Plastic molding methods are commonly used in large-scale production because they provide precision, stability in quality and productivity for the final product. In addition, plastic molding also helps manufacturers save costs and focus resources on improving & developing raw materials for the product. In particular, this method requires high techniques and many years of experience for products with detailed structures & shapes. Therefore, manufacturers cannot avoid influencing factors and errors in the plastic molding process. In this article, EuroPlas not only emphasizes the importance of the plastic production process but also suggests some ways to fix errors to make the plastic molding process more efficient. Don't miss it!
1. The importance of plastic molding in the production process
The core advantage of plastic molding is its popularity & practicality. Almost all plastic products on the market apply this method for mass production. Plastic molding plays an important role for the following four key reasons:
-
Accuracy: After going through the heating process to turn into liquid, plastic materials will be molded into molds to create shapes. Plastic molds are designed specifically to be able to reproduce the curves, angular details and overall shape of the product accurately as required. In particular, the mold is very hard to ensure the crystallization and concentration of the product towards the standard of shape and size.
-
Diverse variations: In plastic molding, there are 3 separate variations: Blow molding, rotational molding and vacuum molding. Each form will meet the criteria of each separate product and industry. Specific examples are as follows:
-
Blow molding: Suitable for plastic products with hollow insides such as plastic bottles, fuel tanks, etc. This method is often combined with HDPE plastic materials and is used more widely than injection molding.
-
Rotational molding: Is a combination of high temperature plastic and low pressure so that the plastic mixture covers the mold evenly to form solid products. Therefore, plastic molding by this method is suitable for simple products that require rounded corners or need stable thickness such as toys, fuel tanks, plastic barrels, etc.
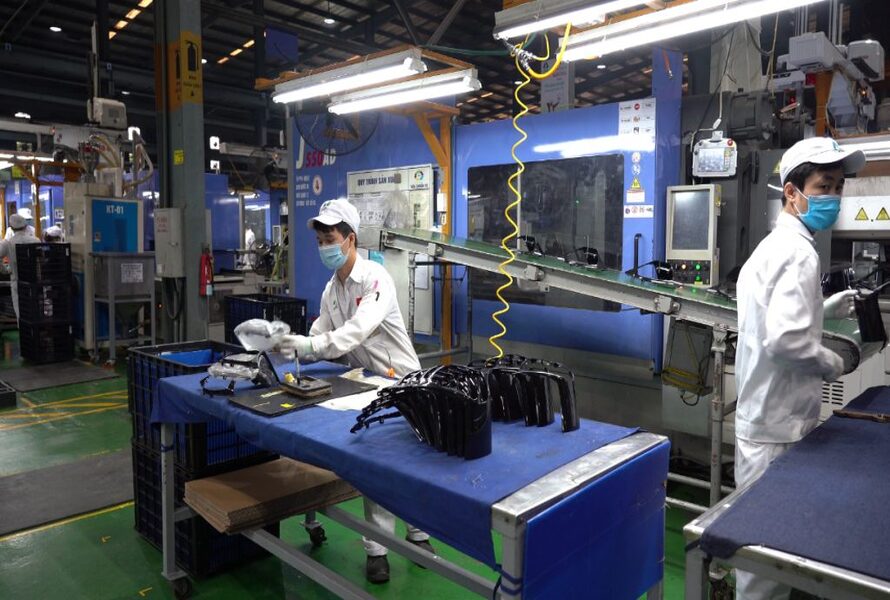
Plastic molding is applied in diverse industrial fields
-
Vacuum molding: Take advantage of the vacuum mechanism to remove air from the silicone mold when pouring plastic to create a smooth surface. Vacuum plastic molding is popular for parts with partially transparent surfaces such as: Electronic device housings, display products, phone cases, etc.
-
Time saving & stability: Compared to other manufacturing methods such as CNC turning, plastic molding has a shorter completion time, but still ensures the shape, size and aesthetics of the product. The main reason is because the plastic mold has been fixed from the beginning.
-
Increasing productivity: The rate of defective or damaged products is significantly reduced when the mixture is gradually shaped through the plastic mold. Therefore, the method is a suitable choice for large quantity orders and requires high precision & precision. Manufacturers only need to ensure the quality of raw materials and regularly check & maintain the machine system to maintain efficiency.
-
Diverse models: EuroPlas mentioned above that the plastic molding method has 3 main variations, helping them increase their practicality in a variety of key areas. In addition, manufacturers can customize the shape of plastic molds to flexibly meet customer needs. In particular, molds are capable of preserving the integrity of small or complex product details.
-
Cost savings: If the above factors are well controlled, the processing unit will save time and increase profits. Although we can spend an initial investment on mold making and manufacturing, the production time factor as well as the product quality that the plastic molding method brings will positively affect the profits and competitive advantages of the business.
Those are the 6 core benefits and importance of plastic molding in the production process. However, they are not the most perfect method and are still affected by other factors. Refer to the details in the next section!
2. Factors affecting the plastic molding process
The plastic molding process is directly affected by the following factors:
-
Neglect in the inspection and maintenance of plastic molds: Plastic molds will gradually decrease in life over time and production volume. Poor quality plastic molds will affect the shape, size and details of the product. Manufacturers must regularly check the mold details after each batch to make timely adjustments.
-
Deviation in melting parameters of raw materials: Each plastic material will have different melting parameters, for example, PP plastic is 160 - 180 degrees Celsius or PE plastic is 115 - 135 degrees Celsius. Manufacturers must clearly understand the details and accuracy of these parameters to adjust them most appropriately. If the temperature is incorrect, the plastic mixture will not reach the desired state and will affect the entire molding and shaping process.
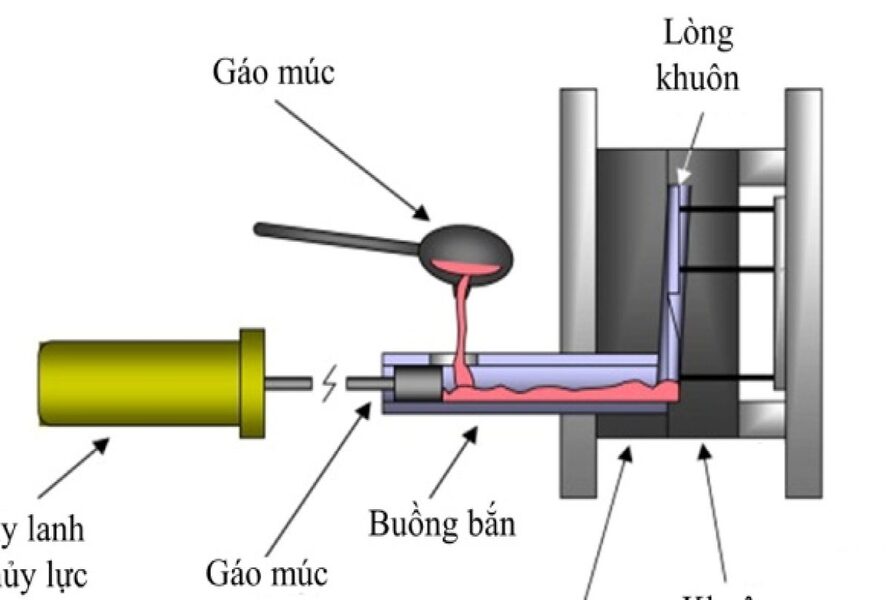
Plastic molds need to be regularly maintained and inspected
-
Imbalance of raw materials: For large-scale manufacturers, calculating the content of each raw material and plastic additives is a prerequisite for the initial success of the process. Adding too much plastic additives will be counterproductive to the plastic molding process. They can affect the entire batch and cost a lot of money to recover & adjust. The recommended ratio of plastic additives will be approximately 1% of the total mass of raw materials.
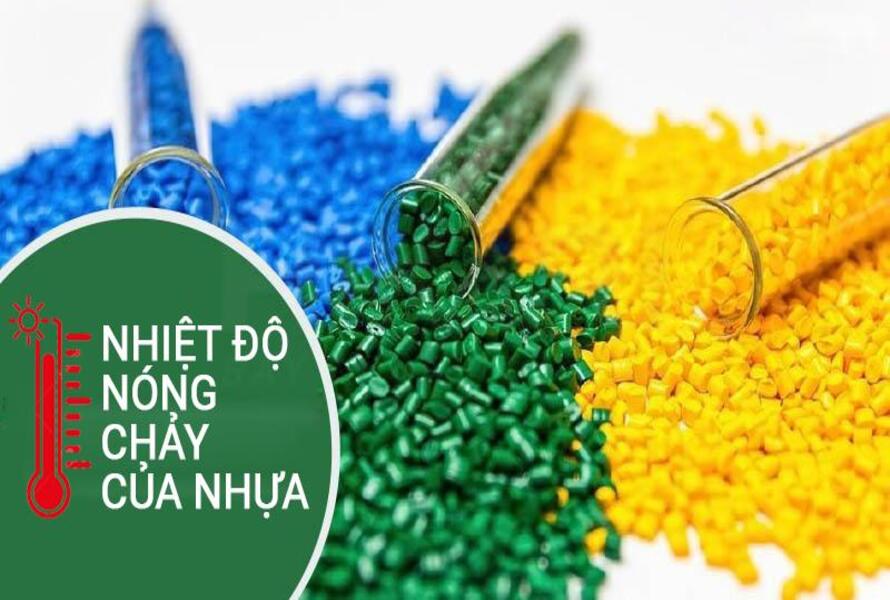
Manufacturers must control the melting temperature of each material during the plastic molding process
-
Not maintaining machine parts regularly: The plastic pump head and the machine gears are parts that are very easy to accumulate compounds and reduce their life after a long-term production process. The gears will run out of oil and gradually lose their smoothness, affecting the transportation of the plastic mixture to the nozzle. Next, if the plastic nozzle accumulates too much scale, the amount of mixture fed into the frame will be uneven, so the shape & size of the product will be affected.
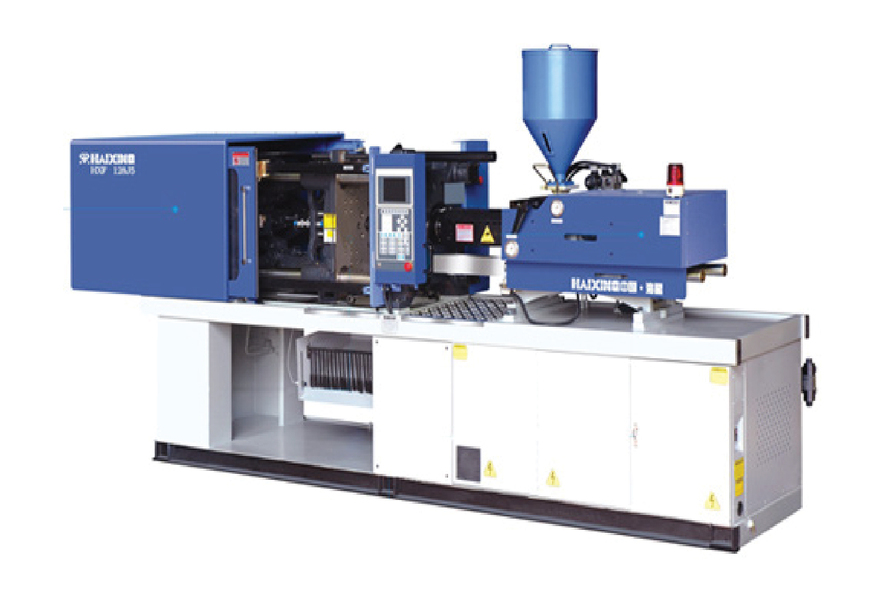
Each part and equipment of the plastic molding machine must be periodically inspected to minimize production errors
3. Common errors in the plastic molding process and how to fix them
Although the plastic molding process is suitable for large production quantities and products requiring complex details, manufacturers cannot avoid errors arising from the properties of the material and the influence of the environment. EuroPlas will help customers identify and solve these common errors. Specifically as follows:
The surface appears concave:
-
Causes: This is a common phenomenon that often occurs during the cooling process of the product after plastic molding. In particular, the imbalance in material content leads to a shortage in the supply to the product during the process of increased shrinkage. Therefore, the product surface is not able to withstand pressure and will be dented.
-
Solutions: Manufacturers must distribute the amount of plastic evenly at a time to avoid the phenomenon of plastic accumulation for too long. In particular, the thickness parameters need to be consistent between. Specific example: the recommended rib thickness is 1/2 - 1/3 of the main wall thickness. In addition, if this phenomenon unfortunately occurs during the production process, we need to change some settings with the machine such as: Increase injection pressure, increase injection speed, or reduce injection temperature.
Burn marks appear on the surface:
-
Cause: Temperature is the main cause of burn marks and black stains on the surface of plastic products. In addition, unstable injection speed also leads to this situation. Because at that time, the amount of plastic remaining in the mold will increase, the plastic mixture will lose thermal balance, leading to the material gradually increasing temperature and exceeding the allowable level. Even too much residual plastic will affect the life of other parts, causing more serious conditions.
-
Solutions: Manufacturers are advised to balance the nozzle speed to limit the risk of plastic and air being trapped inside the product. Next, customers reduce the overheating by reducing the melting temperature and mold temperature. At the same time, widen the vents and air vents to allow trapped air to escape from the mold.

The finished product is deformed and warped:
-
Causes: This problem often occurs during the cooling process of the finished product after the end of plastic molding. The change in chemical structure between the cooling and solidification time of the product occurs too quickly, making them unable to adapt. In addition, the uneven design of the plastic mold is also a direct cause of the above problem.
-
Solutions: First, customers need to perform the cooling process correctly and according to certain standards. You must let the product gradually cool down in the mold before putting it in the coolant. Next, the manufacturer re-checks the size of the plastic molds to ensure they are uniform and complete with the smallest details.
\
Failure to control the melting temperature during the plastic molding process will cause burnt streaks to appear on the product surface
Deformed products due to lack of fuel source:
-
Causes: Manufacturers often think they have calculated the exact content of raw materials before production. However, factors such as nozzle speed, thermal imbalance, plastic mold temperature as well as product thickness will affect the uniformity of plastic materials. If the amount of plastic mixture supplied is uneven through each process, the finished product is very susceptible to deformation or defects.
-
Solutions: Manufacturers must continuously check the operating process of each part of the plastic molding machine. All important factors such as: Mold temperature, nozzle pressure & velocity, mold size, product thickness parameters as well as cooling process must be considered in detail through each stage.
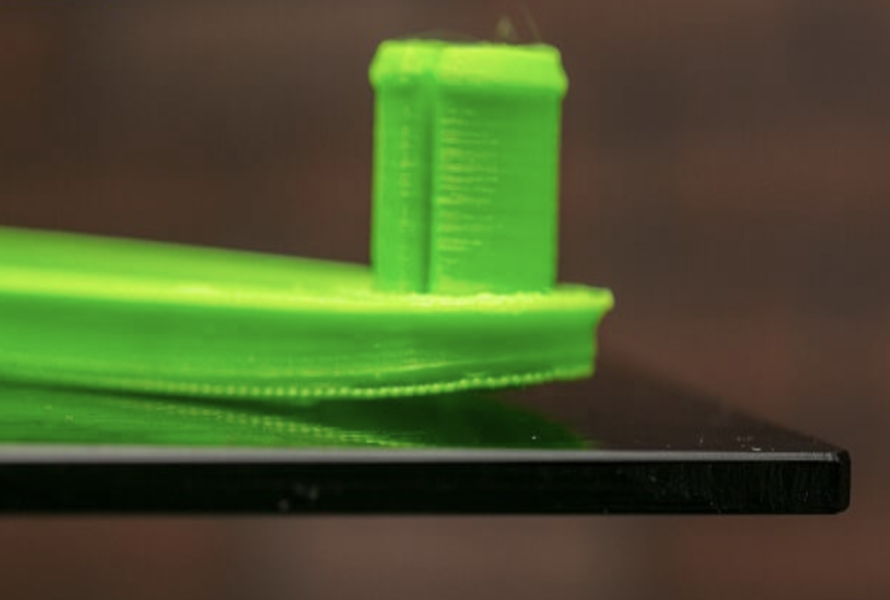
Warping error during plastic molding process
The connection and connection in the product part is faulty:
-
Cause: For some reason, the plastic is divided into different directions to fill the mold cavity and these flows merge on one line. This line is called the connection line or weld line. Normally, the molten plastic when forming the product will be completely melted and melted together when forming. But when separating different flows, the material in front of the flow tends to be cooler than the inside of the flow. When these two layers of material come into contact with each other, they are not completely melted.
-
Solutions: This is one of the errors that is difficult to completely fix. Therefore, the manufacturer will try to move their position to minimize the impact on the product's function. However, EuroPlas will still suggest some methods to customers, specifically as follows: Increase mold temperature, set different pressure & nozzle speed at each position to suit product design requirements and adjust the flow of plastic by changing the position, shape, size or number of plastic pouring gates.
4. About EuroPlas
EuroPlas is one of the leading manufacturers in the Vietnamese market and has become a strategic partner with many manufacturing & supplying units in more than 95 countries worldwide. In addition, EuroPlas has been applying plastic molding methods in the production of a variety of raw materials and distributing them all over the world.
EuroPlas's current main product lines are: Bioplastics, color masterbatch, filler masterbatch, engineering plastic compound and color masterbatch. In particular, the system of 7 factories with a scale of tens of hectares in 6 provinces and 1 factory in Egypt helps the enterprise to be able to supply approximately 0.8 million tons of plastic materials/year.
5. Conclusion
EuroPlas has highlighted the core importance of the plastic molding process in material production. More specifically, we have analyzed in detail each factor and error affecting this process, along with providing practical solutions to increase production experience for customers. In the article, EuroPlas has popularized the 4 factors and 5 most common errors in the plastic molding process. Please continue to follow EuroPlas blog and contact us immediately to update and solve all material problems as soon as possible!