The plastic machining industry has seen remarkable advancements over the years, driven by innovations that improve precision, speed, and efficiency. Plastic machining is evolving rapidly from high-speed multitasking machines to advanced cooling systems and automation. This article will explore some of the top innovations in plastic machining technology and explain their importance in modern manufacturing.
1. Development of Plastic Machining Over The Years
1.1. Early Days Of Plastic Machining
The use of plastics in manufacturing began in the early 20th century, with the advent of materials such as Bakelite, the first synthetic plastic. At that time, plastic machining was a relatively simple process that involved using hand tools to shape and cut plastic parts. Machinists used a variety of cutting tools, such as knives, saws, and chisels, to remove material and create the desired shapes.
In the 1930s, the introduction of thermoplastics, such as polystyrene and polyvinyl chloride (PVC), further expanded the use of plastics in manufacturing. However, plastic machining remained a manual process, with workers using hand tools and manual lathes to shape and cut plastic parts.
1.2. Advancements In Plastics And Machining Technology
In the 1950s, the development of high-performance plastics like nylon and acrylic changed the plastics industry. These new materials were stronger, tougher, and could handle heat better than earlier plastics, making them perfect for many different uses.
At the same time, advancements in machining technology were making it possible to produce more complex plastic parts with greater precision. CNC (Computer Numerical Control) machines were invented, allowing machinists to program them for various cutting and shaping tasks automatically. This made the production of plastic parts faster, more accurate, and more consistent.
In the 1970s and 1980s, new materials such as polycarbonate and acetal came along, further expanding the options for machining plastics. These materials were even stronger and more resistant to heat and chemicals, making them suitable for demanding industries like aerospace, automotive, and medical devices.
.jpg)
CNC (Computer Numerical Control)
1.3. The Future Of Plastic Machining
In recent years, 3D printing has become a powerful tool for making plastic parts. 3D printing, also known as additive manufacturing, involves building up parts layer by layer using a variety of materials, including plastics. This method is especially helpful for creating complex shapes that would be hard or impossible to make with regular machining techniques.
While 3D printing is not a direct replacement for traditional machining methods, it is increasingly being used in conjunction with these methods to produce plastic parts more efficiently and effectively. For example, 3D printing can be used to create a prototype of a plastic part, which can then be machined to create a finished product. This allows for faster and more efficient product development, as well as greater flexibility in design and manufacturing.
Another new technology impacting plastic machining is the use of artificial intelligence (AI) and machine learning. These tools are being used to develop software that can analyze and improve machining processes, making them faster, more accurate, and better controlled.
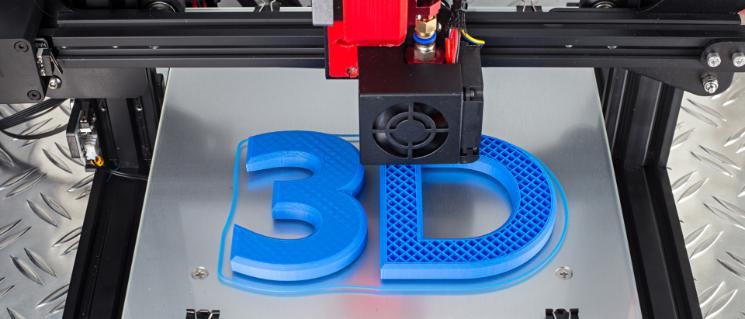
3D Printing
Read more: Popular methods of processing composite materials
2. Best Innovations In Plastic Machining Technology
2.1. High-Speed Multitasking Machines
One of the most significant innovations in plastic machining is the development of high-speed multitasking machines. These machines can perform multiple operations, such as milling, drilling, turning and other operations within a single setup. For example, manufacturers in the automotive industry rely on complex, high-quality plastic components for vehicle interiors and assembly. These requirements are ideal for custom plastic manufacturers to improve their methods.
Some of the key benefits of high-speed multitasking machines in plastic machining include:
- Increased Productivity: These machines can perform multiple tasks without the need for manual intervention, reducing production time.
- Improved Precision: With fewer setups required, there is less risk of errors, resulting in higher accuracy.
- Cost-Effectiveness: The ability to complete multiple processes in one machine reduces labor and operational costs.
2.2. Advanced Cooling Technologies
Plastic machining often involves high temperatures, which can affect the material’s properties and lead to warping, melting, or other defects. To address this, advanced cooling technologies have been developed to maintain optimal temperatures during the machining process.
One innovative method is cryogenic cooling, which uses liquid nitrogen to cool the cutting area. This approach prevents heat buildup, reduces tool wear, and enhances the overall surface finish of the plastic part. Additionally, cryogenic cooling is more environmentally friendly than traditional methods, as it eliminates the need for harmful lubricants and coolants.
Key benefits of advanced cooling technologies include:
- Enhanced Surface Quality: Effective cooling reduces the risk of heat-induced defects, improving the surface finish of the machined part.
- Increased Tool Life: Lower operating temperatures result in less wear and tear on tools, extending their lifespan.
- Environmental Benefits: Some advanced cooling methods eliminate the need for traditional coolants, reducing environmental impact.
.jpg)
Plastic Processing Cooling Chiller
2.3. Robotics and Automation
Automation and robotics have revolutionized plastic machining by improving efficiency and reducing human error. Robotics can handle repetitive tasks with precision, allowing for higher production volumes and consistent quality. Additionally, automated systems can operate continuously without the need for breaks, leading to a significant increase in throughput.
Robotic arms and automated systems can be incorporated at various stages of the plastic machining process, from loading raw materials to removing finished parts. They can also contribute to quality control by utilizing sensors and vision systems to inspect parts for defects or deviations from specifications.
Key benefits of robotics and automation in plastic machining include:
- Higher Efficiency: Automated systems can work continuously, increasing production speed.
- Improved Accuracy: Robotics minimize the risk of human error, ensuring consistent quality.
- Reduced Labor Costs: Automation reduces the need for manual labor, lowering operational costs.
.jpg)
Industrial robots
2.4. Advanced Tooling and Cutting Techniques
Significant advancements in tooling materials and cutting techniques have also elevated plastic machining operations. Polycrystalline diamond (PCD) and cubic boron nitride (CBN) tools are exceptionally wear-resistant and offer a long service life. They improve the machining of abrasive and high-strength materials. High-feed milling and trochoidal milling are innovative cutting techniques for rapid material removal rates while minimizing heat generation and tool wear.
Key benefits of advanced tooling and cutting techniques include:
- Improved Finish Products: Specialized tools and techniques result in smoother and more accurate finishes.
- Enhanced Durability: High-quality tools, such as diamond-coated options, last longer and provide better performance.
- Ability to Machine Complex Geometries: Multi-axis CNC machines and ultrasonic machining allow for the creation of intricate plastic components.
.jpg)
Polycrystalline Diamond (PCD)
2.5. Digitalization and Data Analytics
The digital transformation of plastic machining has introduced advanced data analytics and monitoring systems that provide real-time insights into the machining process. Through the use of sensors, connected machines can track performance metrics such as temperature, speed, tool wear, and material behavior during machining. This data can be analyzed to optimize processes, predict maintenance needs, and improve overall efficiency.
Digital twin technology is another significant innovation, allowing manufacturers to create a virtual model of a machine or production line. This virtual model can be used to simulate different machining scenarios and identify potential improvements before implementing them in the real world.
The integration of Industry 4.0 technologies, such as the Internet of Things (IoT), has made it possible to automate decision-making processes based on data. Smart factories can now automatically adjust machining parameters to optimize production without human intervention.
Key benefits of digitalization and data analytics in plastic machining include:
- Process Optimization: Data analytics enable manufacturers to identify inefficiencies and make real-time adjustments to improve performance.
- Predictive Maintenance: By monitoring machine health, manufacturers can schedule maintenance before breakdowns occur, reducing downtime.
- Increased Flexibility: Digital twin technology allows for better planning and process optimization, reducing error.
Read more:
3. Why Are These Innovations Important?
The innovations in plastic machining technology are important for several reasons. First, they help manufacturers meet the growing demand for plastic components in industries such as automotive, aerospace, healthcare, and consumer electronics. As the complexity and precision requirements of plastic parts increase, so does the need for advanced machining technologies.
These innovations also improve sustainability by reducing waste, energy consumption, and the use of harmful coolants. High-speed machines and automation systems increase productivity while reducing operational costs, making plastic machining more cost-effective. Additionally, advanced tooling and cooling methods enhance the quality of machined parts, ensuring that manufacturers can meet stringent quality standards.
Moreover, the integration of digital technologies, such as data analytics and IoT, has transformed plastic machining into a more intelligent and adaptable process. Manufacturers can now monitor and adjust operations in real time, resulting in higher efficiency, reduced downtime, and better overall performance.
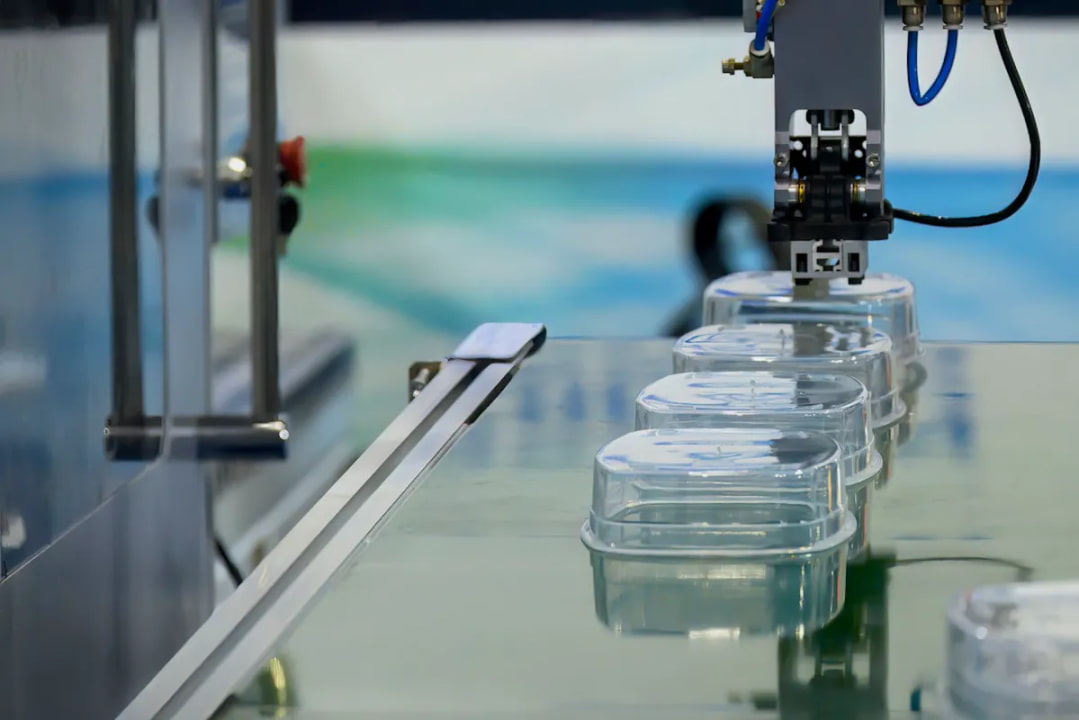
Why Are Plastic Machining Technologies Important
4. Conclusion
Plastic machining has come a long way since its early days of manual cutting and shaping. Advancements in plastics technology, machining technology, and manufacturing practices have made it possible to produce plastic parts that are stronger, more durable, and more precise than ever before.
As we look to the future, it is clear that the process of plastic machining will continue to evolve, driven by new technologies and materials. Whether it is the use of multitasking machines, advanced cooling technologies, robotics, automation, and digitalization, it’s likely that plastic machining will become even more efficient, cost-effective, and flexible in the years to come.
5. About EuroPlas
As the world's No.1 filler masterbatch manufacturer, EuroPlas proudly brings customers unique plastic raw material solutions to help their factories optimize production costs and improve the competitiveness on the market. Some products of EuroPlas include: bioplastic compounds, color masterbatch, plastic additives, engineering plastic compounds, filler masterbatch and bio filler. EuroPlas is committed to delivering customized solutions tailored to meet specific customer needs, ensuring top-tier quality and performance.
For more information and samples, please contact us HERE!