Injection molding is an economical process of producing various kinds of plastic products through the use of molds. However, one must carefully select the type of plastic material that should be used since the costs of the final products depend on the plastic material used. In this article, we will zoom into 7 low cost plastics that are frequently used within an injection molding process.
1. Overview Of Injection Molding
One of the most common manufacturing processes is injection molding, in which the material, typically polymer, under high pressure, is injected into a mold before it solidifies to the shape of the mold. This process is particularly appreciated for its precision but also for its quickness because It has the capability to produce outstanding shapes and patterns. This process is widely used across such industries as automotive, electronics, home appliances, packaging, and consumer goods industries.
The key features and benefits of injection molding include:
- Possibility to manufacture a great number of similar and identical parts with a high rate of effectiveness.
- Capability of making thin edges or fine lines and shapes and forms.
- Good dimensional stability and close tolerance of the individual part and parts within the set.
- Versatility in working with a host of thermoplastic and thermoset type of materials
- A characteristic where an item has the ability to make individual parts using different molds as production proceeds.
Read more: What is injection molding? How does it work?
2. Seven Low Cost Plastics For Injection Molding
As with many molding technologies, the type of plastic material used considerably impacts the overall value of the final product in injection molding. However, there are several generic low cost plastic materials available with a wide spectrum of properties and functions suitable for different applications across different sectors.
Read more: Plastic injection molding cost
7 Low cost plastic for Injection molding |
Price per pound |
Polypropylene (PP) |
$0.90 |
Polystyrene (PS) |
$1.00 |
Polyethylene (PE) |
$1.20 |
Acrylonitrile Butadiene Styrene (ABS) |
$1.30 |
Nylon (PA) |
$2.20 |
Polyoxymethylene (POM) |
$2.20 |
Polycarbonate (PC) |
$2.30 |
For more details about these low cost plastics for injection molding, let’s read the below content.
2.1. Polypropylene (PP)
Polypropylene is a low cost plastic material that can be effectively used in injection mold processes. Its properties have mechanical, thermal, and chemical applications which makes it ideal for a broad range of products. Polypropylene injection molding is widely utilized to manufacture household products, automotive components, and packaging elements.
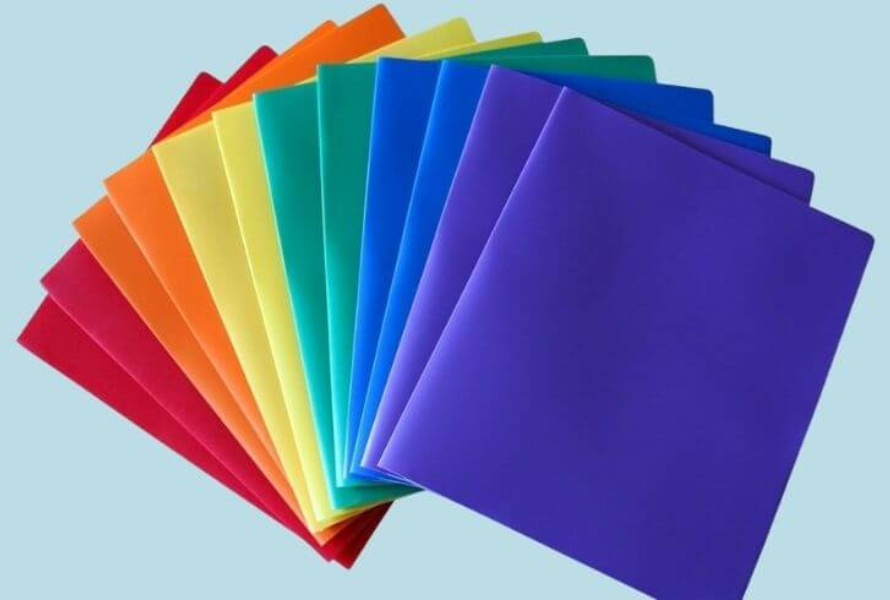
Polypropylene is a low cost plastic material that is widely used in injection molding applications.
2.2. Polystyrene (PS)
Polystyrene is one of the low cost plastics and much easier materials in injection molding. In this regard, the product presents adequate fire resistance, good insulation functions, and aesthetic looks, a proper material selection for the undertaking. This low cost plastic is common in the manufacture of disposable cups and plates, shed and carrier materials, and toy parts.
2.3. Polyethylene (PE)
Polyethylene is a commonly low cost plastic in injection molding. It is relatively cheaper, easily gotten from the market and mostly used in the injection molding process. Different types of polyethylene are LDPE, HDPE, LLDPE and each has its own characteristics and uses.
This low cost plastic is widely applied for the production of packing material, barrels, pipes, toys, and many other things because of its good chemical stability, impact strength, and easy processability.
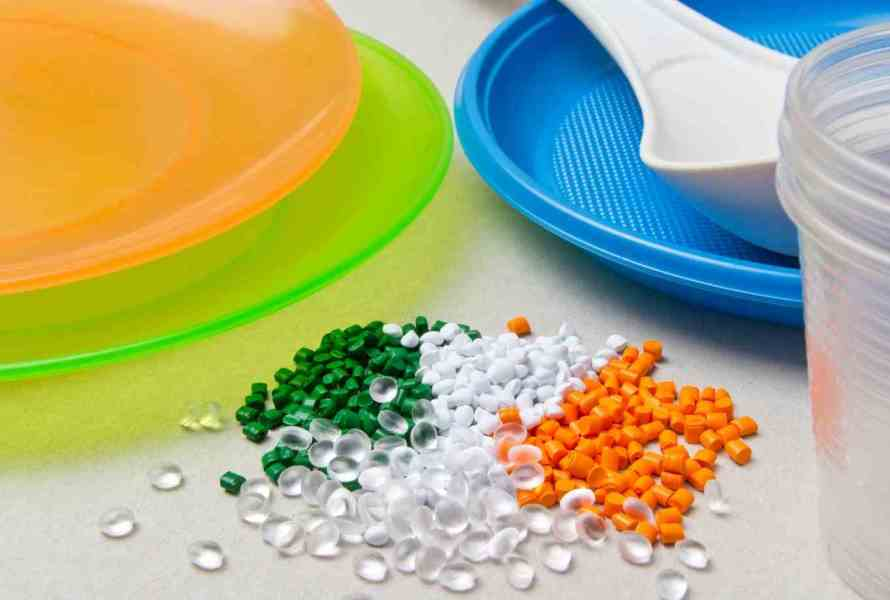
Polyethylene is relatively cheaper and easily accessible and thus is one of the most low cost plastics frequently used in injection molding.
2.4. Acrylonitrile Butadiene Styrene (ABS)
Acrylonitrile Butadiene Styrene (ABS) is one of the low cost plastics on the market. One of the properties of ABS is its ease of molding and its toughness and therefore it is frequently utilized in the injection molding processes. Injection molding products made from this low cost plastic include application enclosures, household items, and automobile components.
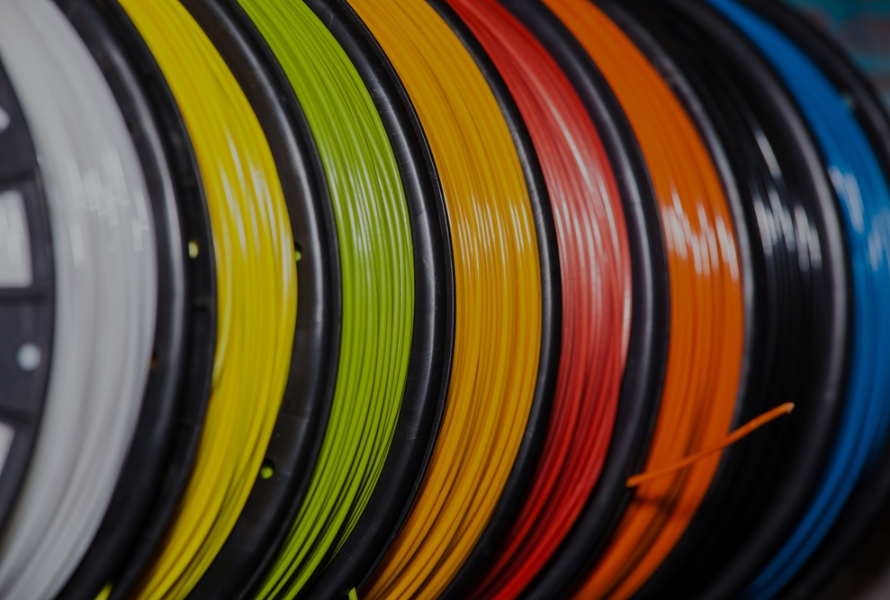
ABS is one low cost plastic, which is widely chosen for injection molding applications.
2.5. Nylon (PA)
Polyamide or more commonly called nylon, is a low cost plastic with fairly good mechanical characteristics, and good abrasion resistance. Thus, nylon is relatively cheaper in cost to qualify it to be used in injection molding. This low cost plastic is widely utilized for the production of automotive and electrical parts, and as a material in producing sports articles.
2.6. Polyoxymethylene (POM)
Polyoxymethylene or POM is a low cost plastic mostly valued for its stable dimensions, durability, and low friction. These characteristics make it possible to manufacture highly complicated and accurate products such as gears, bearings, and mechanical parts. This low cost plastic’s chemical resistance and thermal stability also play a significant role across several industries.
2.7. Polycarbonate (PC)
Polycarbonate is another low cost plastic used in injection molding. Thanks to its highly transparent, very resistant to impacts, and dimensionally stable, this material has found use in areas related to lenses, shields,... This low cost plastic’s high-temperature endurance and nonflammability add to the application versatility of the material.
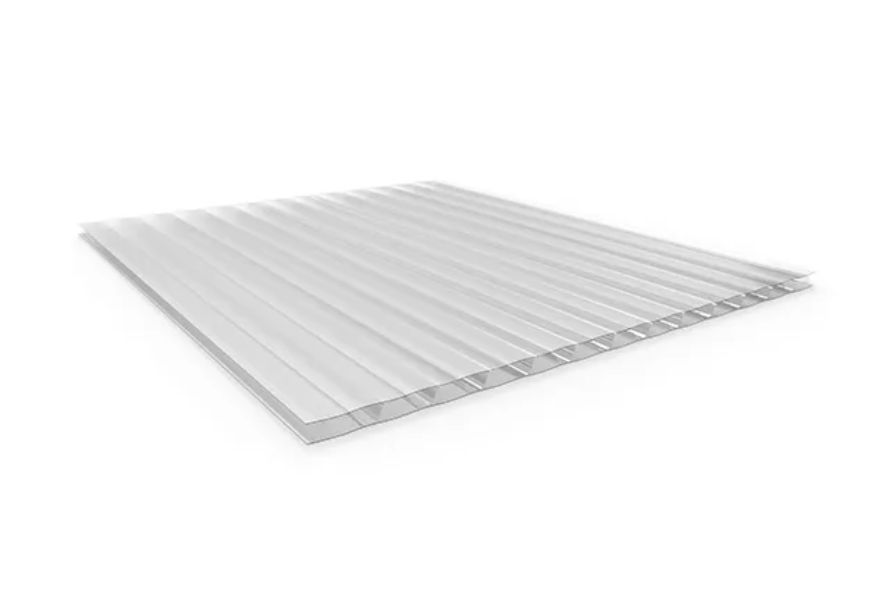
Another low cost plastic that is exceedingly transparent, impact-resistant, and dimensionally stable is polycarbonate.
3. Conclusion
To optimize the production cost of plastic materials across various industries, the selection of cost effective and suitable plastic types is crucial. The following seven low-cost plastics are options that manufacturers can consider:
- Polypropylene (PP)
- Polystyrene (PS)
- Polyethylene (PE)
- Acrylonitrile Butadiene Styrene (ABS)
- Nylon (PA)
- Polyoxymethylene (POM)
- Polycarbonate (PC)
4. About EuroPlas
Being one of the key suppliers of plastics to clients, EuroPlas takes pride in delivering a range of plastics products that have high quality, meet the new and changing needs of the markets. If you are sourcing for low cost plastic that could be used in injection molding, then EuroPlas is a station that you can consult.
4.1. Polypropylene (PP)
EuroPlas’s PP products include:
4.2. ABS
EuroPlas’s ABS products include:
4.3. Polycarbonate (PC)
EuroPlas’s PC products include:
For more detail about our products, please contact us right now or visit our blog for more information about the plastic industry.