Colorant for plastic is properly the most popular additives added into the process of plastic manufacturing. Colorant for plastic is necessary in bringing an attractive appearance to the plastic products. They are variable in types (pigments, dyes, etc.) and forms (liquid, powders or pellet). Let us give you a more insightful and specific look at this important additive.
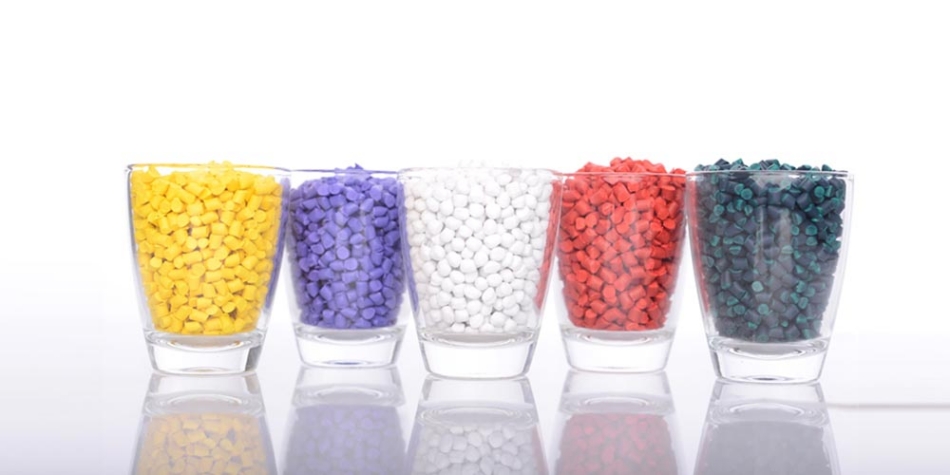
Why do we need to work with colorant for plastic in plastic industry?
The answer is that adding
colorant for plastic can bring a huge benefit to this type material over other traditional materials such as wood or metals, which is the ability to appear brightly and colorfully. As the world keep developing throughout years, the demand of human in owning and using products keeps increasing nonstop. Nowadays, they not only looking for quality products but also expect them to achieve high aesthetics. Hence, choosing the right
colorant for plastic became a vital task in production. Without coloring your plastic properly, the attractiveness of the final products is taken away, leading to the immense lost in productivity and this directly affects the profit of producers.
In addition, in some particular case,
color masterbatch is also used as a protection to cover and enhance durability of plastic-based products. For instance, outdoor furniture and automobile accessories products usually contain black pigments (usually came from black carbon powders) since black color acts like a shield protect product from severe weather conditions such as rains, UV rays, winds, temperature changing, etc.
How did manufacturers add colorant for plastic into plastic products?
There are 2 main ways to add colors to plastic: internal coloring and external coloring. As its name stated, external coloring is the method in which we adding colorant for plastic only in the surface of the plastic-based product. It consists of coating, printing, spraying, painting and plating/deposition techniques. Advantages of this method are that it will be done quickly, easily and cost-effectively. However, since there was the outside surface of the plastic colored, as time passed by, it may be faded. In general, this method does not have the long-lasting effect and only in accordance with the purpose of decoration the final products.
On the other hand, internal coloring seems to require more efforts as colorant for plastic will be added into the materials of masterbatch manufacturing. By adding colorant directly to the mixture, when masterbatches is passed through the modification process, under the impact of high temperature, pigment particles will be spread out more evenly. And when the plastic set in solid form, the color will be maintained even when left outdoor for long time.
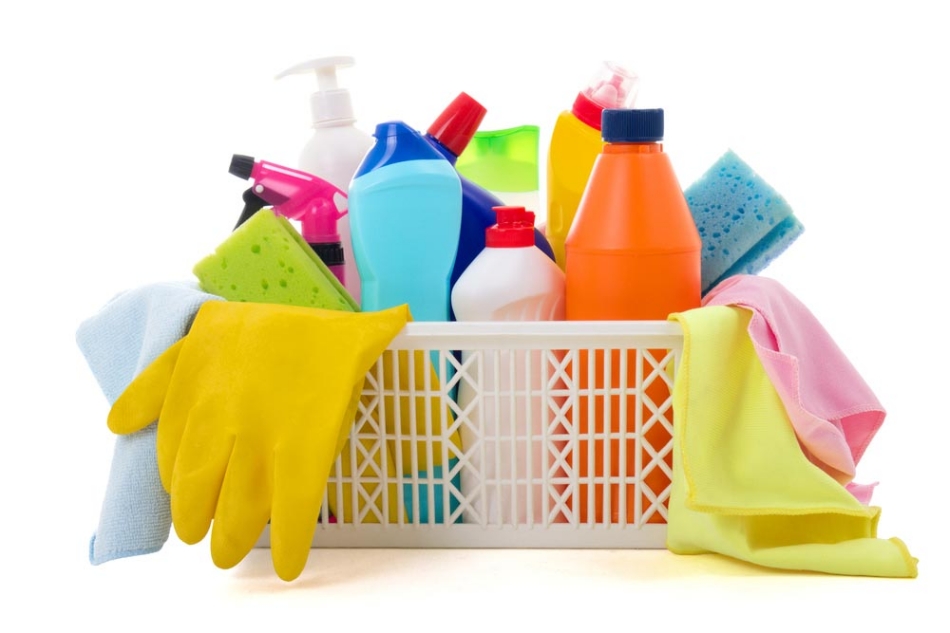
How to choose the proper colorant for plastic that guarantee perfection for your products?
There are multiple of selections for you choose when making a decision on which
colorant for plastic is good for your production. To accomplish their function when adding masterbatch mix, the colorant must meet some basic standards.
First, the chemical composition of the
color masterbatch must be compatible with the chemical composition of the plastic compound to which they are added. Since there are so many types of resins that can become the carrier in masterbatch manufacturing and their characteristics are different, you cannot use a single colorant for all your masterbatches. For example, dyes are often used with plastics such as polystyrene, polycarbonates or acrylic polymers. In contrast, pigments are a more suitable choice for polyolefins, which is a sub-group in thermalplastics including polyethylene (PE), polypropylene (PP), polymethylpentene (PMP), polybutene-1 (PB-1).
Secondly, the stability of the colorant is also a criterion that needs to be monitored because during the plastic processing procedure, the masterbatch must be constantly exposed to high-temperature condition. Therefore, if the stability cannot be ensured in these processes, the color of the final product may be affected. In particular, for plastic production using in the food and beverage industries, the stability of plastics is especially important. If manufacturers use the toxic
colorant for plastic, not only the quality of plastic products is affected, but the quality of the food inside them is also affected, resulting in harming consumer’s health.
Lat but not least, "color matching" according to customer requirements is also an improtant factor. Each plastic product has different color requirements, therefore, the manufacturer must study the formula for mixing different
colorant for plastic with the most appropriate ratio. The ultimate goal is to bring customers the most accurate color with their requirements.
Color masterbatch is the best choice of colorant for plastic products
3 methods of coloring for plastic products today include:
- Color masterbatch
- Color powder
- Thick color
In particular, colorant for plastic in pellets (granules) are most used because of its diversity and efficiency in production. This form of colorant is usually called as color masterbatch and it will be mixed with other masterbatches such as filler or additive in plastic processing. Pigment in color masterbatch is at a high concentration (10-70%) with excellent dispersion that will give final product a beautiful appearance.
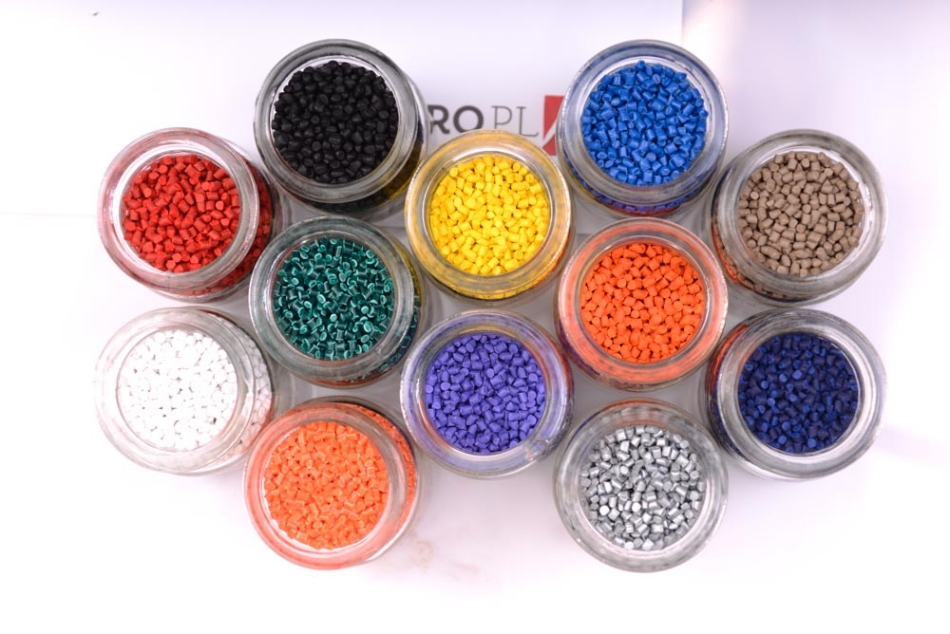
Another advanced type of color masterbatch is colored pellets or colored compound, which does not require the association of other masterbatches. Since the concentration in this pellet is specially adjust at a proper concentration (usually less than 5%) for final products, plastic producers can directly use this type of plastic colorant to generate products.
In comparison of colorant for plastic in other liquid or powder form, the sub-group of color mastebatches exhibit outstanding features on dispersion, storage stability and greater flexibility in use. Thanks to that the costs related to production and storage have also been optimized.
In addition, some manufacturers still use pigments powder for plastic products. With cheaper prices, pigments are often used at concentrations of approximately 30-80%. The disadvantage of this type of colorant for plastic is that they do not have good color dispersion as color masterbatch, higher pollution levels, dirtying machinery as well as surrounding environment because the particles are very light and easy to flutter.
Paste color is also less used than color masterbatch because their dispersion is not good. Therefore, manufacturers only use this color whenever they want to to create plastic-based products with lightly or semi-transparent color appearances.