Plastic extruders are extremely important components throughout the production process of plastics such as: HDPE, PVC, PP, PET, ABS. However, many people are hearing about this machine for the first time, so EuroPlas will explain to you in detail all the information, functions and applications of plastic extruders in the material production industry. Refer to the article below!
1. What is a plastic extruder?
A plastic extruder is a device that creates plastic pipes, plastic films, plastic floors, etc. using extrusion compression technology. The main function of the machine is to melt the plastic mixture in a very short time to serve the product shaping process. The mixture will rest and gradually maintain its solid form according to the specified extrusion mold.
Without a plastic extruder, solid materials as well as plastic granules of all kinds cannot be shaped in a short time. In particular, the plastic extruder can be compatible with a variety of different input materials such as: PP, PE, PET, ABS, PVC or POM plastic. Not only can it load heavy materials, the machine's heating time for the plastic mixture is also very fast.
Therefore, manufacturers can both save operating costs and provide quality and safe plastic products to consumers. Thanks to this equipment, the world plastic industry has also made great progress in many fields from recycled plastic to high-quality bioplastic.
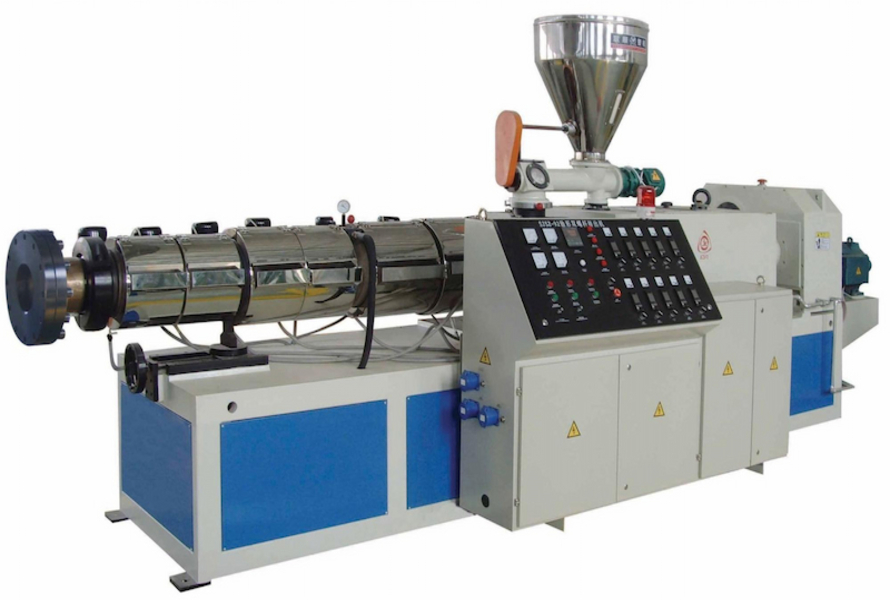
2. Classify types of plastic extrusion machines
Currently, plastic extruders are divided into two popular types on the market. These are: Single screw machine (1 screw machine) and twin screw machine (2 screw machine). Basically, materials in the form of granules and flakes will be suitable for single screw machines. Meanwhile, twin screw machines will be used more in powder or mixed form.
2.1. Single screw plastic extruder
The specific raw materials in flake form will be PP, PE, PET, PS plastic. ABS, PA, PVC, EVA, many types of recycled plastic and color mixing granules. The gear reducer of single screw plastic extruder is capable of stable operation and has low noise characteristics because they use the torsion of the gear to perform the actions of heating and shaping the plastic mixture by pressure.
In particular, plastic products created from single screw extruders will be more stable and dense. Because the specialized design will help the single screw plastic extruder eliminate water vapor, natural exhaust and foot gas. Therefore, the product always ensures safety indicators for consumers' health and has better quality than other plastic extrusion machines.
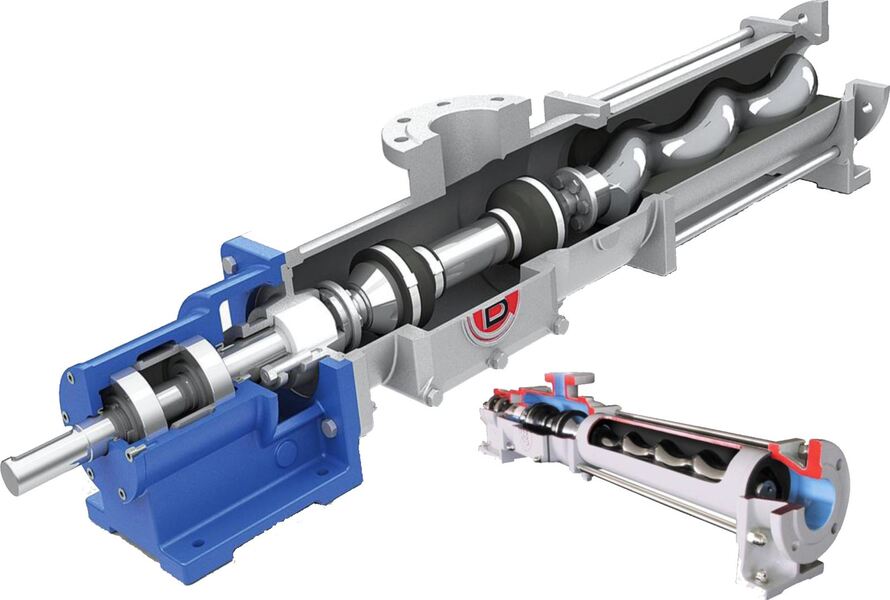
2.2. Twin screw extruder
The two-screw extruder includes a variety of screw and barrel designs, multiple screw configurations with different functions can be set up according to the requirements of the entire production process. Therefore, a twin-screw extruder can ensure the process of conveying, compressing, mixing, cutting, heating, cooling, shaping.. etc.
The parallel twin screw extruders are specially designed for PVC processing. The purpose of this design is to increase efficiency and save costs thanks to high performance and outstanding product quality. With a diverse product portfolio based on modular production lines, we are able to provide highly efficient and highly efficient production solutions for specific applications.
Therefore, the twin screw plastic extruder will have some outstanding advantages as follows:
-
The machine's screw and barrel parts are cooled by air, so they have stable thermal balance
-
Like single screw plastic extruders, twin screws are also compatible with a variety of formulas and materials, creating flexibility for the processing process.
-
Minimize investment costs thanks to longer operating life of the plasticizer and high performance with good product quality.
3. Structure and operating principle of plastic extruder
To understand more details about plastic extruders, EuroPlas will introduce to you their structure and operating principles!
3.1. Structure of plastic extruder
Basically, the plastic extruder has 7 main parts with each specific function as follows:
-
Motor
-
Gearbox
-
Input funnel
-
Cylinder: They are made from steel, so they have very high hardness. Standard thickness of cylinder is from 10 - 15mm. Steel material also helps the cylinder withstand high temperatures during the fusion process.
-
Screw: An important part whose main task is to receive, mix and convey materials to the compression area. At the same time, they will inject liquid plastic into the shaping head
-
Heating part: The system is capable of adjusting the melting temperature from 200 - 300 degrees Celsius and provides the highest accuracy. Without this part, the plastic extruder cannot heat and balance the temperature during the processing process.
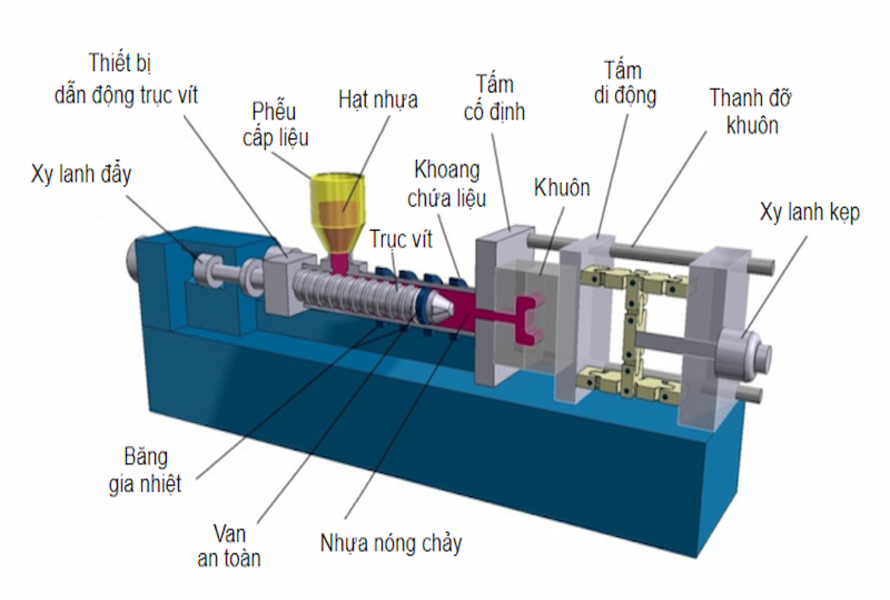
-
Shaping head: The part that determines the shape of the liquid plastic mixture after a short time of melting. Currently, shaping heads have a variety of designs, for example: tube shape (creating cylindrical products), hole shape (round fiber products, flat fiber products,...) and slot shape (products with flat membrane, flat sheet,...)
3.2. Operating principle of plastic extruder
The basic goal of a plastic extruder is to melt the material at a temperature of 200 - 300 degrees Celsius and shape the liquid material mixture to create the highest quality finished product. Next, EuroPlas will introduce in detail the operating principle of the plastic extruder, including 4 main steps as follows:
-
Step 1: All plastic materials, additives and colorants will be thoroughly tested from surface to structure before being put into the plastic extruder.
-
Step 2: The materials will be fed into the feed throat and moved through the extruder area. At this time, the machine's temperature starts from 200 degrees Celsius and gradually increases so that the plastic material is melted into a mixture.
-
Step 3: During that time, the water will be heated by the screw. Meanwhile, the plastic extruder system is always maintained at a stable and cool temperature level throughout the processing process with the support of fuel oil.
-
Step 4: Next, the material will be moved to the end of the screw. The liquid resin mixture will have all air bubbles removed and impurities filtered by a vacuum pump at the end of the machine.
-
Step 5: In order for the product to form the correct shape, it will be transferred to the cooling stage. In particular, the products will continue to be cooled to ensure they retain their structure and shape for long periods of use.
As EuroPlas mentioned above, plastic extruders are compatible with a variety of the most popular materials today such as: PP, PET, PE, PS, ABS, PA, PC, PVC, POM, PMMA, EVA, recycled plastic and color mixing granulation. Therefore, they become irreplaceable equipment in the plastic industry and play an important role in production fields such as: Flat thin film production, packaging production, plastic bottles or plastic cans.
Furthermore, EuroPlas will also give you some tips on choosing a quality plastic extruder. First, check all 7 main parts of the machine. EuroPlas recommends that you remove the shell of the machine to conduct a detailed check of each engine. You should not buy in advance or make a deposit.
Instead, you must go to the production area or dealer to check the machine directly. Besides, it is also very important to fully consult the warranty policies as well as costs from many suppliers, they not only help you save costs but also own a quality machine. Choosing a single or twin screw extruder depends on the needs and production materials of the business.
4. Introduction to EuroPlas
European Plastic Company is a reputable address specializing in providing the leading bioplastic products, plastic additives and compound engineering plastics today. We have a total of 7 factories with a scale of tens of hectares in 6 provinces including Ha Nam, Yen Bai, Hai Phong, Nghe An, Long An and Ho Chi Minh.
With a modern production line system, EuroPlas's annual production capacity reaches about 0.6 million tons, enough to meet large quantity orders from all over the world. We are proud to be a trusted partner of thousands of factories in more than 85 countries globally.
EuroPlas is committed to providing high quality products, reasonable prices and excellent customer service. EuroPlas has a team of experienced and professional staff, always ready to support customers in all matters.
EuroPlas is a great choice for businesses looking for high quality bioplastic products, plastic additives, and engineering plastic compounds, reasonable prices, and excellent customer service.
The above article has introduced detailed information related to plastic extrusion machines. Plastic manufacturing facility owners need to pay careful attention to owning the best equipment and providing the best quality products to the market.