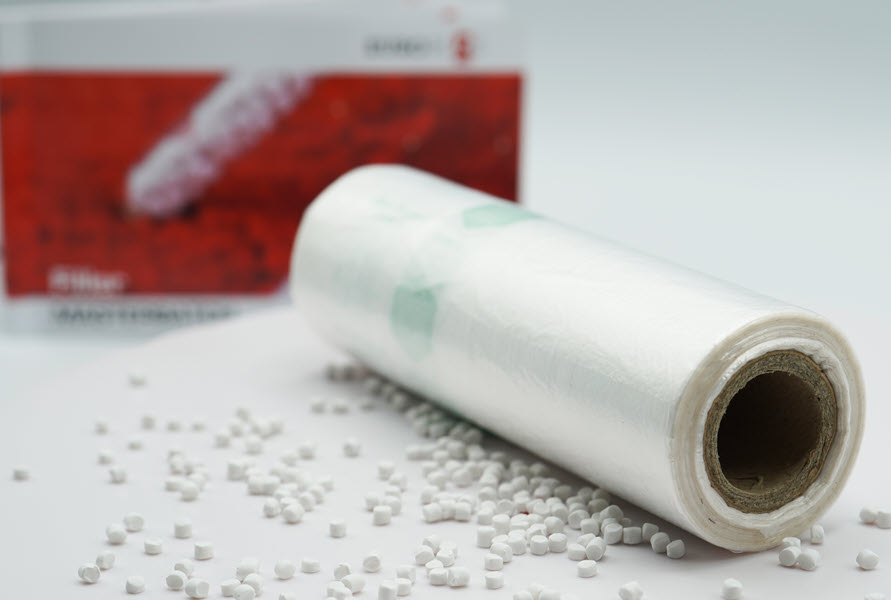
In the last post, we provided you with detailed information about plastic extrusion and its manufacturing process. Today we’ll dig deeper into one type of this method - blown film extrusion. Stay tuned and enjoy!
1. What is blown film extrusion?
Blowing film is a system producing continuous semi-finished products. The blown film extrusion complex is applicable for creating semi-finished products which are thin film rolls made from plastic resin and additives. The system includes extruder components, blower components, and a winding system.
This method is the best fit for producing food packages, shopping bags, and continuous sheeting.
2. The blown film extrusion process
2.1. Basic blown film line
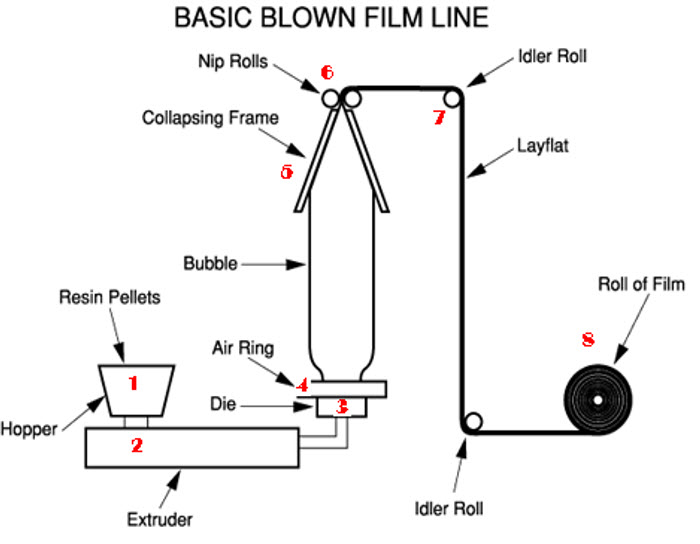
- Hopper: This is where people pour granular pieces of plastic into the extruder. It stores the plastic and prepares for the next process stage.
- Extruder: It’s the most pivotal part of the line. An extruder includes a motor, gearbox, screw, cylinder, and cast heaters.
- Die: The die consists of many layers of molds joined together.
- Air ring: This is where the wind cools down and shapes the product.
- Collapsing frame: It presses the film into a flat form.
- Nip rolls: It pulls the film from the collapsing frame.
- Idler roll: It pulls and stretches the film.
- Roll of film: It rolls the film into the core.
2.2. Blown film extrusion process
- Step 1: The plastic beads are filled into a hopper. The hopper then delivers the plastics into a heated barrel with a screw. This is where the resin is heated and turned into molten materials.
- Step 2: The screw will push the molten material to the end of the barrel. Plastics will be extruded through a die. In blown film extrusion, there are several types of die, but the most common one is annular, which is a simple circle.
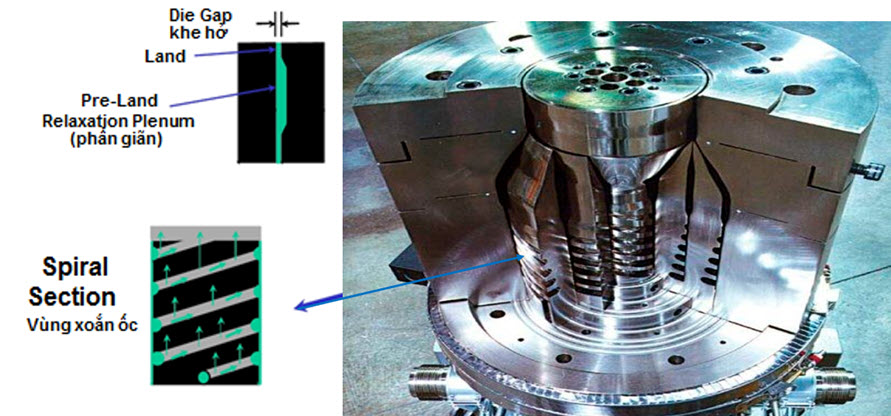
When the molten material enters the die, the air will be injected via a hole in the die center to inflate the plastics into a thin tube radially.
- Step 3: Afterward, the hot tube film will be cooled with high-speed air, and pulled upward by the nip rollers.
- Step 4: As the tube reaches the nip rollers, at the top of the line, the film is now cool enough to flatten and is then referred to as lay-flat or collapsed tubing. The film is transported downstream by rollers for further processing and eventually wound into rolls.
3. Blown film troubleshooting
When processing plastic using the blown film extrusion method, you should remember:
- Die: If the gap of the die is uneven, the film thickness is uneven.
- Temperature: If there is not enough heat, the plastic will not melt completely. But when overheated, it will burn, creating a film with many black spots.
- The higher the screw speed is, the thicker the film will be.
- The faster the roll is, the thinner the film will be.
- The larger the airflow is, the larger the film specification will be.
- The higher the cooling level, the quicker the film will be cooled down. However, the film is less crystallized and the mechanical properties are reduced.
3.1. Poor dispersion
The causes of this problem may be:
- Using out-of-date fillers, materials are blocked when topping the machine.
- Using the inappropriate taical. Remember the level of filler dispersion is HDPE > LLDPE > LDPE.
- Mixing the desiccant with the materials.
- Machine: unstable temperature, equipment wear out during long use…
Solutions:
- Reduce the melt temperature, or increase the extruder barrel temperatures
- Control the thermocouple installation and accurate heater control
- Replace the worn or damaged extruder screw/barrel…
- Remove foreign contamination, angel hair, and fluff,...
3.2. Sharkskin
This is the phenomenon of films with thinner spots appearing on the film surface. It reduces film uniformity, mechanical properties, and aesthetics. The cause of this problem is that the raw material (usually the fillers) contains too many substances that are vaporized or decomposed into volatile substances under processing conditions (usually steam). Solution: - Increase the melt temperature - Increase the die lip temperature - Activate die lip heaters - Increase the die gap - Add PPA (polymer processing additive)
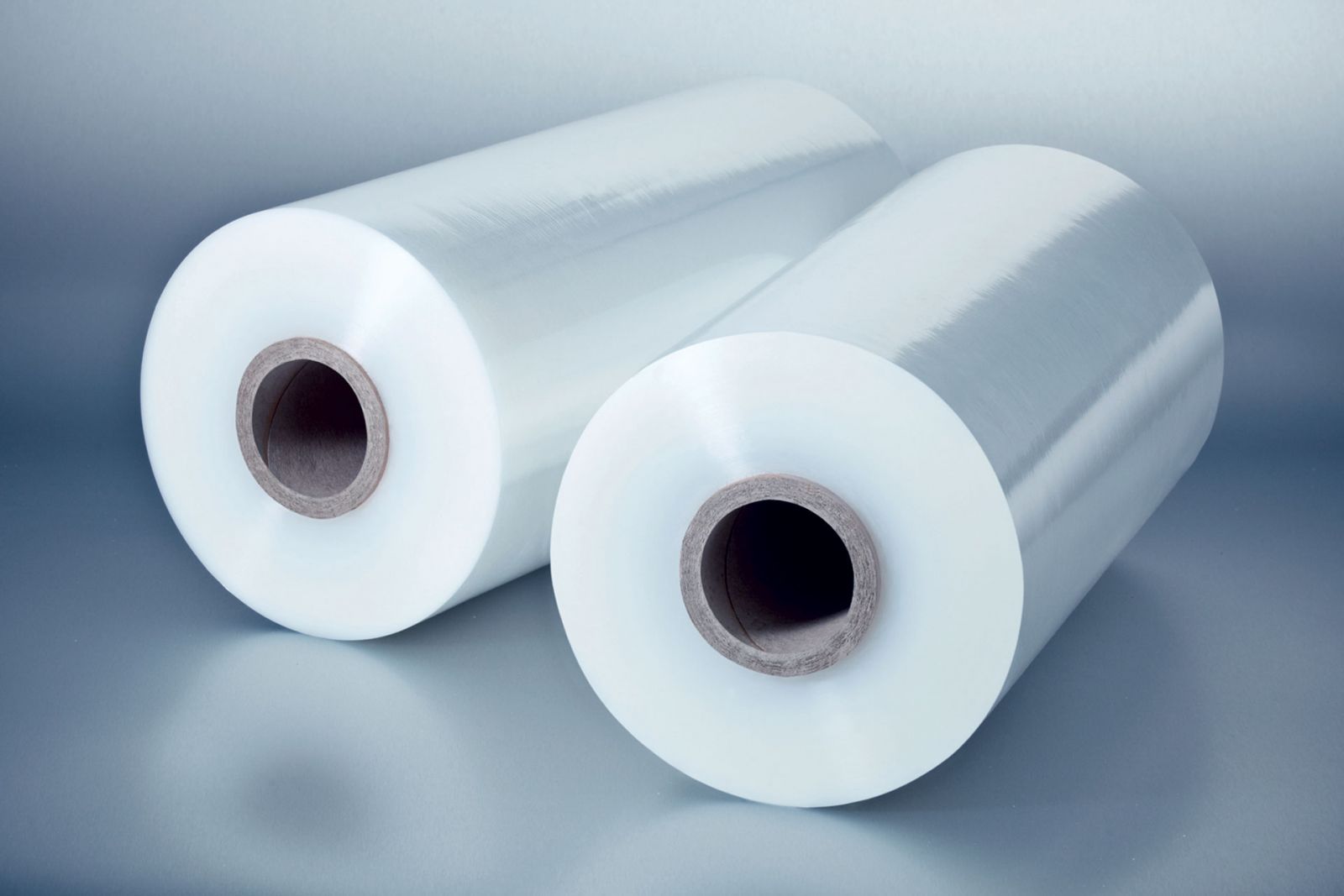
3.3. Film lines
After a long time using, there is a black or yellow burnt layer around the extruder. It affects the quality of the film and causes film lines.
Solution:
- Clean up die lips at localized lines
- Re-gap the die and clean the gap
- Check the internal/external air rings for proper centering, blockages, leaks, and localized high/low air velocities
- Ensure the die, collapsing frames, nip roll are centered.
- Check to see if all transport rollers rotate freely; do non-uniform tensions exist?
- Remove external influences such as drafts
3.4. Milky areas
Milky areas are caused by the use of incompatible materials (usually because the proportion of filler is too high) or contamination.
Solution:
- Identify where the contamination is occurring and eliminate it
- Clean resin material handling system, hopper, and dryer
- Consider the appropriate fillers
European Plastic Company (EuP) is the world’s largest filler masterbatch manufacturer located in Vietnam. Our filler masterbatch is a quality-proven product that satisfied thousands of customers in +85 countries all around the world. This product is a cost-effective solution and helps you enhance many properties of your final products.
If you want to get more details about our PP filler masterbatch, please fill in this form or contact us via email/phone number. Any questions and product inquiries are welcome!