Injection mold design plays a pivotal role in the manufacturing industry, determining the quality, consistency, and efficiency of plastic products. For enthusiasts and professionals alike, a well-designed mold ensures smooth production, reduced costs, and high-quality outputs. Whether you’re looking to improve your understanding of injection mold design or seeking ways to refine your processes, this guide provides valuable insights. We'll explore the importance of effective design and share the top 5 tips to master this crucial aspect of manufacturing.
1. Overview of the Importance of Injection Mold Design
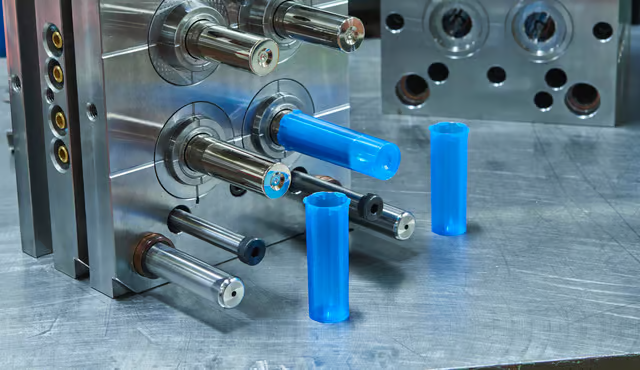
The Importance of Injection Mold Design
Injection mold design is the backbone of any successful plastic manufacturing process. It involves creating a precise mold that forms the shape and structure of a product when molten plastic is injected into it. Here’s why it’s so crucial:
Quality Control: A well-crafted injection mold design is essential for maintaining product consistency. Proper design ensures that each part produced meets the required specifications without defects, such as warping, flashing, or sink marks.
Cost Efficiency: Effective injection mold design can significantly lower production costs. By optimizing the design for ease of manufacturing and minimizing material wastage, manufacturers can save money on materials, reduce cycle times, and extend the lifespan of the molds.
Production Efficiency: A good design minimizes the potential for production issues such as short shots, burn marks, or flow lines. This allows for faster cycle times and higher productivity, which is especially important when scaling up for large production runs.
Durability of Molds: A robust injection mold design also affects the durability of the mold itself. By considering factors like stress points, cooling channels, and proper gating systems, designers can create molds that withstand repeated use without premature wear or damage.
With the importance of injection mold design established, let's dive into the practical tips that can enhance your design process.
2. Top 5 Injection Mold Design Tips
1. Focus on Proper Material Selection
The choice of materials for both the mold and the product is a critical first step in injection mold design. Different plastics have varying melting points, flow characteristics, and shrinkage rates, which can affect the final product’s quality. Additionally, the material used for the mold itself (such as steel or aluminum) impacts the durability and cooling efficiency of the mold. Understanding the properties of materials ensures compatibility between the mold and the injected plastic, leading to optimal performance.
Pro Tip: For high-volume production, opt for hardened steel molds as they offer durability and can handle the heat and pressure of multiple cycles. For prototyping or low-volume runs, aluminum molds can be a cost-effective and faster option.
2. Optimize Part Geometry for Moldability
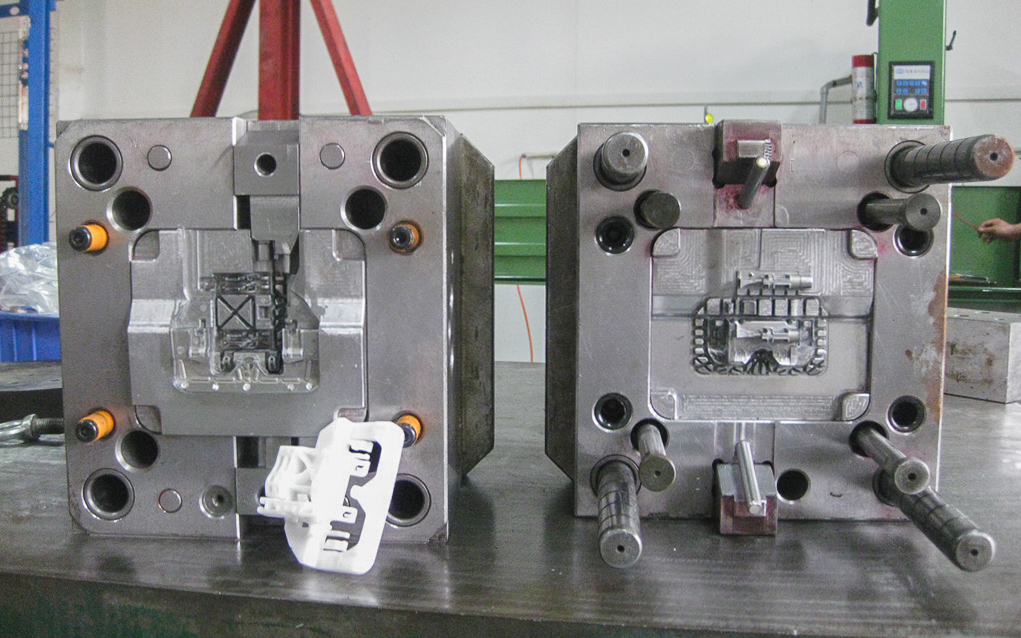
Injection Mold Design in manufacturing
The geometry of the part being produced directly affects how easy it is to mold. Complex shapes with undercuts, thin walls, or intricate features can complicate the design process, increasing the likelihood of defects. Designing parts with uniform wall thickness, avoiding sharp corners, and incorporating draft angles ensures smooth ejection from the mold and reduces internal stresses.
Pro Tip: A draft angle of 1-2 degrees is generally recommended for easy ejection, but this can vary depending on the plastic material used. Including radii in corners instead of sharp edges also helps to distribute stress evenly.
3. Design Efficient Cooling Channels
Cooling time is a significant part of the injection molding cycle, often constituting 50-70% of the total cycle time. Efficient cooling channel design in the mold can drastically reduce cooling time, leading to faster cycle times and improved productivity. Properly placed channels ensure uniform cooling, which minimizes warping and shrinkage, resulting in more accurate parts.
Pro Tip: Use conformal cooling, which follows the contour of the mold cavity, to achieve more even cooling across complex shapes. This method can reduce cycle times and improve part quality, especially in intricate designs.
4. Use Flow Simulation Software
Leveraging modern technology, such as flow simulation software, is a game-changer in injection mold design. These tools allow designers to predict how molten plastic will flow through the mold cavity, identifying potential issues like air traps, weld lines, or short shots before physical testing. This simulation helps to optimize gate placement, runner size, and cooling systems, leading to better first-time accuracy and reduced mold rework.
Pro Tip: Use softwares for detailed analysis. This will save time and resources by minimizing trial-and-error adjustments in the design phase.
5. Pay Attention to Gate Design
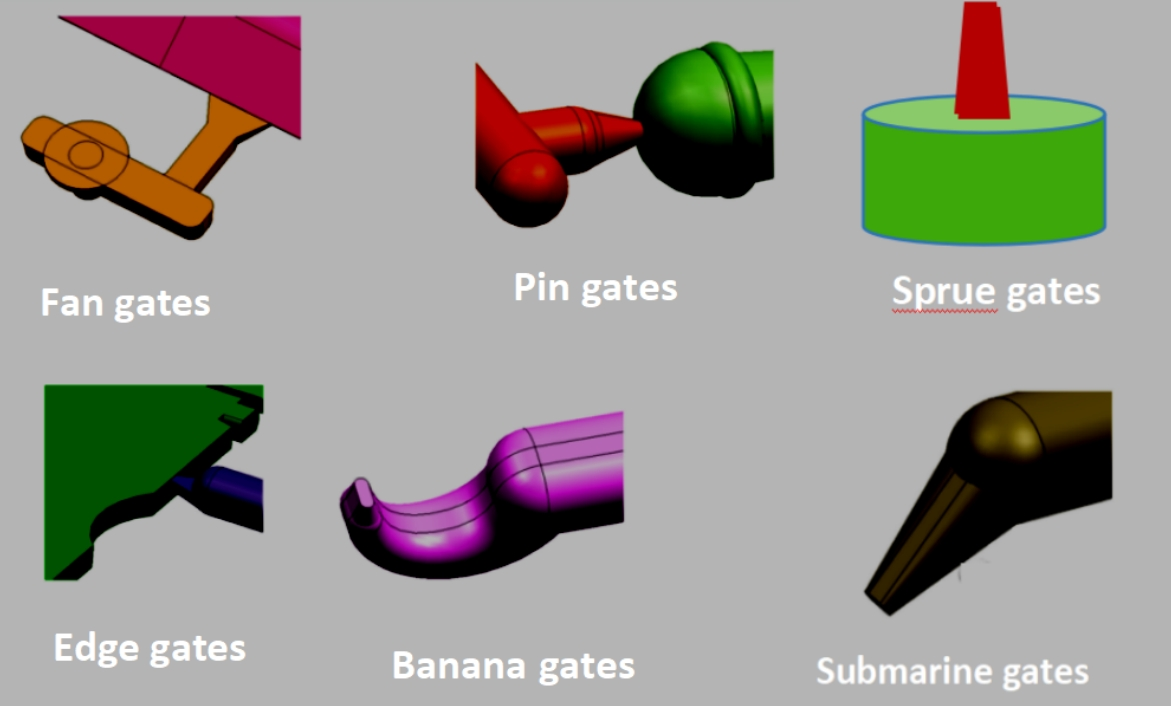
Multiple Injection Mold Design
Gates are the entry points through which molten plastic flows into the mold cavity. The location, type, and size of the gate have a direct impact on the final product’s appearance and strength. An improperly placed gate can lead to defects like sink marks or excessive residual stress in the part. It’s essential to select a gate type that suits the part’s geometry and the type of plastic being used.
Pro Tip: Consider using hot runner systems for large or complex molds to reduce material waste and improve cycle time. Cold runner systems, while simpler, can be suitable for smaller runs or less intricate parts.
3. Conclusion
Mastering injection mold design is a blend of art and science, requiring a deep understanding of materials, part geometry, cooling systems, and the latest simulation technologies. A well-designed mold not only ensures high-quality products but also optimizes production efficiency and cost-effectiveness. By following these top 5 tips—focusing on material selection, part geometry, cooling channels, simulation software, and gate design—designers can achieve better outcomes in their injection molding projects.
For injection mold design enthusiasts, continuously refining your skills and staying updated with the latest tools and techniques is key to staying competitive in this ever-evolving field. Implementing these strategies can elevate your design process and ensure consistent success in plastic manufacturing. Happy molding!
4. About EuroPlas
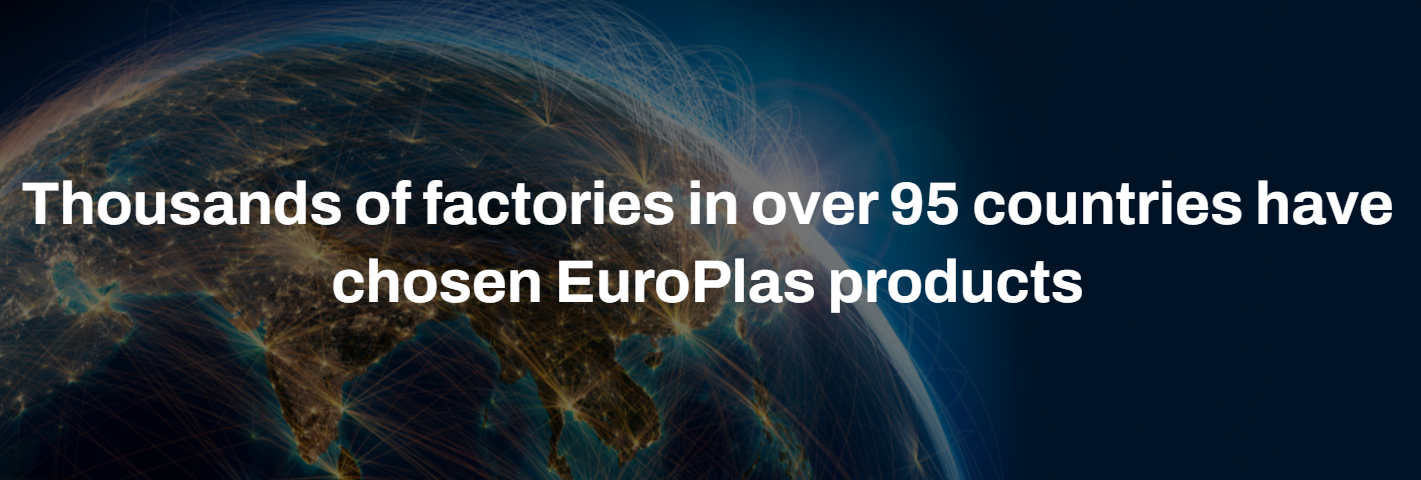
EuroPlas - No. 1 filler masterbatch manufacturer
As the world’s No. 1 filler masterbatch manufacturer, EuroPlas offers tailor-made plastic material solutions that enhance the competitiveness of plastic enterprises. With a global mindset and dedication to innovation, EuP provides materials that meet high-quality standards while ensuring sustainable development practices. EuP operates seven state-of-the-art factories, equipped with advanced technology to produce up to 0.8 million tons annually, serving industries in over 95 countries worldwide. EuP’s commitment to customer satisfaction and optimal material solutions makes it a trusted partner for companies working with plastic materials.
Looking for advanced plastic material solutions? Visit our Contact Us page to learn how EuroPlas can help your business thrive.