Blown film extrusion is a widely used process in the plastics industry for the production of films and sheets. This process involves melting down polymer materials and extruding them through a flat die to create a continuous tube of melted plastic. The 3 layer blown film extrusion process is a specific type of blown film extrusion that allows for the production of multi-layer films with improved properties compared to single-layer films.
In this blog, we will dive into the details of the 3 layer blown film extrusion process, including each step involved, and the benefits of this method.
Related:
- Difference between thermoforming and injection molding
- Injection molding troubleshooting
- Types of plastic extrusion and its manufacturing process
- Common applications of filler masterbatch in thermoforming
1. What is blown film extrusion
1.1. Definition
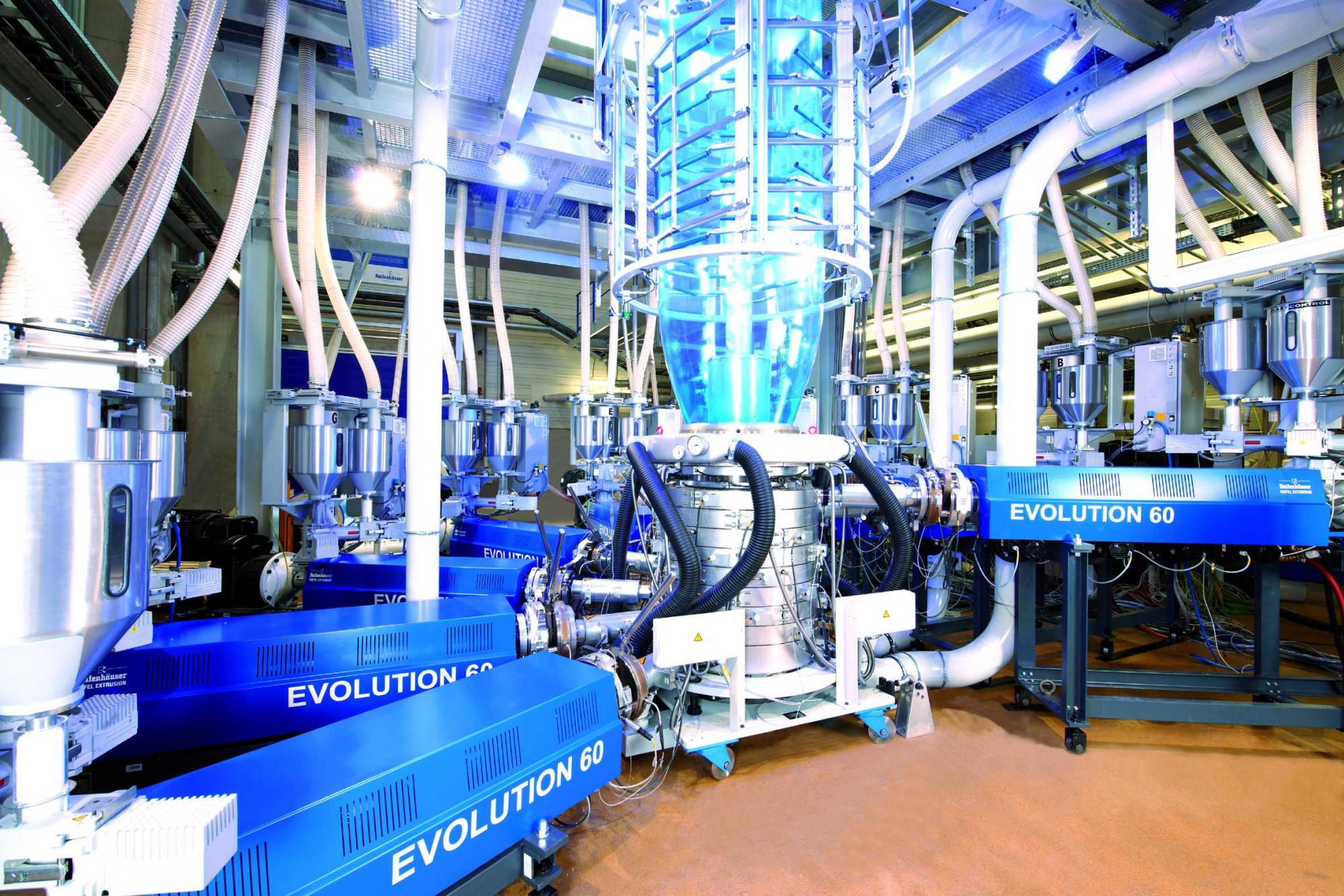
Blown film extrusion is a process used to manufacture plastic films and sheets. The process starts with the melting of plastic resin pellets, which are then extruded through a circular die to form a tube, or "bubble," of plastic. The bubble is then inflated by blowing air into it, causing it to expand and form a flat film. The film is then cooled and collapsed to form a flat plastic sheet, which can be wound onto a roll.
1.2. Benefits
Blown film extrusion is a popular choice for a wide range of applications, and there are numerous benefits proving that it continues to be a crucial component in many industries. Here are the main benefits of using blown flim extrusion:
- Flexibility: Blown film extrusion produces films and sheets that are flexible and able to conform to irregular shapes, making it ideal for packaging applications that require flexibility.
- Durability: Blown film extrusion creates films and sheets that are strong and durable, which makes them ideal for packaging and industrial applications that require toughness and resistance to punctures, tears, and impacts.
- Versatility: Blown film extrusion can produce a wide range of films and sheets with different thicknesses, strengths, and properties, making it a versatile choice for a wide range of applications.
- Cost-effectiveness: Blown film extrusion is a cost-effective method of producing films and sheets, especially when compared to traditional methods such as cast film or blown film extrusion.
- Customizability: Blown film extrusion can be customized to produce films and sheets with specific properties, such as transparency, UV resistance, and electrical conductivity, making it a suitable choice for applications that require specialized properties.
- Environmental sustainability: Blown film extrusion is a green process that generates minimal waste and reduces the use of energy and resources compared to traditional methods.
1.3. Applications
The applications of blown film extrusion are vast and diverse, ranging from food packaging to construction and beyond. In this article, we will explore the various applications of blown film extrusion:
- Food packaging: Blown film extrusion is commonly used in food packaging due to its ability to create flexible and durable films that protect food products and preserve their freshness.
- Medical packaging: Medical packaging requires high-quality and sterile materials to ensure the safety and protection of medical products. Blown film extrusion is used to create films and bags that meet these stringent requirements.
- Industrial packaging: Heavy-duty sheets and films, such as pallet wrap, stretch wrap, and product coverings, are produced via blown film extrusion for use in industrial packaging.
- Agriculture: People also use this method to to create mulch films and covers for agriculture, providing protection and insulation for crops and soil.
- Consumer goods packaging: Packaging for a range of consumer goods, such as toys, home goods, and personal care products, is made using blown film extrusion.
- Automotive packaging: In order to preserve automobile parts and components during storage and transit, blown film extrusion is utilized.
- Construction: Construction films and sheets are produced via blown film extrusion and are used for walls, floors, and roofs.
- Geotextiles: Geotextiles are produced by blown film extrusion and employed in soil stabilization and erosion control applications.
- Textile manufacturing: Production of synthetic textiles, such as nonwovens and woven fabrics, uses blown film extrusion.
2. 3 layer blown film extrusion process
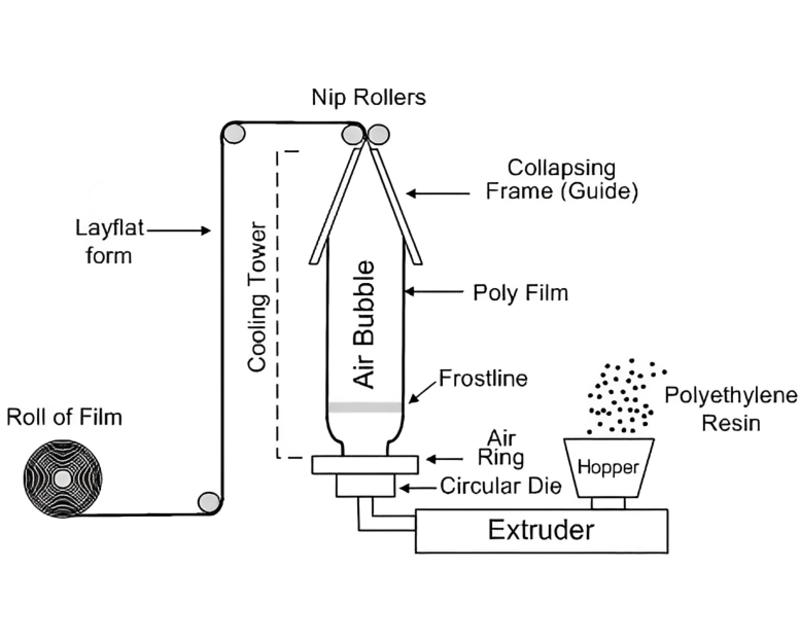
3 layer blown film extrusion is a process used to produce multi-layer plastic films with specific properties and improved performance compared to single-layer films. In this process, three layers of plastic are co-extruded and merged together to form a single, multi-layer film.
Here is a step-by-step explanation of the 3 layer blown film extrusion process:
Step 1: Raw materials preparation
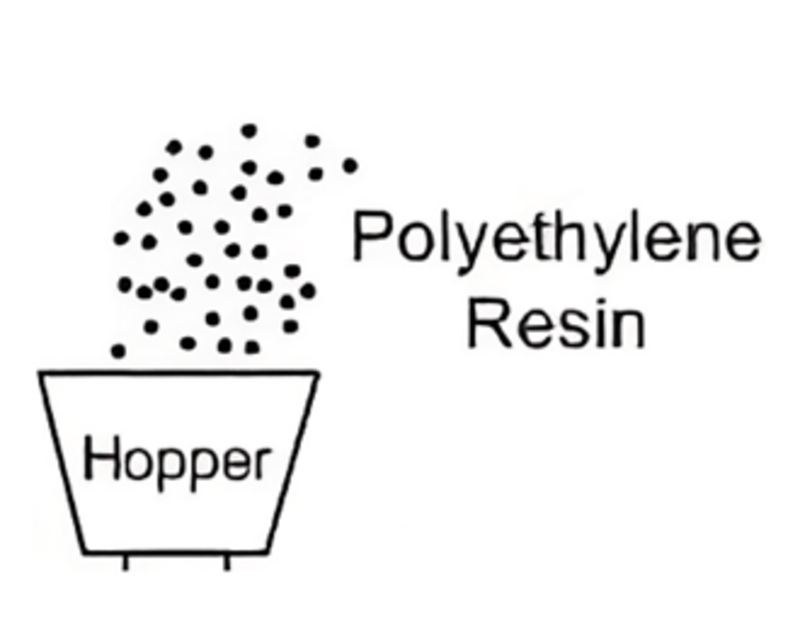
In this first step, the plastic pellets or granules are melted and prepared for the extrusion process. The pellets are fed into a hopper, which is typically located above the extruder. The hopper is designed to store and feed the plastic pellets into the extruder, ensuring a consistent and continuous supply of plastic to the extruder. The plastic is then melted in the extruder through a combination of heat and mechanical shear. The temperature, pressure, and speed of the extruder are carefully controlled to ensure that the plastic is melted at the right temperature and pressure, without degradation or contamination.
The melted plastic is then filtered through a screen changer to remove any impurities, such as contaminants or undissolved pellets. The screen changer is designed to allow the melt stream to flow through a screen or mesh, which traps any impurities or undissolved pellets. The screen is periodically changed or cleaned to maintain a clean and consistent melt stream. The filtered melt stream is then ready for the next step of the process, which is extrusion.
Step 2: Extrusion
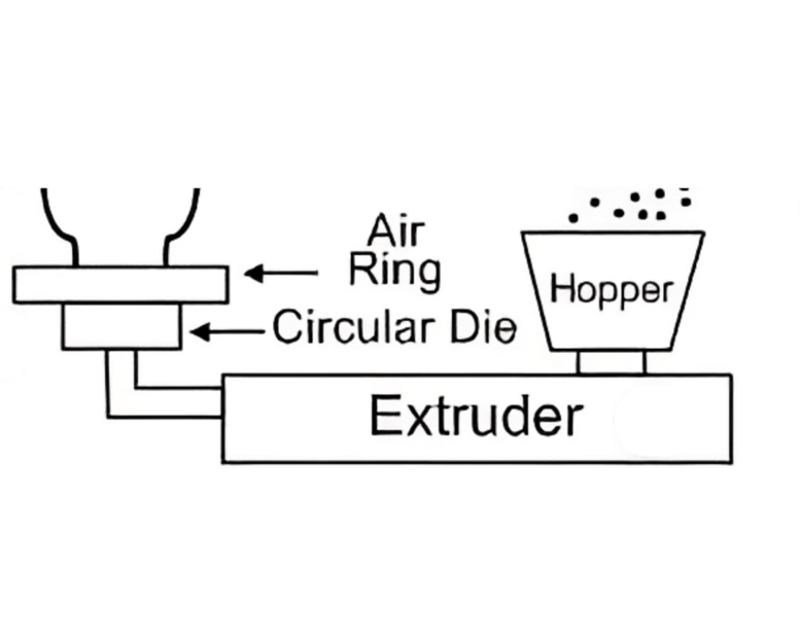
The melted and filtered plastic is then fed into the extruder, which is equipped with multiple feed ports to accommodate the different resin types used in the 3-layer film. The extruder is designed to apply pressure and heat to the melted plastic, forcing it through a circular die, which shapes the plastic into a tube. The diameter of the tube can be adjusted to create the desired size of the film bubble. The tube is then transported to the next stage of the process, which is inflation.
Step 3: Inflation
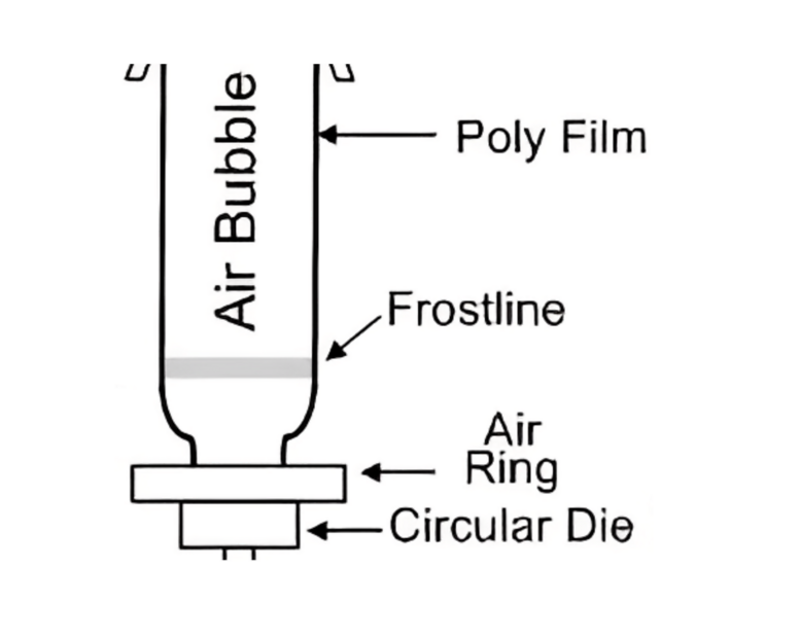
Air is introduced into the tube to create a bubble that expands the tube to a desired diameter. The inflation process helps to create a uniform and consistent layer of plastic that will form the basis of the multi-layer film. The diameter of the bubble is controlled by adjusting the air pressure and the speed of the inflation process. The air pressure and speed must be carefully controlled to ensure that the bubble has the correct size and shape, without collapsing or breaking.
Step 4: Cooling
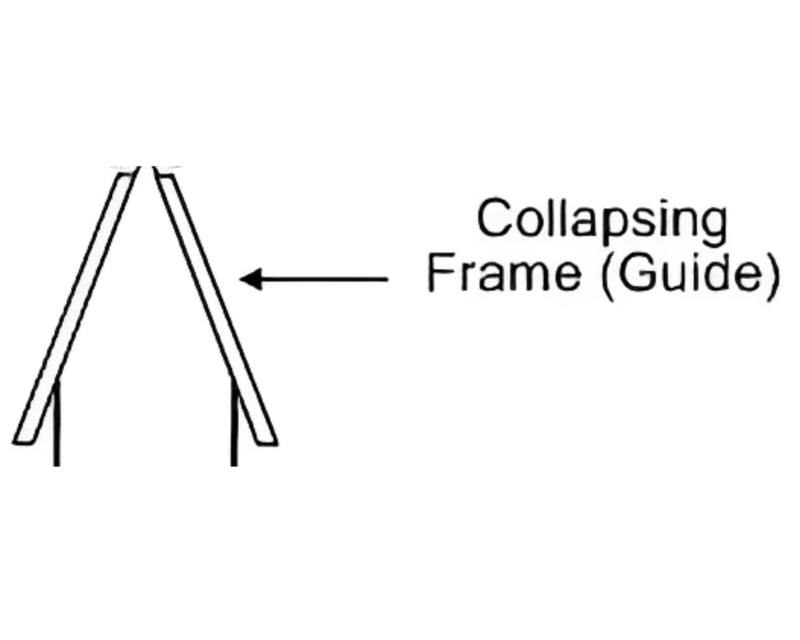
The film bubble is then cooled by blowing air over it. The cooling process solidifies the film and helps to maintain its shape. The cooling process is critical to the final properties of the film, as it affects the crystallinity, orientation, and dimensional stability of the film. The temperature, pressure, and speed of the cooling process must be carefully controlled to ensure that the film has the desired properties and dimensions.
The film is cooled using a combination of air knives, which direct a stream of air over the surface of the film, and cooling rings, which surround the film and provide additional cooling. The air knives and cooling rings are carefully positioned to ensure that the film is cooled evenly and consistently, without causing any distortions or deformations.
Step 5: Collapsing
The film bubble is then collapsed to form a flat film. This is done by adjusting the air pressure and the speed of the collapsing process. It is important to control the pressure and speed carefully to ensure that the film collapses evenly and consistently, without causing any distortions or deformations. The flat film is then wound onto a roll for further processing.
Step 6: Lamination
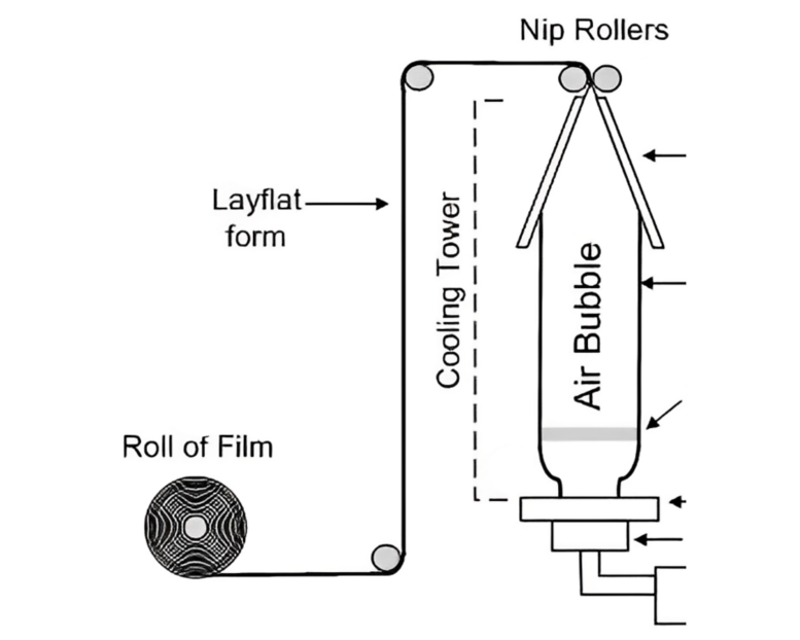
The flat film is then laminated to create the desired multi-layer film. In the case of a 3-layer film, two additional layers of plastic are added to the flat film, creating a total of three layers. The two additional layers can be added using co-extrusion, where two or more layers of plastic are extruded simultaneously, or by laminating two separate films together.
The lamination process is critical to the final properties of the multi-layer film, as it affects the mechanical properties, barrier properties, and optical properties of the film. The temperature, pressure, and speed of the lamination process must be carefully controlled to ensure that the different layers are bonded properly and that the final film has the desired properties.
Step 7: Optional Additional Procedures
In addition to the 6 main steps, there are additional post-processing procedures that might be used to create final products meeting specific customers’ requirements. These include:
- Printing: Printing is the process of adding graphics or text to the surface of the film. This is done to improve the aesthetic appeal of the film or to add information such as product specifications, instructions, or branding. Printing can be performed using a variety of techniques, including flexography, rotogravure, or digital printing. Flexography is a common method for printing on blown film products and uses flexible printing plates that can be easily changed to produce different designs. Rotogravure printing uses a cylinder that has been etched with the desired pattern to transfer the ink onto the film surface. Digital printing uses a high-resolution inkjet printing system that can produce precise and vibrant images.
- Slitting: Slitting is the process of cutting the film into smaller widths or lengths to meet specific customer requirements. This is typically done using a slitting machine that uses a series of rotating knives to cut the film. The slitting process is important because it allows the film to be used in a variety of applications where different widths or lengths are required.
- Punching: Punching is the process of creating holes in the film. This is typically done using a punch press that uses a die and punch to create the holes. Punching is often used to make handle holes in bags or to create vents in packaging to allow air to escape.
- Embossing: Embossing is the process of impressing a pattern or texture into the surface of the film. This is typically done using a roller that has been engraved with the desired pattern. Embossing can be used to improve the aesthetic appeal of the film or to improve its functional properties, such as providing grip or reducing the slipperiness of the film surface.
- Coating: Coating is the process of adding a layer of material, such as an adhesive, to the surface of the film. This is typically done using a coating machine that applies the coating to one or both sides of the film. Coating can be used to improve the durability and performance of the film, such as making it water-resistant or providing a stronger bond for lamination.
These additional steps can help to improve the performance, durability, and functionality of the final product and make it better suited to specific applications. However, it's important to note that not all films require these additional post-processing techniques, and the exact steps involved in a 3-layer blown film extrusion process can vary depending on the requirements of the film being produced.
3. Finding a plastic supplier for blown film extrusion?
Finding a reliable plastic supplier for blown film extrusion is essential to ensure the quality and consistency of your finished products. One top supplier in the industry is EuroPlas, a leading masterbatch manufacturer based in Vietnam.
EuroPlas provides high-quality masterbatch products specifically designed for blown film extrusion. Our product range includes color masterbatches, additive masterbatches, and filler masterbatches that can enhance the performance and appearance of blown film products. When selecting a plastic supplier for blown film extrusion, it is important to consider factors such as the quality of the raw materials, production techniques, and the supplier's commitment to customer satisfaction. EuroPlas is known for our focus on quality and innovation, and our commitment to delivering the best products and services to our customers.
In conclusion, EuroPlas is a trusted supplier for blown film extrusion, offering a range of high-quality masterbatch products to support the needs of the industry. We are dedicated to providing the best solutions to meet the demands of our customers and helping them achieve their goals. So if you have any requirements or want to know further about our products and services, please contact us now!