On the market today, there are many types of plastic pipe products that differ in size, shape, and purpose of use. Each type of pipe will be applied to a different plastic pipe manufacturing process by the characteristics to optimize costs, productivity and operation. Each plastic pipe production process has its advantages and disadvantages. EuroPlas will review some popular methods currently used to produce plastic pipes.
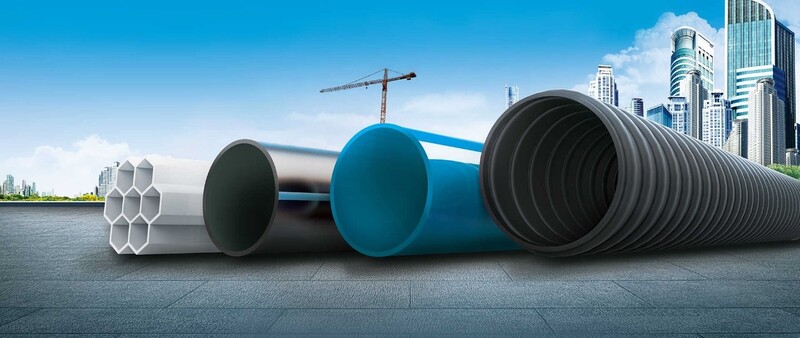
Some types of plastic pipes are used in industry
1. Which process is used to manufacture plastic pipes?
How to make plastic pipe is a question proposed by many people. Today, along with the development of technology, more and more methods of manufacturing plastic pipes have been born to meet the needs of many fields. The more modern the plastic pipe production line, the better the quality and cost of products will be.
1.1. Plastic pipe extrusion
Extrusion is the most commonly used method today to create plastic pipes. The plastic pipe extrusion line undergoes five main steps as follows:
- Step 1: Raw plastic granules and additives are put into the hopper. The plastic will gradually go from the hopper to the barrel.
- Step 2: A rotating screw in the barrel will mix the plastic with the additives and push it all forward. At the same time, the material chamber will heat and melt the plastic into a liquid.
- Step 3: The breaker plate will filter the liquid plastic. This sheet helps to remove any foreign material from the liquid plastic. The liquid then passes through a feed pipe before entering the mold.
- Step 4: Liquid plastic is pushed into the mold to fix the desired shape of the plastic tube
- Step 5: Once out of the mold, the plastic pipe will be cooled immediately to shape the tube permanently
Related:
- Plastic blown film extrusion - the ultimate guide
- Slip and antiblock additives for extrusion industry
- Types of plastic extrusion and its manufacturing process
A model plastic pipe extrusion line
Advantages:
- Low production cost
- Ease of operation control
- Consistent product quality
- More durable than other methods
- Can produce continuously in large quantities
Disadvantages:
- Lots of leftover plastic
- The plastic pipe extrusion machine system is quite cumbersome and difficult to automate
- Operational skills affect product quality
1.2. Plastic pipe rotational molding
Rotational molding is a plastic fabrication method used to manufacture hollow parts, including plastic pipes. The basic steps of this plastic pipe production process of this method have four stages:
- Mold charging: A predetermined amount of plastic material is loaded into the mold
- Mold rotation and heating: The mold is heated to melt the plastic, then begins to rotate sequentially around the axes. When rotating the molten plastic will stick to the mold wall, the process continues until all the plastic adheres to the mold wall
- Mold cooling: During the rotation, the mold will be cooled until the product solidifies completely
- De-moulding of the final product: The finished product will be taken out from the mold
A kind of rotational molding machine
Advantages:
- Leftover plastic can be reused for production
- There is no restriction on the shape and size of the mold, so it is possible to produce plastic pipes with complex shapes and large sizes
Disadvantages:
- The process of molding a product is quite long, so it cannot be continuously produced in large quantities like other methods
1.3. Plastic pipe injection molding
Plastic pipe injection molding is a method of forming a plastic pipe through two stages of melting plastic and pressing it into a mold to create a shape for the tube. The basic steps in an injection molding cycle include clamping, injection, cooling, and de-molding.
- Clamping: The mold is prepared for one cycle by clamping the two halves
- Injection: The granules that have been heated into a liquid are injected into the mold through a nozzle
- Cooling: The melting plastic will be cooled so that the plastic turns into a solid state and fixes its shape
- De-molding: When the product is cooled, the injection mold is opened, and the product is ejected from the mold. The mold will clamp and prepare for the next cycle
A PVC plastic injection molding machine
Advantages:
- Can make products with many details
- High precision
- Stable product quality
- Fast molding cycle
Disadvantages:
- High production cost
- Complex injection mold structure
- The molding process must be continuously monitored, or it will easily affect the product quality
2. Are you looking for material solutions for your plastic pipes?
European Plastic Joint Stock Company (EuP) is the world's largest
filler masterbatch manufacturer based in Vietnam. We supply a variety of different materials for the production of plastic pipes. All materials of EuP are tested for quality and trusted by thousands of customers around the world. Using our materials is the perfect solution to complete your company's plastic pipes by saving costs, increasing productivity, and improving the characteristics of plastic pipes.
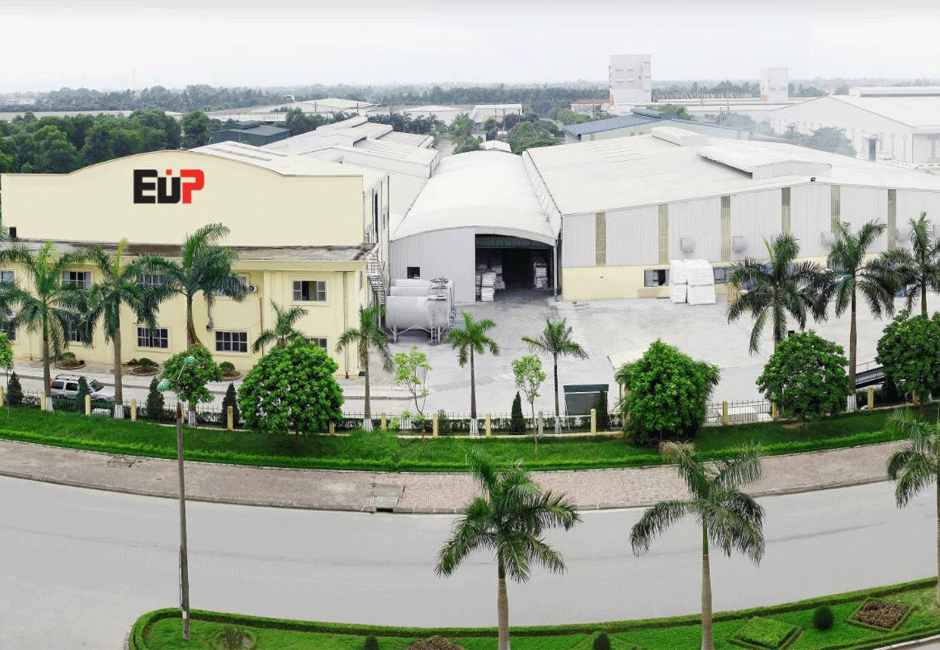
EuP factory
2.1. Competitive price
In the plastic pipe manufacturing industry in particular and the plastic industry in general, filler masterbatch has long been widely used because of the great benefits it brings. Filler masterbatch partially replaces input materials, which allows manufacturers to reduce production costs to the maximum and increase competitiveness compared to competitors.
EuroPlas offers a wide range of filler masterbatches including PE filler masterbatch, EFPE 1001 filler masterbatch, PP filler masterbatch, EFPP filler masterbatch, HIPS filler masterbatch, transparent filler masterbatch, etc. These products are suitable for each purpose of different plastic pipe productions. Filler masterbatch is a cost-effective solution for enterprises producing finished plastic pipes.
2.2. Enhance productivity
The main ingredient in the filler masterbatch is CaCO3 which effectively reduces the pressure of plastic to melt when molding thanks to the good thermal conductivity of CaCO3. Thereby, helping to improve productivity by saving fuel and shortening the production cycle.
Another property of CaCO3 is its good stabilizing ability which helps to improve bubbles in the plastic pipe production process.
2.3. Improve pipe properties
Currently, there are many different types of plastic pipes such as PVC, PPR, HDPE, etc., which are widely applied in many fields such as industry, agriculture, wastewater, healthcare, ... and daily life.
In making plastic pipes, only using raw plastics can not guarantee hardness, durability, toughness, heat resistance, impact resistance, and many other outstanding properties. Therefore, in all methods of the plastic pipe manufacturing process, it is necessary to add plastic additives to improve the necessary properties of the pipes.
Plastic additives from Europlas
In addition,
plastic additives significantly increase the aesthetics of the product by improving and adjusting the gloss and opacity. At the same time, these additives increase the ability to print on the surface of the finished plastic pipe.
Various additives provided by EuroPlas such as desiccant, flame retardant, anti-aging additive, anti-static additive, anti-UV additive, and anti-blocking additive, etc., will help the finished pipe product improves the following outstanding properties:
- Good heat resistance
- Withstands sunlight and UV rays for a long time
- Durable
- Resistant to fire and high temperature
- Flexible flexibility
- Withstands high loads
- Hard to deform and crack
- No leaks of water and steam
- Long life of plastic pipes, which can be up to 50 years
Please feel free to contact EuroPlas via email/phone number or fill in
this contact form for more advice. EuroPlas is always happy to answer all your questions about the products we offer.