Blow molding vs injection molding are two prominent plastic manufacturing techniques, each offering distinct advantages. Choosing between them is pivotal in achieving the best results for your project. In this article, we'll compare blow molding and injection molding, helping you determine the most suitable method for your specific manufacturing needs.
1. What is blow molding?
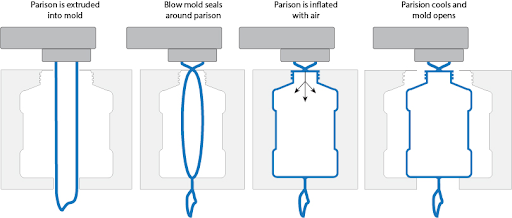
The process of blow molding
Blow molding is a method of manufacturing 3D plastic products in which hot plastic is blown into a mold to create the final shape of the product. This process is often used to produce plastic bottles, containers, toys, and many other plastic products with mixed shapes or special shapes. The way the blow molding process works is as follows:
- Plastic raw materials are melted at high temperatures.
- The hot plastic is bonded to the blow mold, and the mold is closed.
- One end of the mold has a knob that shapes the final product and is blown in with compressed air, causing the hot plastic in the mold to expand and fill the space inside the mold, ensuring the product has the desired shape.
- After the product has cooled and solidified, it is removed from the mold.
Blow molding is an effective method for producing plastic products at a low cost and can create products with complex shapes.
The primary methods of blow molding include:
- Extrusion blow molding (EBM): In EBM, the parison (thermoplastic raw material before it is blown and shaped to create the final product) is created by extruding molten plastic through a die. It is a widely used method for producing hollow products.
- Injection blow molding (IBM): This is a method of manufacturing plastic products by using a mold to form a parison (pre-formed plastic tube) and then injecting liquid or compressed air into the parison to create the final product. This method is often used to produce plastic products with complex shapes and high precision.
- Injection-stretch blow molding (ISBM): This method of manufacturing plastic products uses a mold to extrude the parison, then uses a stretch process to create the final product. ISBM is often used to produce plastic products of specific shapes and sizes, often products such as PET plastic bottles used for water, soft drinks, and similar products.
2. What is injection molding?
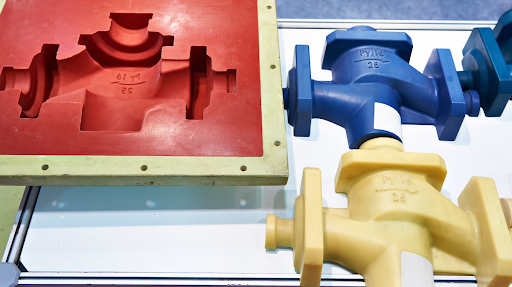
The product can be made from injection molding
Injection molding is the process of manufacturing plastic products by using molds to compress or squeeze plastic into the desired shape. The process typically involves plastic thermodynamics, in which the plastic is typically placed in a mold, and then pressure and temperature are applied to cause the plastic to flow and stay within the shape of the mold. Once the plastic has cooled and solidified, the created plastic product can be removed from the mold.
Injection technology can be used to produce many different types of plastic products, from toys to industrial components. This process is typically performed in factories and manufacturing facilities using specialized equipment and techniques to ensure the quality and precision of the final product. Types of plastic commonly used in injection molding are ABS, Polypropylene (PP), Polycarbonate (PC), PVC, and Nylon.
Read more: What is injection molding? How does it work?
3. Differences between blow molding vs injection molding
Blow molding and injection molding are two distinct plastic manufacturing processes, each with its own set of characteristics and applications.
Injection molding involves injecting molten plastic material into a mold cavity under high pressure. It is particularly well-suited for producing complex, three-dimensional plastic parts with intricate details. This process offers high precision and repeatability, making it ideal for applications such as automotive components, consumer electronics, and medical devices. Injection molding is cost-effective for large production runs, but it requires an upfront investment in molds, which can be expensive. Additionally, it's less suitable for hollow and thin-walled parts.
On the other hand, blow molding is specifically designed for creating hollow and thin-walled plastic products. In blow molding, a hollow tube of molten plastic, known as a parison, is placed in a mold. Compressed air is then used to expand the parison and shape it to the interior of the mold cavity. This process is commonly used to produce items like bottles, containers, and automotive fuel tanks. Blow molding is cost-effective for large volumes of identical products, and it requires simpler tooling compared to injection molding. However, it may not provide the same level of precision and detail, and it is less suitable for solid, intricate components.
4. Blow molding vs Injection molding: Which one is suitable?
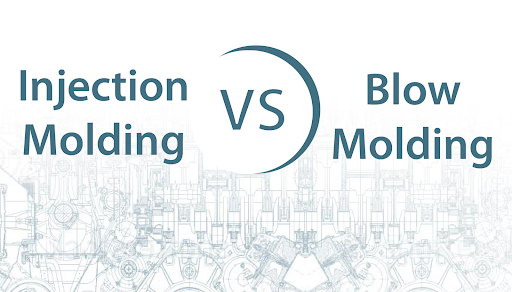
Should choose blow molding or injection molding
The choice between injection molding and blow molding depends on many factors, including the type of product being produced, quality requirements, product quantity, and cost. Here are some points to consider to decide which is more appropriate:
- Product type: Injection molding is often suitable for products with complex shapes or small details, such as electronic components, machinery housings, or technical plastic products. Blow molding is often used to produce products with 3D shapes and large quantities of identical products, such as plastic bottles or containers.
- Quality requirements: Injection molding is often capable of creating products with high precision and smooth surfaces. Blow molding can create products with smooth surfaces, but cannot produce small parts or high-precision products like injection molding.
- Product quantity: Blow molding is often suitable for mass production of the same product in large quantities, while injection molding can be used for both sporadic batch products or those in small quantities.
- Cost: Injection molding typically has a higher start-up cost due to the need to create molds, while blow molding can start out at a lower cost, especially if you already have molds or large batch production.
5. Conclusion
In this article, we learned about two important processes in the production of plastic products: blow molding and injection molding. Both of these methods produce a variety of plastic products that we often encounter every day. Both processes have their own benefits and are widely used in industry to create high-quality plastic products. Selecting the right molding method – be it blow molding vs injection molding – is pivotal in achieving your manufacturing goals. Understanding the strengths and limitations of each process and considering factors like design complexity, material selection, and production volume will empower you to make an informed choice that aligns with your project's objectives.
6. Plastic products are used for injection molding and blow molding at EuroPlas
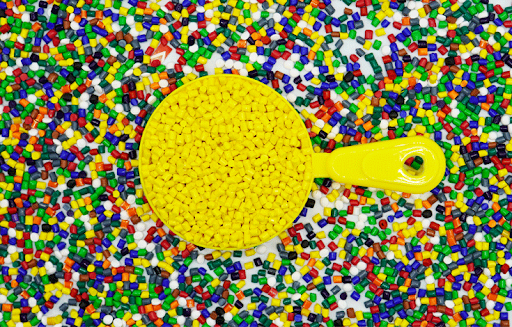
Color masterbatch products at EuroPlas
Color masterbatch serves as an indispensable component in the world of plastic manufacturing, offering a reliable means of adding vibrant and consistent coloration to plastic products. In blow molding, achieving a uniform distribution of color is paramount. The masterbatch must be expertly integrated into the base resin, ensuring that the resulting plastic product displays an even, streak-free hue. Furthermore, it is crucial to select a color masterbatch that can withstand the elevated temperatures characteristic of blow molding, maintaining its color integrity even in the face of heat. For applications where the blow-molded parts may be exposed to the sun or outdoor elements, UV-resistant color masterbatches provide added protection against fading or degradation due to UV radiation.
Understanding these things, EuroPlas brings customers high-quality colored plastic masterbatch products, suitable for blow molding and injection molding processes. The foremost advantage offered by EuroPlas color masterbatch lies in its remarkable surface dispersion on the final product, ensuring stable coloration and impressive heat resistance. EuroPlas offers a diverse range of color options, including white, black, red, gray, purple, blue, brown, orange, and yellow, and specialized color masterbatch variants that can produce a wide array of effects to cater to the unique requirements of the finished product.
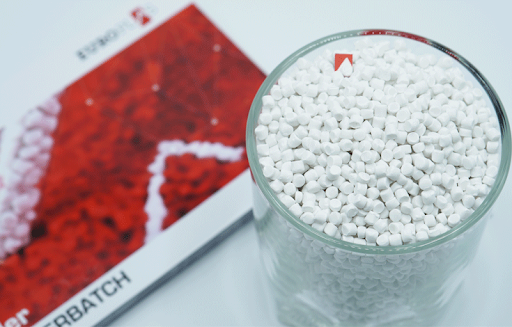
High-quality filler masterbatch from EuroPlas
Filler masterbatch is a valuable addition to both blow molding and injection molding processes, contributing to improved material properties and cost-efficiency. In blow molding, the incorporation of a filler masterbatch, which consists of fine particles like calcium carbonate or talc embedded in a carrier resin, enhances the stiffness and rigidity of the plastic product. This is particularly advantageous for applications where structural integrity is crucial, such as industrial containers or automotive components.
Similarly, in injection molding, filler masterbatch plays a pivotal role in reinforcing the base resin, increasing its strength and stiffness, and reducing the overall production cost. By reducing the consumption of the more expensive base resin, filler masterbatch offers an economical solution for producing solid and lightweight plastic parts with enhanced mechanical properties. Whether in blow molding or injection molding, filler masterbatch is a versatile and cost-effective tool for tailoring material characteristics to meet specific application requirements.
EuroPlas has more than 16 years of manufacturing and exporting filler masterbatch to thousands of businesses in Asia, the Middle East, Africa, and Europe... We provide many types of filler masterbatch to help you save costs, improve productivity, and produce high-quality plastic products.
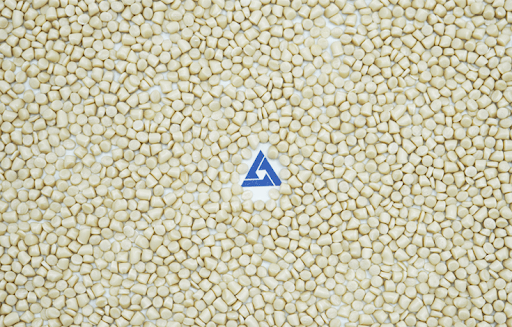
Bio filler: Cost-effective material solution for bioplastic end-products
Bio filler in injection molding are a sustainable and eco-friendly addition to the world of plastic manufacturing. Bio filler offer the dual benefit of improving the material properties of injection-molded products while promoting a greener and more sustainable approach to plastics manufacturing.
At EuP, BiOMates stands out as an excellent choice for the production of environmentally friendly goods, including biodegradable packaging, injection-molded items, and single-use plastic extrusions. This versatile material offers a range of benefits, making it a preferred option for eco-conscious manufacturers. It aids in saving production costs for bioplastic end-products, ensuring that businesses can reduce expenses while still contributing to sustainability.
Founded in 2007, European Plastic Company (EuP) is the top producer and exporter of filler and masterbatch in Vietnam. Our filler masterbatch is specially manufactured to optimize the usage and reduce the production cost of injection-molded and blow-molded products. Nowadays, EuP has been a reputable partner of plastic producers from 70 countries across the world. Contact us for more details!