Polypropylene (PP) is one of the most widely used plastics globally, favored for its excellent balance of strength, flexibility, and chemical resistance. This article introduces the concept of the PP melting point, explaining its significance for manufacturing, processing, and product durability. One key property that defines its performance in different applications is the PP melting point. Understanding the melting behavior of polypropylene is crucial for manufacturers, engineers, and designers who rely on its consistent performance.
Read more: Temperature ranges for different plastic materials
1. Understanding Polypropylene (PP)
Polypropylene is a versatile, synthetic plastic that falls within the thermoplastic category. Composed of repeated units of individual propylene monomers joined by a chemical process, polypropylene is a large molecular compound.
The material exhibits superior molecular crystallinity, flexibility, physical toughness, chemical tolerance, and temperature resistance compared to other polymers. It can be liquified for production and recycling since it softens at temperatures close to the melting point. Products made of polypropylene are frequently branded with the #5 resin code and symbol, suggesting that they can be recycled.
Read more:
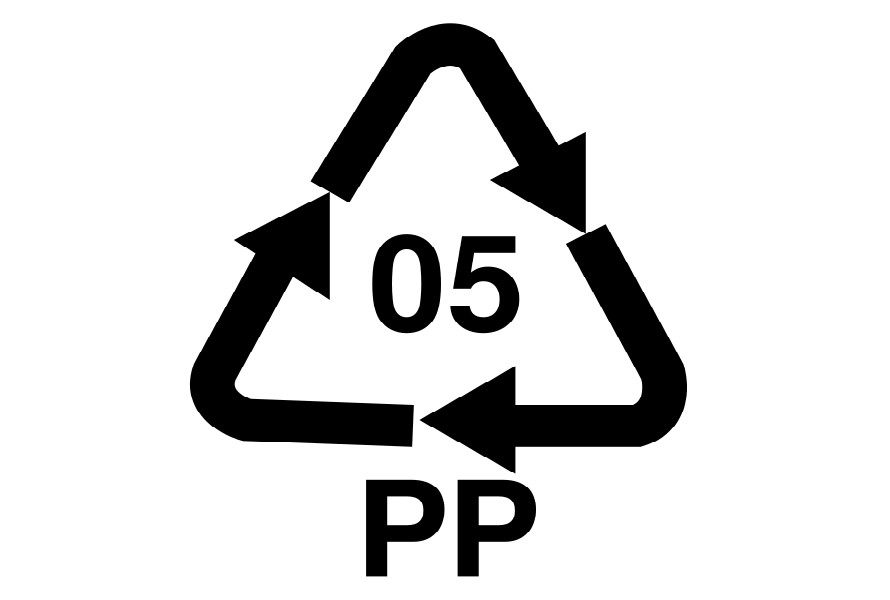
The concept of the PP melting point
2. What is PP Melting Point?
PP melting point ranges from 160°C to 170°C (320°F to 338°F). Isotactic PP has a higher melting point than atactic PP. It's because the former has a regular molecular structure, while the latter features a more disordered molecular arrangement.
3. Why PP Melting Point Matters?
The significance of the PP melting point extends across several critical aspects of manufacturing and product design.
First, during manufacturing processes like injection molding and extrusion, knowing the exact melting point is vital. Polypropylene must reach the appropriate temperature to melt properly, flow evenly into molds, and cool down without introducing internal stresses. If the temperature is too low, incomplete filling or structural weaknesses can occur. If it is too high, material degradation and discoloration may result, compromising product quality.
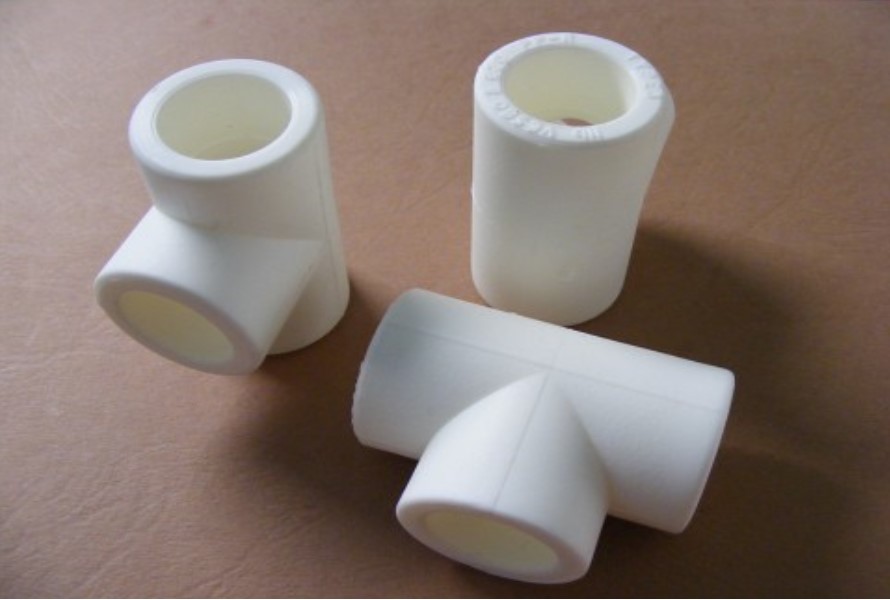
The significance of the PP melting point extends across several critical aspects of manufacturing and product design.
Second, the heat resistance of PP affects its performance in real-world applications. Automotive parts made from polypropylene, for example, must withstand elevated temperatures near engines without deforming. Similarly, food containers and packaging must endure reheating in microwaves without losing their shape or releasing harmful substances. An in-depth understanding of the PP melting point ensures these products perform reliably under intended thermal conditions.
Third, material selection decisions often hinge on melting point considerations. For high-temperature environments, polypropylene may not always be the best choice if even higher thermal stability is required. In such cases, alternatives like PEEK or PPS, known for superior heat resistance, might be selected instead. Nevertheless, for a vast array of moderately high-temperature applications, polypropylene remains a cost-effective and reliable material.
The table below shows how the PP melting point plays a role in various industries:
Automotive parts |
The stability and longevity of parts like door panels, dashboards, and bumpers depend heavily on the melting behavior of polypropylene. It's because these components are subjected to a range of temperatures during vehicle operation. |
Medical devices |
Understanding the PP melting point guarantees the functionality and safety of medical equipment, such as syringes and IV components, since some PP grades have to tolerate high temperatures during the sterilization process. |
Packaging materials |
The integrity of packing materials such as bottles, films, and containers must be maintained during storage, transit, and use, and this is where the PP melting point comes into play. |
Fibers |
PP melting point is important for fiber manufacturers to achieve desirable qualities, such as dimensional stability and strength. |
4. Factors Affecting PP Melting Behavior
Several factors influence the melting behavior of polypropylene, which in turn affect its suitability for different applications.
Crystallinity is a primary factor. A higher degree of crystallinity within the polymer structure results in a higher melting point, providing better heat resistance but sometimes at the expense of toughness and impact resistance. Homopolymers typically exhibit greater crystallinity than copolymers.
Additives also play a role. Manufacturers may introduce fillers like talc or glass fibers, stabilizers, or plasticizers to modify the thermal and mechanical properties of PP. These additives can slightly adjust the melting point, either raising it to enhance heat performance or modifying it to improve processability.
Moreover, processing conditions, particularly post-processing treatments like annealing, influence the final crystalline structure of polypropylene products. Annealing can increase the polymer’s crystallinity and thus raise its effective melting point, improving heat resistance for specific end uses.
5. Comparing PP Melting Point To Other Polymers
PP melting point is quite similar to HDPE. Meanwhile, it's higher than that of LDPE and much lower than PC, PA, and PET. Here's the detailed table:
HDPE |
120-180°C |
LDPE |
105-115°C |
PC |
260-270°C |
PA |
220-260°C |
PET |
250-260°C |
6. Conclusion
The PP melting point is far more than a simple technical detail. It is a cornerstone of polypropylene's versatility and success in a wide range of industries. By mastering the nuances of its melting behavior, manufacturers and engineers can optimize production processes, improve product performance, and ensure long-term durability.
Polypropylene’s balanced properties, coupled with its manageable melting range, make it an indispensable material for sustainable and cost-effective solutions in modern manufacturing. As industries continue innovating, the consistent and predictable behavior of polypropylene, anchored by its melting point, will remain a critical asset for developing next-generation products.
7. About EuroPlas’ PP Products
EuroPlas has a list of engineering plastic compounds blending PP resins with additives and reinforcements to enhance the properties of the final product. The perfect combinations create a single material with all functions in one, making the production process easier and faster. Thus, our customers can improve their productivity.
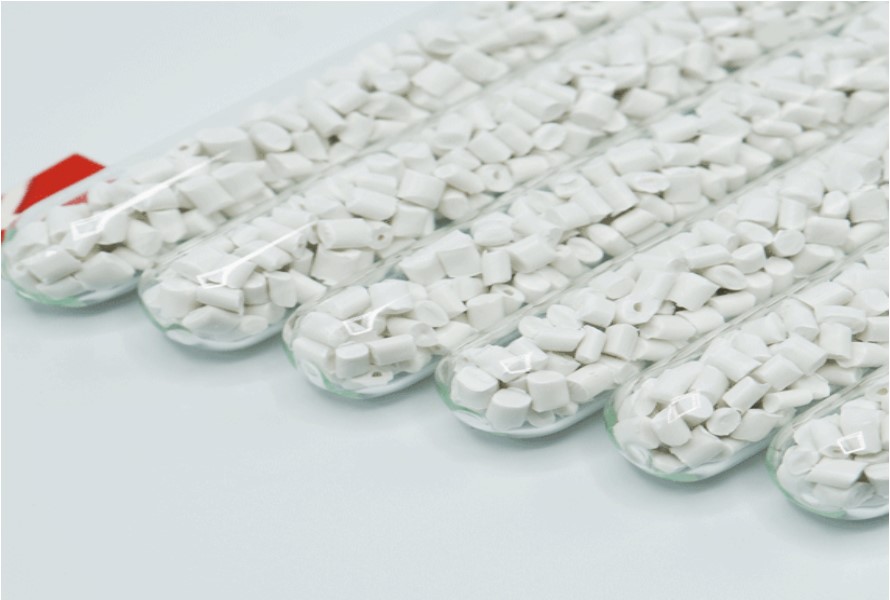
Here’s the list of our PP compound and the suggested applications:
- PP glass fiber compound: You can use it for car doors, kettle handles, rice cooker covers, etc.
- PP glass bead compound: It's suitable for home appliances, interior, and automotive decoration.
- PP talc compound: Outdoor equipment, motorcycles, and car interiors are common applications.
- PP BaSO4 compound: It's ideal for sanitary ware, water purifiers, vacuum cleaners, rice cookers, etc.
- PP conductive compound: You can use it for household appliances, pumps, pipes, ESD film, etc.
- PP flame retardant compound: It has better flame retardancy, which is ideal for household electrical and electronic equipment.
Contact us now for more details!