PP engineering plastic compound is a preferred material in the automotive industry because it helps manufacturers save time, costs, and improve the properties of finished products. Due to the specific requirements of each car's parts, plastic manufacturers have researched and released 6 different types of PP engineering plastic compounds. So what are they? What are their advantages and applications? Let's find out with EuroPlas in the article below.
Related:
Polypropylene pellets for injection molding - everything you should know
Producing non-woven fabrics with PP filler masterbatch
The significance of polyolefins - PP, PE
6 polypropylene compounds for automotive applications
1. What is PP compounds?
Engineering plastic compound definition: Plastic compound is an engineering plastic material made from primary plastic, special reinforcing agents, and appropriate additives according to different formulas to meet the specific characteristics of each finished product. With outstanding advantages, engineering compound plastic is the optimal and specialized material solution to help manufacturers improve production efficiency and finished product quality.
So what is polypropylene compounds? PP compounds are engineering plastic compounds made from PP carrier resin mixed with various types of additives such as conductive carbon black, fireproof additive, etc, and reinforced with Talc minerals and glass fiber/beads in accordance with different formulations in order to create particular properties for plastic end-products.
Here are some applications of polypropylene compounds for automotive applications:
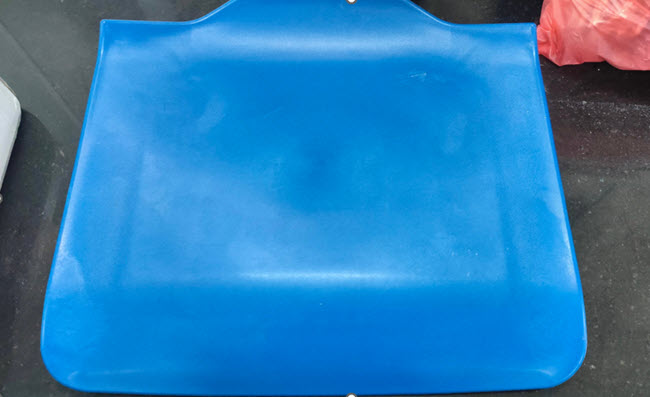
PP GF 30% for bus chair
Compound PP EPDM TD20 for car interiors
ECPPA66R033GF for car fuel tank cap
2. Polypropylene compounds for automotive applications
As mentioned above, depending on the requirements of the finished product, plastic manufacturers will create different types of PP plastic compounds. However, we have the following 6 common types of PP compounds:
PP conductive compound is made from PP resin and carbon black conductive. The small carbon particles added to the PP base resin will help increase the fluidity, impact resistance, and elongation of the finished product. Besides, conductivity is the most outstanding feature of this material. The product brings higher stability compared to standard PP and it increases electrical conductivity to end-products. Manufacturers use PP conductive compound to minimize the anti-static condition for car interior details.
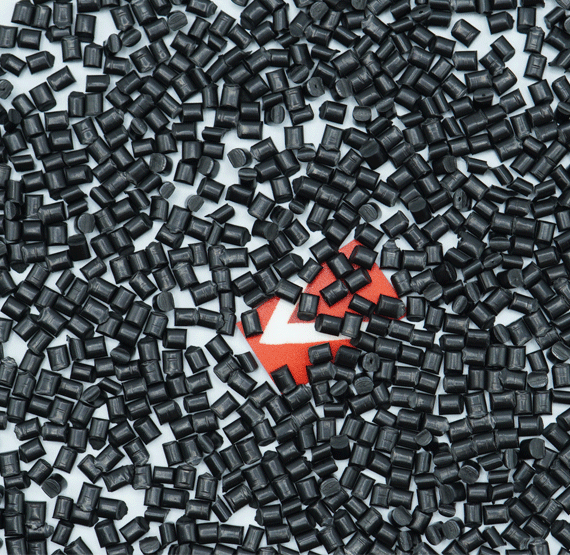
PP conductive compound
In addition to its application in the automotive industry, PP conductive compound is also used to manufacture electronic products, headphone cases, and electronic component pallets.
PP glass fiber compound is a PP engineering plastic compound mixed with reinforced glass fiber and some other additives. Glass fiber is an inorganic filler commonly found in the production of PP plastic compounds for the automotive industry. Compared with other filler materials (such as talcum powder, and CaCO3 powder...), fiberglass has the advantage of cost optimization and enhanced properties:
- Increasing product hardness
- Reducing product shrinkage
- Strengthening the PP plastic base
- Increasing product heat resistance
- Good impact resistance
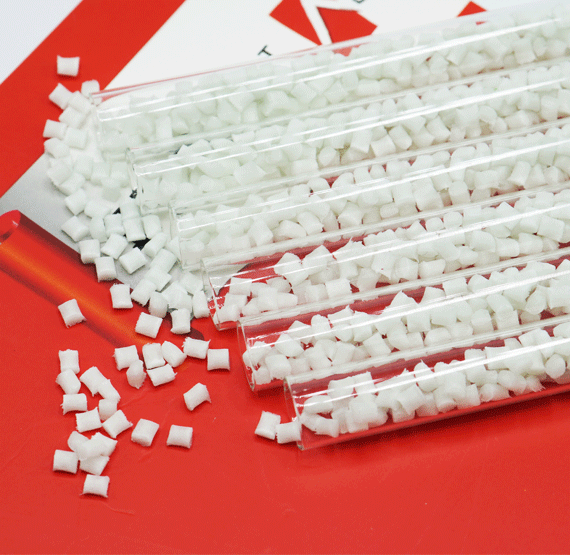
PP glass fiber compound
This product is widely used in injection molding of automotive parts. One note when choosing PP glass fiber compound products is that glass fibers are very fragile during injection molding, affecting the hardness of the finished product. Therefore, it is essential to choose a supplier with extensive experience in the design of fiberglass-reinforced compound products.
Applications of PP glass fiber compound can be mentioned as front-end modules, back door panels, and door interior panels.
In addition to carbon black and fiberglass, glass beads are also an ingredient that can be added to compound PP in automobile manufacturing. Glass beads are transparent, spherical in shape, have compression resistance, and have high thermal stability. In addition, it also improves the mechanical stress under load. With these advantages, PP engineering plastic compound reinforced with glass beads is an optimal choice for cost and quality in automotive manufacturing.
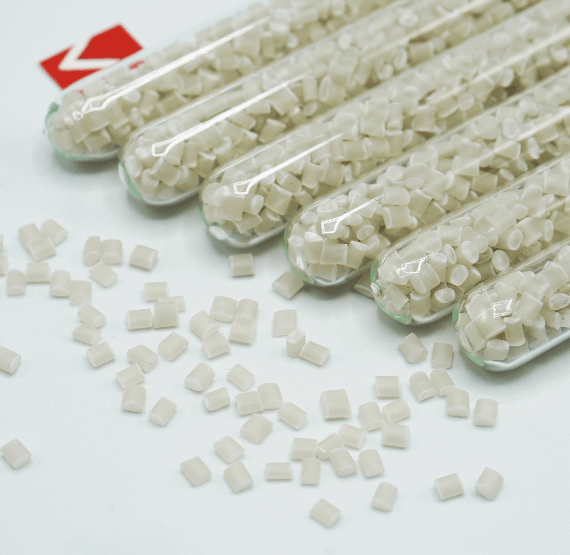
PP glass bead compound
Since the birth of the plastic filler concept, talc powder has always been the most preferred ingredient for manufacturers. Adding talc powder to the resin compound reduces costs and enhances desired properties. Different proportions of talc powder will give different results to the finished product. You can refer to the table below for examples.
PP talc compound is PP engineering plastic compound reinforced with talc powder. Talc powder added to the PP resin compound can potentially be a filler that changes some properties of the mixture. It helps increase some properties of end-products like stiffness, flexural modulus, impact strengths, surface hardness, and electrical conductivity.
Talc function
|
Examples
|
Improvement in rigidity
|
20% of talc in homopolymer PP doubles elastic modulus
|
Increase in tensile strength
|
40% of talc in polyamide 6 improves tensile strength by 25%
|
Nucleating effect
|
500 ppm of fine talc in semi-crystalline polymers significantly increases the crystallization temperature
|
Reduction of Shrinkage
|
20% filling in polypropylene lowers molding shrinkage by 30÷40%
|
Improvement of thermal properties
|
40% of talc in Polyamide 66 almost triples HDT value
|
Improvement of dimensional stability
|
Talc filling provides a certain equalization between cross molding shrinkages, improving the overall dimensional stability and minimizing warpage effect.
|
Lower permeability
|
20% loading in polypropylene increases by 50% moisture barrier
|
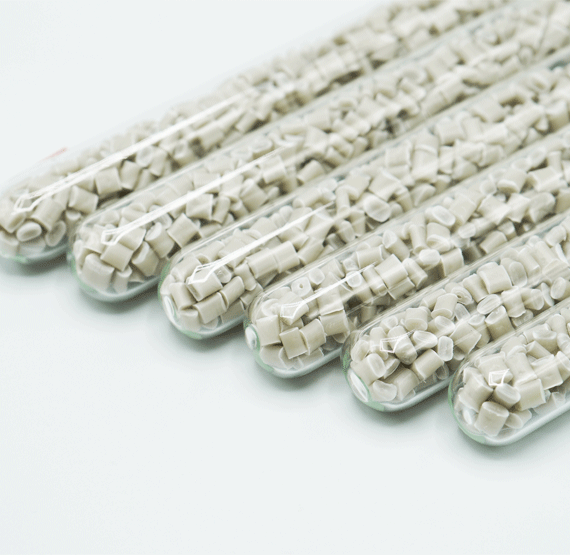
PP talc compound
PP talc compound is applied in manufacturing automotive parts including
- Interiors: instrument panels, door panels, armrests, pillar covers, consoles, seat backs, headliners, and mirror housings
- Exteriors: bumper fascias, rocker panels, and grills
- Under the hood: cooling fans, the housing of headlights and wheel arc liners
PP BaSO4 is made from PP resin, BaSO4 salt, and other additives. BaSO4 is the perfect solution to enhance the density of PP. PP BaSO4 compound increases the glossiness of end-products, creates good shape formation, and decreases shrinkage and heat-induced warping.
In the automotive industry, the PP BaSO4 compound is used to produce sound insulation parts. It helps prevent engine noise from reaching the interior of the vehicle.
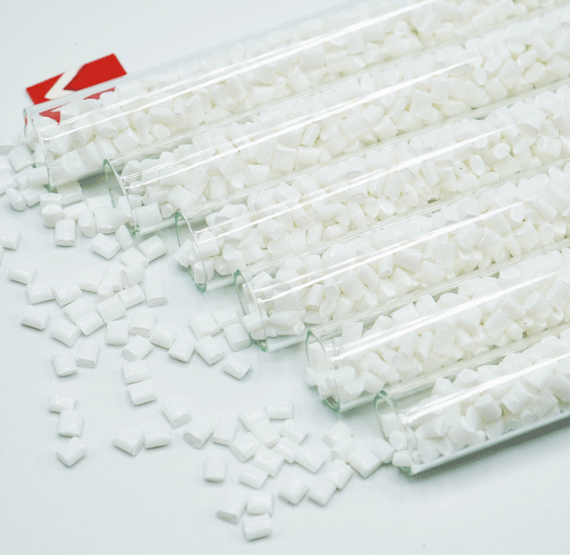
PP BaSO4 compound
PP flame retardant compound consists of PP resin and flame retardant additives. Adding halogen/halogen-free additives makes PP compound less flammable, with high performance and more desired mechanical properties.
This compound is used in the automotive industry for producing automotive parts that require high anti-flammability like battery pack covers.
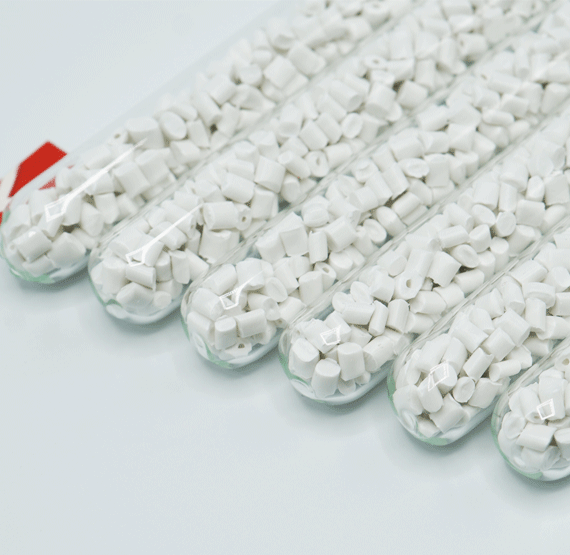
PP flame retardant
3. EuroPlas - a reliable polypropylene compound provider
EuroPlas is the leading manufacturer of plastic materials in Vietnam, trusted and selected by more than 85 customers worldwide. We provide automotive engineering plastic compound products with outstanding features, saving time and costs. The PP compound under intense investigation by EuroPlas has the following advantages:
- Bring desired properties to the finished product such as increased hardness, increased heat resistance, and increased impact resistance, ...
- Bring the full features of the finished product in a single input material
- Can directly process finished products without mixing any other materials
- Easy to process
- Specialized design according to finished product characteristics
Contact us for more information and free sample!