Processing PET bottles is necessary to achieve both recycling and manufacturing. The improper management of PET results in serious difficulties, despite its potential for versatility and recyclability. This article points out four regular problems linked to PET bottles and recommends solutions to facilitate a more efficient processing scenario.
1. Overview Of PET Plastic
PET plastic is prominent for its remarkable transparency, mechanical strengths, and relatively light density. By and large, it mainly serves for producing beverages, foods, and the packaging industry, however, it serves with a remarkable quality of being not only rigid but also reusable.
Read more:
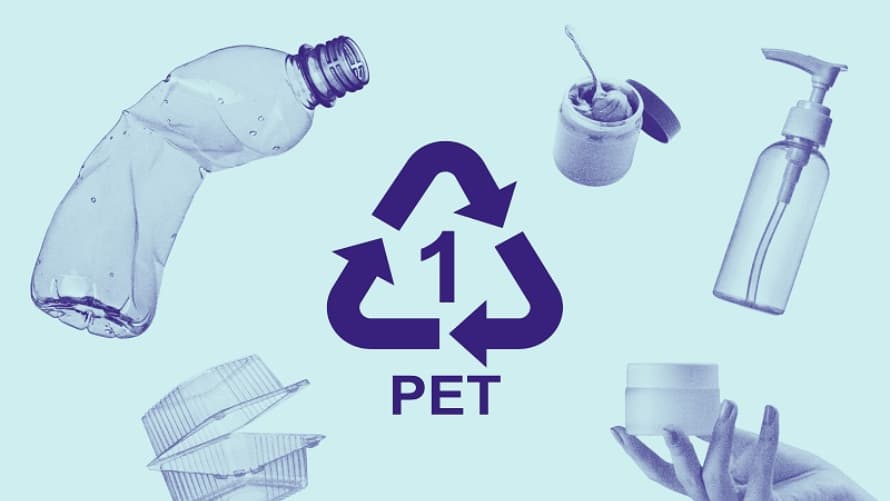
PET plastic finds its applications in beverages, foods, and the packaging industry.
2. PET Bottles: Four Common Problems You Should Avoid
Several problems might develop during the processing of PET bottles that compromise the quality and effective use of the final result. Here are four usual problems, along with their causes, and offer suggestions for solutions.
2.1. Uneven Wall Thickness
Problem
PET bottles with differing wall thicknesses present major problems related to quality and strength. Differences in thickness may result in fragile areas, which makes the bottles more breakable under stress or in the course of handling. Inconsistency of this kind can also impact the container's ability to keep its shape and integrity in the processes of filling and transporting.
Solution
Regular examinations of the extrusion head and molds are necessary in order to deal with uneven wall thickness. Here are some actionable steps:
- Inspect for clogs or wear: These blockages in the head of the extruder can keep the material flow contained, and it is worth checking regularly. Also, this irregular extrusion through clogs can cause differences in wall thickness.
- Adjust extrusion speed: The speed of the extrusion should be adjusted to ensure that a continuous flow and the same flow of the PET material is made possible. The perfect speed supports continuous pressure during the process of extrusion.
- Monitor air pressure: Confirm that the air pressure utilized in blowing corresponds to and is suitable for the bottle design. Air pressure fluctuations may have a direct effect on wall thickness.
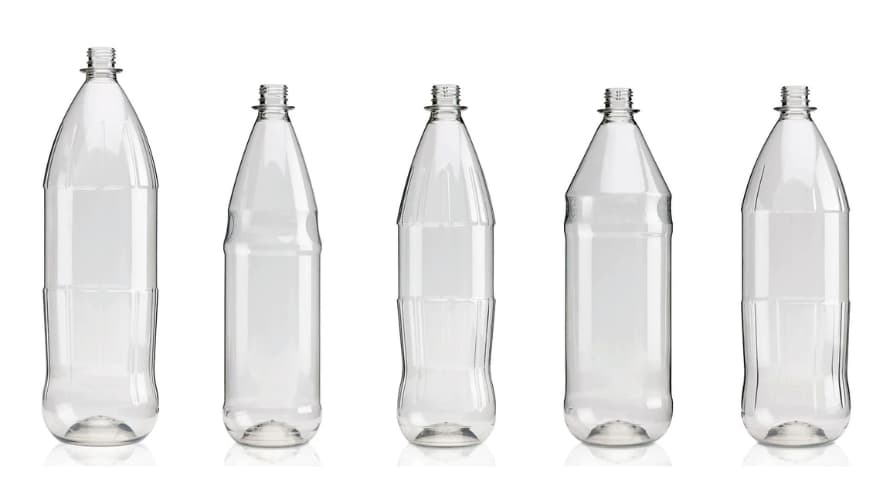
PET bottles with varying wall thicknesses pose serious issues with strength and quality.
2.2. Bottle Deformation
Problem
Changes to mold heating or early shifts in temperatures in processing can regularly produce asymmetric deformities or folds in bottles. The errors might impair both the appearance and the performance capabilities of PET bottles.
Solution
You have to check that the molds sufficiently receive heat and that the temperature settings are specific for the desired bottle design to stop bottle deformation. Consider the following ways:
- Ensure uniform mold heating: Apply heating systems that equally maintain temperature throughout all parts of the mold surfaces. The creation of hot or cold spots leading to uneven expansion and deformation can benefit from this.
- Preheat according to size and shape: Aligning the warming of molds with the unique dimensions and forms of the bottles may result in more stable bottle formation. Design complexity really requires this.
- Verify machine settings: At common intervals, you must ensure that the processing machine's air pressure and temperature correspond to the guidelines for the produced bottles. Adjust these settings according to your specifications to optimize performance.
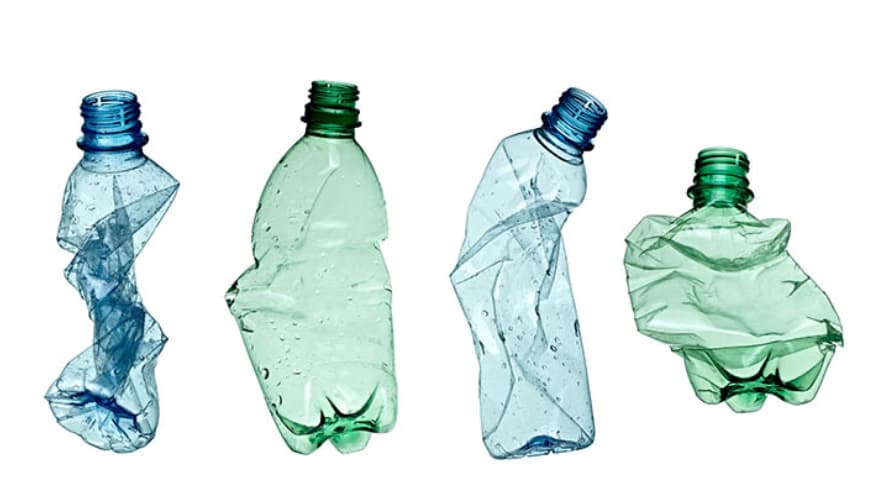
Changes in mold heating or early temperature shifts can lead to asymmetric deformities or folds in PET bottles.
2.3. Inadequate Stretching
Problem
The desired quality and strength depend on the correct stretching of PET bottles. Inadequate stretching techniques might generate containers that are fragile and more likely to break during use, or change shape. The apprehension usually follows from inappropriate processing parameters or an inadequate level of material quality.
Solution
To ensure adequate stretching of PET bottles, the following steps should be taken:
- Confirm extrusion head speed: It is necessary to modify the rate of operation for the extrusion head in order to facilitate extensive stretching of the PET material. Research the association between speed and bottle thickness to find out which settings are best.
- Evaluate mold design: Make certain that the design of the mold supports the necessary stretching. The design of the mold must contain a feature that supports a uniform distribution of stress during the forming operation.
- Inspect PET resin quality: The performance of PET resin dramatically influences its stretching properties. Be certain that the resin fulfills industrial standards and is free from contaminants that can compromise its strength.
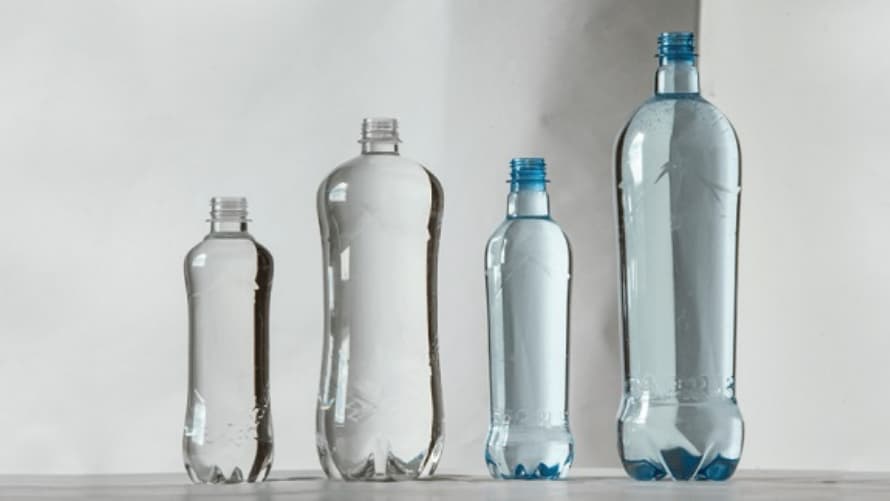
Proper PET bottle stretching is essential to achieving the desired strength and quality.
2.4. Irregular Neck Finish
Problem
A non-uniform neck can result in leakages, reducing product integrity, which is predominantly necessary in applications concerning packaging.
Solution
In order to have a smooth neck finish, the following are factors that need to be considered :
- Mold and neck design check: The design of the neck mold should be reviewed for leakage-free finishing. The defects in the mold will be reflected in defects in the final product.
- Heating and cooling operations: Heating and cooling mechanisms that are involved in the neck should be done with care. To attain proper surface quality, it is necessary to regulate temperature in these states with good accuracy.
- Quality checks: Set up a quality control system aimed at reviewing neck finishes on a regular basis. This approach will allow the identification of possible problems at the early stages of production and enable one to make quick adjustments.
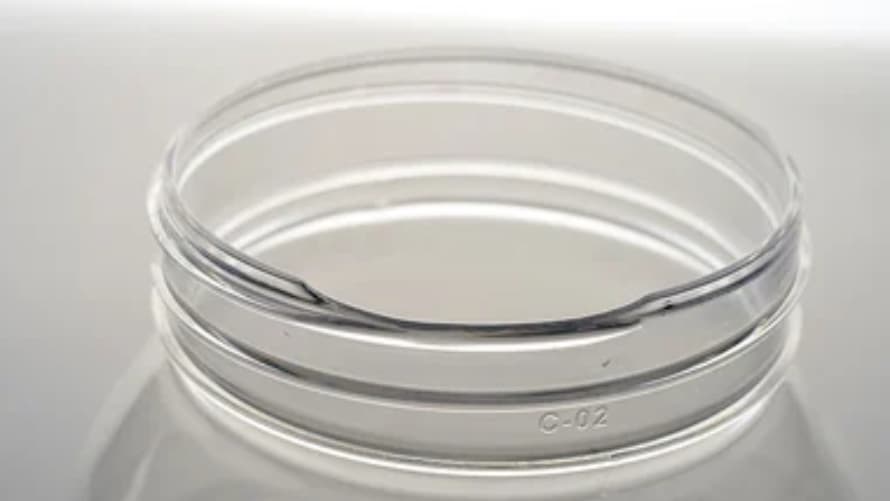
A roughneck will negatively impact the performance of PET bottle closures and caps.
3. Conclusion
Solving the four standard issues found in PET bottle processing is important for improving the quality and performance of the end product. The proposed solutions improve manufacturers' production efficiency, reduce waste, and reinforce the longevity of the bottles.
Read more: PET bottle recycling: A sustainable packaging solution
4. About EuroPlas’ PE Filler Masterbatch
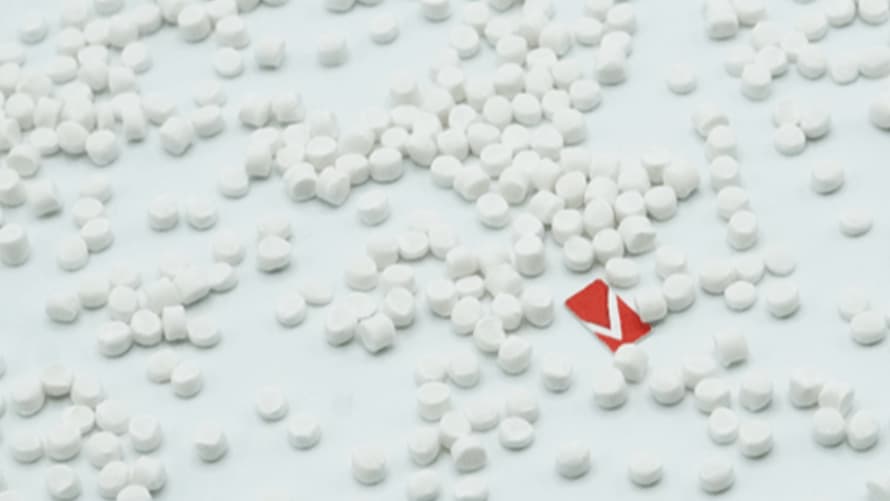
At EuroPlas, we pride ourselves on being one of the world leaders in the manufacture of plastic masterbatches. Therein, Our PE Filler Masterbatch at EuroPlas will get you the best results in manufacturing, which offerings the following features:
- Save production cost
- Improve several properties of end-products: brightness, opacity, shrinkage reduction,...
- Save energy thanks to CaCO3's great thermal transmission ability
- Increase the stability in manufacturing process
Kindly contact us for further information!