Polystyrene is one of the most versatile and widely used plastics in the world. Known for its durability and cost-effectiveness, polystyrene plays a critical role in various industries, from packaging to construction. One key property that defines its application potential is its melting point. Understanding polystyrene melting point is crucial for industries working with this material, as it affects how products are manufactured, processed, and used. In this article, we will explore polystyrene melting point, how it influences product design, and its various applications.
1. Overview of Polystyrene
Polystyrene is a synthetic polymer made from styrene monomers, which are organic compounds derived from petroleum. As a thermoplastic material, polystyrene has the ability to be repeatedly melted and reshaped, making it highly valuable for various manufacturing processes. Depending on how it is produced, polystyrene can exist in different forms, including solid, foam, and film, each with unique characteristics tailored to specific industrial needs.
There are two primary types of polystyrene:
General Purpose Polystyrene: GPPS is the clear, rigid, and brittle version of polystyrene. It is often used for products that need to be transparent, such as food containers, laboratory ware, and packaging.
High Impact Polystyrene (HIPS): Blended with rubber, HIPS is more impact-resistant than GPPS, making it suitable for products that require extra durability. It’s often used in applications such as refrigerator linings, toys, and electronic housings.
Another form of polystyrene is Expanded Polystyrene (EPS), a lightweight foam material widely used for insulation, packaging, and protective materials. EPS consists of small polystyrene beads that are expanded and fused together, creating a lightweight yet strong material with excellent insulation properties. Additionally, Extruded Polystyrene (XPS) is a denser, more moisture-resistant foam, typically used in construction and building insulation.
Polystyrene is valued for its excellent insulation, rigidity, and lightweight nature. Due to its low production cost and ease of manufacturing, it is one of the most commonly used plastics globally. However, it is important to note that polystyrene, especially in its solid form, can be brittle, which limits its use in certain high-impact or high-stress applications.
2. What Is polystyrene melting point?
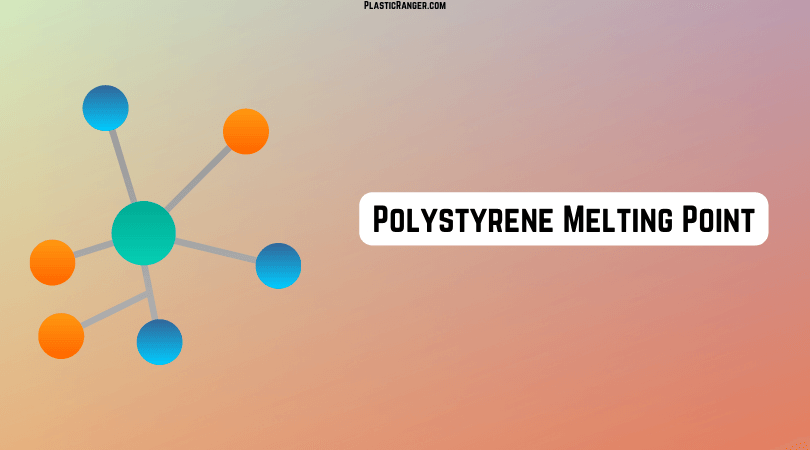
What is polystyrene melting point?
Polystyrene melting point is a key characteristic that determines how the material behaves under heat and during manufacturing processes. The melting point refers to the temperature at which a solid material transitions into a liquid state. For polystyrene, this temperature typically falls within the range of 210°C to 249°C (410°F to 480°F). The exact melting point can vary based on the type of polystyrene and any additives used in its production.
General Purpose Polystyrene (GPPS) typically has a melting point closer to 240°C (464°F). Its relatively high melting point allows it to maintain rigidity and shape under moderate heat, which is beneficial for products such as plastic cups, lids, and containers that may be exposed to warm environments.
High Impact Polystyrene (HIPS), due to the inclusion of rubber in its composition, has a slightly lower melting point, typically around 210°C to 230°C (410°F to 446°F). This lower range allows for easier molding and shaping while still providing enhanced durability.
Read more: Temperature ranges for different plastic materials
It’s important to differentiate between the glass transition temperature (Tg) and the melting point. The glass transition temperature for polystyrene is around 100°C (212°F). Below this temperature, polystyrene behaves as a rigid, glass-like material. Above the glass transition temperature but below the melting point, polystyrene becomes soft and flexible, yet not fully melted. This softening property is crucial for applications that involve thermoforming, where polystyrene is heated just enough to allow for molding but not to the point of liquefaction.
The melting point of expanded polystyrene (EPS) is typically in the lower part of the range, closer to 210°C (410°F). EPS can begin to lose its structural integrity at even lower temperatures due to its foam structure, making it unsuitable for high-heat applications.
3. How Its Melting Point Affects Products
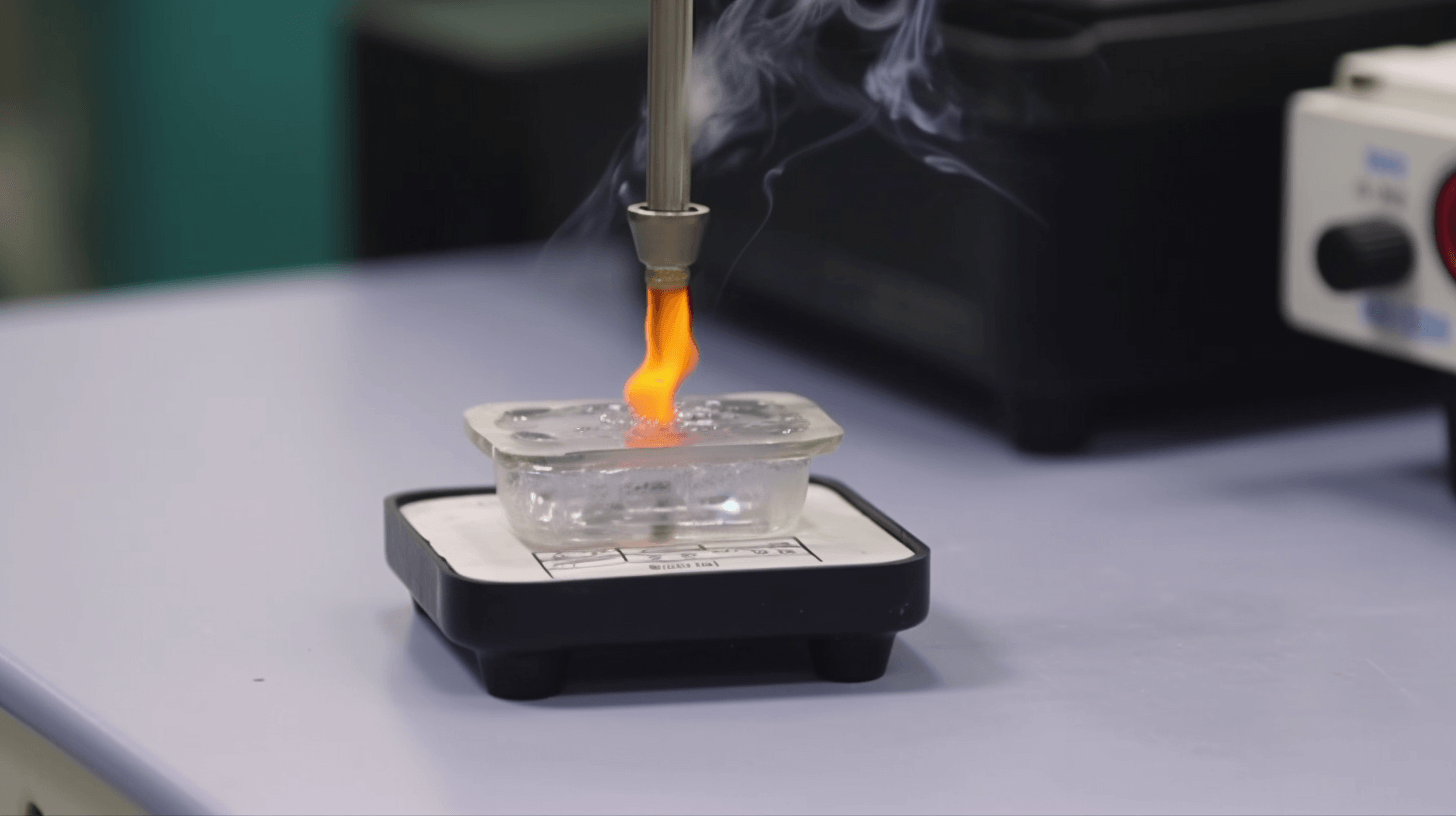
Polystyrene melting point has a lot of effects
The melting point of polystyrene plays a critical role in determining how it is processed and applied in various industries. During the manufacturing process, polystyrene melting point dictates the temperatures required for processes such as injection molding, extrusion, and thermoforming. These methods allow polystyrene to be formed into a wide range of shapes and products.
Injection Molding: Polystyrene is commonly used in injection molding, a process where melted polystyrene is injected into a mold cavity to form various products like plastic utensils, packaging materials, and electronic housings. The material's relatively low melting point means that it can be molded at moderate temperatures, which helps reduce energy consumption during manufacturing.
Extrusion: In extrusion processes, polystyrene is heated to just above its melting point and forced through a die to produce continuous shapes like sheets, tubes, and films. The low melting point allows for efficient and consistent production, making polystyrene an ideal choice for packaging materials, protective coverings, and insulation.
Thermoforming: In thermoforming, polystyrene sheets are heated to just below their melting point, allowing them to be shaped into specific forms by pressing them against a mold. This process is used to create items like disposable plates, food trays, and take-out containers. The material’s softening point is critical here, as the polystyrene must remain flexible enough to form, yet not melt completely during the process.
However, the low melting point of polystyrene also introduces certain limitations, particularly in applications that require high-temperature resistance. Polystyrene is not suitable for use in environments where it will be exposed to prolonged heat above its melting point. For example, it cannot be used in kitchenware that comes into direct contact with hot surfaces, such as microwaves, stovetops, or ovens, as it would deform or melt.
Despite these limitations, polystyrene melting point provides advantages in environments where temperature control is maintained. It offers excellent insulation properties in packaging, protecting contents from temperature fluctuations while also maintaining its structural integrity. In construction, polystyrene foam is used for insulation in walls and roofing, but it must be shielded from high temperatures to prevent degradation.
Eventually, the melting point of polystyrene is a defining feature of its functionality. Manufacturers must consider the temperature range in which the material can operate to ensure the product's safety, durability, and efficiency. With its relatively low melting point, polystyrene is a preferred material for industries that prioritize lightweight, cost-effective solutions, as long as temperature limitations are factored into product design.
4. Applications of Polystyrene
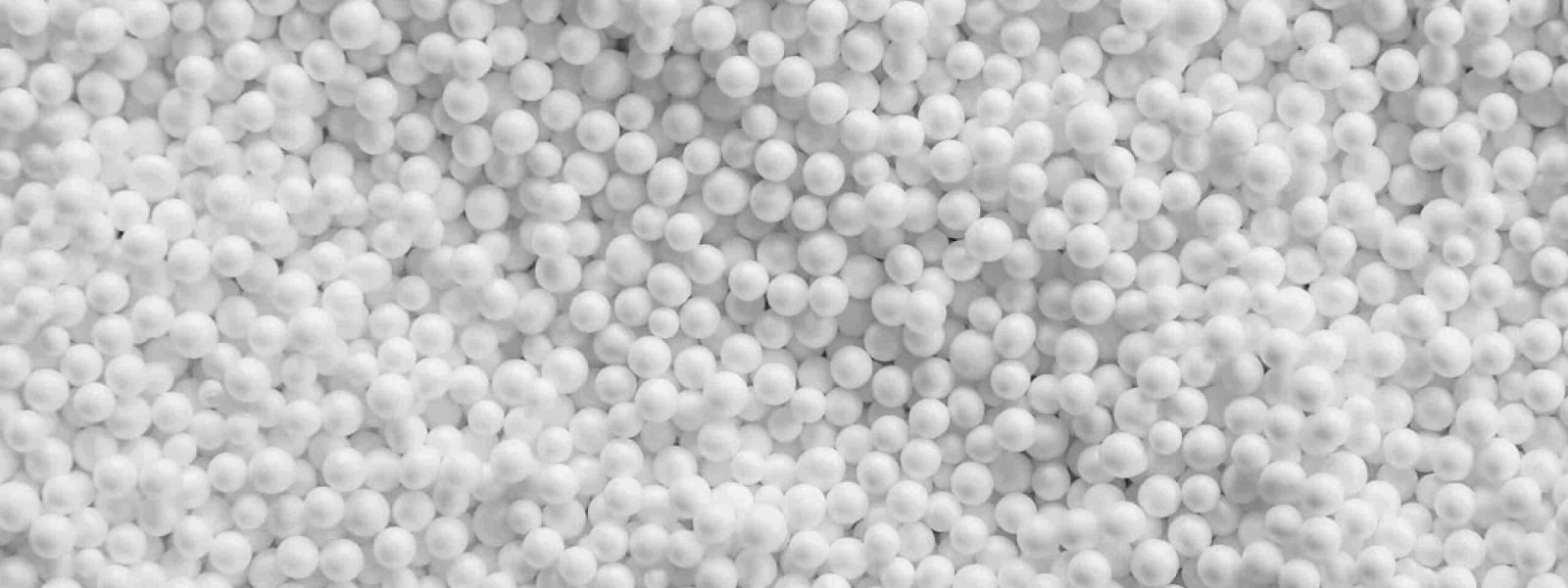
Different polystyrene melting points has different applications
Polystyrene’s versatility allows it to be used in a wide array of applications across various industries, making it one of the most commonly utilized plastics globally. From everyday consumer goods to specialized industrial components, polystyrene’s unique properties suit a multitude of needs.
Packaging: One of the most significant applications of polystyrene is in packaging materials. Its lightweight nature and excellent insulating properties make it ideal for protecting goods during shipping and storage. Polystyrene is widely used for disposable containers, cups, and food trays due to its ability to maintain structural integrity while keeping food items insulated. Expanded polystyrene (EPS) is especially favored for protective packaging, as it cushions delicate items like electronics, glassware, and fragile components during transport.
Construction and Insulation: Polystyrene plays a crucial role in the construction industry, particularly as a thermal insulator. Both EPS and extruded polystyrene (XPS) are used for insulating walls, roofs, and floors in residential and commercial buildings. Their low thermal conductivity helps reduce energy consumption by maintaining a stable indoor temperature, contributing to energy efficiency and sustainability in building practices. Additionally, polystyrene foam is often employed in concrete forms and foundation insulation to improve structural performance and longevity.
Consumer Products: In the consumer goods sector, polystyrene is used in various everyday items. From toys and household appliances to electronics and furniture components, polystyrene’s durability and cost-effectiveness make it a popular choice. High-impact polystyrene (HIPS) is particularly valued for products that require greater resilience to impact and stress. Items such as refrigerator liners, remote control casings, and plastic toys benefit from the material's strength and versatility.
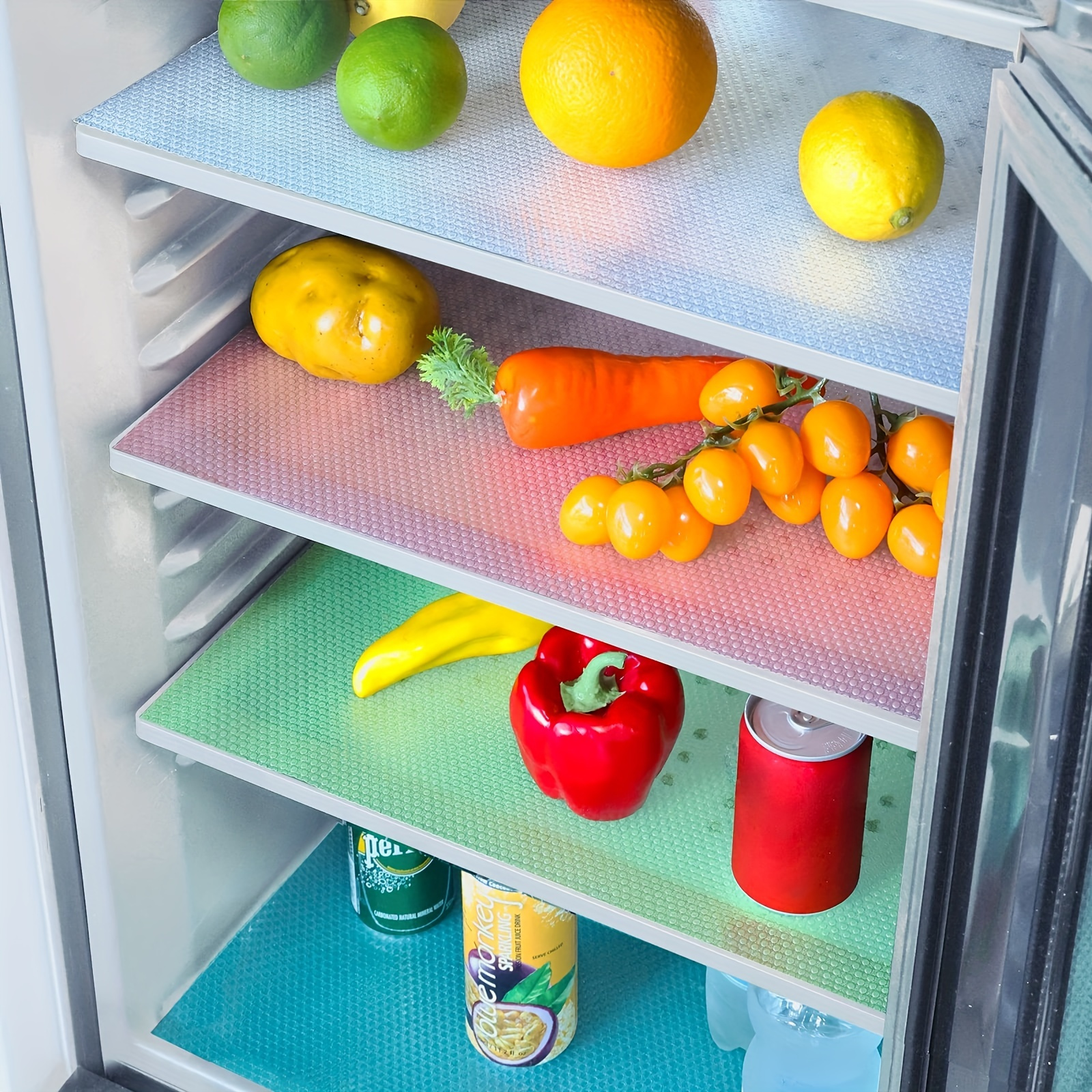
Polystyrene melting points applied in refrigerator liners
Medical Applications: The medical industry also utilizes polystyrene due to its clarity, rigidity, and ease of sterilization. Polystyrene is commonly used for laboratory ware, such as petri dishes, test tubes, and blood collection trays. Its low cost and reliable performance make it an ideal material for disposable medical supplies, including syringes and specimen containers. Additionally, its chemical resistance ensures that it can safely store various biological samples without contamination.
Electrical and Electronic Applications: In the electrical and electronics industry, polystyrene is used for its excellent insulating properties. It is commonly found in the production of electrical housings, circuit boards, and components where protection from moisture and heat is essential. The material's ability to be molded into intricate shapes allows for the creation of customized enclosures that meet specific electrical safety standards.
Crafts and Arts: Polystyrene is also a popular material in the arts and crafts sector. It can be easily cut, shaped, and painted, making it an excellent choice for various creative projects. Artists and hobbyists often use polystyrene sheets and shapes for model building, decoration, and artistic installations. Its lightweight nature allows for easy handling and transportation, making it a favorite among creators.
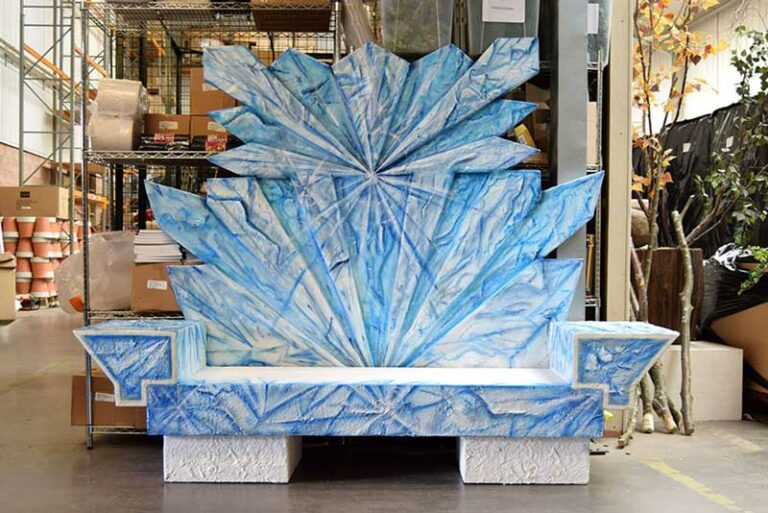
Polystyrene melting points applied in crafts and arts
As diverse as its applications may be, it’s important to note that the characteristics of polystyrene can vary depending on its form and the specific requirements of each application. For example, while general-purpose polystyrene is suitable for transparent products, high-impact variants are more appropriate for items that require enhanced durability. Understanding these nuances enables manufacturers to select the appropriate type of polystyrene for their specific needs, ensuring optimal performance and quality.
5. Conclusion
In summary, polystyrene is a vital material that has found its way into numerous applications across various industries, thanks to its unique properties and advantages. Understanding polystyrene melting point, along with its characteristics and types, is essential for manufacturers and consumers alike.
From packaging and construction to consumer products and medical applications, polystyrene's versatility and cost-effectiveness continue to make it a preferred choice in many sectors. As industries evolve and new technologies emerge, polystyrene will likely remain a key player in material science, adapting to meet the demands of modern manufacturing and design.
6. About EuroPlas
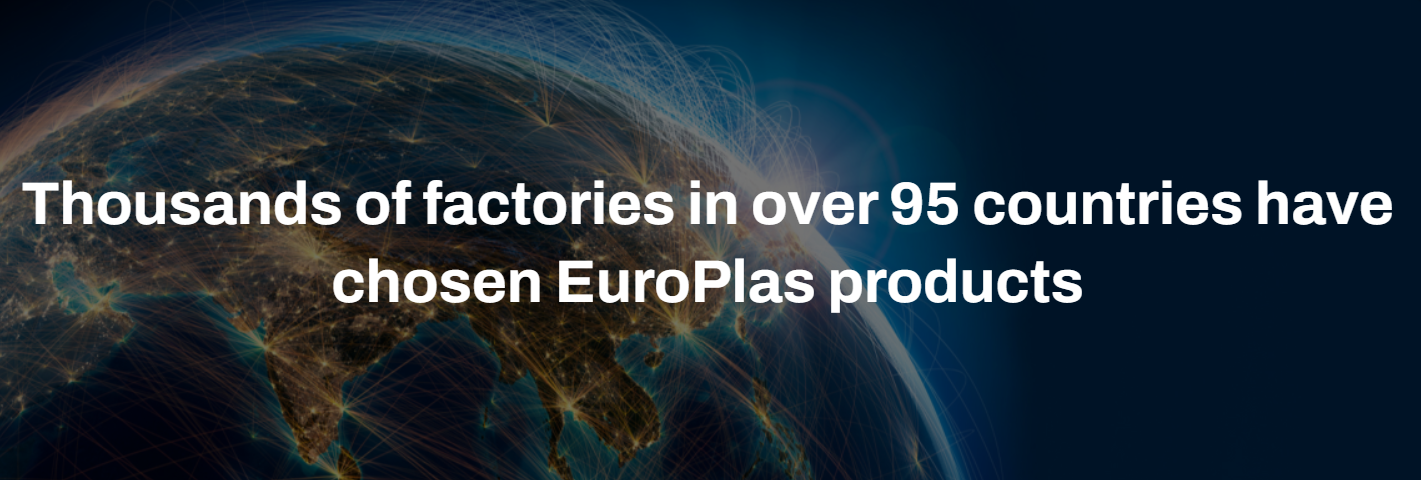
EuroPlas - No. 1 filler masterbatch manufacturer
As the world’s No. 1 filler masterbatch manufacturer, EuroPlas offers tailor-made plastic material solutions that enhance the competitiveness of plastic enterprises. With a global mindset and dedication to innovation, EuP provides materials that meet high-quality standards while ensuring sustainable development practices. EuP operates seven state-of-the-art factories, equipped with advanced technology to produce up to 0.8 million tons annually, serving industries in over 95 countries worldwide. EuP’s commitment to customer satisfaction and optimal material solutions makes it a trusted partner for companies working with plastic materials.
Looking for advanced plastic material solutions? Visit our Contact Us page to learn how EuroPlas can help your business thrive.