Plastic material shrinkage is a fundamental aspect of the manufacturing process with far-reaching implications for product quality. As molten plastic cools and solidifies, it undergoes contraction, impacting dimensions, structural integrity, and overall performance. In this comprehensive exploration, we'll define shrinkage, examine its types, and delve into the factors influencing this phenomenon.
Understanding the nuances of shrinkage is essential for designers, engineers, and manufacturers seeking precision in their plastic components. From the nuances of different polymers to mold design considerations, this blog will guide you through the complexities of managing shrinkage, offering practical insights to enhance your approach to plastic manufacturing.
1. What is shrinkage of plastic material?
Plastic materials undergo a phenomenon known as shrinkage during the manufacturing process, a crucial aspect that engineers and manufacturers need to consider.
1.1. Definition
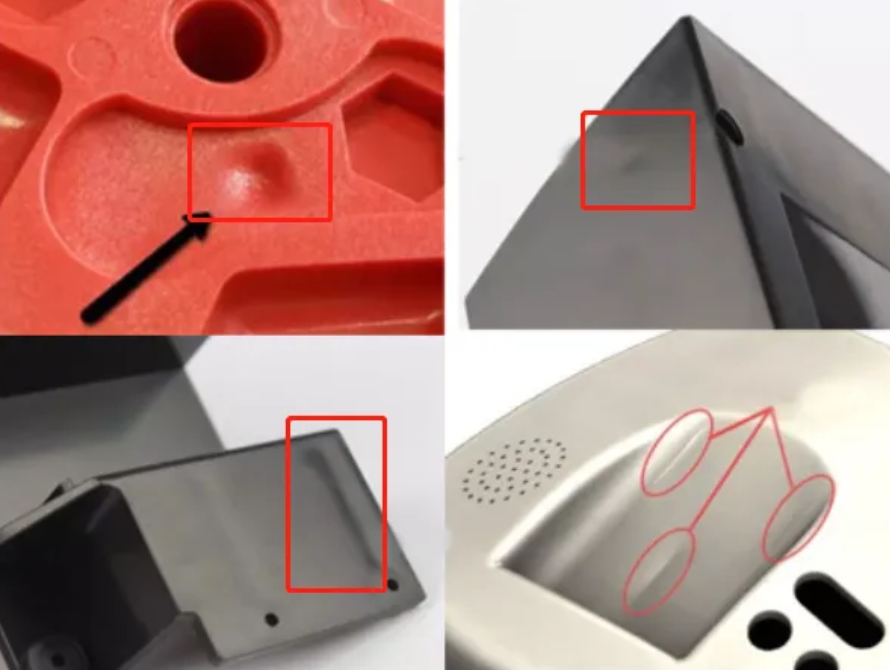
Shrinkage in plastic materials is the dimensional change that occurs as the material cools and solidifies. This process is inherent to the nature of plastics and is a consequence of the polymer chains rearranging themselves as the material transforms from a fluid to a solid state. The extent of shrinkage varies among different types of plastics and is a critical factor in the design and production of plastic components.
1.2. Types of shrinkage in plastic materials
There are several types of shrinkage in plastic materials:
- Thermal Shrinkage: This occurs due to the change in temperature. As the plastic cools, it contracts, leading to shrinkage.
- Phase Transition Shrinkage: This type of shrinkage happens when the plastic material changes from one state to another, such as from a liquid to a solid.
- Orientation Shrinkage: This occurs when the molecules in the plastic align in a particular direction during the molding process, and then attempt to return to their natural state after the process, causing the material to shrink.
- Compression Shrinkage: This happens when the plastic is compressed during the molding process, and then tries to regain its original volume after the pressure is released.
- Elastic Recovery: This type of shrinkage occurs when the plastic material is deformed during the molding process and then tries to return to its original shape after the process.
The shrinkage process consists of three parts: shrinkage before solidification, cooling shrinkage, and shrinkage after demoulding. Each type of plastic material has a different shrinkage rate, which can be influenced by several factors including processing conditions, flow path, mold, part design, and material composition.
1.3. Factors affecting shrinkage of plastic material
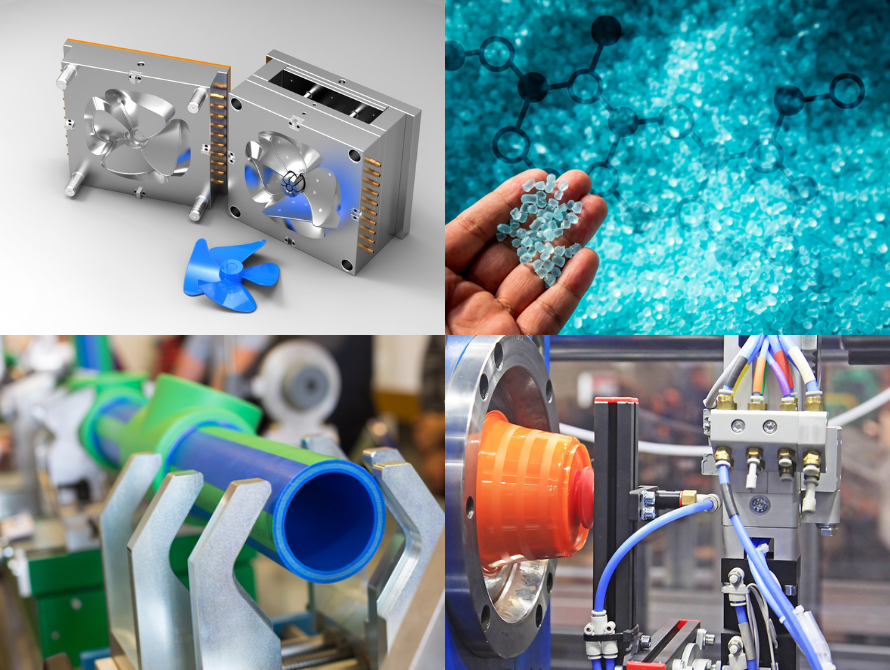
Several factors play a significant role in determining the extent of shrinkage in plastic materials:
Polymer type:
Different polymers exhibit varying shrinkage behaviors. Amorphous polymers, for example, tend to have higher shrinkage compared to semi-crystalline polymers. Understanding the specific properties of the polymer being used is crucial in predicting and managing shrinkage.
Cooling rate:
The rate at which the plastic material cools during the manufacturing process influences shrinkage. Rapid cooling can lead to increased shrinkage, while slower cooling may result in reduced shrinkage but could affect production efficiency.
Mold design:
The design of the mold has a direct impact on shrinkage. Factors such as the shape, size, and surface finish of the mold can influence how the plastic material solidifies and, consequently, the degree of shrinkage.
Processing conditions:
Parameters such as temperature, pressure, and cycle time during the molding process can affect shrinkage. Optimizing these conditions is essential for controlling and minimizing shrinkage in the final product.
2. Plastic material shrinkage chart
A plastic material shrinkage chart serves as a valuable tool for manufacturers and designers in predicting and managing the shrinkage of various plastic materials. This chart provides a visual representation of the expected shrinkage values for different types of plastics under specific molding conditions. Understanding these values is crucial for achieving precision and accuracy in the manufacturing process.
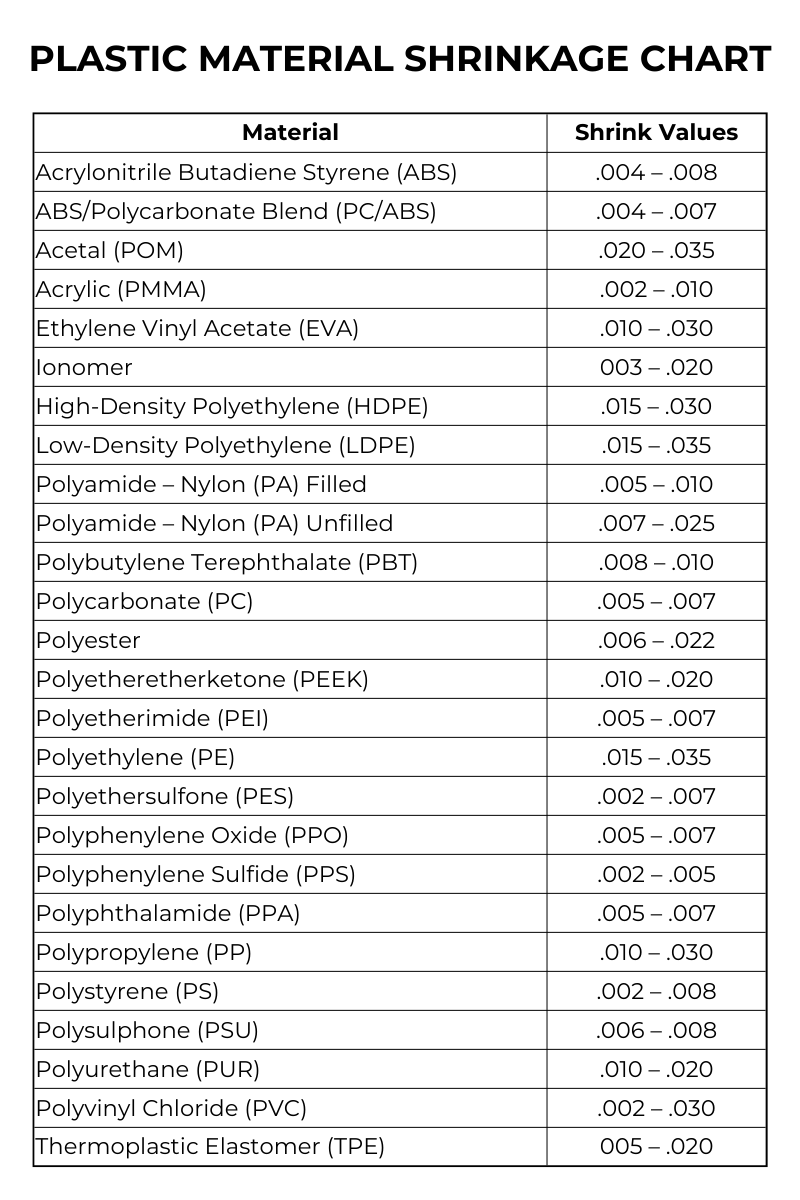
3. How shrinkage affects plastic material
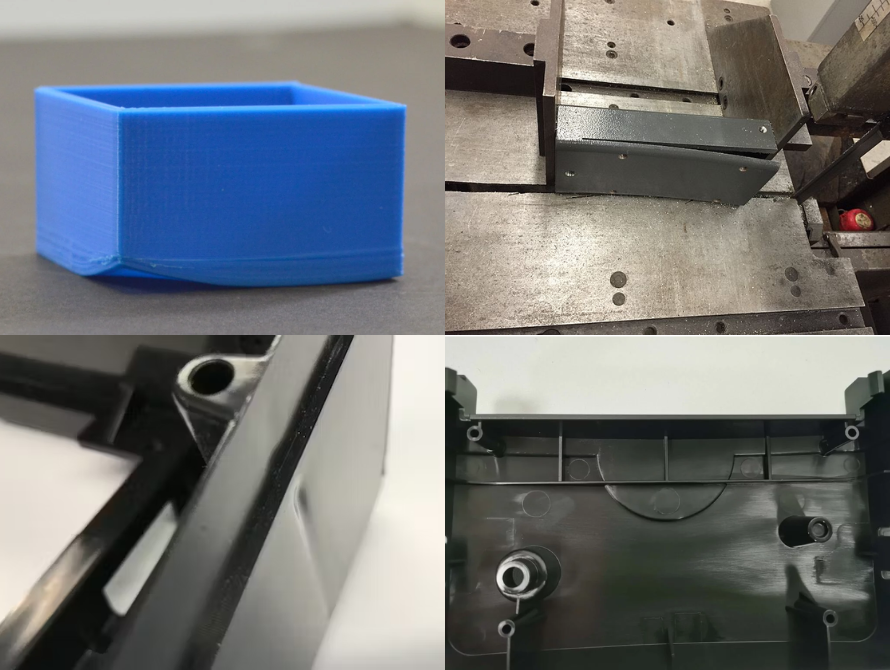
Understanding the impact of shrinkage is crucial for anyone involved in the plastic manufacturing process. Shrinkage can have far-reaching consequences that go beyond simple dimensional changes. In this section, we will explore the various ways in which shrinkage affects plastic materials.
3.1. Dimensional accuracy:
One of the most direct effects of shrinkage on plastic materials is a change in dimensional accuracy. As the molten plastic cools and solidifies, it contracts, leading to a reduction in size. Failure to account for this shrinkage in the design and molding process can result in products that do not meet the desired specifications.
3.2. Warpage:
Shrinkage, if uneven or inconsistent, can contribute to warpage in plastic components. Variances in cooling rates or inadequate mold design may lead to non-uniform shrinkage, causing the material to warp or distort. This can compromise the structural integrity and aesthetic appeal of the final product.
3.3. Residual stress:
The cooling process that induces shrinkage can generate internal stresses within the plastic material. These residual stresses may affect the mechanical properties of the material, making it more susceptible to cracking, deformation, or reduced durability. Proper consideration of shrinkage is essential to mitigate the impact of residual stress.
3.4. Tolerances and fitment:
Shrinkage plays a pivotal role in determining the tolerances and fitment of plastic components. Designers and manufacturers must carefully account for shrinkage to ensure that assembled parts align correctly and meet the required specifications. Failure to do so can result in components that do not fit together as intended.
3.5. Surface finish:
Shrinkage can influence the surface finish of plastic materials. Rapid or uneven cooling may lead to surface irregularities, such as sink marks or surface depressions. Understanding the shrinkage characteristics of the chosen polymer is essential for achieving a smooth and aesthetically pleasing surface finish.
3.6. Material selection:
The choice of plastic material itself is influenced by its shrinkage characteristics. Different polymers exhibit varying degrees of shrinkage during the cooling process. Manufacturers and designers must consider these properties when selecting a material for a specific application, ensuring that the chosen polymer aligns with the desired final dimensions.
3.7. Tooling considerations:
Shrinkage affects not only the plastic material but also the tooling used in the manufacturing process. Mold designs must incorporate allowances for shrinkage to produce accurate and consistent results. Failure to account for shrinkage in tooling can lead to increased wear, maintenance issues, and a decrease in overall tool life.
3.8. Production efficiency:
Shrinkage can impact the overall production efficiency and yield. Incorrectly accounting for shrinkage may result in the production of defective parts, leading to increased scrap rates and production costs. Optimizing processing conditions and mold designs based on shrinkage considerations can enhance efficiency and reduce waste.
4. Tips on how to deal with shrinkage of plastic material
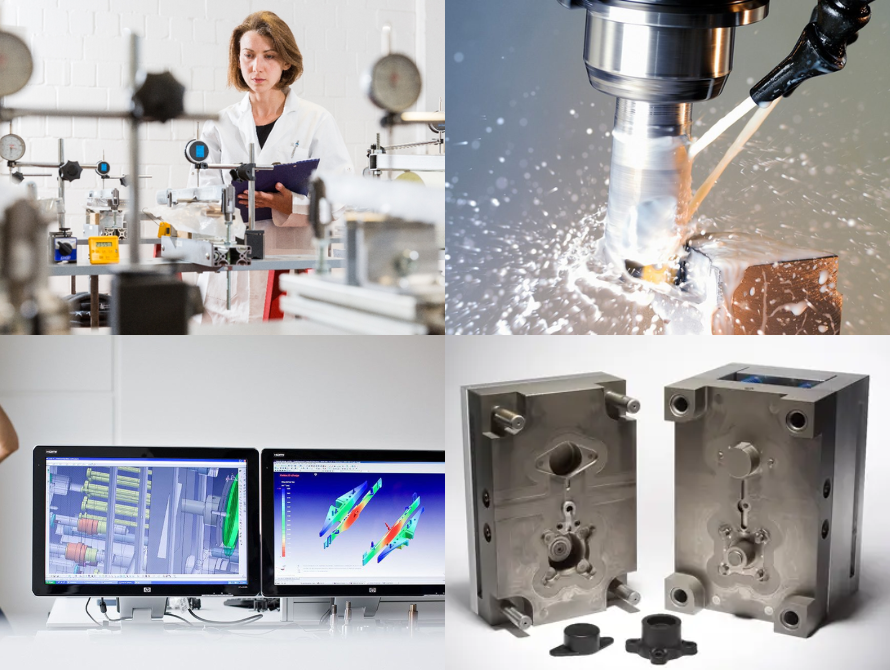
Effectively managing the shrinkage of plastic materials is a critical aspect of successful manufacturing. Whether you're a designer, engineer, or involved in the production process, here are some valuable tips to help you navigate and address the challenges associated with shrinkage.
4.1. Understand material properties:
Begin by thoroughly understanding the properties of the plastic material you're working with. Different polymers exhibit varying shrinkage behaviors. Consult material data sheets, conduct testing, and consider the amorphous or crystalline nature of the polymer to make informed decisions about shrinkage expectations.
4.2. Incorporate design allowances:
Anticipate shrinkage in the design phase by incorporating allowances for the expected contraction of the material. Adjust dimensions accordingly, factoring in both mold and post-mold shrinkage. This proactive approach ensures that the final product aligns with the intended specifications.
4.3. Optimize mold design:
Pay meticulous attention to mold design. Consider factors such as gate placement, cooling channels, and venting to control and distribute heat effectively. Well-designed molds can help minimize uneven shrinkage, reducing the likelihood of warpage and improving the overall quality of the molded parts.
4.4. Optimize processing conditions:
Fine-tune processing conditions such as temperature, pressure, and cooling rates to achieve the desired balance between mold fill and shrinkage control. Experiment with different settings to find the optimal conditions that minimize shrinkage without compromising the efficiency of the production process.
4.5. Conduct material testing:
Conduct comprehensive material testing to gather data on shrinkage behavior under various conditions. This empirical approach provides valuable insights into how a specific plastic material responds to different molding parameters, enabling more accurate predictions and adjustments.
4.6. Implement post-molding techniques:
Consider post-molding techniques to address shrinkage issues. Secondary processes, such as annealing or stress relieving, can be employed to minimize residual stresses and enhance dimensional stability. However, it's essential to carefully assess the impact of these techniques on material properties.
4.7. Collaborate with material suppliers:
Establish open communication with material suppliers. They can provide valuable guidance on the characteristics of the plastic material and offer insights into optimal processing conditions. Collaboration ensures that you have access to the latest information and technologies related to shrinkage management.
4.8. Monitor and adjust:
Regularly monitor the production process and inspect finished parts for adherence to dimensional specifications. If deviations are observed, be prepared to make necessary adjustments to processing conditions, tooling, or design elements to address any unexpected shrinkage issues.
4.9. Continuous improvement:
Treat shrinkage management as an ongoing process of continuous improvement. Gather feedback from production runs, learn from any challenges encountered, and apply this knowledge to refine future designs and manufacturing processes. Continuous improvement ensures that your approach to shrinkage remains dynamic and responsive.
5. Conclusion
In navigating the intricate world of plastic material shrinkage, precision is paramount. By incorporating design allowances, optimizing mold features, and fine-tuning processing conditions, manufacturers can minimize the impact of shrinkage, ensuring that the final products meet stringent specifications. Collaboration with material suppliers, continuous monitoring, and a commitment to improvement contribute to a holistic approach in managing shrinkage challenges.
As we conclude this exploration, it is evident that a nuanced understanding of shrinkage empowers industry professionals to create plastic components with precision, durability, and optimal performance.