Talc masterbatch, a key additive in the plastics industry, plays a crucial role in enhancing mechanical properties, improving processability, and reducing production costs. As industries shift toward sustainability, efficiency, and enhanced performance, talc masterbatch is undergoing significant advancements. This article will examine the current market landscape, emerging trends, and innovative breakthroughs that are shaping the future of talc masterbatch.
1. Current Overview of Talc Masterbatch Market
1.1. Market Size and Growth
The Talc Masterbatch market is projected to grow significantly in the coming years. Recent estimates suggest that the market could reach a valuation of over $1 billion by 2025, with a compound annual growth rate (CAGR) of approximately 5-7%. This growth is largely attributed to the increasing demand for sustainable materials across various industries, including automotive, packaging, and construction.
.jpg)
Market Size and Growth of Talc Masterbatch
1.2. Key Drivers of Market Growth
- Rising Demand for Sustainable Packaging: With the global focus on reducing plastic waste, there is a substantial shift towards sustainable packaging solutions. Talc filler masterbatch is increasingly being used in the production of eco-friendly packaging materials that maintain strength and reduce environmental impact.
- Advancements in Technology: Innovations in production techniques have led to improved quality and performance of talc masterbatch. New formulations are being developed to enhance compatibility with various polymers, broadening their application scope.
- Regulatory Support: Governments worldwide are implementing regulations aimed at promoting sustainable practices. This support is encouraging manufacturers to invest in talc filler masterbatch as a viable solution to meet compliance standards.
Read more: Talc filler masterbatch: Components, properties, and applications
2. Emerging Trends of Talc Masterbatch
The talc masterbatch industry is evolving rapidly to meet the demands of modern manufacturing, sustainability initiatives, and enhanced performance requirements. Below are some of the most significant trends shaping the future of talc masterbatch:
2.1. Advanced Functional Additives
- UV and Thermal Stabilizers: Talc naturally improves heat resistance, but when paired with UV stabilizers, it offers superior protection for outdoor plastic applications. This combination is particularly beneficial for agricultural films, automotive components, and construction materials.
- Antimicrobial Properties: With increasing concerns about hygiene and product safety, antimicrobial talc masterbatch is becoming more popular in food packaging, medical devices, and household appliances. This helps prevent bacterial growth and extends the shelf life of these products.
- Improved Impact Resistance: New formulations of talc masterbatch enhance toughness while maintaining stiffness, making them ideal for automotive parts, protective packaging, and consumer goods.
.jpg)
Advanced Functional Additives
2.2. Increased Talc Concentration for Enhanced Efficiency
The trend towards higher talc loading in masterbatch formulations is driven by the need for cost reduction and improved performance. Recent advancements in dispersion technology have enabled several benefits, including:
- Increased Stiffness and Rigidity: Final plastic products exhibit improved stiffness and rigidity, allowing them to serve as replacements for heavier materials like metal or wood in industries such as construction and automotive.
- Better Processing Efficiency: There is a reduction in cycle times during injection molding and extrusion processes, leading to more efficient production.
- Enhanced Dimensional Stability: Higher talc concentrations help minimize shrinkage and warping in plastic components, ensuring better quality and consistency.
2.3. Digitalization and Smart Manufacturing
- Automated Quality Control: Real-time monitoring and AI-driven quality control systems ensure consistent particle size distribution and dispersion, resulting in more reliable masterbatch performance.
- Data-Driven Formulation Adjustments: Machine learning algorithms are utilized to optimize talc-polymer ratios based on specific application requirements, minimizing waste and enhancing product consistency.
- Eco-Friendly Production Processes: Advanced processing techniques, such as energy-efficient extrusion and reduced emissions manufacturing, are being adopted to minimize environmental impact.
.jpg)
Digitalization and Smart Manufacturing
2.4. Customization for Industry-Specific Applications
Different industries have unique material requirements, leading to the development of tailored talc masterbatch solutions:
- Automotive Sector: Talc masterbatch is specifically engineered for high impact strength and lightweight properties. It is increasingly replacing traditional materials to enhance fuel efficiency in electric vehicles
- Packaging Industry: High-performance talc masterbatch improves the barrier properties of plastic films, which helps extend the shelf life of food and enhances durability in flexible packaging.
- Electronics: The insulating properties of talc are being optimized for applications in wire coatings, electronic housings, and heat-resistant components.
3. Remarkable Innovations Made of Talc Masterbatch
3.1. Automotive Industry
Talc masterbatch has revolutionized the automotive industry by providing lightweight, durable, and cost-effective solutions. Its application in the production of automotive parts has led to significant weight reduction, which in turn improves fuel efficiency and reduces greenhouse gas emissions. Key innovations include:
- Interior Components: Talc masterbatch is used in the production of interior components such as dashboards, door panels, and trim parts. It provides excellent surface finish, improved scratch resistance, and enhanced dimensional stability, making these parts more durable and aesthetically pleasing.
- Under-the-Hood Components: Talc masterbatch is also used in the production of under-the-hood components such as engine covers, air intake manifolds, and radiator end tanks. Its high thermal stability and mechanical strength make it ideal for withstanding the harsh conditions under the hood, including high temperatures and exposure to chemicals.
.jpg)
Using Talc Masterbatch in Automotive Industry
3.2. Packaging Industry
The packaging industry has greatly benefited from the use of talc masterbatch in the production of plastic films, containers, and other packaging materials. Talc masterbatch offers several advantages, including improved barrier properties, enhanced stiffness, and reduced production costs. Key innovations include:
- Flexible Packaging Films: Talc masterbatch is used to produce flexible packaging films with improved barrier properties, such as increased resistance to moisture and oxygen. This helps to extend the shelf life of packaged products and maintain their quality.
- Rigid Containers: Talc masterbatch is used in the production of rigid containers, such as bottles and jars, to enhance their stiffness and dimensional stability. This results in more robust and reliable packaging solutions that can withstand the rigors of transportation and handling.
3.3. Consumer Goods
- Household Appliances: Talc masterbatch is used in the production of household appliances, such as washing machines, refrigerators, and vacuum cleaners. Its high thermal stability and mechanical strength ensure that these appliances can withstand the stresses of daily use, while its cost-effectiveness makes them more affordable for consumers.
- Sports Equipment: Talc masterbatch is used in the production of sports equipment, such as helmets, protective gear, and various plastic components. Its lightweight and durable properties make it ideal for use in products that require both strength and flexibility.
3.4. Construction Industry
- Plastic Pipes and Fittings: Talc masterbatch is used in the production of plastic pipes and fittings, providing improved dimensional stability, mechanical strength, and resistance to chemicals. This results in more reliable and durable plumbing systems that require less maintenance.
- Flooring and Wall Panels: Talc masterbatch is used in the production of flooring and wall panels, offering enhanced stiffness and dimensional stability. This results in more durable and aesthetically pleasing building materials that can withstand the rigors of daily use.
.jpg)
Using Talc Masterbatch in Construction Industry
4. Conclusion
The future of talc masterbatch is marked by continuous innovation, sustainability-driven advancements, and expanding industrial applications. As manufacturers seek lighter, stronger, and more cost-effective plastic solutions, talc masterbatch is evolving to meet these demands. From automotive lightweighting to sustainable packaging, talc masterbatch is becoming a critical component in next-generation plastic products.
5. About EuroPlas’ Filler Masterbatch
EuroPlas is renowned as the world's leading manufacturer of filler masterbatch, a cost-effective solution for plastic production. Filler masterbatch, primarily composed of calcium carbonate (CaCO3), virgin plastic resin, and specific additives, is widely used to enhance the properties of plastic products. By incorporating filler masterbatch, manufacturers can significantly reduce production costs while improving the mechanical properties of their products, such as hardness, impact resistance, and printability.
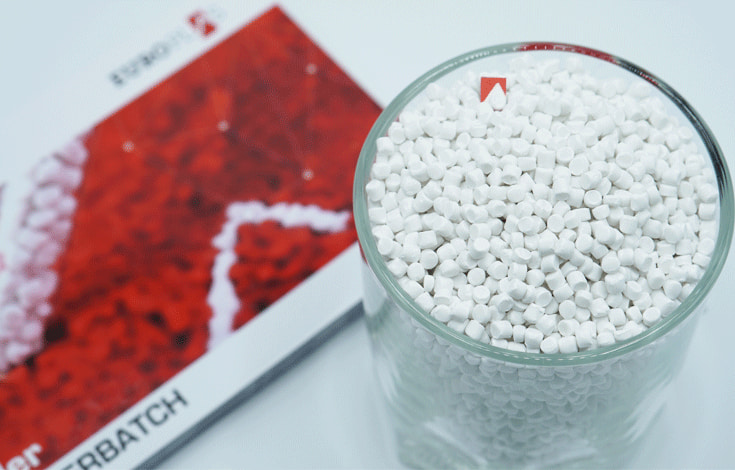
EuroPlas’ Filler Masterbatch
One of the key advantages of EuroPlas' filler masterbatch is its ability to improve the stability of the production process and the quality of the final product. EuroPlas' filler masterbatch is versatile and can be used in various applications, including blow molding, injection molding, packaging, plastic frames, door manufacturing, and PVC pipe production.
With over 16 years of experience, EuroPlas has been exporting filler masterbatch to thousands of businesses across Asia, the Middle East, Africa, and Europe. Their commitment to quality and innovation has made them a trusted partner for companies looking to optimize their production processes and create high-quality plastic products.
For more information and samples, please contact us HERE!