1. The Definition of Pressure Forming
Pressure forming is a process of creating a highly detailed and textured mold by applying air pressure to heated plastic.
While pressure forming and vacuum forming are both well-known thermoforming techniques, pressure forming is a more sophisticated process. This method is suitable for meeting the demands of greater design and aesthetics. It is widely applicable in manufacturing equipment housings, medical device enclosures, and automotive components.
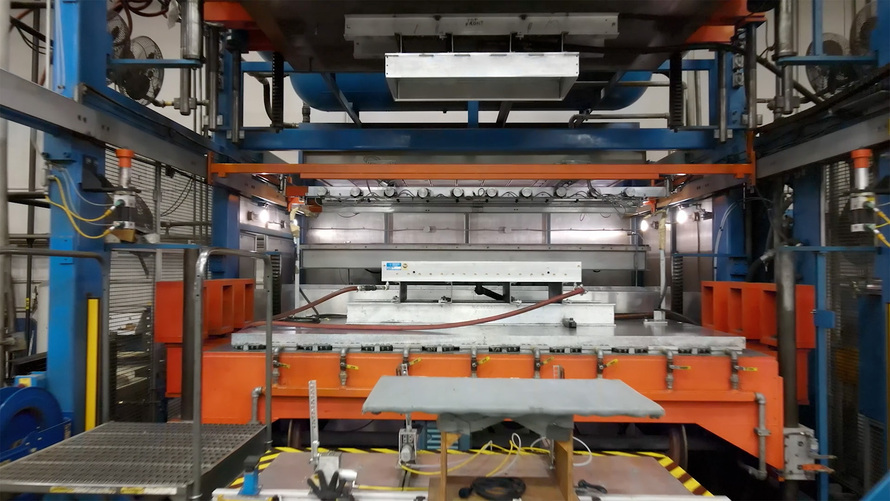
2. How Does Pressure Forming Work?
Below are the main steps in the pressure-forming process:
- Step 1: Insert a plastic sheet into the pressure-forming machine, ensuring it lays over a template.
- Step 2: Once the appropriate temperature is reached, the plastic sheet is pushed over the template by nearly 5 tons of pressurized air and then held under high pressure. To eliminate excess air, an air vent is used during the process.
- Step 3: Once the plastic sheet has cooled and hardened into a mold, it is removed from the template for use or further processing.
The term "template" refers to a tool used for making molds or parts. It can be a positive template or a negative one.
The positive template features a convex shape. When a heated plastic sheet is placed on it, this template helps create the dimensions inside the object. In contrast, the negative template has a concave form, used for creating a precise exterior of the object, as the plastic sheet is inserted inside the template. Accordingly, negative templates are more commonly used than positive ones because they contribute to greater levels of texture, detail, and aesthetics.
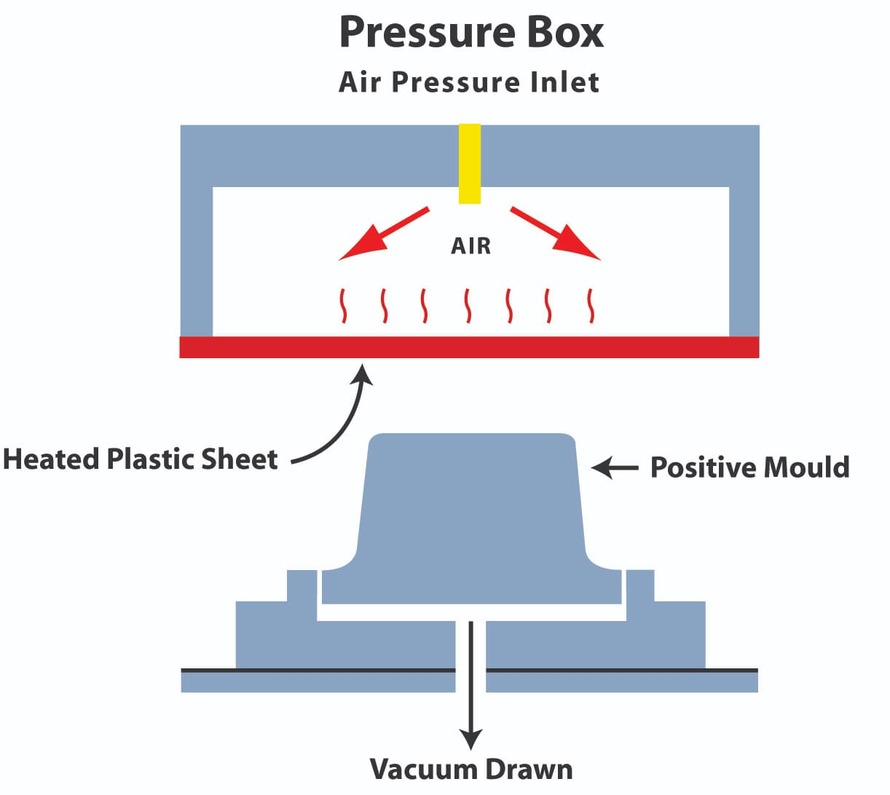
3. Advantages of Pressure Forming
Manufacturers can benefit from applying pressure forming to their manufacturing processes, thanks to its wide range of advantages, such as:
- Surface Detail: A pressure-formed mold can be crafted easily with numerous crisp surface details, particularly textured or grained finishes.
- Style Features: Pressure forming can be an ideal alternative to injection molding. By applying this method, molds can be designed with different logos, texts, images, or model designations, all with great sharpness.
- Defined Edge and Corner Radii: Pressure forming excels at creating sharp corners in molds, a task that conventional vacuum forming cannot achieve.
- Cost Efficiency: Another notable reason that makes pressure forming an outstanding alternative to injection molding is its 90% lower cost.
- Speed: The process of pressure forming is much simpler than injection molding or other plastic manufacturing processes. Therefore, it takes less time to complete all steps, from designing to obtaining finished products.
4. Disadvantages of Pressure Forming
Though the precision of pressure forming is highly regarded, this technique has limited applications in certain situations. For instance, it is less effective than injection molding for manufacturing products and components that feature varying thicknesses and require a lot of detail.
Additionally, the high pressure requires sturdier tooling, resulting in a higher initial cost compared to vacuum forming, although it remains cheaper than injection molding.
5. Conclusion
If you are a plastic manufacturer looking for an appropriate tool to transform a raw plastic sheet into a highly textured and detailed finished mold, look no further than the pressure forming technique. This method will speed up your process, save costs, and enhance the aesthetic appeal of the exterior of your plastic parts.
6. About EuroPlas
As a pioneer in manufacturing filler masterbatch, EuroPlas is confident in providing our customers with cutting-edge technology and tailor-made solutions customized to specific needs. Here at EuroPlas, you can find everything you need to optimize your plastic manufacturing procedures. We offer a wide range of products, including:
- Bioplastic compound: A green material solution that enables end-products to biodegrade within 12 months.
- Color masterbatch: A material solution that enhances the aesthetic appeal of end-products by providing exact colors.
- Plastic additives: A material solution that improves production efficiency and enhances the functions of end-products.
- Engineering plastic compound: A comprehensive material solution that integrates multiple functions into one for end-products.
- Filler masterbatch: A cost-effective material solution for plastic enterprises.
- Bio filler: A cost-effective material solution for bioplastic end-products.
We are always ready to discuss and resolve any queries you have about our offerings. Contact us today!