Ultem vs. PEEK: What are the differences?
Ultem and PEEK are two high-performance thermoplastics with unique properties and applications. It is essential to understand their differences to make informed decisions for various engineering needs. Let’s explore this topic with us!
1. Basic understanding about Ultem Plastic
Ultem plastic is a high-performance thermoplastic material known for its exceptional heat resistance, mechanical strength, and chemical resistance:
- Heat resistance: With a high glass transition temperature, Ultem can maintain its properties and dimensional stability even at elevated temperatures.
- Mechanical strength: It exhibits outstanding mechanical strength, including tensile strength and impact resistance, ensuring durability and structural integrity.
- Chemical resistance: Ultem plastic also offers excellent resistance to a wide range of chemicals, making it suitable for applications in harsh chemical environments.
Additionally, Ultem is lightweight, has exceptional electrical insulation properties, and meets stringent fire safety standards. Its versatility and reliability make Ultem plastic a preferred choice in industries such as aerospace, automotive, electrical and electronics, medical devices, and more, where high-performance materials are required.
Read more: An Introduction to Ultem Plastic: What is it?
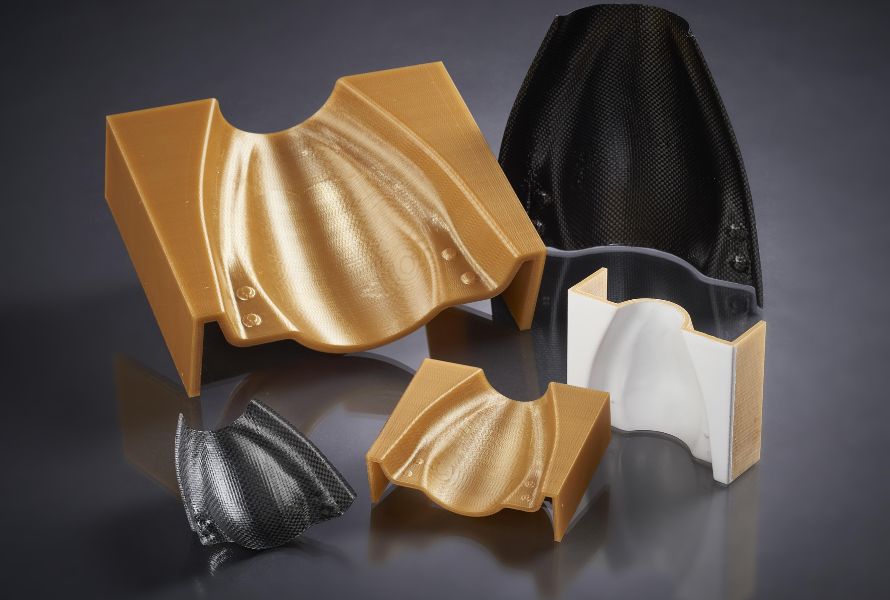
Ultem plastic is a high-performance thermoplastic material known for its exceptional properties
2. Basic understanding about PEEK Plastic
PEEK plastic is a high-performance thermoplastic known for its exceptional properties and versatility. Here are some its key properties:
- High temperature resistance: PEEK Plastic exhibits a high melting point, allowing it to withstand continuous use at elevated temperatures without significant loss of performance.
- Mechanical strength: It possesses remarkable mechanical properties, including high tensile strength, flexural strength, and impact resistance, making it suitable for applications requiring structural integrity and durability.
- Chemical resistance: PEEK plastic also demonstrates excellent chemical resistance to a wide range of acids, bases, solvents, and oils.
- Dimensional stability: Its dimensional stability ensures consistent performance under varying conditions.
PEEK is widely used in industries such as aerospace, automotive, electrical and electronics, medical devices, and oil and gas, where superior performance in demanding environments is required.
Read more: PEEK Plastic: Definitions and Applications
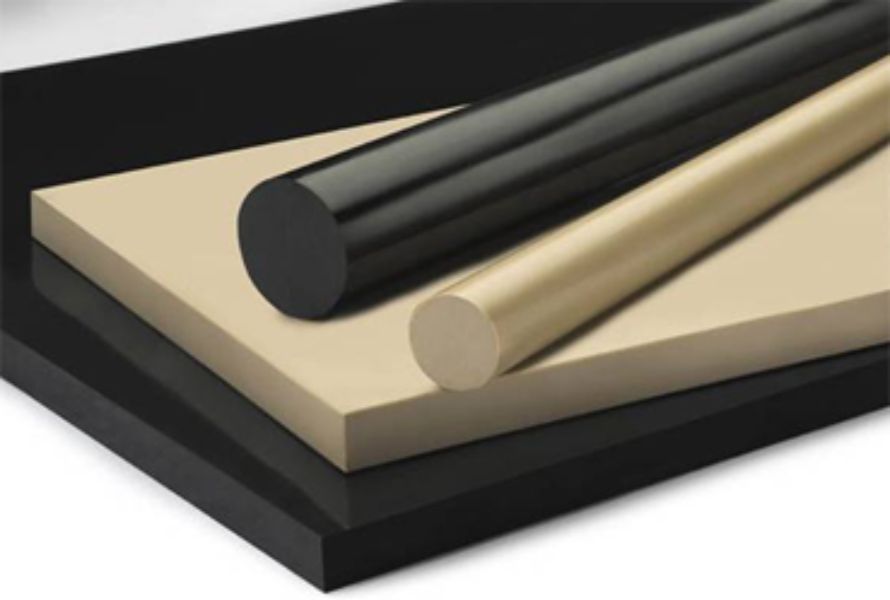
PEEK plastic is also a high-performance thermoplastic known for its exceptional properties
3. Ultem vs. PEEK: A Comparison
Ultem and PEEK are both high-performance thermoplastics with unique properties and applications. Here's a short comparison table based on properties between Ultem vs PEEK :
Properties |
Ultem |
PEEK |
Chemical Structure
|
Amorphous thermoplastic
|
Semi-crystalline thermoplastic |
Temperature Resistance
|
High, transition temperature ~217°C |
Very High, Melting Point ~343°C |
Mechanical Strength |
High |
Very High |
Chemical Resistance |
Excellent |
Excellent, Broader Range |
Electrical Insulation |
Excellent |
Excellent |
Biocompatibility |
Limited |
Biocompatible Grades Available |
Cost |
Relatively lower than PEEK |
Relatively higher than Ultem |
Application |
Aerospace, Automotive, Electrical/Electronics, Consumer Goods |
Aerospace, Automotive, Electrical/Electronics, Oil/Gas, Medical Devices, Semiconductor Manufacturing
|
3.1. Ultem vs Peek: Chemical Structure
- Ultem, also known as polyetherimide (PEI), is an amorphous thermoplastic. Its chemical structure consists of repeating units of imide groups. The amorphous structure of Ultem gives it unique properties such as transparency, good flowability during processing, and outstanding dimensional stability.
- PEEK, or polyetheretherketone, is a semi-crystalline thermoplastic. The semi-crystalline nature of PEEK means that it has both amorphous regions (the areas between the crystalline regions) and crystalline regions. The crystalline regions contribute to its high strength and stiffness, while the amorphous regions provide toughness and impact resistance.
3.2. Ultem vs Peek: Temperature Resistance
- Ultem has a high glass transition temperature (Tg) of approximately 217°C, providing excellent dimensional stability and mechanical properties at elevated temperatures.
- PEEK has a high melting point of approximately 343°C and can operate continuously at temperatures up to 260°C, making it ideal for applications requiring extreme temperature resistance.
- In summary, Ultem offers good temperature resistance with its high Tg, while PEEK surpasses Ultem with its higher melting point and ability to withstand higher temperatures.
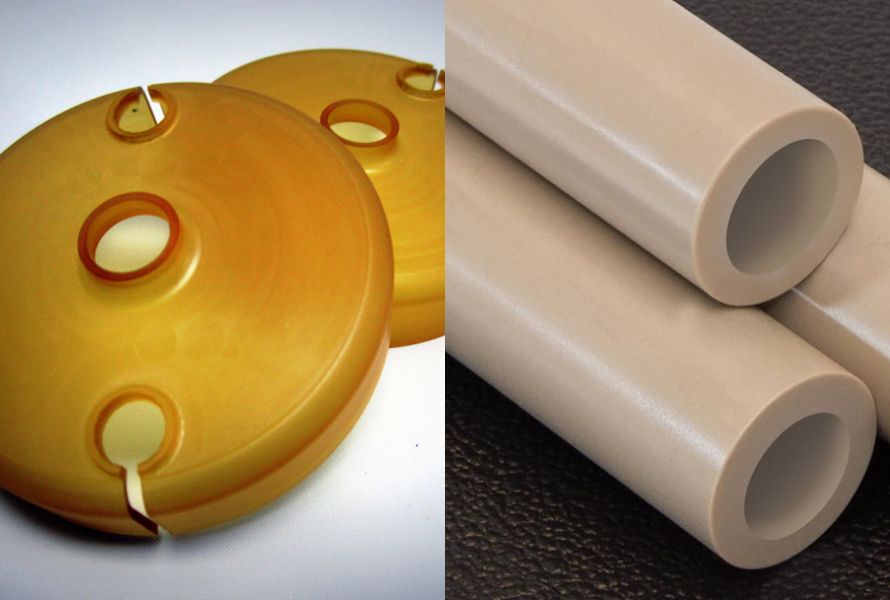
PEEK surpasses Ultem with its higher melting point
3.3. Ultem vs Peek: Mechanical Strength
- Ultem has a high tensile strength, flexural strength, and impact strength, allowing it to withstand significant loads and forces without deforming or breaking.
- PEEK excels in mechanical strength, surpassing Ultem in tensile strength, flexural strength, and impact strength. It is ideal for demanding mechanical applications..
- In conclusion, both Ultem and PEEK offer good mechanical strength, but PEEK outperforms Ultem in terms of tensile strength, flexural strength, and impact strength. PEEK's superior mechanical properties make it a preferred choice for applications that require exceptional strength and durability.
3.4. Ultem vs Peek: Chemical Resistance
- Ultem offers good chemical resistance. It can withstand exposure to acids, bases, and some solvents without significant degradation or damage. Ultem's chemical resistance makes it suitable for applications that involve contact with various chemicals.
- PEEK is highly resistant to a wide range of chemicals, including aggressive solvents, acids, bases, and industrial chemicals. PEEK's superior chemical resistance makes it a preferred choice for demanding applications in chemical processing.
- To sum up, both Ultem and PEEK offer good chemical resistance, but PEEK surpasses Ultem with its exceptional resistance to a wider range of chemicals.
3.5. Ultem vs Peek: Electrical Insulation
- Ultem possesses high dielectric strength and low dielectric constant, making it suitable for electrical and electronic applications. Ultem's electrical insulation properties contribute to its use in components such as connectors, insulators, and electrical housings.
- Meanwhile, PEEK has outstanding dielectric strength and low dissipation factor, providing superior electrical insulation properties. PEEK's electrical insulation capabilities make it an ideal choice for applications requiring high-performance electrical insulation, such as electrical connectors, circuit boards, and insulation components.
- Both Ultem and PEEK offer good electrical insulation properties, but PEEK stands out with its exceptional electrical insulation performance.

PEEK stands out with its exceptional electrical insulation performance
3.6. Ultem vs Peek: Biocompatibility
- Ultem exhibits good biocompatibility when it is considered biocompatible and suitable for use in medical and dental applications. Ultem's biocompatibility makes it a preferred choice for components such as surgical instruments, medical device housings, and dental implants.
- PEEK is highly biocompatible with a long history of successful use in medical and dental applications. PEEK's biocompatibility, combined with its mechanical and chemical properties, makes it a popular material for implants, orthopedic devices, and other medical components.
- Overall, Ultem and PEEK offer good biocompatibility, but PEEK is widely recognized for its excellent biocompatibility and has a long track record of successful use in biomedical applications.
3.7. Ultem vs Peek: Cost
- Ultem is generally more expensive than many other thermoplastics thanks to being considered a premium material due to its exceptional properties. The higher cost of Ultem is attributable to its advanced formulation and manufacturing processes.
- PEEK is also a relatively expensive material compared to common thermoplastics. It is known for its outstanding properties. The cost of PEEK is higher due to the specialized production methods required to achieve its exceptional performance characteristics.
- In summary, Ultem and PEEK are higher-priced materials compared to standard thermoplastics. Ultem tends to be relatively more expensive than PEEK, but the specific cost can vary depending on factors such as supplier, grade, and quantity purchased.
3.8. Ultem vs Peek: Application
- Ultem is well-suited for structural components and electrical applications, while PEEK excels in demanding environments such as aerospace, automotive, and medical fields.
- Consider the specific requirements of your application when choosing between Ultem and PEEK to ensure the best performance and suitability for your needs.
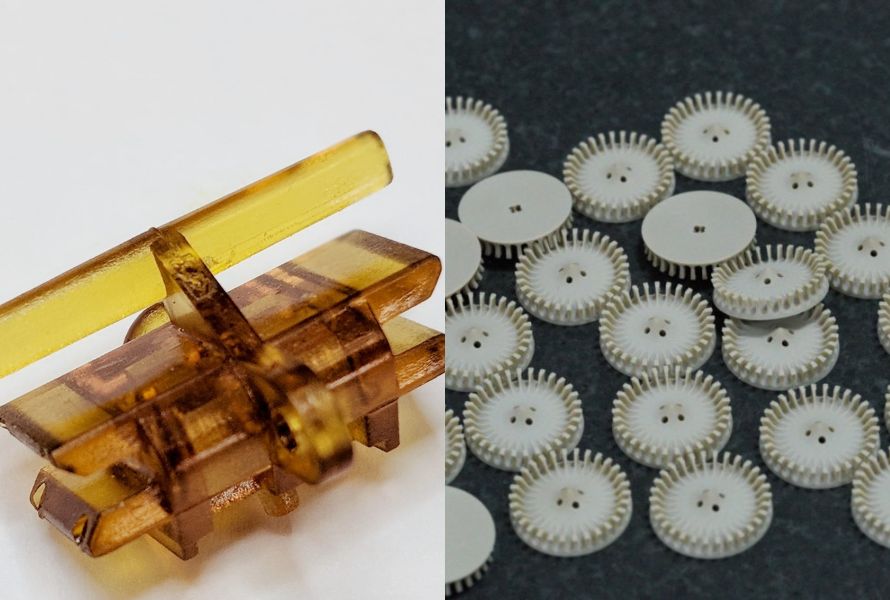
Ultem is well-suited for electricity while PEEK excels popularly in aerospace, automotive, and medical fields
4. Conclusion
Understanding the differences between Ultem and PEEK is crucial for selecting the appropriate material for specific engineering requirements.
Ultem offers good temperature resistance, chemical resistance, and cost-effectiveness, making it suitable for various applications. On the other hand, PEEK excels in extreme temperature environments, exhibits superior mechanical properties, and provides broader chemical resistance.
By considering the specific needs of a project and balancing performance and cost factors, one can make an informed decision between Ultem and PEEK, ensuring optimal material selection for the desired application.
We trust that this article has furnished you with valuable and enlightening information. To remain up-to-date with the most recent updates, we encourage you to explore other informative articles on our blog.
Additionally, when it comes to procuring high-performance plastics, EuroPlas is your dependable supplier to reference. With over 15 years of experience in the industry and an unwavering dedication to providing top-notch materials, we have solidified our position as a trustworthy partner for manufacturers in various sectors. Please don't hesitate to contact us HERE.