It is crucial to know the PP melting point, especially for manufacturers that want to produce great polypropylene products. In this article, we’ll explore the importance of PP melting point and how it affects the functionality of polypropylene heat resistance in products used in different applications.
1. Understanding The Definition Of PP
Polypropylene (PP) is a type of thermoplastic polymer that is particularly appreciated for its flexibility and resistance. PP is utilized in the production of packaging materials, automotive parts, textiles, and consumer products owing to properties such as lightweight, heat resistance, and chemical resistance.
The PP melting point is usually within the range of 160-170 centigrade, which is equivalent to 320-338 Fahrenheit. This melting point is essential in understanding how polypropylene will respond to heat and how this response affects its performance across multiple uses.
Read more: PP Plastic: Everything you need to know
Read more: Is PP Plastic safe?
Read more: PP Melting Point: Discover Polypropylene's Temperature Ranges
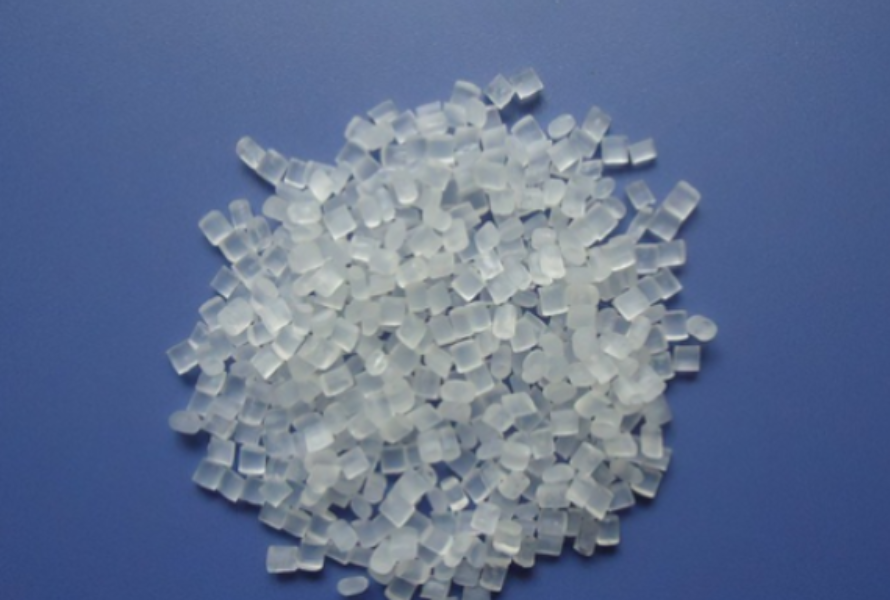
PP melting point is commonly 160°C-170°C.
2. Reasons Why PP Melting Point Is Important In Creating Products
2.1. Consistency in Molding and Shaping
The PP melting point has a vital role in determining the quality and uniformity of the final molded or shaped products.
Polypropylene has a specific melting temperature at which it can be easily shaped and this is very important when it is to undergo manufacturing processes such as injection molding and blow molding.
Stable polypropylene temperature range ensures that the products have to undergo the same temperature conditions thereby improving chances of minimizing defects and also ensuring that each of the end products is produced to the utmost standard.
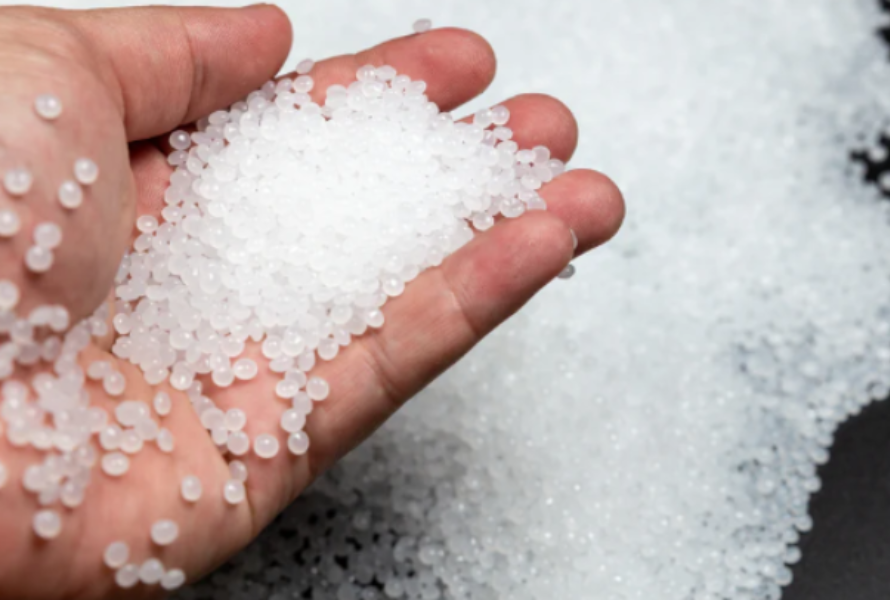
PP melting point has much influence on the quality and homogeneity of final molded or shaped products.
2.2. Impact on Durability and Strength
The PP melting point has a direct impact on the overall strength as well as the durability of the final product.
The polypropylene maximum temperature that a product can withstand without compromising its integrity is determined by how well the material is processed around its melting point.
Polypropylene when appropriately processed, and exposed to an ideal melting point shows improvements in mechanical strength essential in the demand application.
This relationship assists manufacturers in understanding whether their products will be capable of withstanding stress, impacts, or environmental conditions.
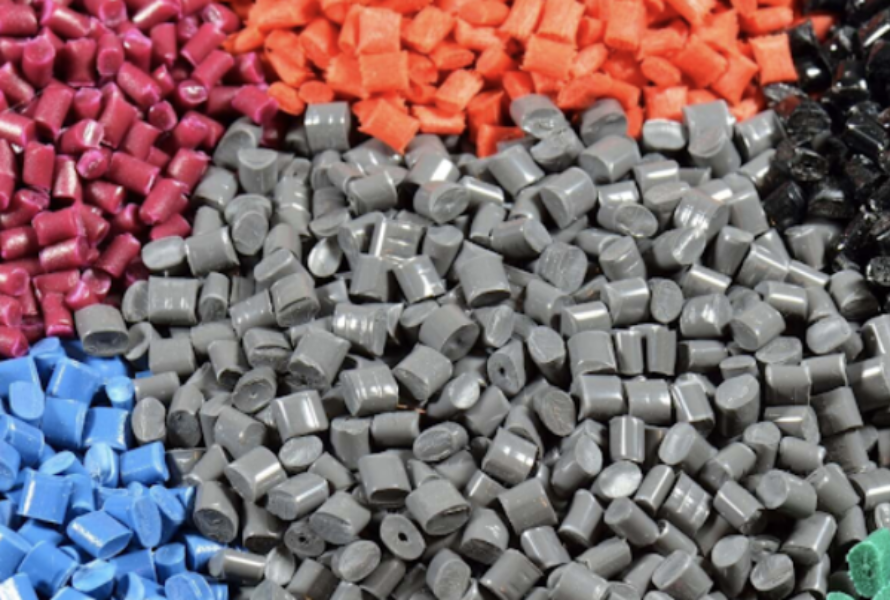
The final product's durability and overall strength are directly influenced by the PP melting point.
2.3. Suitability for Heat-Sensitive Applications
Products in industries such as automotive and packing often undergo high temperatures. Selecting the appropriate polypropylene grade available with a high melting point, which also possesses polypropylene heat resistance helps to ensure that the material remains functional and stable when exposed to heat.
Once the polypropylene temperature range is defined, manufacturers can eliminate thermal degradation that results in loss of strength and flexibility. This is important for safety-related applications like implanted medical devices and electrical housing.
Moreover, understanding the PP melting point is useful for product design. To achieve this, manufacturers can develop components that will prevent exposure to heat while the chosen polypropylene retains functionality. Exploring the polypropylene temperature range, one would be able to design products that meet specifications and compliance where heat is a paramount factor.
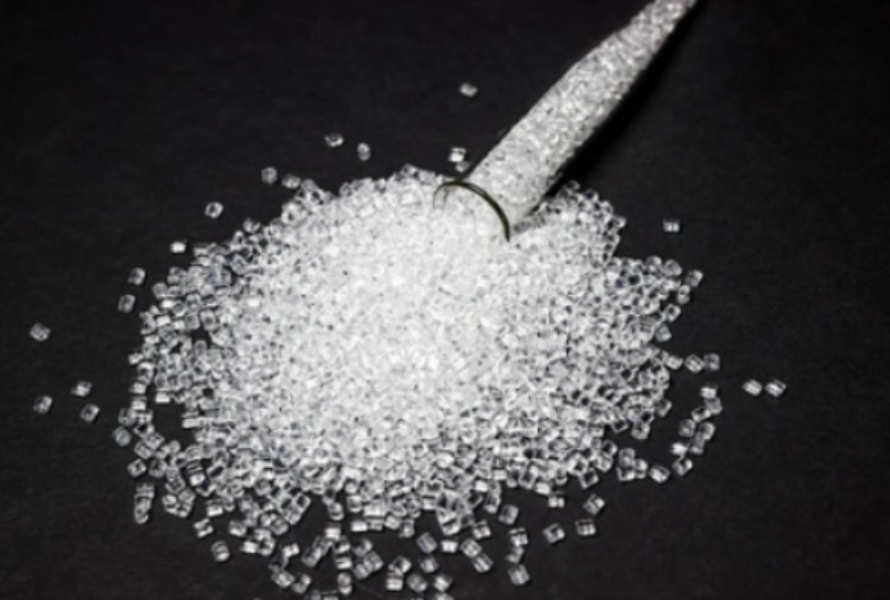
Understanding the melting point of PP is important for applications involving heat-sensitive objects.
2.4. Efficient Processing and Production
The polypropylene temperature range shows the specific thermal conditions which must be used in order to mold and shape polypropylene.
When the PP melting point is correctly measured and regulated, it enables a proper flow from one step to another of the processing procedure since overheating the material is a real possibility as is underheating it. This control is vital to enable uniform melting and reduce material losses and defects that may arise from the manufacturing process.
For instance, in injection molding, the polypropylene maximum temperature allows it to fill molds and cover every gap without trapping gases or forming vacuums.
Also, if the polypropylene heat resistance used is enhanced during the manufacturing process it is possible to experience short cycle times. When the material gets to its melting point more efficiently, the total time required for production is shortened, thus manufacturing a higher number of items in the same duration. This direct increase in throughput can be most effective in markets, where the rate of goods being manufactured is very important.
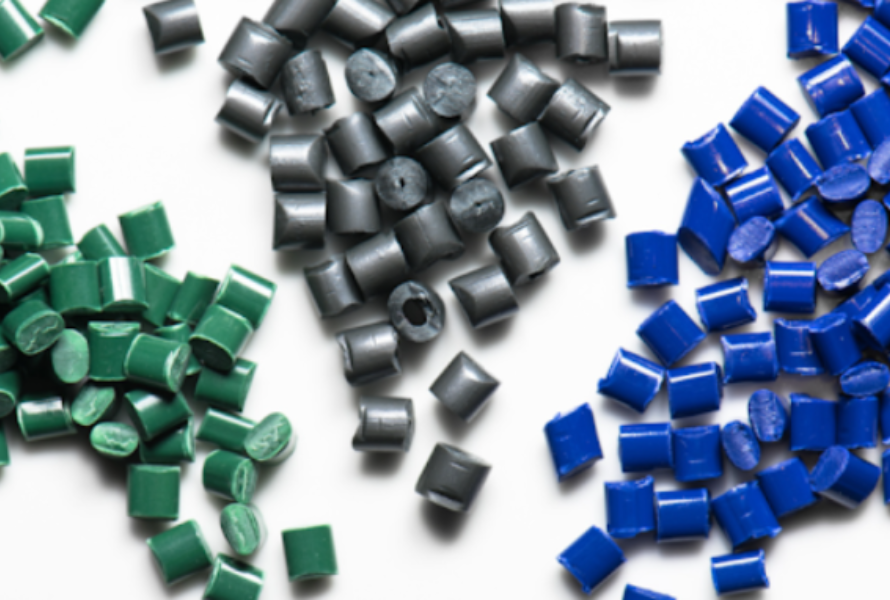
Understanding the PP melting point helps manufacturers gain efficient production.
2.5. Avoiding Thermal Degradation
Over PP melting point results in thermal degradation and tends to bring about a degradation of the material in use.
Above the melting point too much, polypropylene is likely to degrade chemically, leading to discoloration, strength reduction and brittleness if exposed for long.
Knowing the PP melting point enables manufacturers to develop the right processing parameters which should not exceed this limit since excessive heat can affect the physical and chemical properties of the final products.
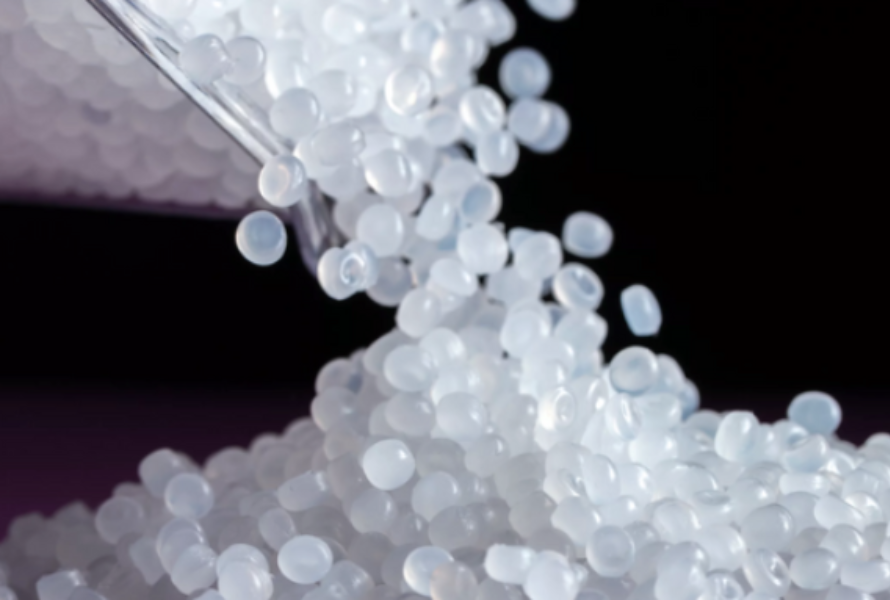
Knowledge of the PP melting point helps producers develop an ideal condition for processing.
3. Conclusion
The PP melting point is a vital consideration in the manufacturing of polypropylene products. Its influence on molding consistency, durability, suitability for heat-sensitive applications, and processing efficiency makes it essential for producing high-quality, reliable products.
4. About EuroPlas’ PP Products
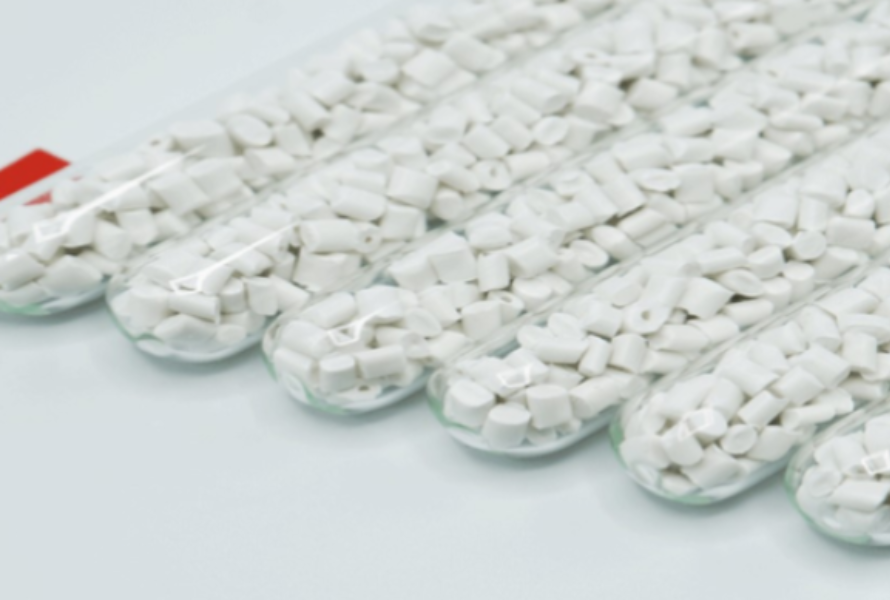
At EuroPlas, we stand ready for customers' different demands with a series of high-quality PP products.
Our polypropylene materials have been engineered with excellent heat resistance and toughness to provide the best performance in various applications. EuroPlas’s PP products include:
Contact us for details and support for your needs!