Plastic materials have become an integral part of our daily lives, being used in a wide range of applications, from packaging and construction to automotive and electronics. One essential property to consider when working with plastics is their melting temperature. Knowing the temperature at which a plastic material melts helps determine its processing capabilities and suitability for specific applications. In this article, EuroPlas will delve into the melting temperature ranges of various plastic materials commonly used across industries.
Read more: What is plastic? Everything you need to know about plastic
1. What is the melting point of plastic?
The melting point of plastic is the temperature at which a solid plastic material transitions from its solid state to a liquid state. At this temperature, the intermolecular forces holding the plastic's polymer chains together weaken, allowing them to move more freely. As a result, the plastic softens and eventually turns into a liquid form.
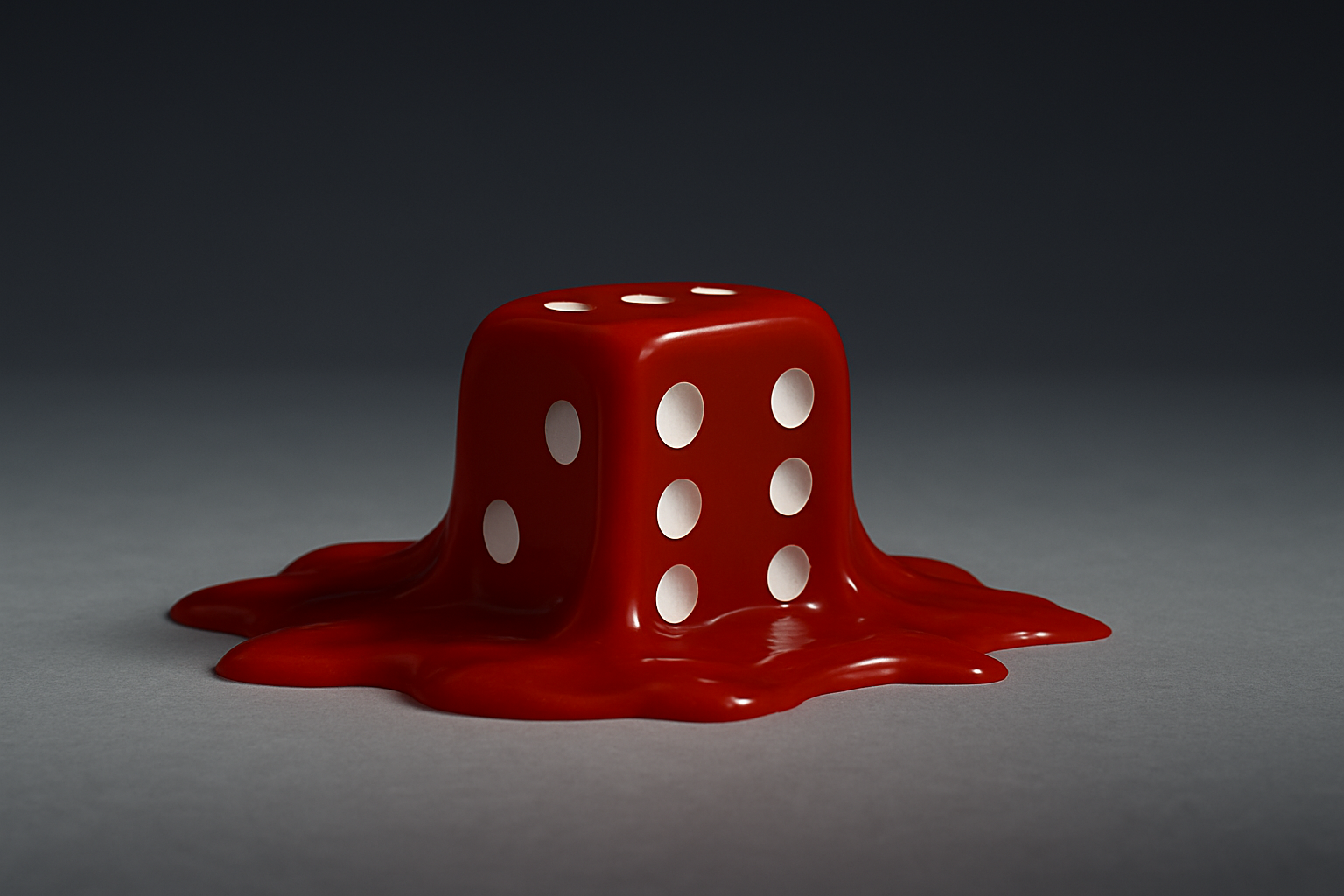
Plastic after reaching the melting point
The specific melting point can vary depending on the type and composition of the plastic material. Different types of plastic have different chemical structures and properties, leading to varying melting points. For example, some plastics have relatively low melting points, average around 70°C (158°F), while others have higher melting points, reaching temperatures of over 200°C (392°F).
Some plastics have low melting points, such as polyethylene (PE), which typically melts around 105°C to 135°C (221°F to 275°F). Others have higher melting points, like polycarbonate (PC), which typically melts around 220°C to 250°C (428°F to 482°F). The specific melting point also depends on factors such as molecular weight, crystallinity, and additives present in the plastic.
The melting point of plastic helps determine the temperature at which plastic can be processed, shaped, and molded. By heating the plastic to or above its melting point, manufacturers can utilize techniques like injection molding, extrusion, or blow molding to form the plastic into desired shapes products.
Moreover, the melting point is essential for ensuring the stability and performance of plastic products. Exceeding the melting point can result in degradation, deformation, and loss of desired physical properties. On the other hand, if the plastic is not heated enough to reach its melting point during processing, it may not have sufficient flowability for molding or shaping.
In conclusion, the melting point of plastic is a critical factor to consider when working with plastic materials. It allows for proper handling, processing, and utilization of plastics in various industries, ranging from packaging, construction to automotive and electronics.
2. Why is the melting temperature of plastic so important?
2.1. Material Selection
Selecting the appropriate plastic for a specific application requires knowledge of its melting point. For example, high-melting-point plastics like PTFE are ideal for high-temperature applications, whereas lower melting point plastics like polypropylene are better suited for everyday consumer goods.
2.2. Processing Efficiency
Plastics with lower melting points require less energy to process, leading to cost savings and faster production cycles. Conversely, high-melting-point plastics demand more energy and time, impacting overall manufacturing efficiency .
2.3. Product Performance
The melting point affects the thermal stability and mechanical properties of the final product. A plastic's ability to withstand service temperatures without deforming is directly related to its melting point.
.png)
Plastic deformed after exceeding temperature range
Exceeding the melting temperature can lead to several negative consequences:
- Firstly, it can cause degradation of the plastic material. The high heat can break molecular bonds within the plastic's polymer chains, resulting in a decrease in strength, loss of desired properties, and the generation of unwanted by-products.
- Secondly, exceeding the melting temperature can lead to deformation. The plastic may warp, distort, or lose its shape during processing, resulting in products that do not meet the desired specifications. Additionally, exceeding the melting temperature can cause undesirable changes in the plastic's properties, such as changes in density, viscosity, or chemical reactivity, which can compromise the performance and quality of the final product.
By controlling and adhering to the recommended melting temperature range, manufacturers can prevent these issues and ensure the stability and quality of the plastic products. The melting temperature acts as a guide for achieving the desired properties, dimensional accuracy, and structural integrity during the manufacturing and processing of plastic materials.
In summary, the melting temperature of plastic is crucial in different situations, including manufacturing and processing. Understanding and controlling the melting temperature are essential in determining the suitable methods for shaping and molding plastic as well as ensuring the overall quality and performance of plastic materials.
3. What is the melting point for different plastic materials?
As mentioned before, we all know that different types of plastic materials have different chemical structures and mechanical properties, consequently resulting in different ideal temperature ranges or melting points.
Some of the questions that EuroPlas receive the most are “What is the melting point of PVC plastic?”, “What is the temperature range of ABS plastic?” or “What is the maximum temperature that PS plastic can withstand?”. In the following part, EuroPlas would like to provide a detailed information sheet including temperature ranges, melting points as well as basic features and applications of some popular plastic materials in the current market.
|
Temperature Range |
Melting Point |
Characteristics |
Polyethelene (PE) |
-50°C to 80°C |
105°C to 115°C |
Flexible, durable, chemical resistant |
Polypropylene (PP) |
0°C to 120°C |
130°C to 171°C
|
High resistance to heat, chemical resistance, lightweight
|
Polyvinyl Chloride (PVC) |
-10°C to 60°C
|
100°C to 260°C (depends on the type)
|
Flame resistance, electrical insulation, rigid or flexible depending on additives.
|
Polystyrene (PS) |
-20°C to 70°C |
210°C to 240°C
|
Transparent or opaque, lightweight, easily molded.
|
Polyethelene Terephthalate (PET) |
-40°C to 70°C
|
250°C to 260°C
|
Transparent, highly durable
|
Acrylonitrile Butadiene Styrene (ABS) |
-20°C to 80°C
|
210°C to 270°C
|
Excellent impact resistance, rigid and tough, easily molded.
|
Polycarbonate (PC) |
-135°C to 135°C |
220°C to 230°C |
Light, durable, good light transmission, easily molded.
|
3.1. Temperature ranges of Polyethylene (PE)
Polyethylene (PE) comes in different types, primarily Low-Density Polyethylene (LDPE) and High-Density Polyethylene (HDPE), and each has its own temperature range.
Low-Density Polyethylene (LDPE):
- Melting Point: 105°C to 115°C (221°F to 239°F)
- Maximum Service Temperature: Approximately 80°C (176°F)
- Brittle Temperature: Around -110°C (-166°F)
High-Density Polyethylene (HDPE):
- Melting Point: 120°C to 130°C (248°F to 266°F)
- Maximum Service Temperature: Approximately 120°C (248°F)
- Brittle Temperature: Around -100°C (-148°F)
Read more: What Is the Melting Point of PE Plastic?
3.2. Temperature ranges of Polypropylene (PP)
Polypropylene (PP) is a versatile thermoplastic with specific temperature characteristics that make it suitable for various applications.
- Melting Point: 130°C to 171°C (266°F to 340°F)
- Maximum Service Temperature: Approximately 100°C to 120°C (212°F to 248°F)
- Brittle Temperature: Below 0°C to -20°C (32°F to -4°F)
Read more: PP Melting Point: Discover Polypropylene's Temperature Ranges
3.3. What is the temperature range of PVC plastic?
Polyvinyl Chloride (PVC) is a versatile plastic with a range of temperature characteristics that vary depending on its formulation (rigid or flexible PVC).
Rigid PVC (uPVC):
- Glass Transition Temperature: 80°C to 85°C (176°F to 185°F)
- Maximum Service Temperature: Approximately 60°C to 70°C (140°F to 158°F)
- Minimum Service Temperature: Down to -15°C to -20°C (5°F to -4°F)
Flexible PVC:
- Maximum Service Temperature: Approximately 60°C to 70°C (140°F to 158°F)
- Minimum Service Temperature: Down to -30°C (-22°F) or lower, depending on the plasticizers used.
Read more: PVC Melting Point And Its Influence In Product
3.4. What is the melting point of PS Plastic?
Polystyrene is a synthetic polymer made from styrene monomers, which are organic compounds derived from petroleum. Polystyrene melting point is a key characteristic that determines how the material behaves under heat and during manufacturing processes, with the melting point from 210°C to 240°C.
Read more: How Polystyrene Melting Point Affect Product's Performance
4. About EuroPlas
After 18 years of establishment, EuroPlas has become a global leader in masterbatch and bioplastic compound manufacturing. With seven factories located in Vietnam and Egypt, and a production capacity of up to 800,000 tons annually, EuroPlas exports to over 95 countries worldwide.
Our products including: Bioplastic compound, filler masterbatch, color masterbatch, plastic additives, biofillers, and engineering plastic compound. At EuroPlas, we place great importance on delivering exceptional plastic products that are created with meticulous attention to detail and precise craftsmanship. Our team consists of dedicated professionals with high levels of expertise, committed to providing excellent customer service to guarantee your complete satisfaction.
Contact us today to discover our wide range of products and find the ideal plastic solution that is customized to meet your specific requirements.
Explore more valuable information right here!