Vacuum Forming vs. Pressure Forming: What Are The Differences?
Thermoforming technology is a widely used process in the plastic manufacturing industry, where plastic sheets are heated to a pliable forming temperature, molded to a specific shape, and then trimmed to create usable products. Among the various methods of thermoforming, vacuum forming and pressure forming stand out as two prominent techniques. This article will explore the differences between vacuum forming vs pressure forming, helping you understand which method best suits your specific needs.
1. What Is Vacuum Forming?
Definition of Vacuum Forming
In the context of vacuum forming vs pressure forming, vacuum forming is a streamlined thermoforming process where a plastic sheet is heated to a pliable state and then formed over a mold using vacuum pressure.
Read more: Vacuum forming plastic - The ultimate guide.
Read more: Vacuum forming plastic - The ultimate guide
Vacuum Forming steps
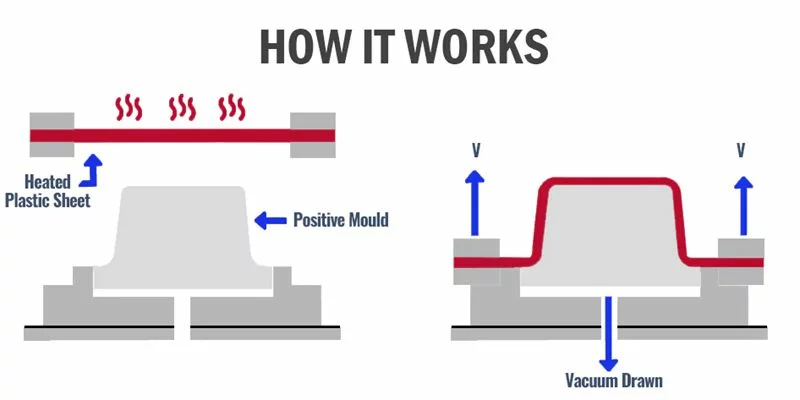
In the comparison of vacuum forming vs pressure forming, understanding the vacuum forming steps is essential to grasp the nuances of each process.
Vacuum forming involves several key steps to shape plastic sheets into desired forms. First, a plastic sheet is clamped securely in place and then heated until it reaches a pliable state. Once the plastic is sufficiently soft, it is draped over a mold. A vacuum is then applied to remove the air between the plastic sheet and the mold, causing the plastic to conform tightly to the mold's contours. After the vacuum shapes the plastic, it is allowed to cool and harden. Finally, the formed plastic is trimmed to remove any excess material, resulting in the finished product.
This straightforward yet effective process makes vacuum forming ideal for producing a variety of items, from packaging and trays to automotive parts, efficiently and cost-effectively.
Types of plastics used
In the discussion of vacuum forming vs pressure forming, the types of plastics used play a crucial role in determining the suitability and performance of each process. Common plastics used in vacuum forming include:
- Acrylonitrile Butadiene Styrene (ABS), is known for its strength and impact resistance
- Polycarbonate, valued for its clarity and toughness;
- Polyethylene is appreciated for its flexibility and chemical resistance;
- Polystyrene, chosen for its ease of forming and cost-effectiveness;
- PETG (Polyethylene Terephthalate Glycol), which offers excellent clarity and durability.
Each of these plastics brings specific properties that make them ideal for different applications, whether it's for creating durable automotive parts, clear packaging, or flexible containers. The choice of plastic can significantly affect the efficiency, quality, and cost of the manufacturing process, highlighting the importance of selecting the right material for vacuum forming vs pressure forming projects.
Applications of Vacuum Forming
In the vacuum forming vs pressure forming debate, the applications of vacuum forming highlight its versatility and efficiency across various industries:
- Packaging: Vacuum forming is widely used to create blister packs, clamshells, and trays that require precise shapes and protection for products.
- Automotive Industry: It is employed to manufacture interior components like dashboards and door panels, benefiting from the method’s ability to produce durable and lightweight parts.
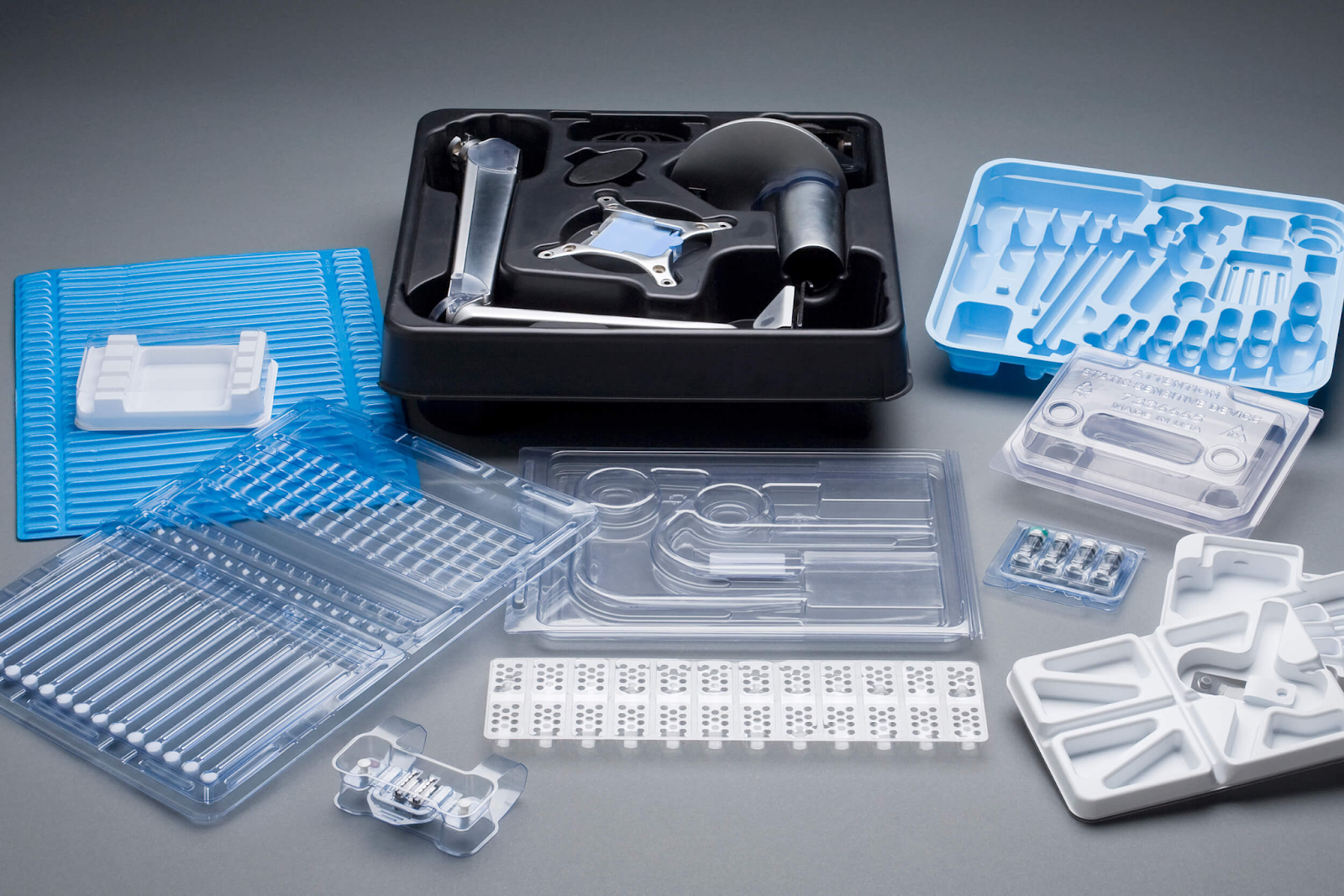
- Medical Field: Vacuum forming is used to create custom trays, housings for medical devices, and ergonomic supports.
- Consumer Goods: It is prominent in the production of plastic containers, display stands, toys, and other everyday items.
- Construction: Vacuum forming is utilized to produce various construction components, such as wall panels and protective covers.
This broad range of applications underscores the adaptability of vacuum forming in meeting diverse manufacturing needs efficiently and cost-effectively.
2. What Is Pressure Forming?
Definition of Pressure Forming
In the comparison of vacuum forming vs pressure forming, understanding the definition of pressure forming is crucial. Pressure forming is an advanced thermoforming technique that involves heating a plastic sheet until it becomes pliable, then using high-pressure air to force the sheet against a detailed mold. This process allows for the creation of highly detailed and textured surfaces, making it ideal for applications requiring intricate designs and precise features.
Unlike vacuum forming, which relies solely on vacuum pressure, pressure forming utilizes additional air pressure to achieve sharper details and tighter tolerances. This makes it a preferred method for producing high-quality, aesthetically pleasing parts, such as medical device housings, automotive panels, and consumer electronics enclosures.
Pressure Forming steps
In the examination of vacuum forming vs pressure forming, it's essential to understand the steps involved in pressure forming to appreciate its advantages.
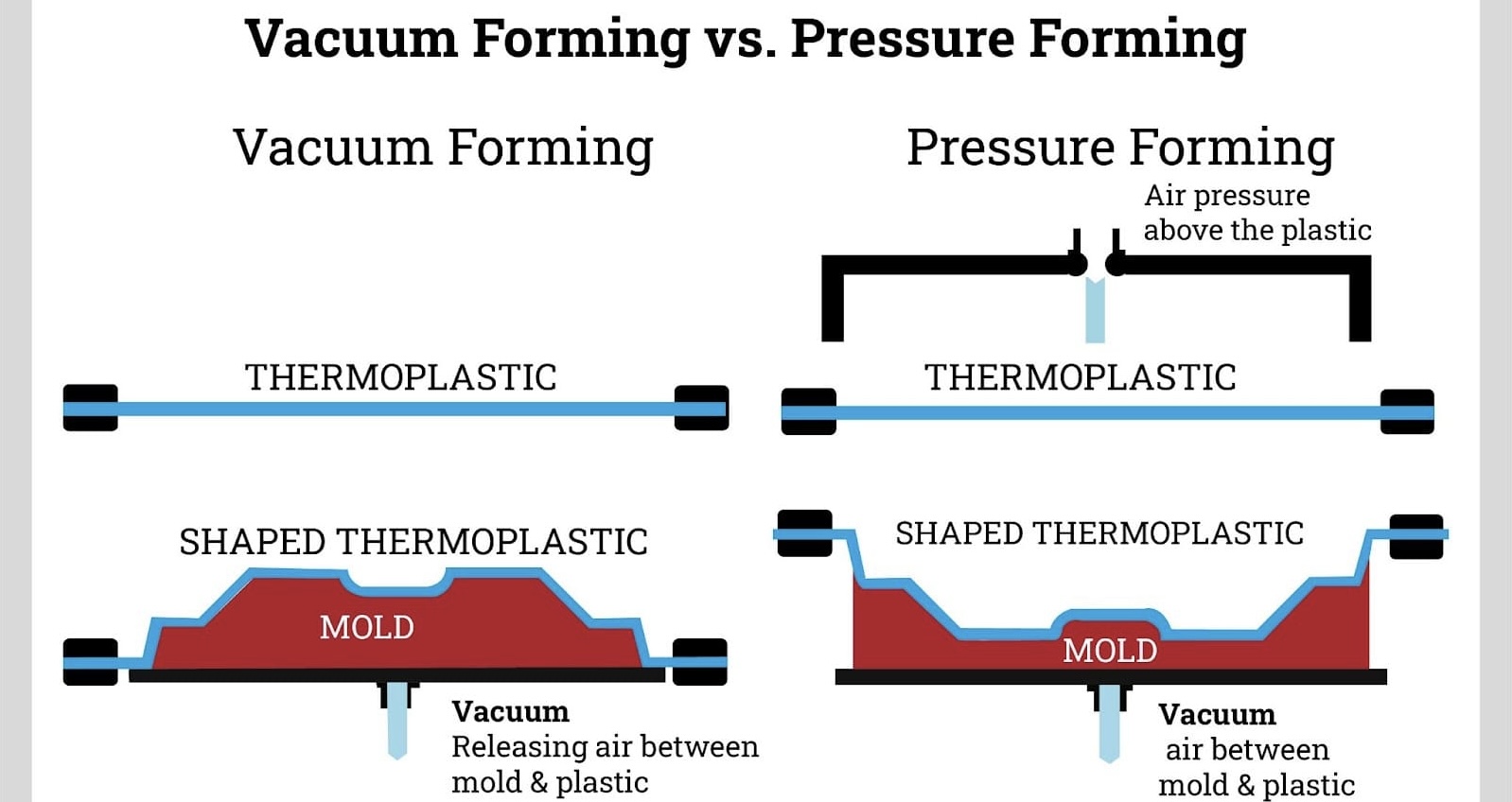
The pressure forming process begins by clamping a plastic sheet securely in place and then heating it until it reaches a pliable state. Unlike vacuum forming, which uses vacuum pressure alone, pressure forming employs both vacuum and high-pressure air. After heating, the plastic sheet is placed over a detailed mold, and high-pressure air is applied to press the sheet tightly against the mold's surface. This high pressure ensures that the plastic conforms precisely to the mold, capturing fine details and textures. Once the plastic cools and solidifies, it is removed from the mold and trimmed to achieve the final shape.
This process results in high-quality, detailed products, making pressure forming ideal for applications requiring precision and intricate designs.
Types of plastics used
When exploring the differences between vacuum forming vs pressure forming, understanding the types of plastics used in pressure forming is essential. Pressure forming utilizes a variety of plastics chosen for their specific properties and performance characteristics. Common types of plastics include:
- Polycarbonate (PC) is renowned for its impact resistance and ability to withstand high temperatures.
- High-density polyethylene (HDPE) is cost-effective and valued for its resistance to impacts, chemicals, and cold temperatures.
- Thermoplastic polyolefin (TPO) is recognized for its durability and impact resistance.
- High-impact polystyrene (HIPS) is economical and available in a wide range of colors.
- Polyvinyl chloride (PVC) offers impact resistance and is available in various colors, textures, and grades with flame-retardant properties.
These plastics are selected based on the requirements of the application, whether it involves creating robust automotive parts, clear medical device housings, or intricate consumer electronics enclosures. Each type of plastic brings unique advantages to the pressure forming process, ensuring that manufacturers can achieve precise, high-quality results tailored to their specific needs and industries.
Applications of Pressure Forming
When comparing vacuum forming vs pressure forming, understanding the applications of pressure forming highlights its versatility and precision in various industries. Pressure forming excels in several applications:
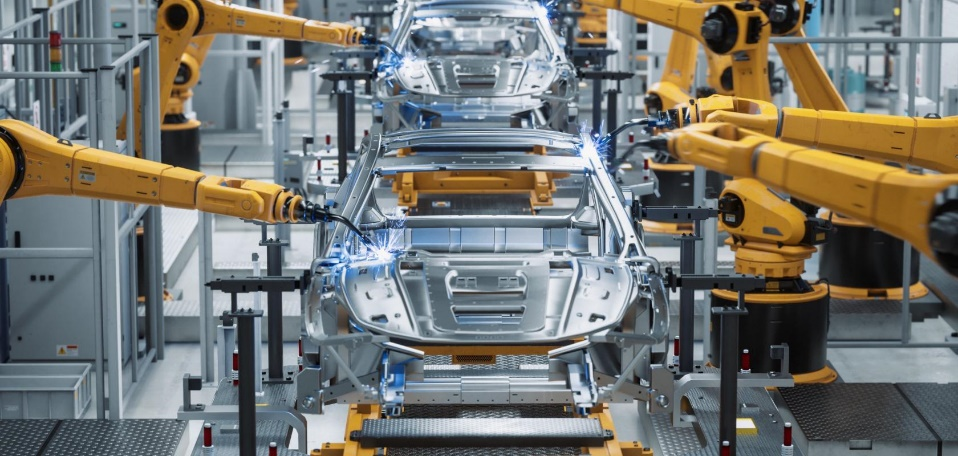
- Automotive Industry: Pressure forming is used extensively to manufacture intricate interior components such as dashboards and door panels, requiring detailed designs and durability.
- Medical Devices: It is crucial to create precise housings and components for medical devices, ensuring exact specifications and robust protection.
Ex: In the medical field, pressure forming is used to create precise housings and components for devices such as MRI machines. These housings must meet exact specifications to ensure compatibility with sensitive electronic components and provide robust protection against external influences.
- Consumer Electronics: Pressure forming is employed to produce sleek and durable enclosures for electronic devices, meeting high-quality finish and dimensional accuracy requirements.
Ex: Pressure forming plays a crucial role in manufacturing sleek and durable enclosures for high-end smartphones. These enclosures not only meet stringent aesthetic requirements but also ensure dimensional accuracy to house sensitive electronic components securely.
- Industrial Equipment: It is utilized for manufacturing various industrial equipment components that require strength, precision, and resistance to harsh environments.
Ex: Pressure forming is employed in the production of robust components for industrial machinery, such as conveyor belt systems used in manufacturing plants. These components require strength to withstand heavy loads, precision to ensure smooth operation, and resistance to harsh environments including exposure to chemicals and extreme temperatures.
- Aerospace: Pressure forming finds applications in aerospace for producing lightweight yet durable components, contributing to fuel efficiency and performance enhancements.
Ex: In aerospace applications, pressure forming is utilized to fabricate lightweight yet durable components for aircraft interiors, such as overhead luggage bins. These components contribute to enhancing fuel efficiency by reducing overall weight while maintaining structural integrity to meet rigorous safety standards
Overall, pressure forming stands out for its ability to meet stringent design requirements across automotive, medical, and consumer electronics industries with superior efficiency and accuracy.
3. Vacuum Forming vs. Pressure Forming: Key Differences
Here's a comparison table highlighting the key differences between Vacuum Forming and Pressure Forming:
Aspect
|
Vacuum Forming
|
Pressure Forming
|
Process
|
Uses vacuum pressure to shape heated plastic sheets.
|
Uses both vacuum and additional air pressure to form plastic.
|
Complexity of Details
|
Suitable for simpler shapes and designs.
|
Capable of creating intricate details and textures.
|
Surface Finish
|
Generally results in a smoother surface finish.
|
Offers higher-quality surface finishes with fine details.
|
Material Thickness
|
Best for thinner materials.
|
Can handle thicker materials effectively.
|
Production Speed
|
Faster production speeds for simpler shapes.
|
Slower than vacuum forming due to additional steps.
|
Tooling Cost
|
Lower tooling costs compared to pressure forming.
|
Higher tooling costs due to more complex molds and equipment.
|
Cost Efficiency
|
Generally more cost-effective for simpler shapes and designs.
|
Higher initial costs but more cost-effective for complex parts.
|
Applications
|
Packaging, trays, basic automotive components.
|
Automotive interiors, medical device housings, electronics.
|
Detail and Texture
|
Limited ability to achieve intricate details and textures.
|
Capable of precise detailing and textured surfaces.
|
This table provides a concise overview of the differences between vacuum forming and pressure forming, helping you to understand their respective strengths and applications in manufacturing.
4. Vacuum Forming vs. Pressure Forming: Which One Should You Choose?
When deciding between vacuum forming vs pressure forming, it's crucial to carefully assess your specific manufacturing needs and product requirements.
Vacuum forming is particularly well-suited for applications prioritizing cost-efficiency and simplicity in design. It excels in producing a wide range of items, including packaging, trays, and basic automotive components that require straightforward shapes and economical production processes. This method leverages vacuum pressure to shape heated plastic sheets over molds, offering a streamlined approach to manufacturing.
In contrast, pressure forming offers advanced capabilities, making it ideal for projects demanding intricate details, textures, and precise dimensions. This technique combines vacuum pressure with additional air pressure to achieve higher levels of mold detail and surface finish quality. Industries such as automotive manufacturing, medical device production, and high-end consumer electronics benefit from pressure forming ability to create complex parts like automotive interiors, medical device housings, and durable enclosures.
When choosing between vacuum forming and pressure forming, several critical factors come into play. These include the complexity of the design, desired surface finish, material thickness considerations, and the scale of production. Evaluating these factors thoroughly is essential to determine which thermoforming technique aligns best with your specific production goals and budget constraints. By understanding the strengths and applications of each method, you can make an informed decision that optimizes manufacturing efficiency and product quality.
5. Conclusion
In conclusion, when choosing between vacuum forming vs pressure forming, understanding their unique advantages is crucial. Vacuum forming is cost-effective and efficient for simpler designs and packaging solutions, while pressure forming excels in precision and versatility, particularly for intricate details in the automotive, medical, and consumer electronics industries. Your decision should hinge on factors like cost-efficiency, design complexity, and desired finish. By evaluating these aspects carefully, you can select the optimal thermoforming technique—vacuum forming or pressure forming—that best meets your specific manufacturing needs and business goals.
6. About EuroPlas
As a reliable partner to numerous clients, EuroPlas offers extensive solutions and support, from material selection to customization and production. With a dedication to continuous customer satisfaction, EuroPlas has demonstrated its outstanding capability in delivering for organizations working on high-performance material projects.
For further details about our services, including innovative solutions for your project, visit our website at EuroPlas. Don’t forget to check out our blog, which contains a wealth of information on different plastic materials and production development solution