In the realm of engineering, high-performance plastics stand out as essential materials, renowned for their remarkable strength and durability. Their unique properties, including thermal stability and exceptional chemical resistance, make them indispensable in demanding environments. This blog post delves into the intricate compatibility of various high-performance plastics with a range of common chemicals, from solvents to acids. By understanding these interactions, engineers can make informed decisions, ensuring the longevity and reliability of their applications.
Read more: The Ultimate Guide to High Performance Plastics
1. Overview of High Performance Plastic
In the dynamic landscape of modern industry, high-performance plastics emerge as indispensable materials, embodying the essence of superior quality and efficiency. Designed to operate at temperatures exceeding 302°F, these advanced polymers offer an impressive array of properties, including exceptional chemical resistance, lightweight characteristics, and remarkable sliding friction capabilities. Their versatility is further enhanced through the incorporation of specialized reinforcing agents such as glass fiber, glass beads, and carbon fiber, which significantly bolster heat distortion resistance and rigidity.
Moreover, the strategic use of additives like PTFE and graphite elevates their sliding and friction performance, while the integration of metal fibers and carbon black enhances electrical conductivity. This unique combination of attributes ensures that high-performance plastics not only meet but exceed the demands of various engineering applications, delivering optimal performance with minimal maintenance. As industries strive for the best cost-to-performance ratio, these materials stand at the forefront, ready to revolutionize the way we approach design and functionality.
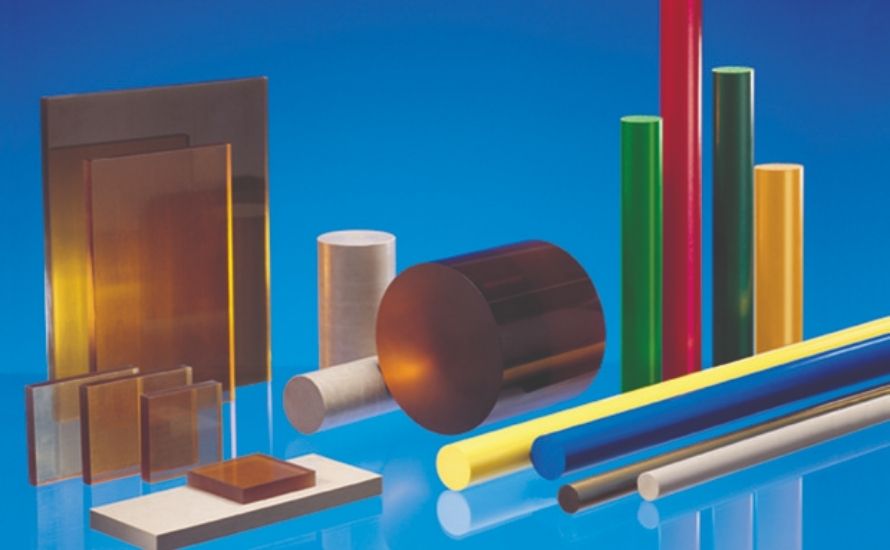
2. Types of High-Performance Plastics with Superior Chemical Resistance
In this section, we will explore the different types of high-performance plastics that offer superior chemical resistance, highlighting their unique properties and applications.
2.1 Polytetrafluoroethylene (PTFE)
Polytetrafluoroethylene, widely recognized by its trademark Teflon, is a remarkable low-friction fluoropolymer celebrated for its unique combination of softness and formability. This exceptional material gracefully adapts to complex shapes, bending rather than breaking under stress, which enhances its versatility in various applications. With unparalleled chemical resistance and outstanding weathering properties, PTFE proves indispensable for components that must endure harsh environments while maintaining flexibility during and after production.
Its impressive thermal stability, remaining steadfast up to 260°C (500°F), makes it a preferred choice for coating cookware and ensuring non-stick surfaces. Additionally, PTFE serves as an effective electrical insulator, finding applications in semiconductor manufacturing and diverse components such as chemical-resistant tubing, scientific instruments, manifolds, valves, and precision bearings.
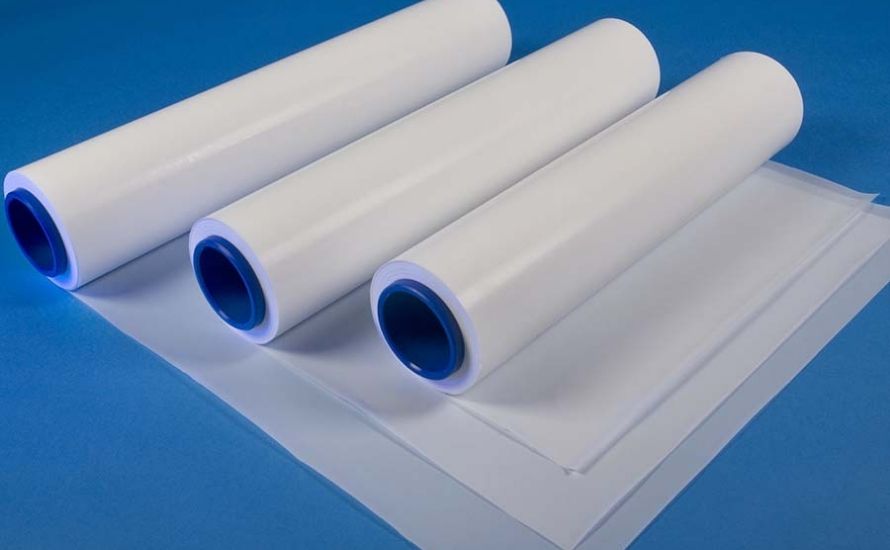
2.2 Polyetheretherketone (PEEK)
Polyetheretherketone (PEEK) stands out as a premier high-performance plastic, renowned for its exceptional resistance to aggressive chemicals, fresh and saltwater, as well as steam. This advanced material retains remarkable stiffness at elevated temperatures, making it suitable for continuous operation up to 170°C (338°F). PEEK's ability to emit low smoke and minimal toxic fumes under flame exposure further enhances its appeal for high-temperature applications.
Beyond its impressive mechanical strength and dimensional stability, PEEK is easily manufacturable, allowing for the creation of intricate shapes in various forms, including sheets, rods, and tubes. Its versatility extends across numerous industries, finding applications in oil and food storage, aerospace components, medical instruments, and even semiconductor machinery, where it serves as a reliable electrical connector. With its unique blend of properties, PEEK is truly a game-changer in the realm of engineering materials.
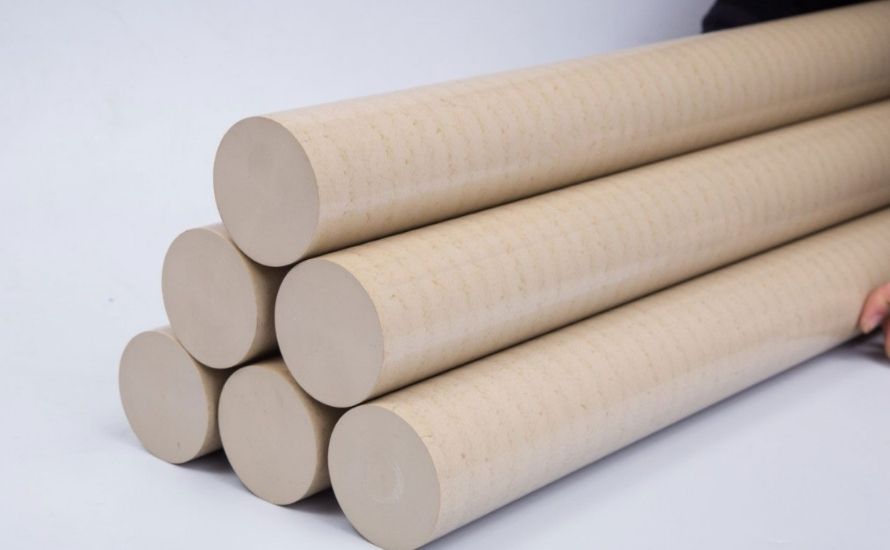
Read more: PEEK plastic: Definition and Application
2.3 Polyvinyl Chloride (PVC)
Polyvinyl Chloride (PVC) is a remarkably strong and rigid plastic, yet it remains highly adaptable for fabrication, bonding seamlessly with adhesives and solvents. Its excellent joining capabilities make PVC an ideal choice for constructing fittings and valves, while its cost-effectiveness appeals to engineers undertaking large-scale projects such as chemical tanks, manifolds, and piping systems.
Beyond industrial applications, PVC provides durability and protection in cabinetry and workspaces, ensuring resilience without the risk of cracking. Available in a spectrum of colors and grades, this versatile material offers designers significant creative flexibility. However, caution is warranted during injection molding, as PVC emits toxic and corrosive gases when melted, limiting its processing to specialized facilities.
2.4 High-Density Polyethylene (HDPE)
High-Density Polyethylene (
HDPE) is a versatile thermoplastic renowned for its excellent chemical and corrosion resistance. With minimal moisture absorption, HDPE effectively safeguards components from chemical infiltration, enhancing their longevity. Despite its impressive stiffness and strength, this lightweight material is easy to fabricate, accommodating various applications through thermoplastic welding techniques.
Its remarkable ability to repel acids, bases, alcohols, and even graffiti makes HDPE a preferred choice for public infrastructure, playgrounds, and military constructions. Available in sheets or rods, HDPE comes in a variety of grades, colors, and textures, including woodgrain and UV-stabilized finishes, offering designers ample creative possibilities.
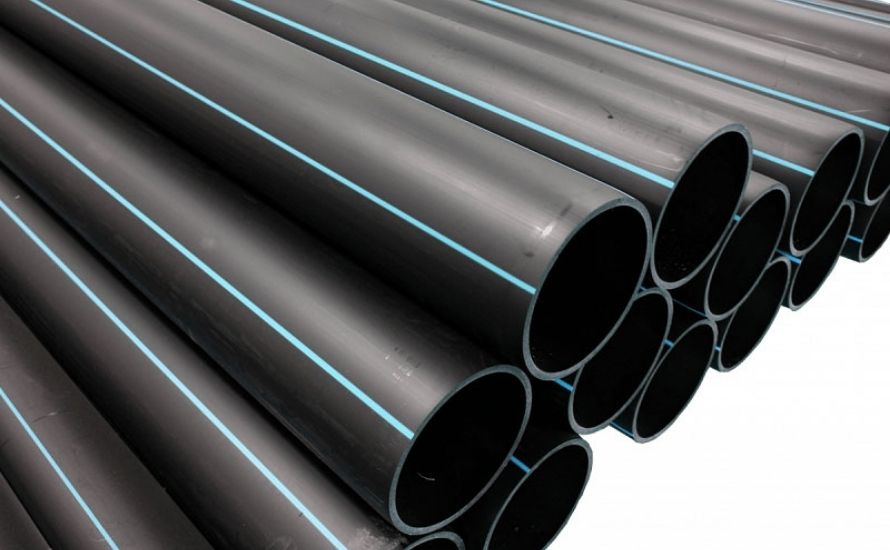
2.5 Polypropylene (PP)
Polypropylene (PP) emerges as a cost-effective polymer distinguished by its remarkable resistance to stress cracking and chemicals, enhancing its durability in challenging environments. This inherent anti-cracking property significantly bolsters its chemical resilience, allowing PP to maintain integrity under duress. With exceptional formability, polypropylene is easily welded and decorated, striking a balance between rigidity and versatility.
While its melting point of 120°C (248°F) is lower than that of some competing materials, PP continues to excel in various applications, including body jackets and outer prosthetic sockets, as well as roofing and hurricane panels. Additionally, its durability makes it a favored choice for outdoor equipment such as terraces, patios, and playground fixtures, ensuring long-lasting performance in diverse settings.
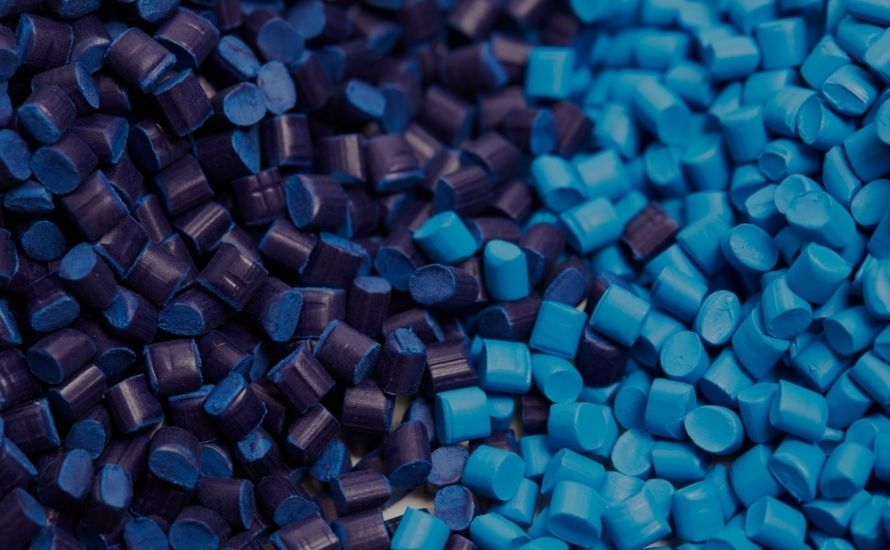
Read more: Why PP Melting Point Is Important In Creating Products
3. How to Choose the Right High-Performance Plastic for Your Needs
Selecting the ideal high-performance plastic is pivotal for the success of your project, whether it involves construction, product design, or packaging. Here are essential guidelines to help you navigate the selection process with confidence and precision:
- Identify Essential Properties for Your Application: Start by assessing the specific requirements of your application, as the performance of high-performance polymers depends on their properties. For thermal stability, PEEK is a top choice due to its strength and heat resistance. For biocompatibility, consider PSU or PPSU, which are ideal for medical environments thanks to their mechanical strength and sterilization resistance.
- Consider Chemical Resistance and Electrical Properties: The chemical milieu in which your product will operate is critical to polymer selection. PDVF, with its remarkable chemical resistance and dielectric properties, stands out as an ideal candidate for electrical applications and environments prone to chemical exposure. Similarly, PTFE’s unparalleled resistance to corrosive substances, coupled with its thermal stability, makes it a staple in both the food and pharmaceutical industries, ensuring safety and reliability in sensitive applications.
- Evaluate Budget Constraints: While high-performance polymers often come with a premium price tag due to their advanced manufacturing processes and superior qualities, budget considerations should not be overlooked. Fortunately, polymers such as PEI offer an excellent balance of affordability and performance. Its ease of machining and fabrication can significantly reduce costs without compromising on the desirable attributes expected from high-performance materials, making it a savvy choice for cost-conscious projects.
- Understand Regulatory Compliance Requirements: Navigating the labyrinth of regulatory requirements is essential, particularly in highly technical industries. Familiarize yourself with the specific certifications your application must meet, such as FDA compliance for food and pharmaceutical uses or ISO standards for medical applications. Polymers like PEEK and PDVF are often favored for their ability to meet stringent industry regulations, ensuring that your product not only performs well but also adheres to necessary safety standards.
- Consult Industry Standards and Certifications: It’s wise to consult industry standards relevant to your application. Polymers like PPS and PEI are designed to meet the demands of sectors such as aerospace and oil and gas, ensuring your material choices align with best practices. Collaborating with knowledgeable.
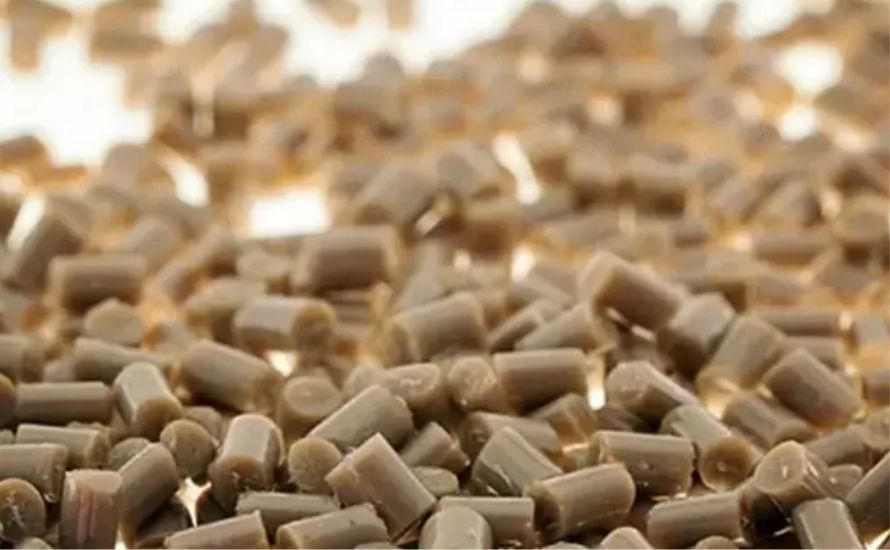
4. Conclusion
In summary, high-performance plastics epitomize advanced material science, delivering exceptional resilience and versatility for demanding applications across industries like aerospace, automotive, and healthcare. Their superior chemical resistance and lightweight durability render them indispensable, yet challenges such as high costs and environmental concerns persist. Engineers and scientists must adeptly navigate this complex landscape to select the most suitable materials, fostering innovation and sustainability. Ultimately, informed choices in high-performance plastics can drive significant advancements in technology and industry.
5. About Engineering plastic compound of EuroPlas
EuroPlas stands at the forefront of the plastic materials industry, offering an extensive array of products, including bioplastic compounds, color masterbatches, plastic additives, and engineering plastic compounds. With over 17 years of expertise, we are the world's leading manufacturer of filler masterbatch, boasting six state-of-the-art facilities and an impressive annual capacity of 0.8 million tons. Our commitment to innovation ensures that each solution is meticulously tailored to meet the unique needs of our clients across diverse sectors such as aerospace, automotive, healthcare, electronics, and energy. Leveraging our distinct natural resource advantage, we provide affordable and eco-friendly materials without compromising quality.
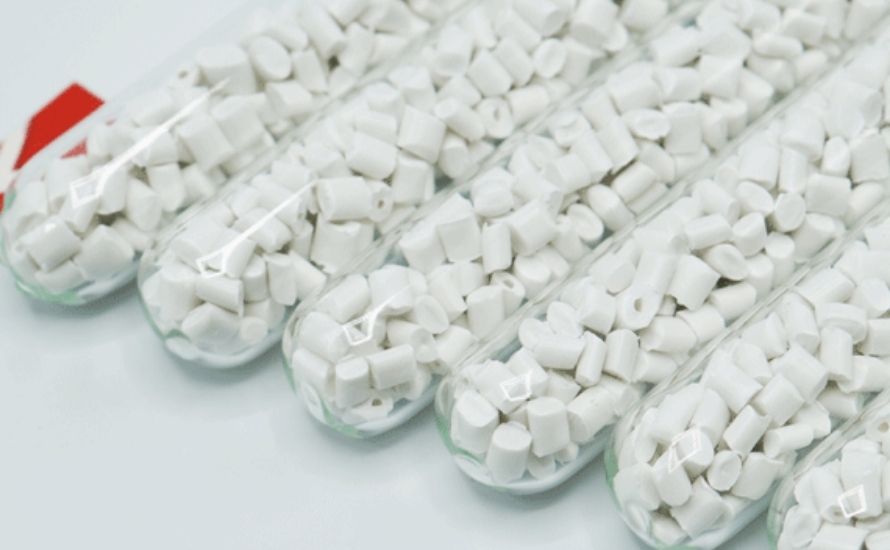
For more detailed information about our engineering plastic compounds, please
contact us.