Đọc thêm:
- Các lỗi thường gặp trong quá trình ép phun nhựa
- Tìm hiểu về hạt nhựa PP cho ép phun
- Tầm quan trọng của polyolefin - PP, PE
- PE, PP, LDPE, HDPE, PEG – Chính xác thì hạt nhựa được làm từ gì?
1. Tổng Quan về kéo sợi PP, HD
Quy trình sản xuất bao PP dệt
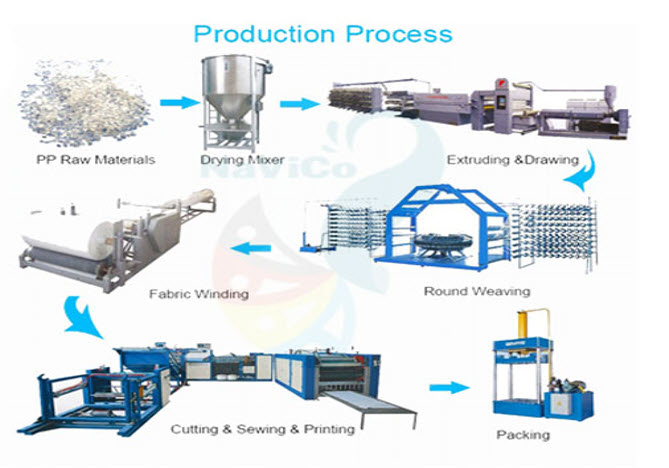
Công đoạn tạo chỉ là công đoạn quan trọng nhất. Nó quyết định trực tiếp đến chất lượng sản phẩm cuối như độ bền, cơ tính, ngoại quan, chất lượng… Đây cũng là công đoạn khách hàng hay phản ánh nhất đối với chất lượng của nguyên liệu đầu vào ( filler, phế, nhựa nguyên sinh...)
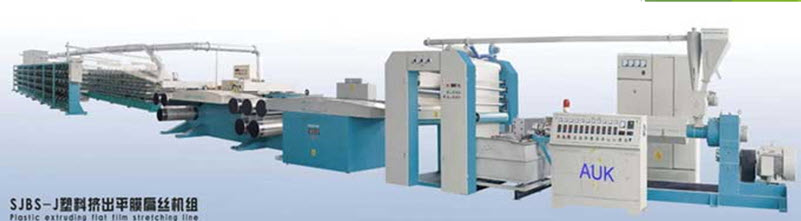
Thành phần nguyên liệu đầu vào của máy kéo chỉ PP bao gồm:
- Nhựa PP nguyên sinh MI= 2.5- 5
- Filler masterbatch (chất độn nhựa): nền nhựa PP hoặc PE, tỉ lệ dùng 2- 45% tùy yêu cầu chất lượng sản phẩm cuối
- Nhựa Phế : phế quay đầu trong nhà máy hoặc phế mua ngoài. Tỉ lệ dùng tùy sản phẩm cuối. Đặc điểm nhựa phế thường lẫn nhiều loại nhựa khác nhau, màu sắc thường ko đồng đều và có nhiều tạp chất bẩn.
- Phụ gia và hạt màu: đáp ứng các yêu cầu khác của sản phẩm về màu sắc và cơ tính.
2. Các lỗi hay gặp trong quá trình kéo sợi
Các hiện tượng lỗi thường gặp trong quy trình kéo sợi có thể kể đến như sau:
Filler kém phân tán
- Loang màu
- Sọc màng
- Mang nước theo màng
- Bụi- Vấn đề về máy móc thiết bịKhi gặp 1 trong cái lỗi thì gây ra hiện tượng trên, nhá sản xuất có thể không chạy sản xuất được chỉ (đứt chỉ, sập dàn) hoặc chỉ bị kém chất lượng so với yêu cầu thành phẩm. Cách xử lí từng hiện tượng trên cụ thể như sau:
2.1. Filler kém phân tán
Hiện tượng chất độn nhựa (filler masterbatch) kém phân tán có thể đến từ 2 nguyên nhân:
- Do nhà sản xuất filler cung cấp sản phẩm kém phân tán. Kém phân tán cục bộ ( lỗi xuất hiện cục bộ tại 1 bao hoặc 1 vài bao là lỗi quá trình sản xuất, hoặc kém phân tán toàn bộ (kém phân tán theo hệ thống là lỗi nguyên liệu đầu vào của filler, công thức sx, thiết bị sx…)
Do người sử dụng filler:
+ Do dừng máy lâu dẫn đến hiện tượng đóng khối đầu đùn. Giải pháp là nhà sản xuất sợi nên chạy 1 máy khoảng thời gian thì sợi sẽ về trạng thái bình thường.
+ Nguyên liệu dùng nhiều nhựa phế hoặc ảnh hưởng bởi độ ẩm của nguyên liệu. Giải pháp cho trường hợp này là bạn nên sấy khô nguyên liệu.
+ Thiết bị, dây chuyền không sạch, nên vệ sinh máy thường xuyên.
2.2. Loang màng
Màng sau khi qua bể nước làm mát, dòng nhựa được định hình nhưng độ dày màng không đồng đều. Thường xuất hiện vệt hình chữ “ V” trên màng film phẳng. Sau khi qua bàn dao được chẻ thành những sợi nhỏ, chịu lực kéo giãn của các lu thì các điểm mỏng hơn trên film trước đó bị dãn mạnh và gây ra đứt sợi.
Kết quả là lực giữa các cuộn chỉ và trên cùng 1 cuộn chỉ không đồng đều, quá trình kéo sợi làm đứt sợi vặt nếu bị nhẹ, sập dàn nếu bị nặng hoặc điều kiện gia công khắc nghiệt ( chạy tỉ tốc cao, tốc độ chạy cao, Dienier chỉ thấp…)
Nguyên nhân:
- Áp lực dòng nhựa chưa đủ lớn tại đầu khuôn để có thể đùn nhựa đều tại mọi vị trí (thường xảy ra với các loại máy có đầu đùn dài hoặc 2 đầu đùn )
- Nhiễu dòng chảy do thành phần nguyên liệu trộn chưa phù hợp ( do sự tương hợp kém giữa nhựa, nhựa phế và nhựa nền Filler, MI, độ chịu nhiệt của nhựa nền Filler hoặc phế
- Sự không đồng nhất của dòng nhựa sau khi ra khỏi đầu khuôn làm melt strength tại 1 và điểm bị yếu à bị kéo dãn mạnh à mỏng hơn
2.3. Sọc màng
Hiện tượng: Màng sau khi qua bể nước làm mát, dòng nhựa được định hình nhưng độ dày màng không đồng đều. Thường xuất hiện vệt các vệt sọc song song nhau do độ dày màng không đều nhau. Định lượng chỉ trên các cuộn dao động, cơ tính và độ dãn của sợi giao động lớn
Nguyên nhân: Chủ yếu do đầu die bị bẩn do quá trình sản xuất lâuà cháy nguyên liệu bám ở đầu đùn, chiếm 1 phần thể tích miệng khuôn
Phía nhà sản xuất filler:
+ Cặn sinh ra do cháy filler: Chủ yếu do cháy phụ gia được thêm vào trong qua trình sx filler
+ Sử dụng tỉ lệ filler cao
- Phía người sử dụng filler: Nhiệt độ máy kéo sợi quá cao ( do cài đặt hoặc do cảm biến nhiệt không chính xác…)
Hình ảnh miệng đầu khuôn sau khi bị sọc màng tháo ra vệ sinh
2.4. Mang nước theo màng
Hiện tượng:
- Hiện tượng: Màng film được lu kéo lên ra khỏi bể nước làm mát sẽ kéo theo 1 lượng nước
- Lượng nước này nếu được kéo lên bàn hấp nhiệt sẽ làm giảm khả năng định hướng của sợi-à chất lượng sợi giảm ( giảm lực, giảm độ dãn dài…) Quá trình gia công sợi có hiện tượng đứt sợi vặt hoặc sập dàn
Nguyên nhân: Do hiện tượng dính ướt giữa màng film và nước. Các yếu tố làm gia tăng hàm lượng nước theo màng:
- Filler
+ Việc dùng thêm filler trong quá trình kéo sợi giúp quá trình sx trơn tru hơn. Tuy nhiên cũng ảnh hưởng làm tăng lượng nước mang theo màng
+ Các hạt độn CaCO3 làm bề mặt film nhám hơn
+ Phụ gia được thêm vào trong quá trình sx Filler thường là các chất có nhóm chức ưa nước
Thiết bị sản xuất:
+ Các máy kéo sợi mới thường được trang bị hệ thống phụ trợ gồm thanh gạt nước, hệ thống thanh hút nước bám bề mặt màng film -à các hệ thống này hỏng hoặc làm việc kém hiệu quả gây ra hàm lượng nước lên màng tang đột biến.
+ Độ cao và độ dốc của màng film cũng ảnh hưởng tới khả năng nước bị kéo màng
2.5. Bụi
Hiện tượng: Trong quá trình kéo sợi thường xuất hiện bột trắng tại các điểm sợi tiếp xúc sinh ra do chỉ ma sát với thiết bị.
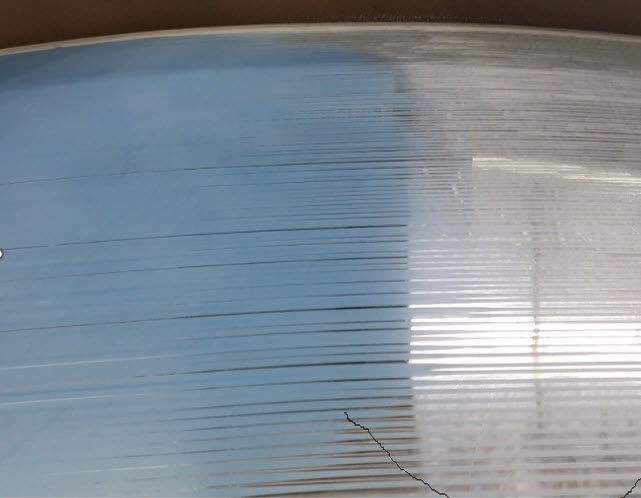
Bụi tại bàn gia nhiệt
Bụi ở bể nước trong quá trình sản xuất chỉ PP
Nguyên nhân: Tiếp xúc giữa chỉ và thành thiết bị sinh ra ma sát bào mòn 1 phần bột đá hoặc làm nứt gãy bề mặt chỉ sinh ra dạng bột nhỏ. Việc bụi sinh ra trong quá trình sx là không thể tránh khỏi, mức độ tùy thuộc vào điều kiện sản xuất, tỉ lệ pha trộn nguyên liệu.