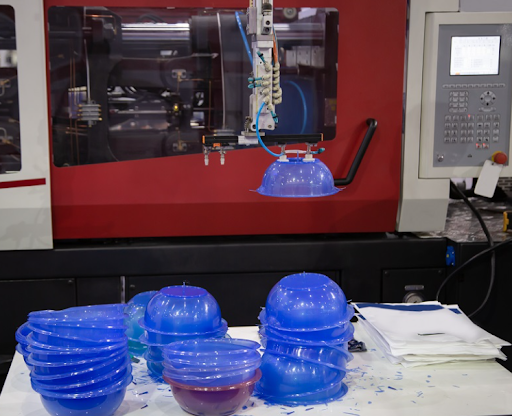
There are a variety of vacuum forming machines compatible with each production need
Vacuum forming machines are considered one of the advanced product shaping methods with benefits that everyone should know about. This is a process that utilizes heat to soften plastic materials and vacuum them into molds to create the desired shape. Currently, there are a variety of vacuum forming machines compatible with each production need. The following article will provide more details about the parts and operating processes of different types of vacuum forming machines. Furthermore, imagine that you can create your own vacuum forming machine at home with very simple steps. All will be revealed soon!
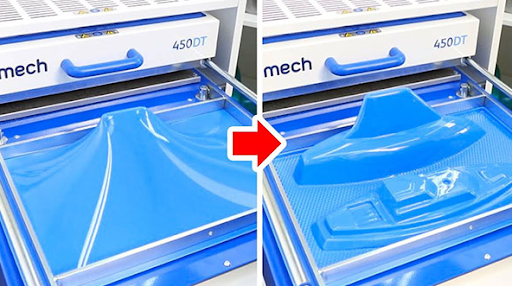
Vacuum forming machines can create a variety of product designs that widely used in many different fields
Vacuum forming is one of the most popular product shaping methods today. Vacuum forming is a manufacturing process in which a heated plastic sheet is stretched over a mold and then sucked tightly into the mold by vacuum. To make it easier to remove the finished product from the mold, the mold will have an angle of about 3 degrees.
Vacuum forming is one of the production methods that is quite flexible. Vacuum forming can be applied to a variety of plastic materials such as acrylic, HDPE, polystyrene and other thermoplastics. Vacuum forming machines can create a variety of product designs, so it is widely used in many fields such as turn signs, machinery protective covers, aerospace components, window covering machines, etc. In addition, vacuum forming is also used for packaging, trays and other products as needed.
Read more: Vacuum forming plastic - The ultimate guide
2. All types of vacuum forming machines
2.1. DIY machines
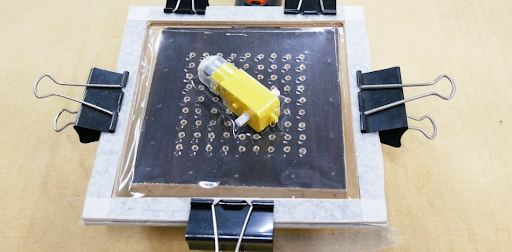
DIY vacuum forming machines help save a large amount of investment costs for machinery
DIY vacuum forming machines can be created based on the needs of each project. DIY vacuum forming machines also help save a large amount of investment costs for machinery. The basic materials needed to prepare your DIY vacuum forming machine include: several sheets of wood (plywood, MDF, etc), vacuum cleaner, glue, clamps, sanding tape, oven, varnish and some manufacturing tools. The process of creating a basic DIY vacuum machine is not too complicated.
- Step 1: Determine the size according to usage needs then proceed to cut the wooden panels. These wooden panels are used as the side walls of the machine. Make sure that the wooden panels are sized to the appropriate size and that the surface of the panel is sanded
- Step 2: Measure and drill suction holes for your vacuum forming machines. Drill holes need to be about 3/4 inch apart on the wood surface where you will place your object. Be sure to clean the surface of the board after drilling to avoid debris
- Step 3: Assemble the wooden pieces into the frame of the vacuum forming machines by applying glue along their edges and gluing them together. Add sealant to the joints to ensure effective vacuum creation
- Step 4: Create the plastic holder with a larger frame than the vacuum frame made in step 3. This frame will hold the plastic sheet in place during the shaping process
- Step 5: Attach the bracket to the vacuum frame. Apply draft-proof tape to the inside edges where the plastic meets the mold surface to improve suction. To help make the machine's appearance more complete, you can apply a layer of gloss paint
To perform the shaping process with vacuum forming machines, first you need to prepare the printing mold. Place the object that serves as the mold inside the vacuum frame. Next, heat the plastic by heating them in an oven until they soften. Then proceed to shape by quickly placing the gradually flabby plastic material into the mold and turning on the vacuum cleaner. The vacuum cleaner will help the plastic to be sucked and adhere tightly to the object (mold) and its shape. The final step is to cool the materials and remove them from the vacuum forming machine.
2.2. Table top machines
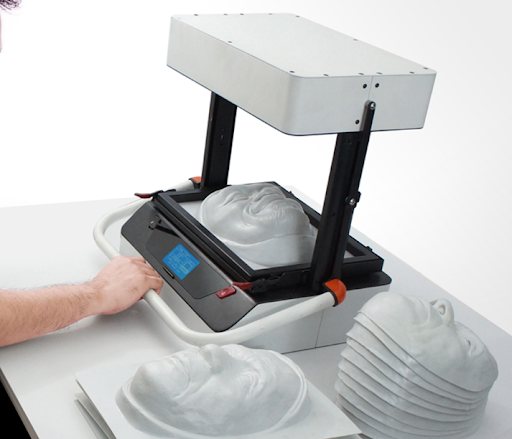
The basic structure of table top machine includes a machine frame, heating element, vacuum system and rollers to hold materials
Vacuum forming is also quite commonly done using table top machines. The process of heating the plastic sheet and then using vacuum pressure to shape it on a pre-set mold will become easier with this device. The basic structure of the machine includes a machine frame, heating element, vacuum system and rollers to hold materials. The machine frame is usually made from wood or metal to help make the machine sturdy. Besides, heating elements such as heaters are often made of ceramic or nichrome wire. A vacuum cleaner or vacuum pump helps create vacuum and a roller holds the plastic sheet in place during the shaping process.
The operating process of table top vacuum forming machines is also very easy to grasp.
- Step 1: Clamp the plastic sheet onto the mold on the roller of the vacuum forming machines
- Step 2: The heating element will take on the role of heating the plastic until it becomes soft and flexible
- Step 3: The roller of the vacuum forming machine moves up to seal the rubber gasket, creating a vacuum chamber below the plastic layer
- Step 4: A vacuum pump or vacuum cleaner will remove the air and firmly suck the heated plastic into the contours of the mold to shape the product
- Step 5: Proceed with the steps to cool and solidify the product. The resulting plastic product can be removed from the mold and used
2.3. Single heater machines
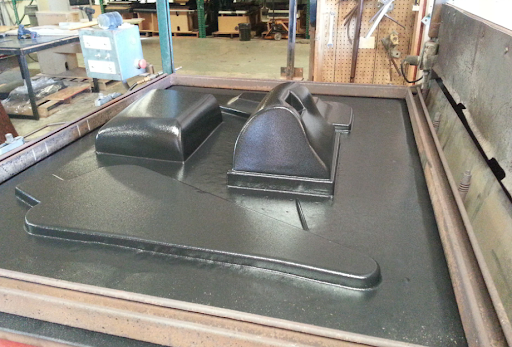
Single heater machines are often used for smaller-scale production or prototyping due to their simpler design and operation
Single heater vacuum forming machines are a type of equipment that is also quite commonly used today. The machine possesses a single heater that helps heat the plastic sheet to make it soft before being cast on the mold. Among vacuum forming machines, single heater machines are often used for smaller-scale production or prototyping due to their simpler design and operation. Single heater vacuum forming machines are often made up of parts such as:
- Single heater or infrared heater: helps heat plastic sheets to a temperature where they become soft
- Frame: helps hold the plastic sheet and move it into position on the mold. Bonus comes with a mandrel plate that helps support the mold during the forming process
- Molds: they are the shape of the product to be shaped
- Vacuum pump system: helps pull heated plastic tightly onto the mold surface
- Cooling system: helps accelerate the cooling process of newly shaped plastic products
The operating steps of those single heater vacuum forming machines are:
- Step 1: Place the plastic sheet on the frame and heat it with a heater until the plastic becomes soft and flexible
- Step 2: Place the plastic sheet close to the mold and fix them at the appropriate distance
- Step 3: Activate the vacuum pump to create suction between the mold and the heated plastic sheet. This process helps pull the plastic sheet tightly to the contours of the mold
- Step 4: Cool the newly shaped product
2.4. Double heater vacuum forming machines
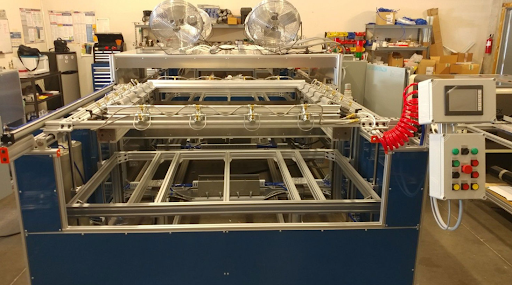
Double heater machines are usually be designed with two heating stations
Double heater machines are also one of the ideal vacuuming forming devices today. Like other vacuum forming machines, they still operate on the principle of heating plastic materials and shaping them using vacuum equipment. However, double heater machines will usually be designed with two heating stations. This allows the machine to heat the plastic more evenly and faster. Similar to the vacuum forming machines mentioned above, this machine also has the following main parts:
- Heating element: They are designed with two heating elements or two different heating stations
- Vacuum equipment: A vacuum machine will help the soft plastic material to be sucked tightly into the mold
- Frame: The frame plays the role of fixing the plastic sheet during the heating process, making this process easier
- Shaping table: This is where molds are placed to shape new products
- Cooling part: This is a very important part that contributes to freezing the product so it can be easily removed from the frame
The forming process of double heater vacuum forming machines is described as follows:
- Step 1: fix the plastic sheet to the clamp frame to stabilize them during the temperature increase
- Step 2: Increase the temperature to soften the plastic sheets. The heating process is taken care of by two heating stations, making the process faster and easier
- Step 3: Shape the product by starting the vacuum unit. This process helps pull the soft plastic sheet tightly onto the mold to form the desired shape
- Step 4: Cool the newly shaped product using cooling wind systems
- Step 5: Separate the product mold and handle excess plastic parts
3. Which type of vacuum forming machine should you use?
In general, all types of vacuum forming machines operate on similar principles. It is the process of heating plastic materials and shaping them using a vacuum machine to create the desired shape. Depending on production needs, the appropriate machine type will be chosen. For home production processes, DIY vacuum forming machines can be applied to help save machinery investment costs. In addition, table top vacuum forming machines are an ideal choice for small and simple forming needs. For medium-sized production processes, you can invest in single heater vacuum forming machines to help ensure the product shaping process is more accurate and of better quality. However, for higher production needs, double vacuum forming machines can be used to help speed up the heating process to save more time.
4. Conclusion
In conclusion, vacuum forming machines are one of the quick and easy methods of shaping products. You can create your own vacuum forming machines or invest in a variety of different machines. Different types of vacuum forming machines, although they have the same operating principle, will possess some of their unique advantages. Products shaped by vacuum forming machines always give the product standard parameters and exquisite details. Depending on your production needs, you can choose the appropriate machine type to save time and costs.
5. About EuroPlas
EuroPlas is proud to be one of the most reputable and trustworthy material suppliers worldwide. You can easily find and buy bio-filler, color masterbatch, plastic additives, engineering plastic compounds, and bioplastic compounds, etc., with just a click of the mouse. Besides, come to EuroPlas' blog today to update more useful materials information. We are a provider of optimal material solutions with a series of high quality plastic lines. Our solutions meet the diverse needs of the world's industries, not only in terms of high standards and reliability but also in terms of environmental obligations.