PLA vs. ABS
Many manufacturers are interested in the competition of PLA vs. ABS as they are popular materials used in various industrial fields. The only similarity between these two thermoplastics is that both can be softened through the heating process before the next steps of cooling and hardening. Yet, they are different in many aspects, affecting their final performance in the final products. All manufacturers acknowledge the importance of choosing the right material to have great final products' quality, functionality, and durability. Thus, let's delve into the details to understand what makes these two polymers differ from each other! Scroll down for more!
1. PLA vs ABS
1.1. PLA vs ABS Plastic - What Are They?
ABS, short for Acrylonitrile Butadiene Styrene, is a thermoplastic made from petroleum. Its 3 monomers (acrylonitrile, butadiene, and styrene) make the material tough, strong, and heat resistant, leading to its popularity in various applications such as electronic enclosures, automotive components, toy production, etc.
Read more: ABS plastic - Everything you need to know
On the other hand, PLA, or Polylactic Acid, is derived from renewable resources such as corn starch, tapioca roots, and sugarcane. Thanks to its biodegradability, it's highly preferred in many industries that have high requirements for an eco-friendly material.
Read more: PLA masterbatch - the future of the plastic industry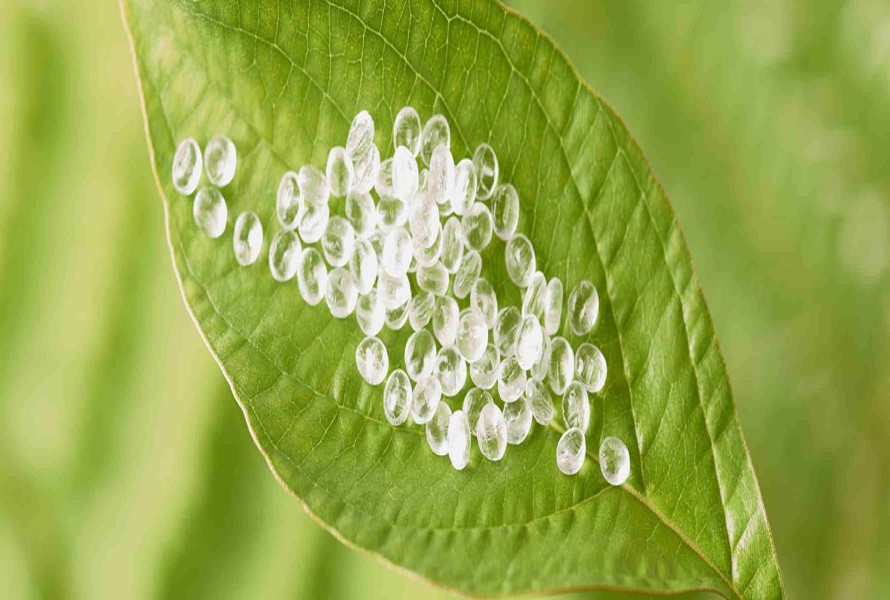
1.2. Comparing Properties
1.2.1. Strength and Toughness
PLA has better tensile strength, which is 50% more than that of ABS (48 MPa and 32 MPa, respectively). It means PLA is stronger and can withstand more tension. Besides, the material also has minor gains in elastic modulus. The stiffness value of PLA is 2.54 GPa, while the figure of ABS is 2.54 GPa.
In terms of toughness or resistance to impact, ABS totally overwhelms PLA with the result of 101 J/m in the Izod impact (notched) test and 291 J/m in the Izod impact (unnotched) test. (Meanwhile, PLA produces 27 J/m and 192 J/m, respectively.) It indicates that ABS has a better ability to absorb energy during plastic deformation and can hardly be shattered under impact. This prized impact-resistant ability of ABS makes it an ideal choice for producing car bumpers.
Talking about PLA vs. ABS density, the former has a higher density than the latter. It means that if you make the two parts from the two materials with the same geometry, the PLA part will be heavier than the ABS one.
1.2.2. Thermal Properties
The Glass Transition Temperature (Tg) of PLA is 63 °C, while the result of ABS is almost double that (105.2 °C), meaning PLA is easier to melt than ABS.
In addition, Heat Deflection (HDT) is another value manufacturers should be concerned about. Here is the HDT test result for both materials:
|
PLA |
ABS |
Heat Deflection (HDT) @ 66 psi |
53 °C |
103.8 °C |
Heat Deflection (HDT) @ 264 psi |
51 °C |
99.9 °C |
Based on the table above, we can see that ABS is the winner since it shows better distortion resistance under a given load at an elevated temperature.
1.2.3. Warping
Due to the higher Glass Transition Temperature (Tg), ABS is more at risk of warping since there's a greater change in the temperature range between the extrusion nozzle and the print environment.
On the other hand, when you do home printing, PLA will not warp if the room air is fairly still. However, the part can be bent due to sudden wind. Therefore, it is highly recommended to use brims and rafts in the slicer program for the part anchored to the bed while it cools.
1.2.4. Applications
Based on each material's specific properties, manufacturers will consider which one meets the final product requirements and delivers better performance. PLA is easy to print but weaker, more fragile, and sensitive to high temperatures; thus, it's more suitable for decorative elements and toys and preferred to be used by new users.
ABS, though it's more difficult to print, is tougher and better resistant to mechanical and thermal stress. Therefore, it's more commonly used in producing toolings, gears, or prototypes.
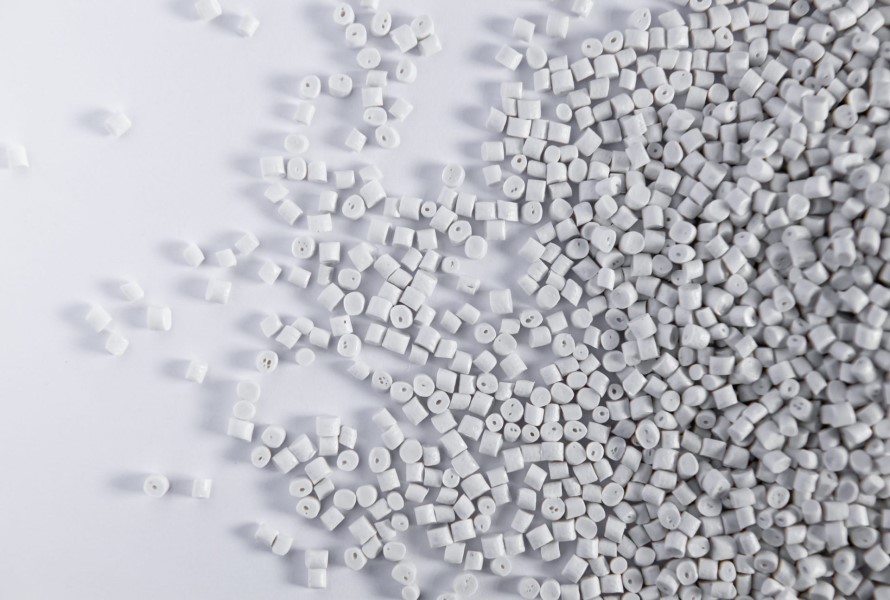
1.2.5. Environmental Impact
Since PLA is made from renewable resources and generates fewer greenhouse gas emissions during production, it's a more eco-friendly choice. One of the biggest advantages of PLA material is that it is biodegradable. I can break down into carbon dioxide, water, and biomass within 2-3 months if under the proper conditions. In case of low humidity and temperature falls below 50°C, the degradation process will be around 6 to 24 months (or more).
On the contrary, ABS is produced based on non-renewable resources such as crude oil and natural gas, creating more carbon footprints for the environment. Plus, it's non-biodegradable and requires several hundred years to decompose.
However, both materials can be recycled to reduce the impact of these thermoplastics on the environment.
1.3. PLA vs. ABS Price
A spool of filament made from either PLA or ABS has a similar price of around $18 to $50 (depending on the quality). However, their raw material cost is probably different, in which the prime cost of producing ABS can be slightly cheaper than making PLA. That's why ABS is more common in injection molding for creating small details such as Lego toys or interior car components.
Keep in mind that the difference in prices of both materials also depends on various factors such as brand, color, diameter tolerance, shipping fee, etc. You can find PLA is more expensive in some cases and vice versa, and that's totally normal.
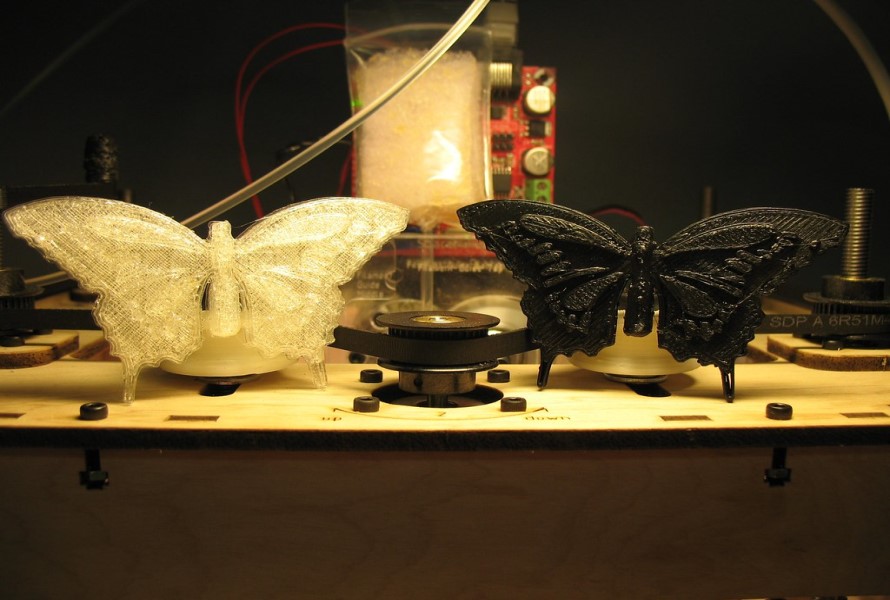
2. EuroPlas - Supplier of All Needs
EuroPlas is one of the leading brands in the masterbatch field. Once you come to us, all your requests will be satisfied as we have a wide range of products to offer, and they are customizable to meet the requirements of your final products.
For example, if you want to choose the ABS engineering plastic compound, you can have a look at our lists of products:
ABS Products |
Description |
Outstanding Features |
ABS Glass fiber compound |
It's the combination of ABS resin, glass fiber, and suitable additives |
It has higher strength, stiffness, and dimensional stability |
ABS Antistatic compound |
It's a combination of ABS resin and an antistatic additive. |
Prevent surface static, thus minimizing the risk of electrostatic discharge and ensuring safety during processing and product use. |
ABS flame retardant compound |
It is made of ABS resin and flame retardant additives in different fire resistance levels according to UL94 standards: V0, V1, and V2. |
It slows or prevents the spread of flames in the event of a fire. |
Or, if you're looking for a more eco-friendly solution, you should not miss our Bioplastic compound and Bio Filler. EuroPlas Bioplastic compound is biodegradable within 12 months after use, allowing you to pursue sustainable development. Our BiONext biodegradable plastic granules have high hardness, excellent impact strength (injection molding and extrusion products), and good elongation (blown film products) with a glossy, beautiful surface and easy machining ability. Thus, your final products can achieve both quality and aesthetic requirements.
On the other hand, our Bio Filler is a well-known, cost-effective material solution for bioplastic end-products. It can improve the finished products' properties, such as flossness, firm hardness, etc., and helps businesses save production costs. It's an ideal choice for producing environmentally friendly products, including biodegradable packaging, injection molding, and single-use plastic extrusion.