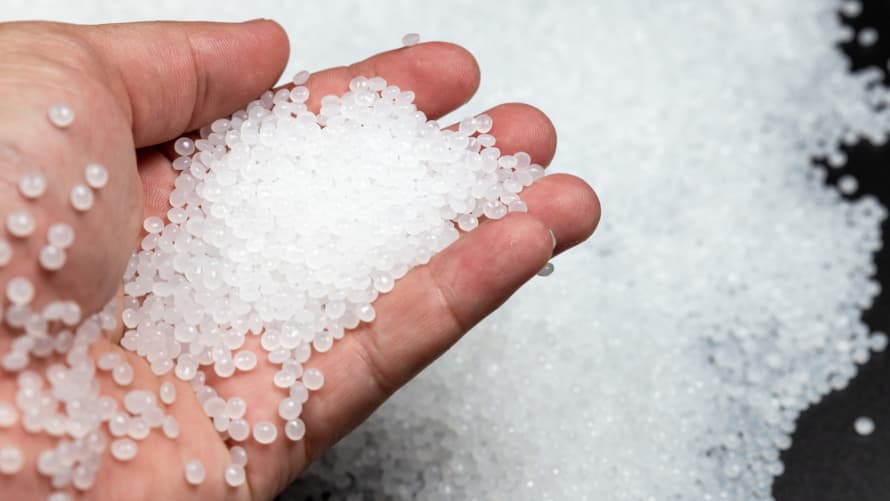
PET plastics
Polypropylene (PP) is another versatile thermoplastic known for its flexibility and resistance to chemicals. It is commonly used in packaging, automotive components, and textiles. PP offers excellent fatigue resistance and is also recyclable.
Read more: PP Plastic: Everything you need to know
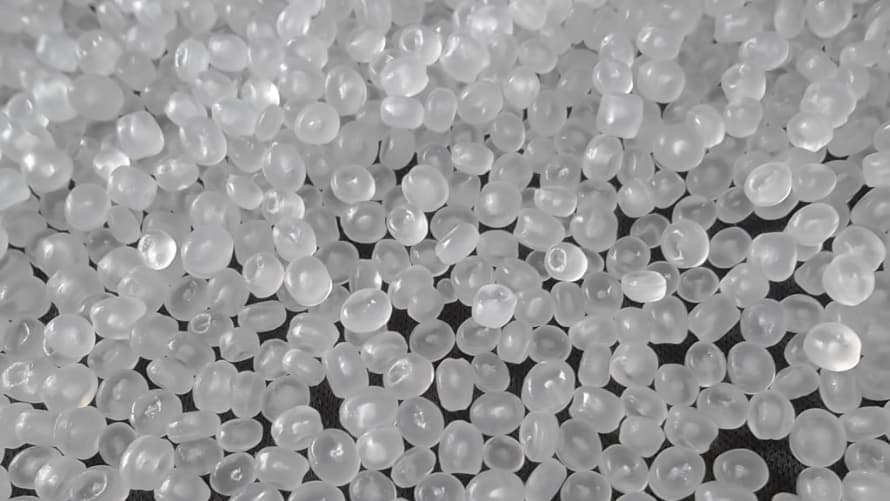
PP Plastic
2. PET vs. PP: Comparing Properties
When comparing PET vs. PP, it's essential to understand their distinct properties. Here’s an overview of their differences in properties:
|
PET |
PP |
Chemical resistance |
Moderate |
Excellent |
Temperature tolerance |
High (up to 70-80°C / 158-176°F) |
Moderate (around 160-170°C / 320-338°F) |
Mechanical strength |
High tensile strength and rigidity |
Good tensile strength; more flexible |
Clarity |
Clear and transparent |
Generally opaque |
Barrier Properties |
Excellent |
Moderate |
Recyclability |
Highly recyclable; widely accepted |
Recyclable; lower recycling rates |
2.1. The comparison of PET vs. PP in chemical resistance
PET has moderate chemical resistance and is well suited to packaging food and beverages. It has good resistance to water and some oil but is soluble in solvents like acetone and certain types of acids; thus it may not be suitable for use in environments where penetrants are used or when the chemical environment is unfriendly.
On the other hand, PP is chemically very inert and resistant to a broad range of chemicals such as acids, alkalis, and solvents. This makes PP an excellent material for use in laboratories, chemical processing, and packaging of highly aggressive or corrosive products.
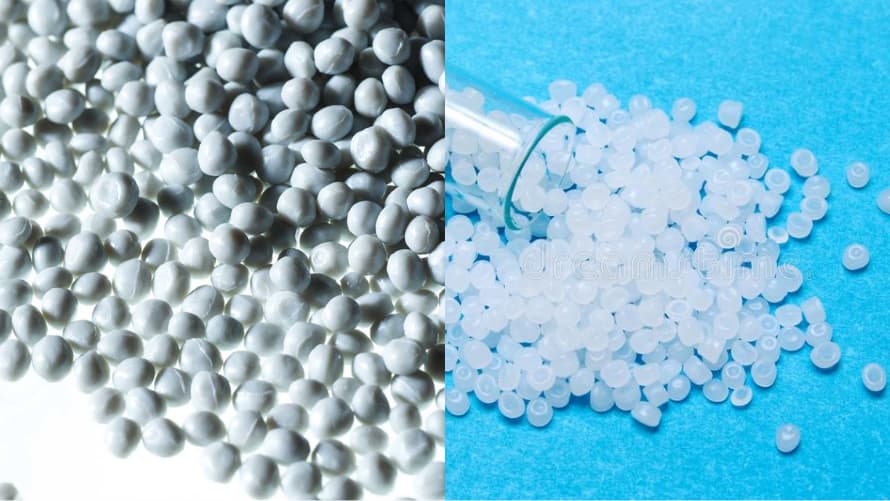
In the chemical resistance of PET vs. PP, PP has a better ability than that of PET.
2.2. The comparison of PET vs. PP in temperature tolerance
PET possesses relatively higher thermal stability up to 70-80°C (158-176°F). Due to its lower heat resistance, PET is best suited for products that do not require high-temperature exposure, such as beverage bottles, food packaging, and some consumer goods.
On the other hand, PP has a much higher heat resistance in most cases. It can tolerate 100-120° C (212-248° F). It is most often used for microwavable food storage, and auto-application, as well as industrial use.
2.3. The comparison of PET vs. PP in mechanical strength
The mechanical strength of PET has high tensile strength and rigidity, which has made it very hard. It is especially important for those uses where the container needs to have structural properties, as with bottles and pressure vessels.
Although PP gives good tensile strength, it is normally more flexible and robust to impact. For this reason, PP is well suited for applications that call for bending or flexing action as in the case of packaging films and automotive parts.
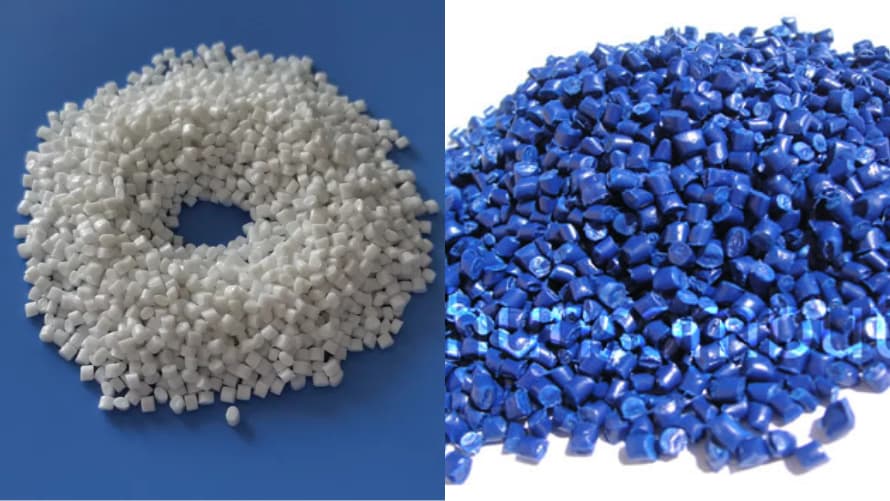
In the mechanical strength of PET vs. PP, PET tends to have rigidity while PP is generally more flexible.
2.4. The comparison of PET vs. PP in clarity
The PET is highly clear and transparent, which makes it more suitable for instance in the bottling of beverages and food packaging. This property enables the consumers to have sight of the contents vested in them, making it a material of choice in packaging.
On the other hand, the PP is normally translucent and is not very suitable for applications where the material needs to be visible. Additionally, PP can be colored but it does not establish the same measure of clarity as PET, making it unsuitable for aesthetic applications.
2.5. The comparison of PET vs. PP in barrier properties
In terms of barrier properties, PET excels with its excellent ability to resist air and moisture, helping to preserve the freshness and shelf life of food and beverages. This characteristic makes PET a popular choice for packaging where maintaining product quality is critical.
Despite being against water vapor, PP is not as efficient as PET in resisting air permeation. Thus, it will be rather useful to use PP when the barrier characteristics are not as crucial as in other cases.
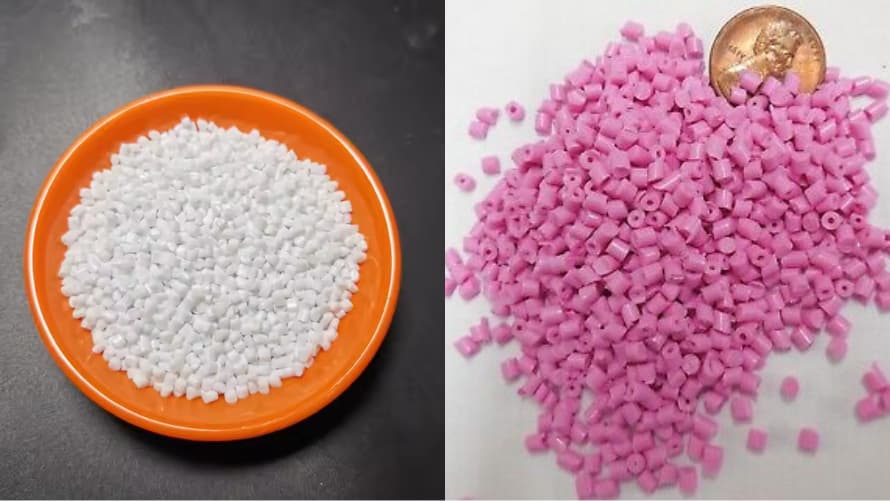
PET offers better barrier properties than PP.
2.6. The comparison of PET vs. PP in recyclability
PET is easily recyclable and bears the recycling symbol on its packaging as #1. They have stepped up recycling programs and their products are already in common use in many recycling initiatives thus countering sustainability efforts greatly.
PP is also a recyclable material. This has the recycling code #5, although its recycling often tends to be less than that of PET. However, the process of PP recycling and creating more efficient methods is not as popular as PET.
3. PET vs. PP: Pros & Cons
|
PET |
PP |
Pros |
- High clarity: Excellent transparency makes it ideal for beverage and food packaging.
- Strong mechanical properties: High tensile strength ensures durability under pressure, suitable for carbonated beverages.
- Recyclability: Highly recyclable and widely accepted, contributing to sustainability.
- Safety: Non-toxic and safe for food contact, ensuring consumer health.
|
- Excellent chemical resistance: Resists a wide range of chemicals, ideal for laboratory and industrial applications.
- Flexibility and impact resistance: Absorbs impacts and bends without breaking, suitable for packaging and containers.
- Cost-effective: Generally cheaper to produce, making it budget-friendly for large-scale manufacturing.
- Good fatigue resistance: Withstands repeated flexing, ideal for automotive parts and living hinges.
- Lightweight: Lower density reduces weight, advantageous for various applications.
|
Cons |
- Limited chemical resistance: Vulnerable to certain solvents, restricting industrial use.
- Heat sensitivity: Deforms at high temperatures, limiting hot-fill applications.
- Environmental concerns: Potential contribution to plastic pollution if not properly recycled.
|
- Lower clarity: Opaque appearance limits use in transparent packaging applications.
- Recycling challenges: Faces lower recycling rates compared to PET.
|
4. PET vs. PP: Comparing Applications
|
PET |
PP |
Applications |
- Beverage packaging: Commonly used for bottles of carbonated drinks, juices, and water due to clarity and barrier properties.
- Food containers: Ideal for trays, jars, and takeout containers; safe for hot-fill applications.
- Textiles: Used in clothing and home textiles; known for durability and resistance to wrinkles.
- Thermal insulation: Utilized in insulation materials for electronics and appliances due to thermal stability.
- Cosmetic packaging: Popular for packaging personal care products due to its aesthetic appeal and safety.
|
- Food packaging: Widely used for containers, wrappers, and bags; suitable for both dry and wet food.
- Automotive parts: common in components like bumpers and interiors.
- Medical supplies: Used for syringes and lab equipment; capable of sterilization and resistant to chemicals.
- Household items: Found in storage containers, kitchenware, and furniture.
- Textiles: Employed in non-woven fabrics for products like diapers and hygiene items; flexible and strong.
|
5. Which Plastic Should You Choose?
When deciding between PET vs. PP, it's essential to evaluate your specific needs and the context in which the material will be used:
5.1. Performance needs:
If your product requires high clarity, strength, and excellent barrier properties, such as in food and beverage packaging, PET is often the superior choice. Its rigidity and resistance to moisture make it ideal for maintaining product integrity and extending shelf life.
Conversely, if your application demands flexibility, heat resistance, and the ability to withstand various chemicals, PP may be more suitable. This makes it an excellent choice for items like containers that will be microwaved or exposed to harsh cleaning agents.
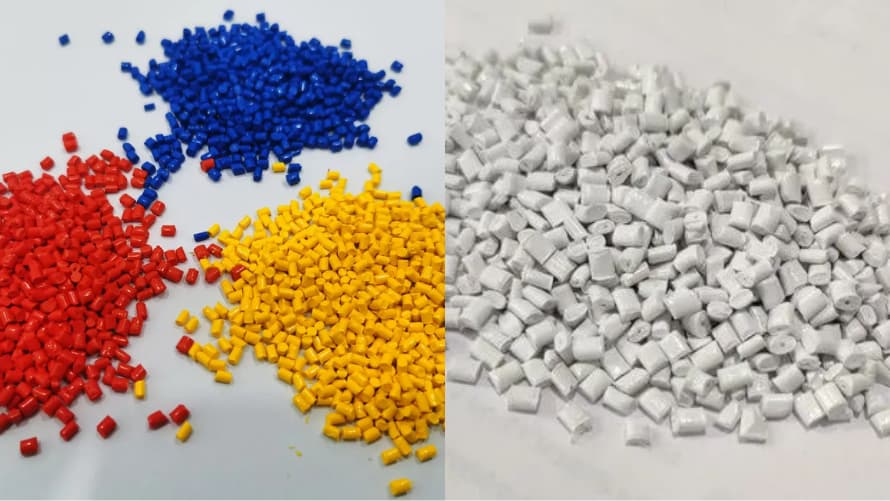
PET is suitable for applications related to rigidity while PP is better for applications demanding flexibility.
5.2. Environmental considerations:
Although both materials have recycling potential, PET typically has a better recycling infrastructure than PP, making it more environmentally friendly in many areas. If sustainability is a primary concern, consider opting for PET.
5.3. Cost and availability:
PP is often cost effective for large scale applications due to its lower cost and easier availability. PET, although potentially less durable, has performance advantages that can offset the cost benefits, especially for high value products.
Consider your budget when choosing the right one between PET vs. PP for your application.
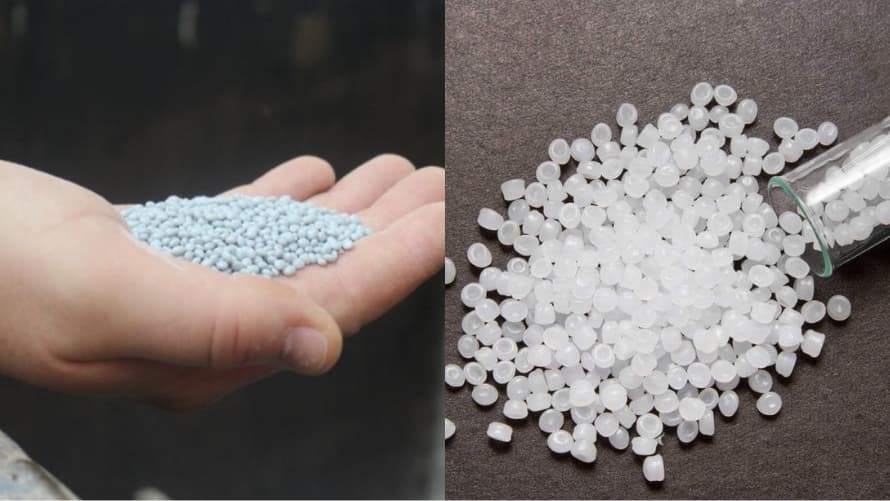
PP is generally cheaper than PET.
6. Conclusion
PET vs. PP have distinct properties and advantages that make them ideal for different applications. Understanding their differences can help you make informed decisions based on your specific needs and environmental considerations.
7. About EuroPlas
EuroPlas is a leading provider of high-quality plastic solutions, specializing in various materials. With a commitment to sustainability and innovation, EuroPlas offers products tailored to meet the diverse needs of industries worldwide.
At EuroPlas, our PP materials are designed for excellent heat resistance and toughness, making them perfect for various applications. We offer a range of PP products, including:
For more information and tailored support to meet your specific needs, please don’t hesitate to contact us!