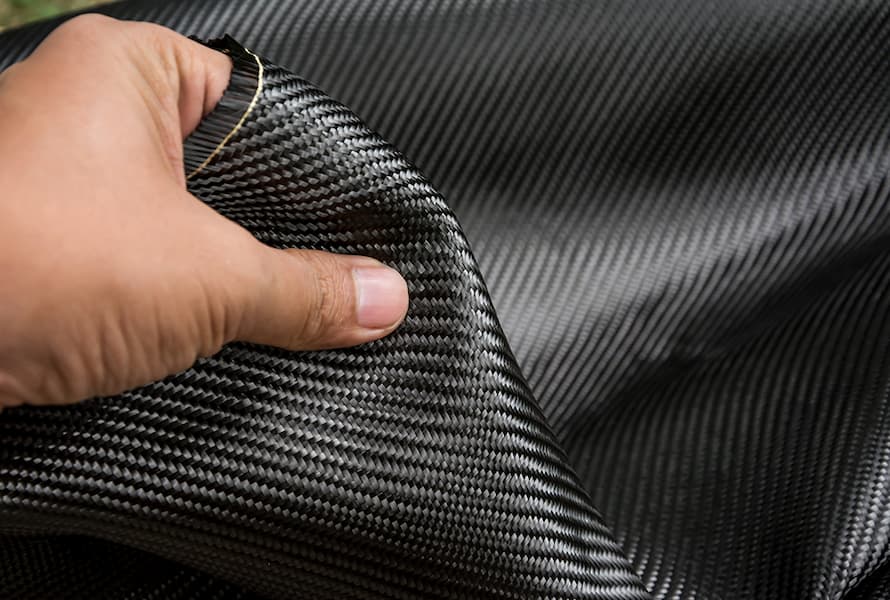
Carbon fiber reinforced plastic (CFRP) is a lightweight and high-strength composite material that has gained popularity in various industries. The unique characteristics of CFRP have led to its use in a variety of applications, from aerospace and automotive to sports and recreational equipment. In this article, we will delve into the world of carbon fiber-reinforced plastic, exploring what it is and the common applications of CFRP.
1. What is carbon fiber reinforced plastic?
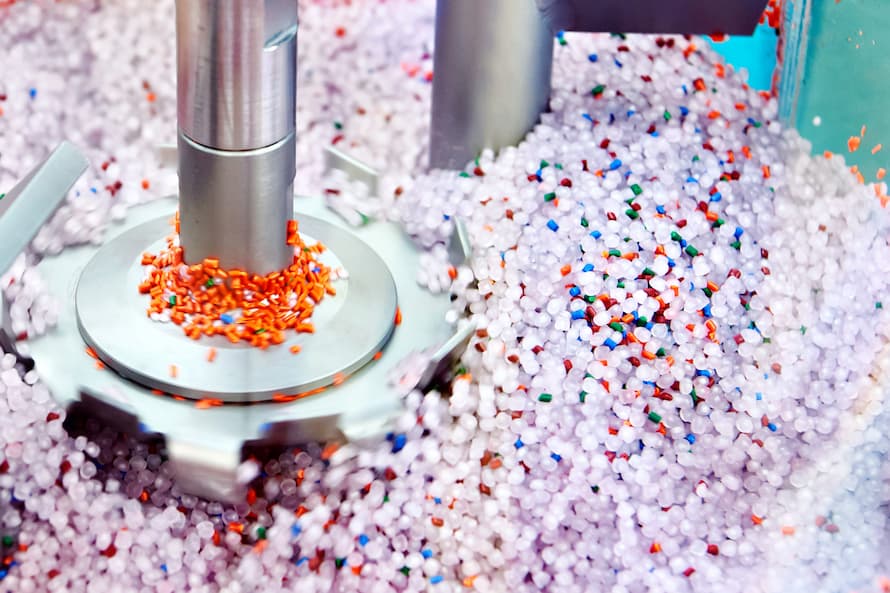
Definition: Carbon fiber reinforced plastic (CFRP) is a composite material made of carbon fibers and a polymer matrix. The carbon fibers are embedded in a resin matrix, typically epoxy, which provides the structure and binds the fibers together.
Properties
- High Strength-to-Weight Ratio: The carbon fibers used in CFRP are incredibly strong, with tensile strength values that can exceed 1 GPa, while the polymer matrix used to bind them together is relatively lightweight.
- High Stiffness: CFRP is also very stiff, with a modulus of elasticity that can exceed 100 GPa.
- Fatigue Resistance: CFRP can withstand repeated loading and unloading cycles without suffering from material degradation or failure.
- Thermal Stability: CFRP has good thermal stability, with a low coefficient of thermal expansion, and can maintain its dimensions and shape under a wide range of temperature changes.
- Design Flexibility: CFRP can be molded into complex shapes, providing designers with a high degree of flexibility in creating custom parts and components.
Applications
- Aerospace: Structural components such as wings, fuselages, and rotor blades.
- Automotive: Body panels, chassis components, and suspension systems.
- Sporting Goods: Golf clubs, tennis rackets, and bicycles.
- Medical Devices: Prosthetic limbs and braces.
- Defense: Aircraft, missiles, and armored vehicles.
- Robotics: Robotic arms and grippers.
However, there are also some limitations to CFRP. For example, it is relatively expensive compared to traditional materials, which can limit its use in some applications. Additionally, CFRP can be brittle and prone to damage from impact or puncture, leading to material failure if not detected and repaired in a timely manner. Finally, CFRP can be difficult to repair or modify once it has been formed, posing a threat of more challenging maintenance than with traditional materials.
2. Carbon fiber reinforced plastic manufacturing process
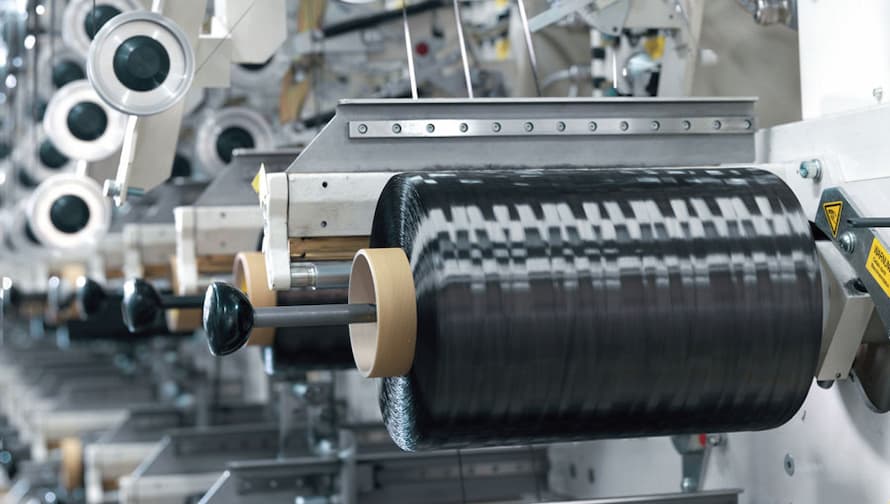
The production process typically involves the following steps:
Material selection
The first step in producing CRP is to select the appropriate carbon fibers and polymer matrix. The carbon fibers used should have high tensile strength and modulus, and the polymer matrix should have good adhesion properties.
Preparing the mold
The mold is prepared according to the desired shape of the final product. The mold should be clean and free from any debris or contaminants.
Applying release agent
A release agent is applied to the mold to ensure that the finished product can be easily removed from the mold.
Preparing the carbon fiber
The carbon fiber is cut to the desired length and orientation. The fibers are then coated with a sizing agent to improve adhesion to the polymer matrix.
Layup
The carbon fibers are arranged in the mold according to the desired orientation and thickness. The fibers are then impregnated with the polymer matrix using a vacuum or pressure process.
Curing
The mold is then placed in an oven or autoclave to cure the polymer matrix. This process typically involves heating the mold to a specific temperature and pressure for a specific amount of time.
Demolding
Once the curing process is complete, the finished product is removed from the mold.
Finishing
The finished product may require additional finishing processes, such as trimming, sanding, or painting, to achieve the desired appearance and dimensions.
Overall, the production of CRP is a complex process that requires careful selection of materials and precise manufacturing techniques to ensure the final product meets the desired specifications.
3. Common applications of reinforced plastic manufacturing process
3D printing
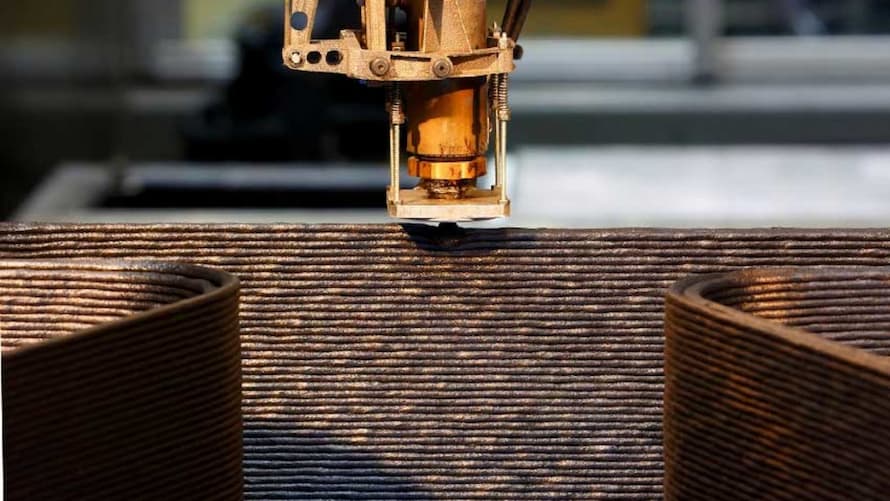
3D printing is a process of creating three-dimensional objects by layering materials on top of each other. Carbon fiber-reinforced polymers (CFRPs) can be used in 3D printing to improve the strength and stiffness of the printed parts.
Benefits of carbon fiber reinforced plastic 3d printing:
- Improved strength-to-weight ratio
- Used to create parts with complex geometries that would be difficult to achieve using traditional manufacturing techniques
- The resulting parts can be lighter and stronger than those made using traditional materials.
- Increase the efficiency of the manufacturing process
- Reduce material waste
However, one of the main challenges of using reinforced plastics in 3D printing is ensuring that the reinforcing materials are distributed evenly throughout the printed part. To overcome this challenge, manufacturers often use pre-made composite filaments or add reinforcing materials to the printing material during the printing process. The use of computer-aided design (CAD) software can also help to ensure that the printed parts meet the desired specifications.
Vacuum bagging
.jpg)
Vacuum bagging is a manufacturing process that involves the use of a vacuum to remove air from between layers of materials during the curing process. It is an application of the reinforced plastic manufacturing process that is commonly used to create composite parts with high strength and stiffness.
The process offers several benefits, including:
- Improved strength and stiffness: By removing air from between the layers of materials, vacuum bagging ensures that the reinforcing fibers are fully saturated with resin.
- Reduction in voids and defects: The vacuum pressure helps to eliminate any voids or defects in the final part, resulting in a more consistent and uniform product.
- Versatility: Vacuum bagging can be used to create parts of different sizes and shapes, then becomes a versatile manufacturing process.
- Cost-effectiveness: The process can be used to create parts that are more cost-effective than those made using traditional manufacturing techniques, such as injection molding or machining.
Vacuum bagging is commonly used in industries such as aerospace, automotive, and marine to create lightweight and strong parts such as wings, fuselages, and boat hulls.
Molding
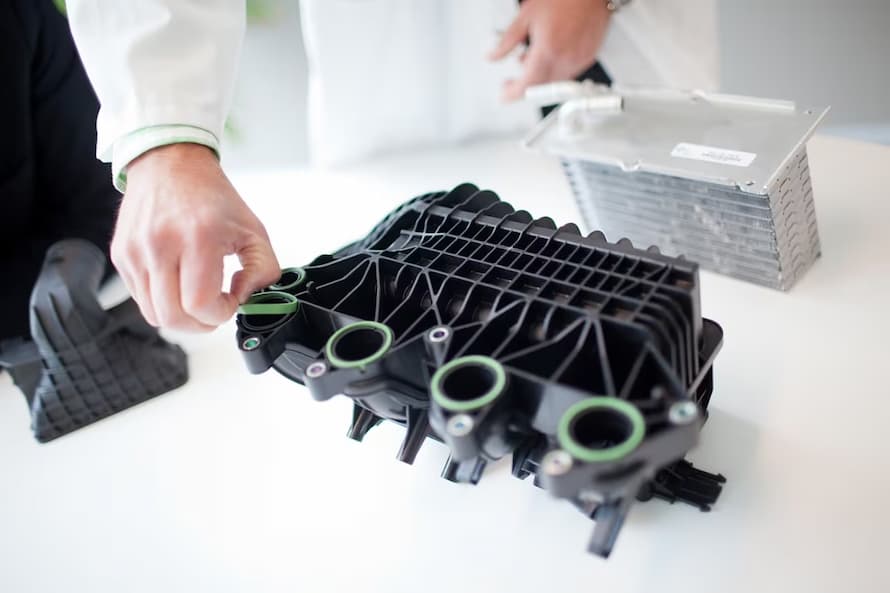
Molding is a manufacturing process that involves shaping the material into a specific form using a mold or die. In carbon fiber-reinforced plastic molding, reinforcing fibers, such as carbon fibers or fiberglass, are combined with a polymer resin to create a composite material. This composite material is then shaped into a specific form using a mold, which can be made of metal, plastic, or other materials.
Molding offers several benefits as a manufacturing process, including:
- High strength and stiffness: Help the final parts suitable for applications that require high performance and durability.
- Design flexibility: Used to create parts of different shapes and sizes, allowing for design flexibility and customization.
- Cost-effectiveness: A cost-effective manufacturing process, especially for high-volume production runs.
Reinforced plastic molding is commonly used in a wide range of segments such as:
- Automotive parts – dashboards, bumpers, grilles.
- Electronic components – electrical connectors, enclosures, protective sleeving.
- Medical devices – syringes, valves, dishes.
- Consumer plastics – mobile phone cases, bottle caps, toys.
- Furniture parts – seat cushions, chairs, seat covers.
Filament winding
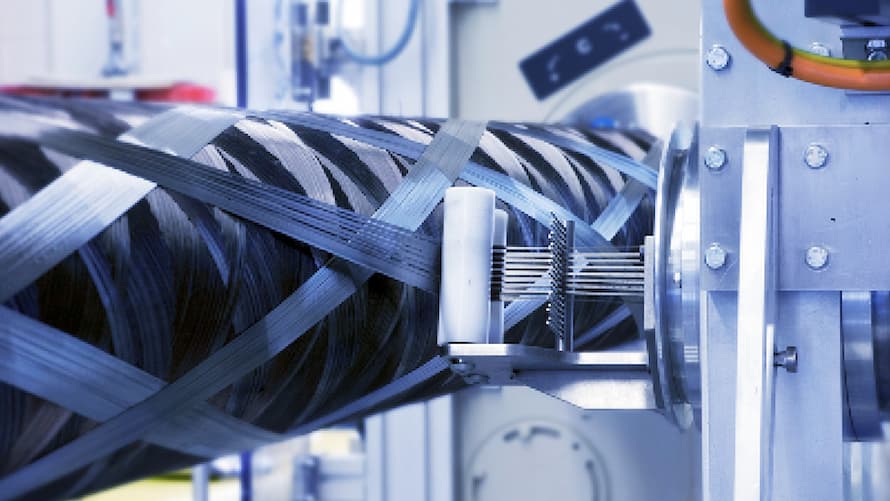
Filament winding is a manufacturing process that involves winding continuous reinforcing fibers around a mandrel in a specific pattern to create a composite material. In reinforced plastic filament winding, the process can be automated, which allows for high precision and consistency in the final product. The resulting structure is then cured to bond the reinforcing fibers and the resin together, and the mandrel is removed to reveal the final part.
Filament winding offers several benefits as a manufacturing process, including:
- Flawlessly timed fiber deposition
- Optimal mechanical properties
- The ideal fiber content in volume
- Low porosity, weight, and inertia of mass
- High stiffness
- Heightened vibrational damping
- Very low thermal expansion
The weight of filament-wound CFRP components may be reduced by up to 20% while maintaining mechanical qualities that are on par with those of other CFRP parts produced from woven textiles. The process is characterized by high accuracy and traceability. An affordable and effective unit cost is easily within reach, even with small series.
Reinforced plastic filament winding is commonly used in industries such as aerospace, defense, and energy, where high-performance cylindrical structures are required. For example, filament winding is used to create rocket motor cases, pressure vessels for gas storage, and wind turbine blades.
4. What is better fiber reinforced plastic than carbon fiber?

The most common alternative to carbon fiber is glass fiber. Look at the table below to get a complete comparison between these two materials.
Property
|
Glass Fiber
|
Carbon Fiber
|
Tensile Strength
|
Lower: 3.5 GPa (500 ksi)
|
Higher: 3.5-7 GPa (500-1000 ksi)
|
Modulus of Elasticity
|
Lower: 72 GPa (10.4 Msi)
|
Higher: 230-850 GPa (33-123 Msi)
|
Density
|
Higher: 2.55 g/cm³ (0.092 lb/in³)
|
Lower: 1.75-1.95 g/cm³ (0.063-0.070 lb/in³)
|
Electrical Conductivity
|
Good electrical insulator
|
Good electrical conductor
|
Cost-effectiveness
|
More cost-effective than carbon fiber
|
More expensive than glass fiber
|
Manufacturing Flexibility
|
More flexible and easier to process
|
Requires specialized equipment and expertise
|
Manufacturing applications
|
Can be manufactured to a wide range of forms
|
Generally limited to woven fabrics and pre-impregnated sheets
|
Durability
|
Generally more resistant to impact and fatigue than carbon fiber
|
Less durable
|
Environmental Impact
|
Can be easily recycled and reused and has a lower carbon footprint
|
Difficult to recycle due to use of epoxy resin or petroleum-based materials
|
The choice between glass fiber and carbon fiber reinforced plastic depends on the specific requirements of the application. Glass fiber may be a more cost-effective and environmentally friendly option for applications that do not require high strength and stiffness, while carbon fiber may be more suitable for high-performance applications where weight reduction and high strength are critical, even though it is more expensive and harder to manufacture.
5. Finding a polymer compound manufacturer?
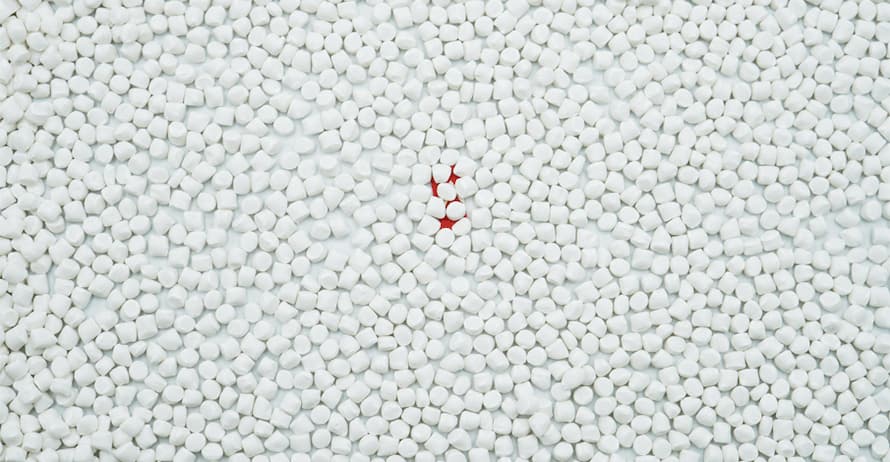
EuroPlas is the world’s largest masterbatch manufacturer, specializing in the production of engineering plastic compounds. EuroPlas plastic engineering compound is the optimal solution with flexibility, high quality, and all functions in just one material.
Features of EuroPlas plastic engineering compound:
- All functions in one single material
- Allow being directly processed without any materials required
- Tailor-made based on end-products requirements
- Improve end-products mechanical properties: stiffness, impact resistance,…
- Reduce shrinkage and enhance thermal resistance ability
At EuroPlas, we are dedicated to using the latest innovative technologies and adhering to stringent quality control methods. If you are interested in learning more about the EuroPlas plastic engineering compound, don't hesitate to contact us for more information.