Vacuum forming is a widely used process for producing high-quality plastic parts and components. This is a versatile and cost-effective process that is well-suited for producing large, simple parts with shallow depth and uniform wall thickness. Whether you are new to vacuum forming or an experienced professional, this guide on vacuum forming plastic will provide you with an in-depth understanding of the process and its applications.
Related:
- 3 layer blown film extrusion process
- Difference between thermoforming and injection molding
- Types of plastic extrusion and its manufacturing process
- How to print on plastic? 7 common methods you should know
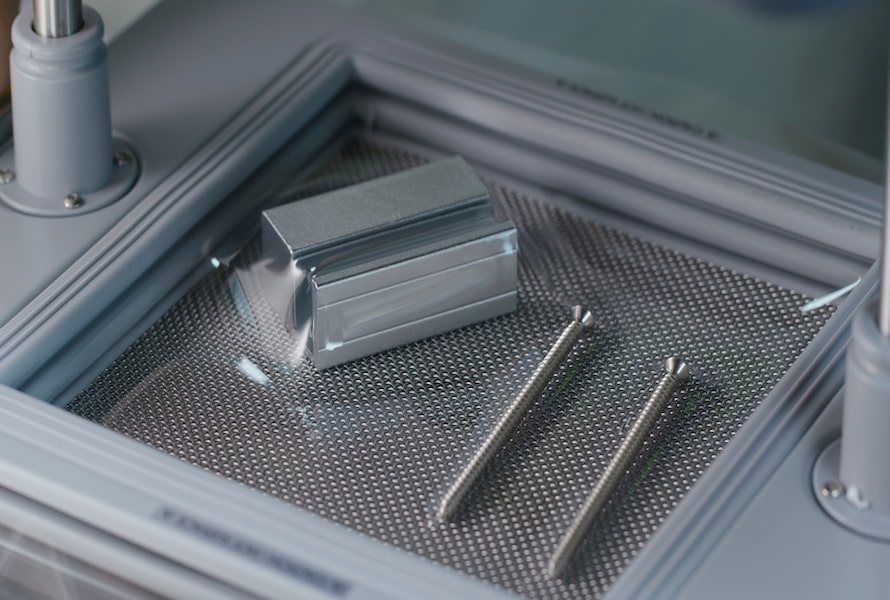
1. What is vacuum forming plastic?
Definition
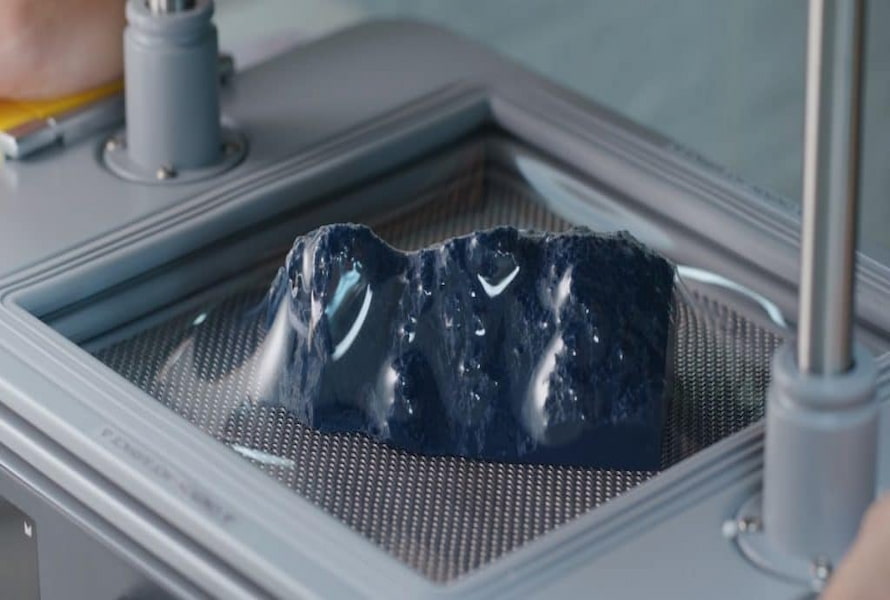
Vacuum-forming plastic, sometimes known as thermoforming, is a manufacturing process that uses heat and pressure to shape plastic sheets into complex three-dimensional parts. The process starts with a flat sheet of plastic that is heated until it becomes pliable, and then it is placed over a mold. Air is then removed from the mold, creating a vacuum that pulls the heated plastic into the mold to take on the desired shape. Once the plastic has cooled, the mold is opened and the finished part is removed.
Plastic vacuum forming is a versatile and cost-effective alternative to traditional injection molding, which can be more expensive and time-consuming for low-volume production runs. The process is also well suited for producing large or complex parts, such as automotive parts, electronic housings, and packaging components.
In addition to its versatility and affordability, vacuum-forming plastic is also environmentally friendly. The plastic sheets used in vacuum forming are made from recyclable materials, and the process generates very little waste compared to other manufacturing methods. This makes vacuum forming an attractive option for companies looking to reduce their carbon footprint and increase sustainability. With its versatility, affordability, and environmental benefits, vacuum-forming plastic is increasingly becoming a preferable choice for many companies.
2. Pros and cons of vacuum forming plastic
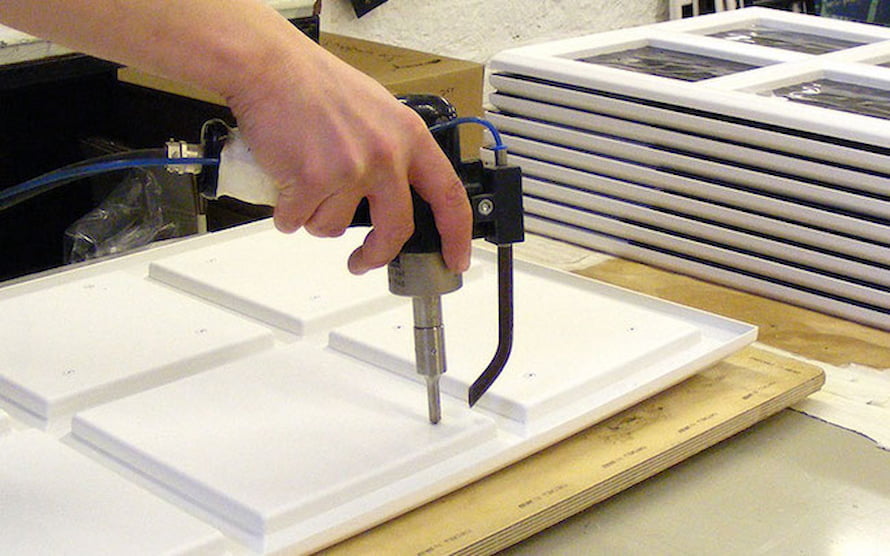
Pros
There are several advantages of vacuum-forming plastic:
Cost-effectiveness
Particularly for comparatively smaller production runs (around 200-300 units/year), vacuum forming is a relatively low-cost manufacturing process, especially compared to other manufacturing methods, such as plastic injection molding. This makes it an attractive option for businesses looking to create high-volume products at an affordable price point.
The decreased costs associated with tooling and prototyping are primarily responsible for the more accessible price point of vacuum forming. When compared to the cost of tooling for vacuum forming, the cost of tooling for injection molding may be anywhere from two to three times higher, depending on the surface area of the components that are being created and the size of the clamp frame. This makes it an attractive option for businesses looking to create high-volume products at an affordable price point.
Versatility
With vacuum forming, designers and producers have the freedom to test out new ideas and create prototypes without incurring significant costs or delays. In contrast to conventional manufacturing techniques, molds may be simply replaced and/or modified since they can be built of wood, metal, structural foam, or polymers that have been 3D printed. It can be used to create everything from simple packaging to complex toys, and everything in between.
Additionally, vacuum forming enables designersto provide clients with more color choices and customization possibilities. This provides numerous firms the ability to create personalized items with one-of-a-kind designs for customers at a reasonable price, like dental retainers.
Quick production time
Because tooling can be manufactured more quickly with vacuum forming, the overall production process can be completed much more quickly than with other traditional methods. In most cases, the amount of time necessary to develop tooling for vacuum forming is approximately one-half of the amount of time required to produce tooling for injection molding.
When 3D printers are utilized to manufacture molds, the turnaround time may be further reduced to a more manageable level. Because it improves the efficiency of the production process, vacuum forming makes it possible for businesses to speed up the delivery of new product designs to customers.
Lightweight
Many products created through vacuum-forming plastic are lightweight, making them easy to handle and transport. This is an important consideration for businesses that need to move large quantities of products from one location to another.
Environmentally friendly
Vacuum forming is a relatively low-waste process and can be used to produce environmentally friendly products, such as recycled plastic parts.
In short, vacuum-forming plastic is a cost-effective, versatile, and efficient manufacturing process that is used to create a wide variety of products. Whether you're looking to create packaging, toys, or signs, vacuum-forming plastic is a great option to consider.
Cons
While vacuum forming offers a number of benefits, it does have some limitations. Here is a more detailed explanation of the disadvantages of vacuum-forming plastic:
Limited material options
Vacuum forming is limited to using thermoformable plastics, which are plastics that can be heated and molded into various shapes. This limits the types of plastic that can be used in the process, and some materials may not meet specific product requirements in terms of strength, durability, or chemical resistance. For example, vacuum forming may not be suitable for products that need to be heat-resistant, UV-resistant, or flame-retardant.
Thickness limitations
The plastic material used for vacuum forming must be of a certain thickness to withstand the vacuum pressure and maintain the structural integrity of the final product. This means that products with complex shapes or very thin walls may not be feasible with vacuum forming, as the plastic material may become too thin or distorted during the molding process.
Strict requirements on surface quality
Vacuum-formed products often have visible flow lines or marks from the mold, which can affect the appearance and texture of the final product. Additionally, the surface of vacuum-formed plastic may be porous, which can lead to problems with paint adhesion or cosmetic defects. Improving the surface quality of vacuum-formed products typically requires additional processing, such as sanding or filling, which adds to the production time and cost.
Exceeded tooling cost for small businesses or startups
Making a vacuum-forming mold can be expensive, especially for low-volume production runs. The mold must be carefully designed and manufactured to produce the desired shape and surface finish, which can add significantly to the cost of producing vacuum-formed products. This cost can be particularly prohibitive for small businesses or startups.
Generally speaking, vacuum forming has more advantages than disadvantages. Vacuum forming is probably a smart choice if the product or component you're manufacturing isn't too thick or complicated. Additionally, short-run production is advised to use it. If your project has any of these characteristics, you should talk to your manufacturer about vacuum-forming possibilities.
3. Applications of vacuum forming plastic
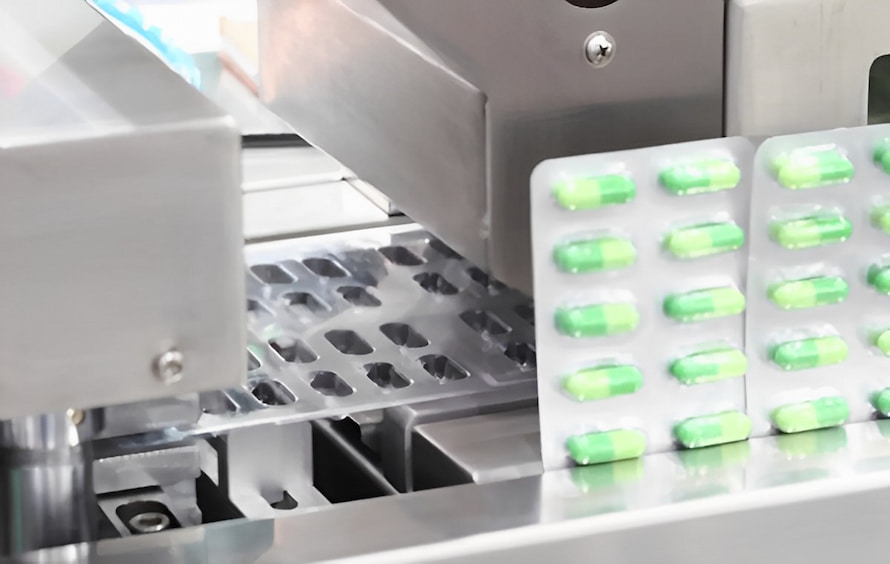
In modern society today, it would be difficult to go an entire day without coming into touch with at least one vacuum-formed component. Many different parts are created using this manufacturing technique across a wide range of sectors, including:
Packaging
Vacuum forming is commonly used to produce packaging for a wide range of products, including food, electronics, medical devices, and consumer goods. Vacuum-formed trays, clamshells, and blister packs provide an effective way to protect and display products while providing a clear view of the contents. Moreover, vacuum-formed packaging can also be customized to fit specific product shapes and sizes, hence, becomes a flexible and cost-effective solution for packaging needs.
Thermoformed Parts
Vacuum forming is used to produce a variety of thermoformed parts for a wide range of industries, including automotive, aerospace, and medical. These parts can be used as replacement parts or as custom components for specific applications.
Protective Equipment
Vacuum-formed plastic is commonly used to produce protective equipment, such as motorcycle helmets, sports equipment, and protective gear. The process allows for the creation of intricate shapes and designs, which can improve the performance and comfort of the final product. Vacuum-formed protective equipment is lightweight, durable, and can be customized to fit the specific needs of the user.
Signage and Display Components
Vacuum-formed plastic can be used to produce signs, trade show displays, and other marketing materials. The process is cost-effective and allows for the creation of eye-catching designs and shapes. Vacuum-formed signs and displays are lightweight and durable, and increasingly becoming an optimal choice for Signage and Display components manufacturing companies.
Toy and Hobby Parts
Vacuum-formed plastic is used to produce a variety of parts and components for toys and hobby products, including model cars, airplanes, and boats. The process allows for the creation of intricate shapes and designs at a relatively low cost.
These are just a few of the many applications of vacuum-formed plastic, and the versatility of the process has led to its widespread use across a variety of industries. Vacuum forming continues to be a popular and cost-effective solution for a wide range of plastic forming needs.
4. Process of vacuum forming plastic
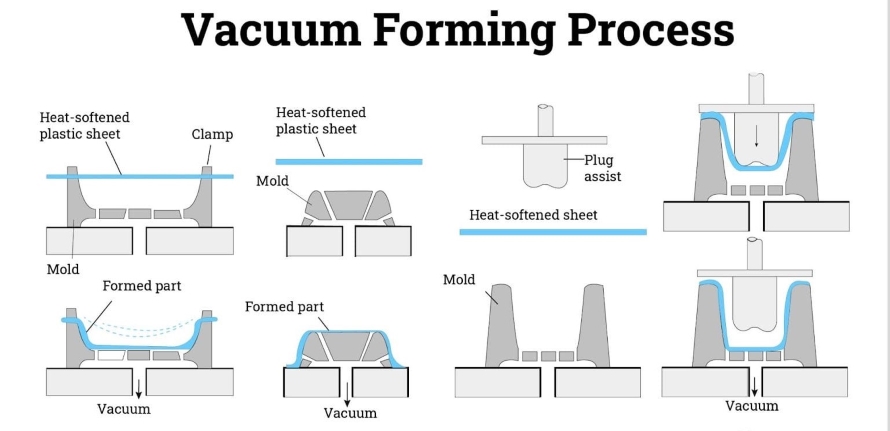
Different vacuum-forming procedures are necessary for efficient and successfulplastic molding. The following is an explanation of how the step-by-step process of vacuum forming works:
Step 1: Clamping
The machine's clamps hold the plastic sheet in place, therefore they need to be sturdy enough to hold the material in place. From 6 mm with a single heater to 10 mm with a dual heater, this clamp can hold and mold the thickest material. To prevent any accidents, all the moving parts must be linked and protected if the machine is automated.
Step 2: Heating
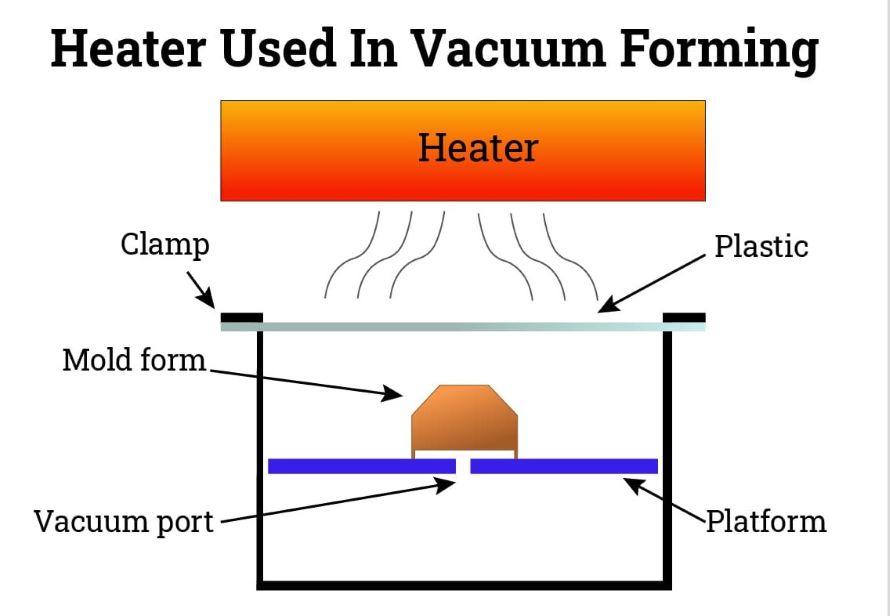
Heaters are infrared elements that are mounted within an aluminum reflector plate and are employed in the vacuum forming process. In this procedure, any material may be utilized, but it's important to make sure that the sheet is heated uniformly throughout its thickness.
Energy controllers are required in each zone to manage the material's ideal temperature for this function. If pyrometers are coupled to a temperature-controlling system, it will be easier to determine the exact melting temperature of the materials.
It is advised to use a dual quartz heater when working with thick sheets since it increases heat penetration to thicker materials and distributes heat more evenly throughout the sheet's surface. These heating techniques can aid in the precise and economical distribution of heat.
Step 3: Sheet Level (Auto-Level)
The reason why plastic doesn't sag is due to sheet leveling, which is not accessible on all machines. The device that scans the heater and the melted plastic sheet is equipped with a photo-electric beam. The way it works is that once the beam is broken and the melted sheet sags down, a little amount of air is pumped into the sheet to lift it up and prevent it from sagging down again.
Step 4: Pre-Stretch (Bubble)
This procedure stretches the plastic sheet to provide an equal thickness over its whole surface once it has melted and is prepared to go into the mold. To prevent any disfigurement, several tools, including vacuum plug assistance and air pressure, ensure that the plastic is pre-stretched.
Step 5: Plug Assist
Stretching is followed by a stage where a plug is employed to provide support. Plug-assisted vacuum forming is used when a standard vacuum forming machine is unable to adequately distribute the plastic sheet on the mold. This plug aids in filling all open areas in the molds by distributing melted plastic sheets with an equal thickness over the mold surface. The plastic sheet won't thin as a result of these plugs, giving the material additional room to reach the mold's bottom.
Step 6: Vacuum
Extra air is taken out of the sheets and molds during the stretching and plugging procedure. After that, a mobile vacuum pump is inserted into the apparatus to remove any air bubbles that may have become wedged between the plastic sheets and the molds. The vacuum pump should be able to generate around a 27" mercury pressure. Larger machines may be handled with the aid of a vacuum reservoir and high-volume vacuum pump, which quickly removes the air particles before the plastic sheet cools.
Step 7: Cooling and Release
Before releasing it, the plastic shape is put through a chilling procedure. Cooling is essential since it will allow the melted plastic time to settle. It will be distorted if not. The machine has fans built in to help with cooling, which aids in the cooling process. Along with the use of fans, there are nozzles that spray a cooled water mist directly onto the plastic sheet, accelerating the cooling process by 30%.
Temperature control devices are present to manage the cooling temperature of these particular polymers as they exit the machine, assisting in the cooling process. The machine releases the molded plastic sheet for the subsequent phase once it has cooled.
Step 8: Trimming and Finishing
The molded sheet is then trimmed with the aid of several types of trimmers once the plastic sheet has been removed from the machine. In accordance with the specifications of the finished product, cuts, holes, or slots are formed in the sheets. Decorating, printing, and strengthening are all examples of finishing.
There are several trimming options, however, the quality of these goods varies depending on the component size, cut style, material thickness, etc. For instance, mechanical trim presses, sometimes referred to as roller presses, are typically used to trim narrow gauge items.
Overall, the heating and vacuuming processes of vacuum forming normally only take a few minutes each, making the whole process of vacuum forming a reasonably short one. However, the amount of time needed for chilling, cutting, and forming molds can vary significantly depending on the size and complexity of the components that are being made.
5. Machines Used In Vacuum Forming
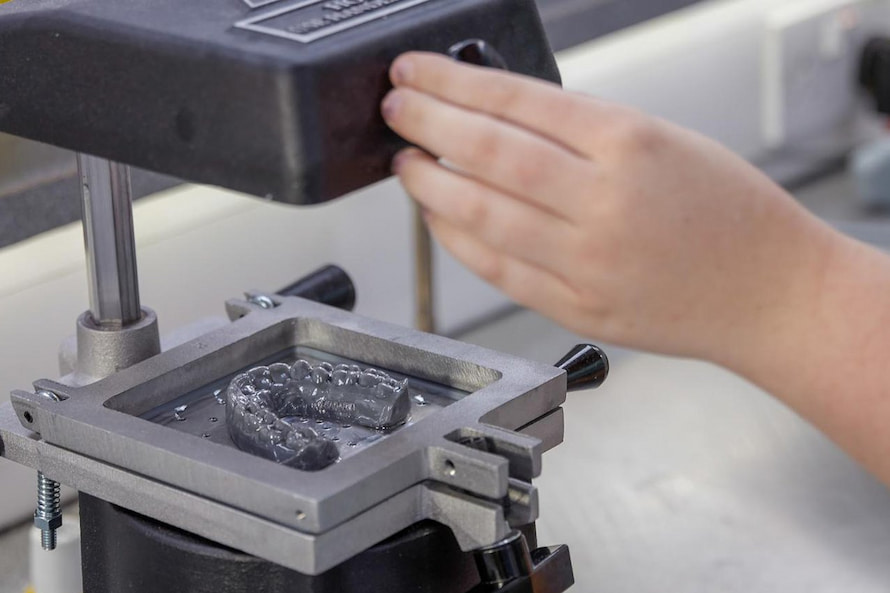
While all vacuum-forming machines operate according to the same formula, various machines operate differently based on their capacities. There are 4 different categories of vacuum-forming machines:
DIY Machine
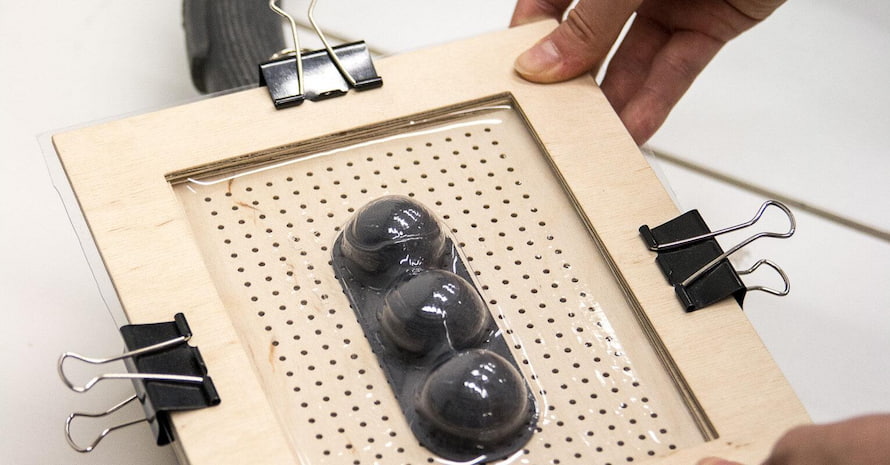
For smaller-scale manufacturing, homemade machines are employed. There are only a small number of heaters in it. They cannot be used in industrial manufacturing as a result. DIY machines may employ ceramic heaters, but they are not specialized enough to handle complicated equipment, such as plugs, and their response times are poor.
These devices have a straightforward construction and are simple to handle, install, and maintain. Three distinct heating zones with various temperature settings are located in a single working station. A vacuum pump is located at the machine's base, and the heating box is covered with a lid. Toys, masks, stationery, dinnerware, tools, blister packs, cosmetics, and other items are made by DIY machines.
Table Top Machine
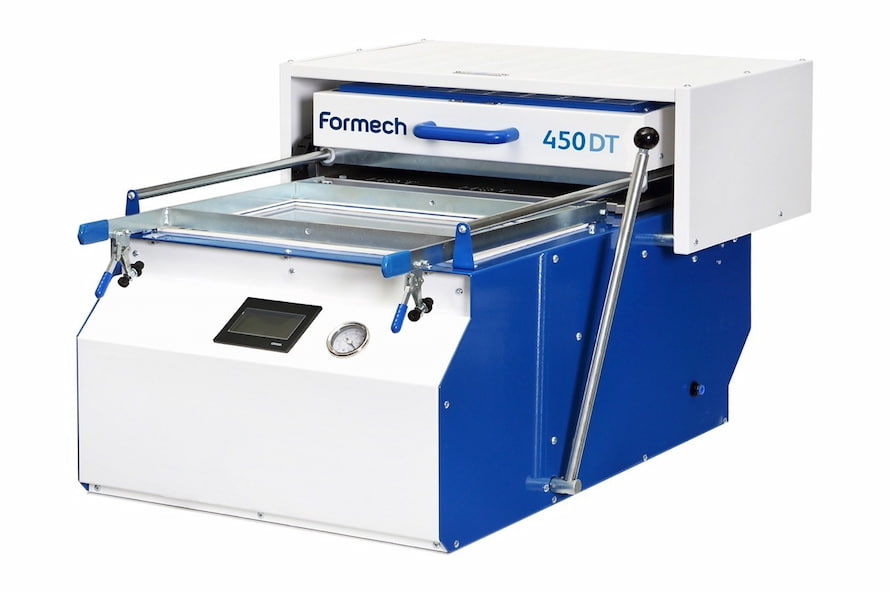
Products made of acrylic are formed using a desktop vacuum-forming machine. There are three main series of these devices, each with a distinct function. The vacuum-forming machine uses the same operating system as other vacuum-forming machines, and acrylic, ABS, PC, PS, PVC, PP, and other materials are appropriate. These are utilized in the vehicle, aerospace, signage, display, and set design industries.
Single Heater Machine
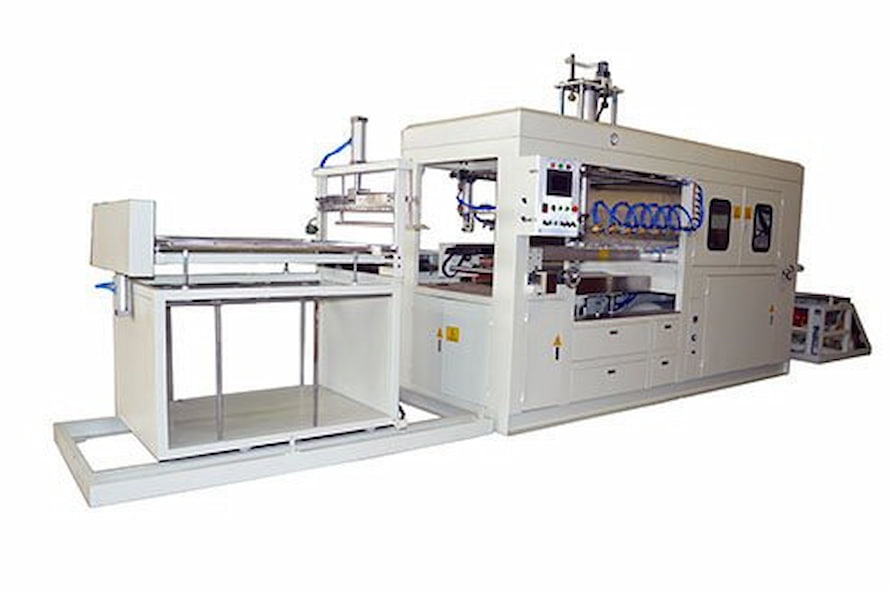
The single heater machine may be used with numerous kinds of plastic sheets, including those that degrade starch, optical materials, and come in a variety of colors (HIPS, PVC, PET, PS, PP, etc.). The mechanical and electrical components of these machines are integrated, and they feature automated temperature controls, high frequency, and effective temperature gain.
Furnaces also have 10 easy-to-install stalls for automated temperature controls and gear switches. This machine produces items such as thin-walled food containers, travel accessories, fabrics, cosmetics, decorations, toys, and electrical goods.
Double Heater Machine
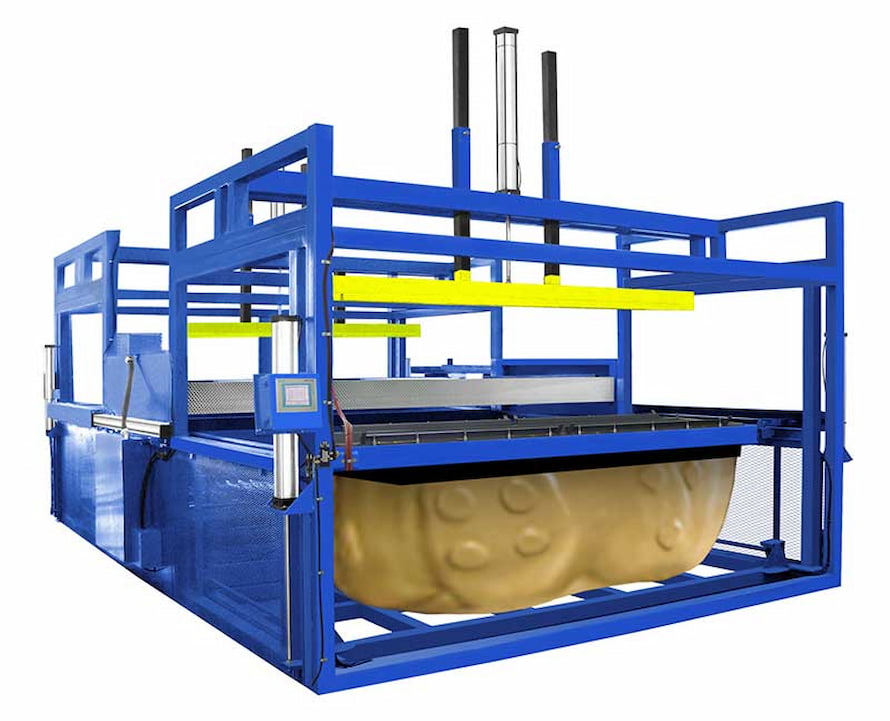
A vacuum-forming machine with two heaters uses electrical-mechanical integration. It is capable of executing all the tasks that are feeding, heating, shaping, cooling, trimming, and finishing. It is completely automated with all digital power controls. It is used on sheets of plastic including PS, HIPS, PVC, PET, and PP.
It has an automated sheet feeding frame that enables proper sheet feeding while reducing personnel. Each of the 60 infrared ceramic bricks that make up the heaters in this machine has a self-regulator that controls the heating temperatures of the sheet. Although the double heater machine is designed for negative molds, it can also produce concave or convex mold as needed. With regulators that adjust the amount of water sprayed in accordance with the product, spray mists are available to cool down the heated sheet.
The double heater machine produces plastic packaging, medical trays, telephones, cookies, hardware, and tableware.
6. Difference between vacuum forming, pressure forming, and thermoforming plastic
Vacuum forming, pressure forming, and thermoforming are all plastic-forming processes that are used to create parts and components from plastic sheets. However, each process has its own unique characteristics and is best suited for different types of applications. Here is a comparison of vacuum forming, pressure forming, and thermoforming:
Vacuum Forming
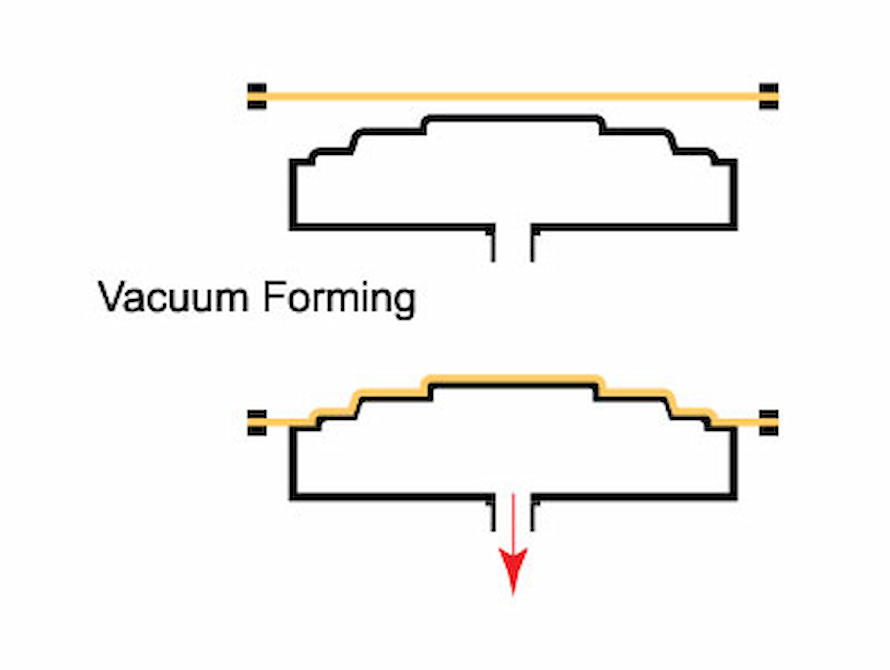
Vacuum forming is a process in which a plastic sheet is heated and placed over a mold. A vacuum is then applied to the underside of the sheet to pull it down onto the mold, creating a part or component with the shape of the mold. Vacuum forming is a low-cost process that is well-suited for creating large, simple parts with shallow depth and uniform wall thickness.
Pressure Forming
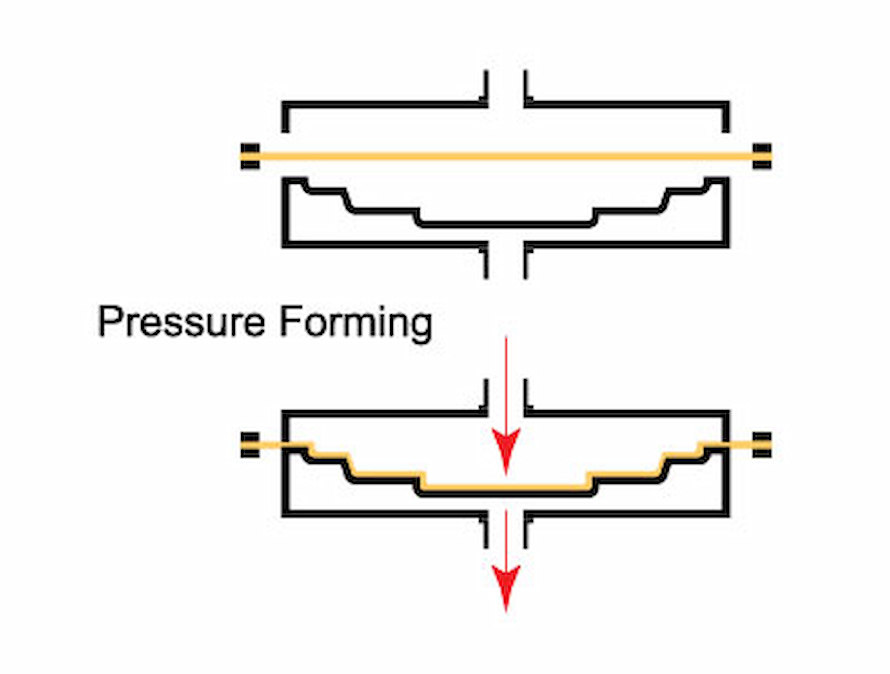
Pressure forming is similar to vacuum forming in that a plastic sheet is heated and placed over a mold. However, instead of using a vacuum, pressure is applied to the underside of the sheet to force it down into the mold, creating a part with more detail and uniform wall thickness than is possible with vacuum forming. Pressure forming is more expensive than vacuum forming but is well-suited for creating smaller, more intricate parts with deep drawers and complex shapes.
Thermoforming
Thermoforming is a broader term that encompasses both vacuum forming and pressure forming. In addition to these two processes, thermoforming also includes other plastic forming techniques, such as twin-sheet forming and drape forming. Thermoforming is a versatile process that is used to create a wide range of parts and components with various shapes, sizes, and thicknesses.
To grasp up, vacuum forming, pressure forming, and thermoforming are all plastic-forming processes with unique characteristics. The best process for a given application will depend on the size, shape, and complexity of the part, as well as the desired wall thickness and surface quality. By understanding the differences between these processes, it is possible to select the best process for a specific application and produce high-quality parts with consistent results.
7. Best clear plastic for vacuum forming
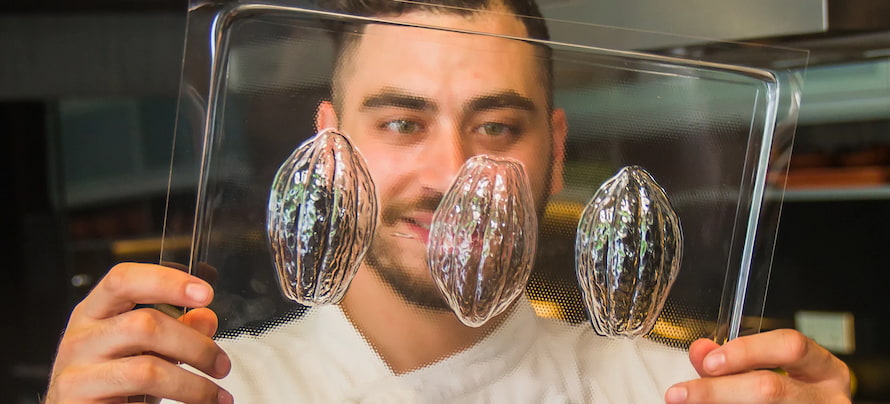
Thermoplastic materials come in a wide variety that can be utilized for vacuum shaping. The product's intended usage must be taken into consideration while selecting the material. Polyester, HDPE, LDPE, polypropylene, polystyrene, ABS, acrylics, polycarbonate, and Kydex are a few typical plastics that may be vacuum-formed.
Polyester
Polyester is a polymer noted for its adaptability, low toxicity, and recyclable nature. Food pouches, beverage bottles, processed meat packaging, and other food containers are examples of typical vacuum-formed polyester plastics.
Polypropylene
A thermoplastic polymer with high mechanical strength, polypropylene, is resistant to a broad range of acids, solvents, and bases. It is also thermally resistant and flexible. It may be used to make yogurt containers, bottle caps for containers, and pharmaceutical bottles. It is the second most extensively produced synthetic plastic in the world.
HDPE
Polyethylene known as high-density polyethylene, or HDPE, is made from petroleum. Its strength-to-density ratio and tensile strength are both high. It can be recycled and is solvent-resistant in a number of ways. Its primary flaw is that it might be challenging to create. Plastic bags, margarine tubes, milk bottles, cereal box liners, and detergent bottles are among the items it is used for.
LDPE
The earliest type of polyethylene is low-density polyethylene, or LDPE, which was created for the first time in 1933. At room temperature, it doesn't react unless there are sufficient oxidizing chemicals present. Some solvents can also induce edema.
Although it is not nearly as robust as HDPE, LDPE is nonetheless resilient and malleable. The material of choice for many items, including squeezable food bottles, plastic bags, shrink wrap, and clothing bags, is LDPE, which can be challenging to deal with like HDPE.
Polystyrene
High-impact polystyrene in particular is a commonly manufactured, low-cost plastic substance. It is either foamed or solid. Styrofoam is a fantastic illustration of foamed polystyrene. Plastic cutlery, fast food platters, egg cartons, and CD covers are all made of polystyrene. Despite being simple to get, polystyrene is infamously difficult to get rid of in an environmentally responsible manner. It takes a long time to disintegrate and frequently becomes litter.
ABS
ABS, also known as Acrylonitrile Butadiene Styrene, is robust, stable, and impact-resistant. Compared to pure polystyrene, it is stronger. Manufacturers can change the composition as needed to improve these characteristics and the product's heat resistance. The majority of vacuum-formed ABS items are intended for domestic usage or broad consumer use.
Acrylics
Acrylic plastics are renowned for their clarity in the eye. Because they are so transparent, colorless acrylic plastic can occasionally be mistaken for glass. Vacuum-molded acrylics are frequently used as a glass alternative for beverage containers because of this. They may be colored and used for a variety of different things, such as kitchenware and medical equipment. Although ABS is relatively heat-resistant, it is not very frost-resistant. Additionally, it doesn't prevent UV rays.
Polycarbonate
Polycarbonate is a thermoplastic resin with remarkable strength and impact resistance. It is typically translucent and effectively transmits light. Additionally, it maintains dimensional stability while being simple to thermoform. For a wide range of uses, including CDs and DVDs, shatterproof display cases, bulletproof security barriers, aircraft panels, and more, polycarbonate sheets may be thermoformed.
Kydex
Kydex is a thermoplastic sheet designed particularly for thermoforming based on PVC. It is robust, stiff, formable, chemically resistant, and rigid. It is offered in sheets with thicknesses ranging from.028 inches to.500 inches for thermoforming. Trays, tote boxes, insulators and housings, kick plates, door liners, vehicle fenders, and many more things may all be made using thermoforming.
Where to find a prestigious plastic supplier for vacuum forming applications?
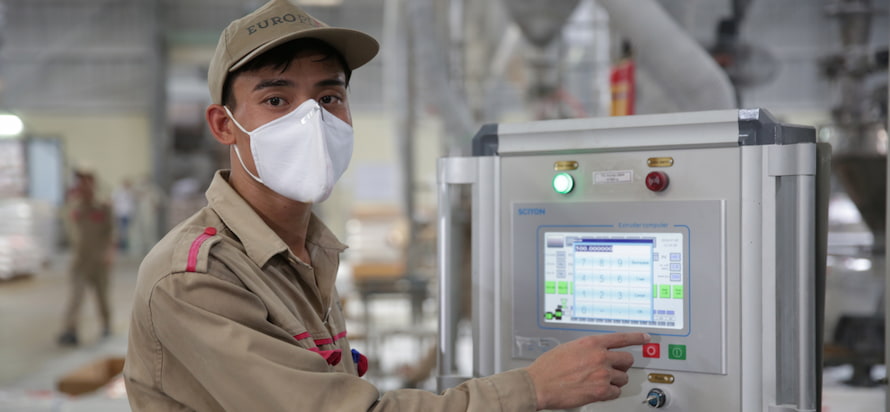
Established in 2007, European Plastics Joint Stock Company (EuP) is proud to be the world's largest filler masterbatch manufacturer and provides specialized material solutions to help plastic businesses improve their competitive advantage.
At Europlas, we understand that our customers have different requirements and needs. Therefore, EuP's custom solutions can be tailored to meet the specific needs of the customer. If you are in need of a plastic supplier suitable for vacuum forming applications, do not hesitate to contact us for the earliest advice and support.