Related:
- Polypropylene pellets for injection molding - everything you should know
- The significance of polyolefins - PP, PE
- PE, PP, LDPE, HDPE, PEG plastic masterbatch
I. HD, PP raffia
1. PP woven bag manufacturing process
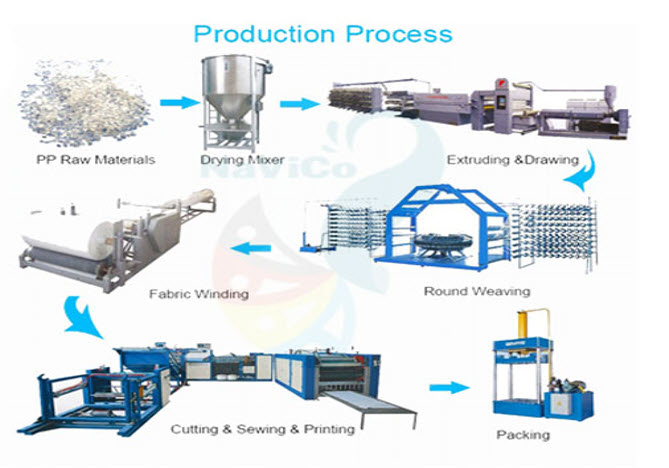
The thread-making stage is the most important step. It directly determines the quality of the end product such as durability, mechanical properties, appearance, and quality... This is also the stage that customers most often reflect on the quality of input materials (filler, waste plastic, primary plastic...)
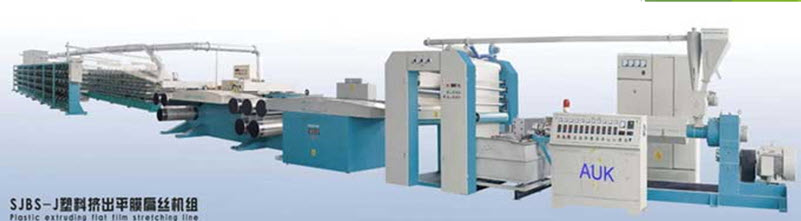
The input material composition of the PP thread tractor includes:
- Primary PP plastic MI= 2.5-5
- Filler masterbatch (plastic filler): PP or PE plastic base, use rate 2- 45% depending on final product quality requirements
- Recycled plastic: recycled waste in the factory or purchased outside. Usage rate depends on the end product. The characteristics of waste plastic are often mixed with many different types of plastic, the color is often uneven and there are many dirty impurities.
- Additives and pigments: meet other product requirements in terms of color and mechanical properties.
II. HD, PP raffia troubleshooting
Common errors in the raffia process can include the following:
- Poorly dispersed filler
- Color fading
- Film stripes
- Film carries water
- Dust
- Machine and equipment problems
When encountering these errors, the manufacturer's production may be interrupted and the finished products have poor quality. Learn how to deal with each of the above phenomena in detail below:
1. Poorly dispersed filler
Poor dispersion of filler masterbatch can come from 2 reasons:
- Because the filler manufacturer provides a poorly dispersed product. Poor local dispersion (failure occurring locally in 1 bag or several bags is a manufacturing process error, or poor dispersion in the whole (systematic poor dispersion is a defect in the filler input material, production formula). , production equipment...)
- Filler users:
+ Due to the long stop of the machine, the extruder block will be closed. The solution is that the yarn manufacturer should run 1 machine for a period of time, the yarn will return to normal.
+ Raw materials use a lot of waste plastic or are affected by the moisture content of raw materials. The solution in this case is that you should dry the material.
+ Equipment and lines are not clean, so the machine should be cleaned regularly.
2. Color fading
After passing the cooling water tank, the film is shaped but the film thickness is not uniform. Often a "V"-shaped streak appears on flat film. After the knife is split into small fibers, subjected to the stretching force of the rollers, the thinner points on the previous film are strongly stretched and cause fabric breakage.
Causes:
- The plastic flow pressure is not large enough at the mold head to be able to extrude the plastic evenly at all positions (usually happens with machines with long extruders or 2 extruders).
- Flow interference due to inappropriate mixing material composition (due to poor compatibility between plastic, waste plastic and Filler, MI, the heat resistance of Filler or waste plastic).
- The inhomogeneity of the resin flow after exiting the mold head causes melt strength at 1 and the weak point to be stretched strongly to thinner.
3. Film stripes
Phenomenon: After passing through the cooling water bath, the film is shaped but the film thickness is not uniform. Streaks of parallel stripes appear due to unequal film thickness. Thread quantification on oscillating spools, the mechanical properties and elongation of the oscillating thread are large.
Causes: Mainly because the die head is dirty due to the long burning process of the raw material attached to the extruder, occupying a part of the mold mouth volume.
- Filler manufacturers:
+ Residue generated by burning filler: Mainly due to burning of additives added during filler production.
+ Use a high filler rate.
- Filler users:
+ Spinning machine temperature is too high (due to incorrect settings or temperature sensor...)
The image of the die causing film stripe after being removed for cleaning
4. Film carries water
Phenomena: When the film is pulled up from the cooling water tank, it will pull a amount of water. This amount of water, if drawn to the steaming table, will reduce the orientation of the yarn - and the quality of the yarn will decrease (reduce force, reduce elongation...)
Causes: Due to the phenomenon of wet adhesion between the film and water. Factors that increase membrane water content:
- Filler
+ The use of filler in the spinning process makes the production process smoother. However, it also has the effect of increasing the amount of water carried by the film.
+ CaCO3 fillers make the film surface rougher.
+ Additives added during Filler production are usually substances with hydrophilic functional groups.
- Equipment of production:
+ New spinning machines are often equipped with auxiliary systems including wipers, water absorbing rod systems that adhere to the film surface - and these systems fail or work inefficiently, causing water content on the film.
+ The height and slope of the film also affect the ability of water to pull the film.
5. Dust
Phenomenon: During the manufacturing process, white powder often appears at the points of contact caused by friction with the device.
Dust created while manufacturing
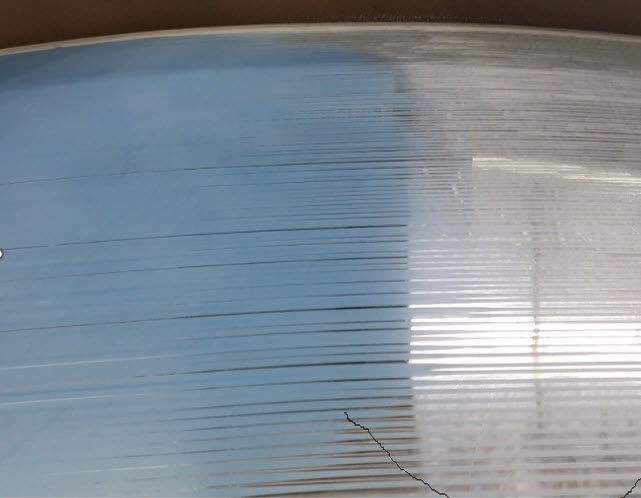
Dust created by the heater
Dust in the water tank during the production of PP thread
Cause: The contact between the thread and the device produces friction that erodes part of the stone powder or cracks the surface, producing a small powder. The dust generated in the production process is inevitable, the level depends on the production conditions, the mixing ratio of the raw materials.