Colorants are key ingredients in the plastics manufacturing industry. They contribute to bringing diverse colors to plastic products as well as meeting customer tastes. In addition, colorants also combine stably with most plastic bases such as PE, PVC or PP, so they will not affect the health of consumers. In the article below, EuroPlas will analyze in detail the influence of colorants in plastics production. Check out now!
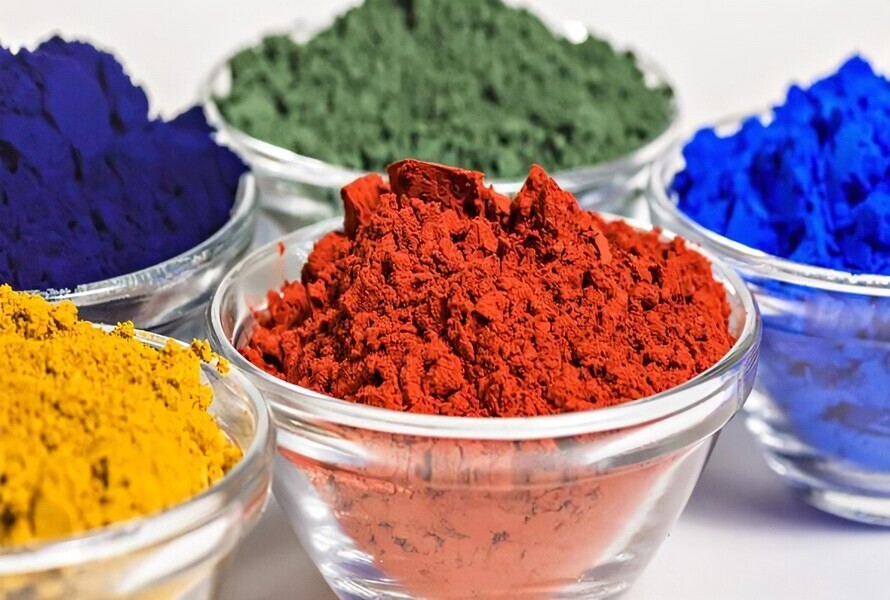
1. Overview of colorants in the plastics industry
Currently, colorants in the plastics industry are divided into two main types: colorants and plastic colorants. Colorants are considered to be finely ground colorants, with very small sizes ranging from micro to nano. The pigments will be mixed with the resins and dispersed into their chemical structure during the manufacturing process, which will create a variety of colors for the products.
-
In addition, the colorants are also shaped in the form of granules, also known as color resins. Color resins include 2 main components: colorants combined with primary resin. Some special formulas will contain processing additives such as zinc, oil, wax, etc. and/or fillers (usually calcium carbonate powder)
-
In particular, color resins are not pure pigments / colorants. On the contrary, pure pigments / colorants or any type of dye is only a part of the color resin, because it contains the resin, so it is less concentrated than the original colorant, usually divided into 3 small groups: organic dyes, organic pigments and inorganic pigments. The market is increasingly demanding on plastic products, so the importance of colorants is increasing.
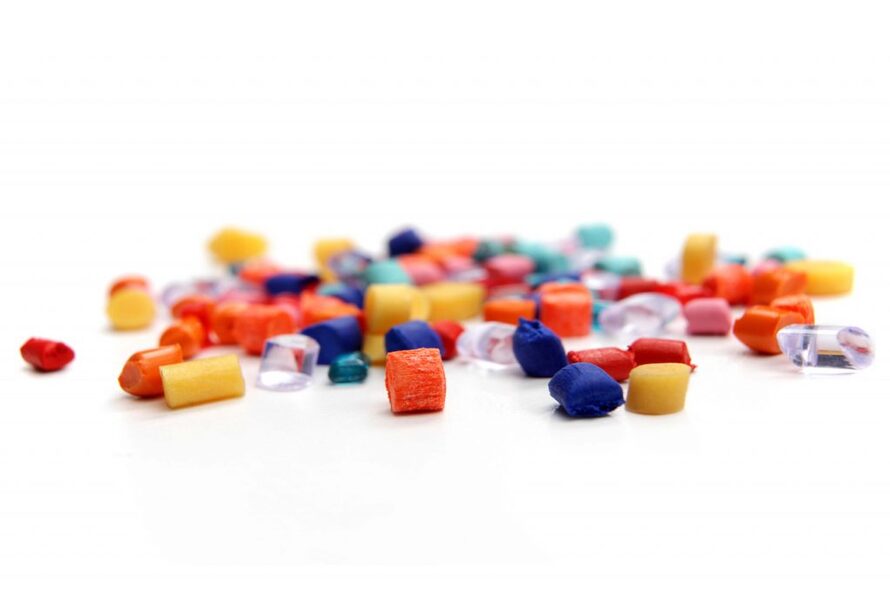
Most popular plastic substrates such as PVC, PET, PP are well combined with colorants in the form of boots or granules. In particular, manufacturers also ensure that the properties of colorants will not affect the product or the health of consumers. In the next section, EuroPlas will mention the effects of colorants in the plastic industry.
2. Effects of colorants in the plastic industry
As we have seen, colorants have played an indispensable role in the plastic industry. All plastic products have their own distinct colors, so we cannot deny the influence and benefits of colorants in the plastic industry.
Colorants contribute to increasing the aesthetics of plastic products. Therefore, compared to metal products, plastic products are more brilliant and eye-catching.
-
The outstanding benefits of colorants are heat resistance, good dispersion and environmental friendliness. Each field will have regulations on the content of colorants, the common index is from 0.3% - 3%. For example, car accessories and outdoor furniture products are often black (from carbon black powder) because black acts as a shield to protect the product from harsh weather conditions such as rain, wind, UV rays, temperature changes, etc.
-
Colorants not only disperse during processing but also act as a surface coating for products. They blend well with most popular plastic substrates on the market such as: PP, PE, PC, PS, ABS, EVA, so manufacturers can save a large part of the cost of using auxiliary materials
-
Although colorants in granular form are very small in size, they are considered an important type of plastic additive. Because most colorants have stable heat resistance and UV resistance. In addition, plastic granular colorants must have more than 90% virgin plastic because the product surface will be smooth with high durability.
-
The applied colorants not only improve the product's features but also help businesses save costs. If the granular colorants are quite expensive, the powder form is the right choice for SMEs or mass production processes. With a cheaper price, color powders are often used at a concentration of about 30 - 80%.
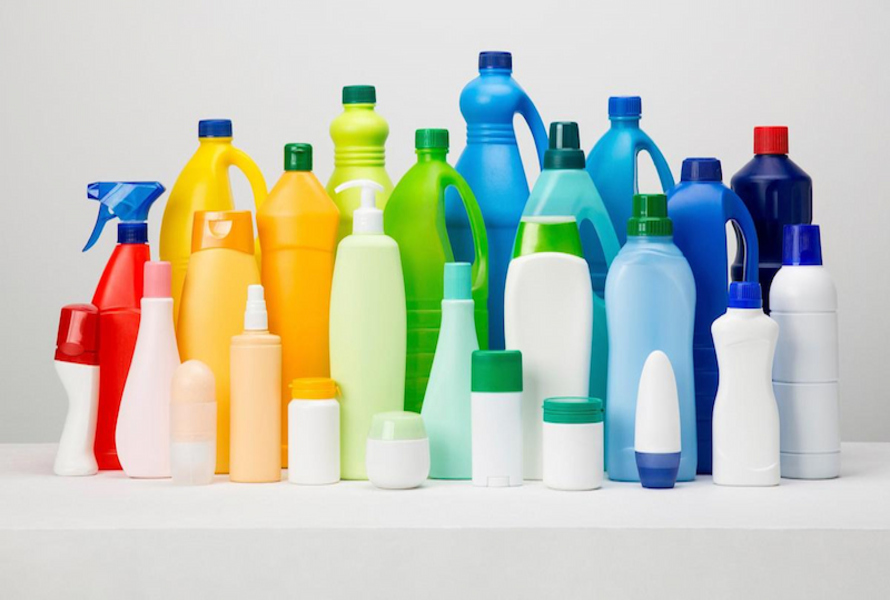
In general, those are the 5 core advantages of colorants in the plastic industry. The combination of colorants and plastic substrates requires the manufacturer and team to have high technical skills. However, we cannot avoid the challenges when mixing colorants during the production process. Refer to the next section to find out what those challenges are!
3. Challenges in coloring plastic products
The application of colorants requires high technical requirements, knowledge and professional experience. Manufacturers must thoroughly understand the physical and chemical structure and properties of the plastic substrate. EuroPlas sends you 2 basic notes when using colorants in the plastic industry.
-
Incompatibility / inhomogeneity in chemical structure: Incompatibility between the chemical properties of Polymers and pigments can occur during the mixing process. Normally, chemicals will combine well in high temperature environments with the help of some catalyst components. However, errors can occur during the chemical interactions between the little-known components hidden behind the core material. Therefore, manufacturers should make many assumptions and test them with their own knowledge and experience before blending the colorant into the resin base.
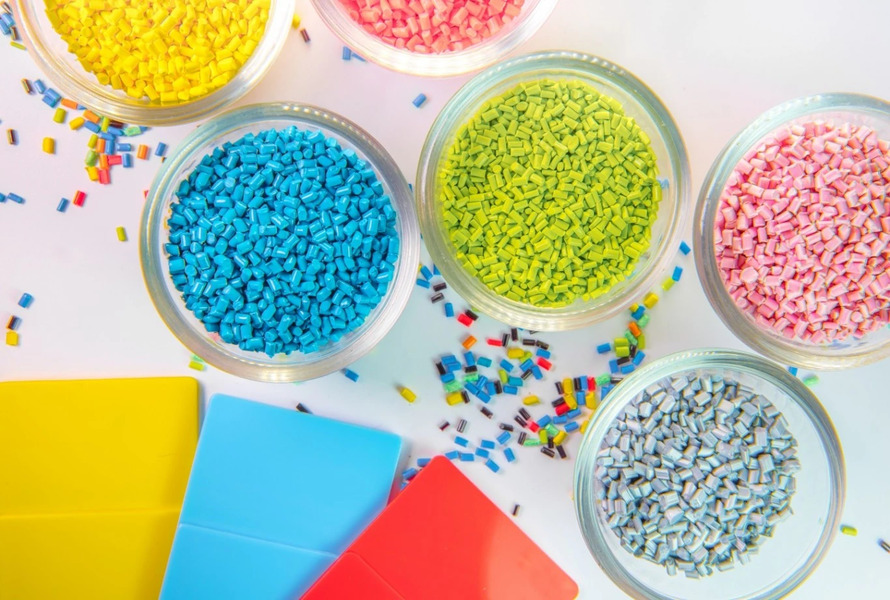
-
Temperature fluctuations from the environment: Each resin base and colorant will have a standard temperature at which they interact well with each other to create bright colors and stable quality. However, abnormal temperature changes can destroy that bond. Therefore, to optimize the formula, the temperature has been raised beyond 150°C (300°F). This is the temperature at which most of the polymer structure is ready to receive and blend with the colorant. What engineers need to ensure next is to choose the right pigment for the right polymer at the right temperature.
These are two basic challenges that manufacturers in the plastics industry face when using colorants for their products.
See more: Key challenges in coloring plastic products
4. About EuroPlas
EuroPlas is one of the leading manufacturers and suppliers of plastic materials in Vietnam. The company currently has 7 factories with a supply capacity of up to 8 million tons/year. In terms of colorants, EuroPlas is always confident in the quality of its color masterbatch products.
The biggest advantage of EuroPlas color masterbatch is its excellent dispersion on the surface of the finished product, stable color shades and good heat resistance. Thanks to its outstanding advantages, EuroPlas color masterbatch has been and is being applied in industrial activities such as film blowing, injection molding, extrusion blowing, and other applications.
-t%E1%BA%A1i-europlas.jpg)
Currently, EuroPlas is providing different types of color masterbatches such as white, black, red, gray, purple, blue, brown, orange, and yellow. In particular, we also provide specialized color masterbatch products with diverse effects according to the requirements of the finished product.
5. Conclusion
The above article has described in detail the influence of colorants in plastic production. At the same time, EuroPlas also mentioned important notes in combining colorants with basic plastic bases. Please continue to follow and accompany EuroPlas to update the earliest news about plastic materials!