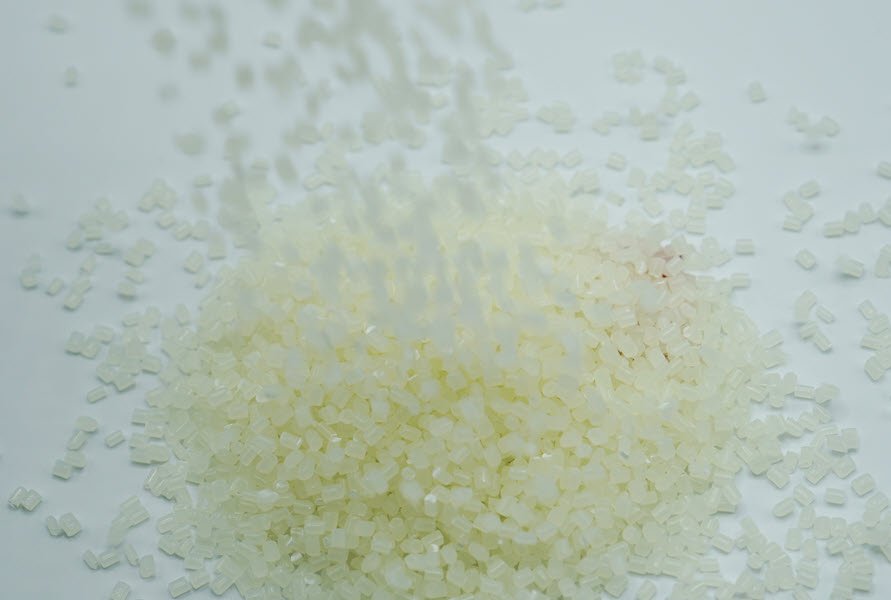
Since plastics are so commonplace nowadays, some of them inevitably come into contact with sunlight. Unfortunately, most plastics are destroyed by ultraviolet (UV) radiation from sunshine. That is why it’s important to understand UV stabilized vs UV resistant as any item intended for outdoor usage must be made from polymers that have been treated to have high resistance to UV light.
However, a lot of people are still unclear about the distinction between these two terms. Therefore, in today's essay, we'll look more closely at the phrases "UV stabilized" vs"UV resistant," including their definitions and examples of usage. Let's get going!
Related:
- Automotive UV stabilizers - All you should know
- UV stabilizers for plastics - everything you need to know
- Why are UV Masterbatches expected to be a key product for the Indian market?
- UV stabilizers in plastic: 4 common types and applications
1. UV radiation and its effects on plastic products
1.1. Definition
UV radiation is electromagnetic energy with a frequency greater than visible light but lower than X-ray radiation. UV radiation may be created artificially using UV lamps, however sunlight is the only natural source of the radiation. When you're outside, UV light either burns your skin a little (to get a tan) or a lot (to have a sunburn).
Although UV radiation cannot be seen by the human eye, it has the power to harm a wide range of materials, including polymer plastics and human skin. The bulk of UV radiation is blocked by the Earth's atmosphere, but some still gets through, making it necessary to shield both organic stuff (like your skin) and non-organic matter (such device parts and electronics enclosures) from its damaging effects.
1.2. Effects
A material's molecular chains are susceptible to disruption and damage by UV radiation, which can cause the molecules to disintegrate and lose their structural integrity. The extremely reactive, unpaired electron atoms known as free radicals are created as the molecules disintegrate. For plastic materials that must spend a lot of time outside, photodegradation—also known as deterioration—is a significant challenge.
When it comes to polymer plastics, chromophores—atoms and atom groups—play a key role. These molecules give polymers their colors, but because of how they interact with light, they are also susceptible to damage from UV rays. The chromophore's breakdown produces free radicals that start to damage the plastic's molecular structure.
Photodegrading plastics start to crack, get discolored, and lose their strength and elasticity. For the delicate parts of electrical equipment, many of which are made of plastic, this might be disastrous. After prolonged exposure to intense sunlight, an electronics enclosure itself can start to deteriorate, increasing the vulnerability of the components inside.
2. Differentiating UV inhibited, UV stabilized, and UV resistant for plastic
2.1. UV stabilized
Definition
“UV stabilized”, also known as “UV inhibited”, implies that a stabilizer has been applied to the resin to increase UV stability of plastics or protect it from long-term breakdown caused by UV radiation.
UV stabilizers are chemicals that stop the chemical reaction known as "photodegradation," which takes place when ultraviolet radiation from the Sun or artificial light sources breaks down chemical bonds in a polymer. UV stabilizers reduce damage by absorbing or screening off UV light.
Although different materials may differ in their UV resistance, most plastics need UV stabilizers or additives to increase their UV resistance.
Applications
UV-stabilized resins can be used to make many different types of UV stabilized plastic including PVC and polycarbonate films, reinforced plastic sheets such as fiberglass, glass fiber reinforced plastics (GRPs), polyester film and sheeting materials such as PET.
The main application for UV stabilized resins is for making UV stabilized plastic for outdoor applications, where the resin has been exposed to sunlight over a period of time. It can be used on plastic surfaces such as boats, car bodies, and sports equipment.
UV-stabilized resins are also used in industrial adhesives where they need to be able to withstand long exposure to sunlight and other weather conditions.
2.2. UV resistant
Definition
UV resistance for plastic is a term that refers to the ability of certain plastics to withstand ultraviolet radiation without being damaged or destroyed. UV resistant plastics offer many advantages over other types of plastics, such as their resistance to heat, cold, or chemicals, while maintaining great strength and rigidity.
Depending on the use of your product and other project criteria, your material will need to have more or less UV resistance. In order to retain the highest level of quality and performance, components for outdoor usage and industrial applications typically need a greater level of UV protection.
As mentioned before, different materials differ in their UV resistance. The following are the top 5 plastics with the highest UV resistance.
- Acrylic
- High Density Polyethylene (HDPE)
- Polycarbonate
- Polyamide-Imide (PAI)
- Polyvinylidene Fluoride (PVDF)
Applications
UV-stabilized plastics are used in many industries including construction, transportation, food packaging, healthcare, and agriculture. For external uses including outdoor signs and displays, light fixtures, ornamental panels, colored lenses, open-air infrastructure, containers, and so on, plastics with strong UV resistance are frequently used.
3. Finding UV additive for plastic?
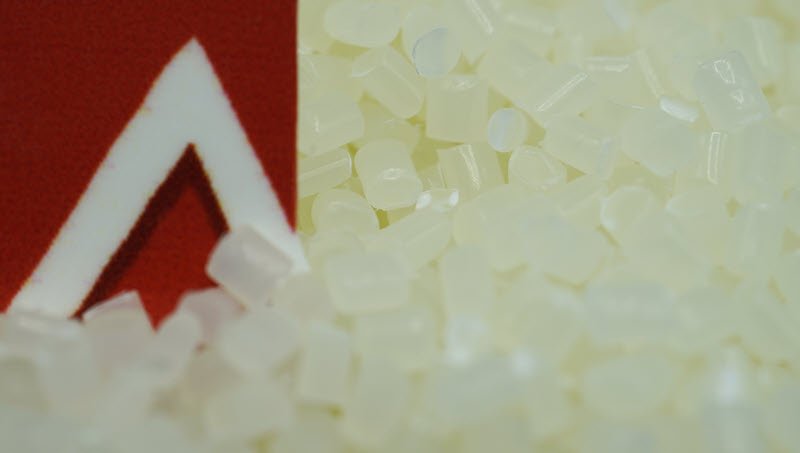
The plastic use is higher than ever, and the demand for UV additives for plastic is also increasing. But how do you know if your supplier is up to the task? EuroPlas is a trusted masterbatch supplier with an impressive range of UV additive for plastic products.
EuroPlas is a leading masterbatch manufacturer in the plastic industry with over 15 years of experience. We offer a wide range of additives and masterbatches for plastics, including UV additives, which are manufactured at our dedicated facility.
Our products are selected from among the most advanced materials available on the market, resulting in superior quality and performance. Our products are manufactured using the latest technology and with strict quality controls, ensuring that each batch meets or exceeds all standards.
We have has been supplying the highest-quality UV additive for plastic to many industrial clients over the years. But what really sets us apart from other suppliers is our ability to provide high-quality products at competitive prices. So if you need UV additives for plastic, please contact us for more information about our products or services.