Injection mold machines are vital for many manufacturing processes, producing everything from automotive parts to household items. To ensure these machines continue to operate efficiently and deliver high-quality results, proper maintenance is crucial. This article will provide insights into why maintaining injection mold machines is so important, along with valuable tips for keeping them in top shape. Finally, we’ll explore how EuroPlas supports businesses by providing high-quality materials that enhance the performance of these machines.
1. The Importance of Maintaining Injection Mold Machines
Injection mold machines are the backbone of many industries, especially in plastic manufacturing, automotive, and packaging sectors. These machines work under extreme pressure and heat to shape and mold materials into precise parts. Over time, wear and tear from consistent operation can lead to reduced efficiency, defects in products, and even costly downtime. That’s why regularly maintaining your injection mold machines is essential for extending their lifespan and ensuring consistent, high-quality production.
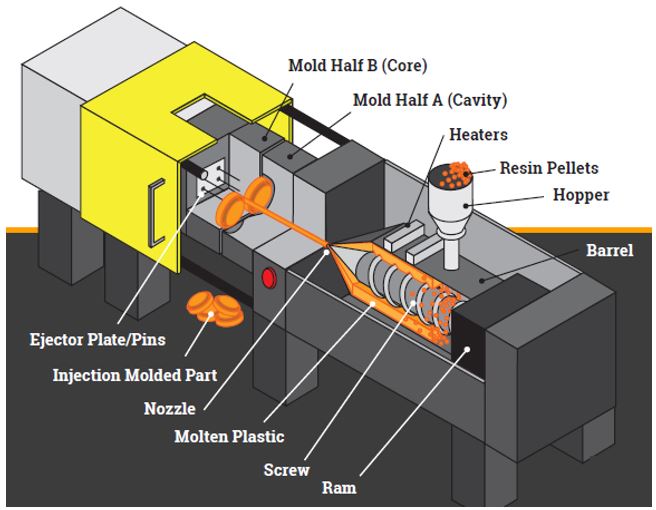
Injection mold machines are the backbone of many industries.
Proper maintenance reduces the risk of machine breakdowns and minimizes the chances of producing defective parts. When injection mold machines are not properly cared for, they are more prone to issues like uneven molding, flash (excess material around the edges of the product), and even structural damage. Additionally, failing to maintain the machines can lead to increased energy consumption, resulting in higher operating costs.
One of the key reasons to keep your injection mold machines healthy is the cost-saving aspect. By avoiding unexpected repairs and part replacements, businesses can reduce unplanned downtime and maintain a smooth production process. Regularly serviced machines also operate more efficiently, contributing to faster cycle times and better-quality products. When your machines are running smoothly, your entire production line benefits, leading to more reliable results and higher customer satisfaction.
Another benefit of regular maintenance is the ability to catch small issues before they become major problems. During routine checks, you can identify components that are starting to wear out or malfunction. Replacing or repairing these parts early helps prevent more significant damage and extends the overall lifespan of the machine. Ultimately, maintaining injection mold machines allows businesses to operate more efficiently and profitably, making it a critical component of any manufacturing operation.
Read more: Startup And Shutdown Protocols Of Injection Molding Machines
2. Tips to Keep Injection Mold Machines Healthy
Keeping injection mold machines in optimal condition requires a proactive approach to maintenance. By following a few key tips, you can prevent common problems and extend the lifespan of your machines, ensuring consistent performance over time. Below are some practical ways to keep your injection mold machines healthy.
2.1. Regular Cleaning and Lubrication
One of the most important steps in maintaining injection mold machines is regular cleaning and lubrication. During operation, the machine accumulates debris, dust, and other contaminants that can interfere with its performance. Regular cleaning helps remove these substances and prevents blockages or malfunctions. Additionally, ensuring that all moving parts are properly lubricated reduces friction and wear, allowing the machine to run smoothly and efficiently. Make sure to use high-quality lubricants designed specifically for injection mold machines.
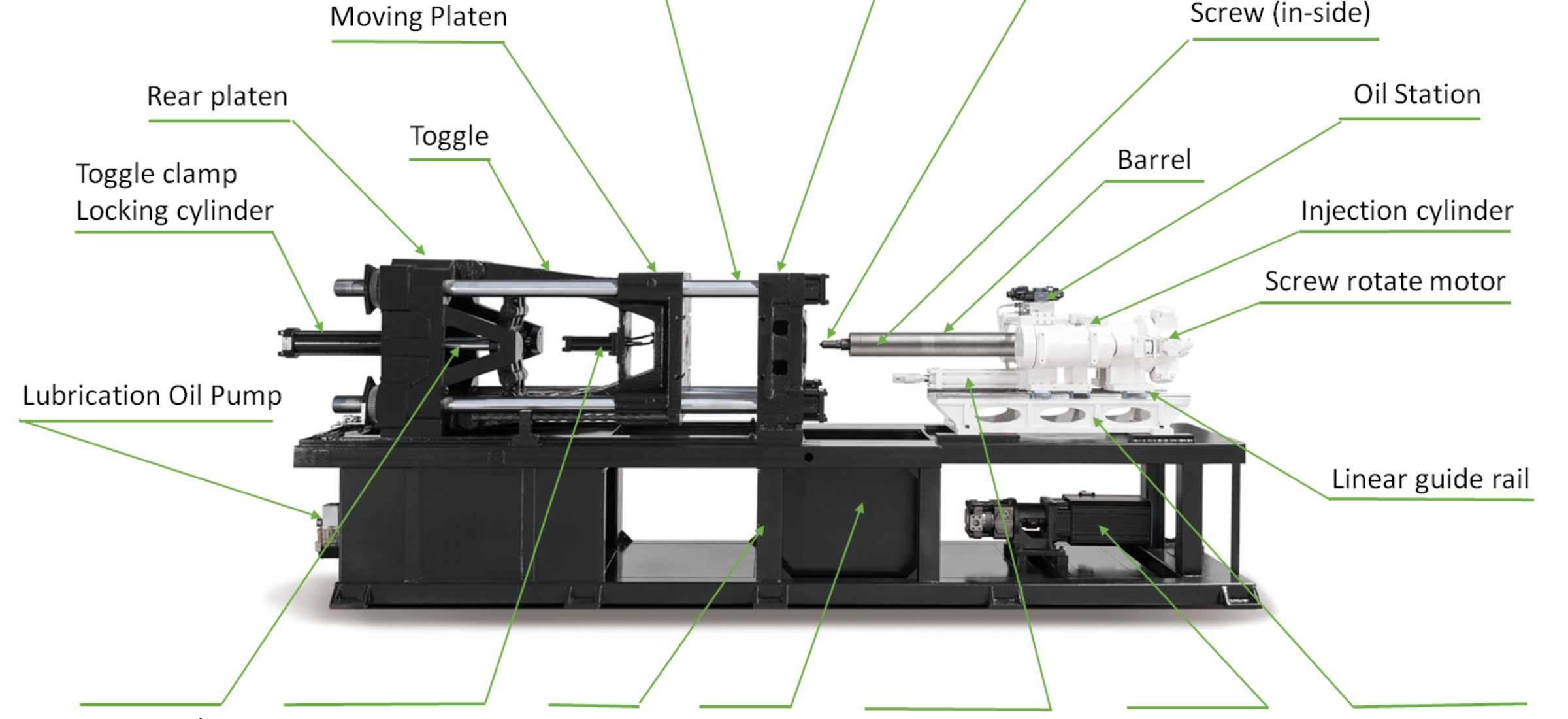
One of the most important steps in maintaining injection mold machines is regular cleaning and lubrication.
2.2. Monitoring Machine Settings
To keep injection mold machines running at their best, it’s important to regularly monitor and adjust the machine settings. Factors such as temperature, pressure, and injection speed can impact the quality of the final product. Over time, these settings may need to be fine-tuned to ensure the machine is operating at peak efficiency. Pay close attention to any fluctuations in performance, and make adjustments as needed to maintain consistent results. Keeping detailed records of machine settings can help identify trends and areas for improvement.
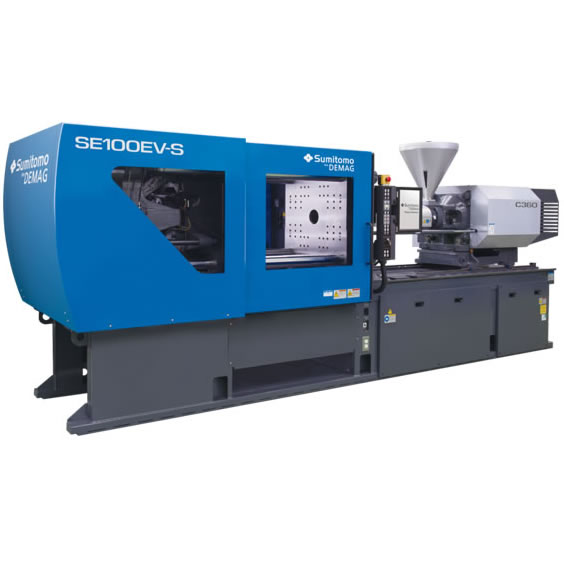
Tips to Keep Injection Mold Machines Healthy
2.3. Inspecting Critical Components
Injection mold machines are made up of numerous parts, many of which are critical to the machine’s overall function. Regularly inspecting components such as screws, barrels, nozzles, and molds is essential for catching signs of wear or damage early. Look for visible signs of wear, such as scratches, dents, or cracks. In some cases, you may need to use specialized tools or equipment to thoroughly inspect internal components. By identifying worn-out parts early, you can replace them before they cause more significant damage to the machine.
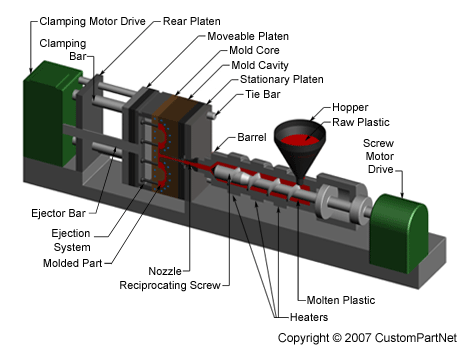
Injection mold machines are made up of numerous parts.
2.4. Maintaining the Cooling System
The cooling system is a vital component of any injection mold machine. It helps regulate the temperature of the machine and prevents overheating, which can lead to machine failure or defects in the molded parts. Regularly inspect the cooling system to ensure it is functioning properly. Look for any signs of blockages, leaks, or worn-out parts that could impact the system’s performance. Cleaning the cooling channels and replacing worn components will help keep the machine running smoothly.
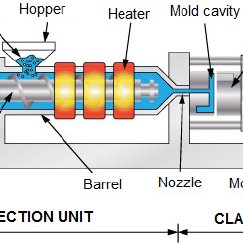
The cooling system is a vital component of any injection mold machine.
2.5. Keeping Accurate Maintenance Records
Effective machine maintenance requires good record-keeping. Keeping detailed records of all maintenance activities performed on your injection mold machines can help identify patterns or recurring issues. It can also provide insight into when certain parts are likely to need replacement, allowing you to schedule maintenance in advance and avoid unexpected downtime. Additionally, maintenance records are essential for troubleshooting any issues that arise, as they provide a comprehensive history of the machine’s condition and repairs.
3. Conclusion
Maintaining injection mold machines is crucial for ensuring long-term efficiency, product quality, and cost savings in any manufacturing process. By following the tips outlined above, businesses can prevent costly repairs, reduce downtime, and extend the lifespan of their equipment. Regular cleaning, component inspections, and keeping accurate maintenance records are just a few of the practices that can help keep these machines running at their best. Ultimately, a well-maintained injection mold machine will deliver consistent performance, contributing to a more efficient and profitable production process.
4. About EuroPlas
At EuroPlas, we understand the importance of reliable and high-performance injection mold machines in manufacturing. As a leading supplier of filler masterbatches, EuroPlas offers innovative solutions that enhance the performance and longevity of injection mold machines. Our filler masterbatches are designed to improve the strength, flexibility, and overall quality of plastic products, while also optimizing the performance of the machines used in their production.
EuroPlas is committed to helping businesses maintain efficiency by providing high-quality materials that reduce wear on machinery and improve output. Our products are widely used in industries ranging from automotive to packaging, and we pride ourselves on delivering sustainable, cost-effective solutions. Whether you need custom formulations or advice on the best materials for your specific applications, EuroPlas is here to support your needs.
For more information about how our filler masterbatches can enhance your manufacturing process or to learn more about our full product range, get in touch with EuroPlas today. We are dedicated to helping you find the right materials to optimize performance, cut costs, and drive sustainability in your operations.