From masterbatches, wood powder and plastic additives we can generate a new material called Wood Plastic Composite (WPC) – the perfect choice for the construction industry. The combination of masterbatches, wood pulp and additives to create WPC - Wood Plastic Composite is a big progress in the material industry.
1. The mixture of masterbatches, wood power and additives instituting WPC with advanced properties
With the ability to protect natural wood resources while maintain the same production procedure, plastic wood composite, with superior properties, can be applied widely in architectural works, replaces natural wood material and avoids common problems such as humidity, being eaten by termite, etc.
The process of combine masterbatches, wood power and additives into a unique material
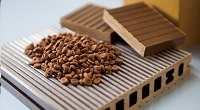
Masterbatches (in various types HDPE, PVC, PP, ABS, PS, etc.) and wood (in many forms of sawdust, pulp, peanut shell, bamboo, rice husk, etc.) is the two most basic ingredients to generate Wood Plastic Composite. These ingredients are mixed at a proper ratio and added several plastic additives such as colorant for plastic, splicing agents, stabilizers, reinforcing agents, etc., either with cellulose or inorganic origins, helping to constitute more durable products with improved properties and new features. The compound will then be put through the production chain to create WPC compound pellets and put into extruders, pressed with high strength to create shaped plastic panels according to customer requirements.
Plastic wood composite made from masterbatches, wood pulp and additives has the superior advantages over other types of wood
As being a product of masterbatches, wood pulp and additives, plastic wood composite inherited many advantages over the original wood. As the name suggests, WPC has both properties of wood and plastic so it can be processed by traditional carpentry tools. Meanwhile they still have the properties of plastic such as moisture-proof, anti-rot, although it is not as tough as normal wood. In general, products made of plastic wood composite not only have surface feels like natural wood, they also gain these the following advantages thanks to the combination of wood materials and plastic additives:
- Easily to be shaped according to customer requirements
- Perfect moisture resistance and waterproofing, even if applied in outside areas with high humidity or exposed to water
- Good anti-chapping and anti-warping ability
- Friendly to the environment
- Be able to making use of non-reusable wood resources in the circumstances in which the wood demand increasingly became scarce
- Good color retention ability. Do not need to use paints or colorant for plastic because it can be mixed masterbatches within the production process to create a variety of colors (instead of the common brown wood when using natural wood)
- Anti-termite, anti-corrosion, hard to be decayed, so there is no need for regular maintenance and repair like natural wood
- Good heat insulation and flame resistance inherited, in general it is less flammable than regular wood
- The weight is lighter than natural wood so it is easy to be transported
- Most important, its price is much cheaper than natural wood
2. From masterbatches, wood powder and additives to the applications of wood plastic composite
Made of masterbatches, wood powder and additives, the demand of using plastic wood composite in construction and architectural works is constantly increasing. If you want to have a cozy, clean interior space without worrying about mold, termites in the kitchen cabinets, the plastic wood composite is the perfect choice because of being able to withstand perfectly watery conditions and able to resist the termites. Common applications nowadays of this material are outdoor plastic wood floors, fences, ceiling tiles, walls, etc.

There are 2 popular types of plastic wood: PVC plastic wood compound (which main component is PVC resin) suitable for interior design with an economical price and PE plastic wood compound (which main component is PE plastic) that is widely used in outdoor buildings, also known as exterior constructive material because of the ability to withstand extreme weather conditions.
Plastic wood composite from PE masterbatches - new material for outdoor construction
Made by PE plastic masterbatches, wood pulp and additives (colorant for plastic), PE plastic wood composite can overcome weaknesses of other materials such as stone, brick or natural wood. PE plastic wood compound combined with anti-plastic additives resist to cracking, warping and color fading so it is suitable for outdoor decoration without fear of being damaged by weather. Moreover, PE plastic wood is reusable and highly durable, only requires low maintenance cost.
Constructors often utilize PE plastic wood composite in flooring, building columns, multipurpose bars, multi-purpose blisters and wall panels.
WPC made from PVC masterbatches - new material for interior design
Combining PVC masterbatches, wood powder and additives, PVC wood plastic composite is suitable for making indoor furniture and features thanks to the properties of lightweight, easy processing, good moisture resistance and termites resistance. PVC plastic mixed with wood pulp and plastic additives will be the ideal choice to make kitchen cabinets, interior furniture of yachts, bathrooms, windows, etc. with high aesthetics and durability.