PBT resin is a versatile engineering thermoplastic known for its excellent mechanical properties, chemical resistance, and thermal stability. While PBT offers a robust performance profile on its own, there are instances where blending it with other polymers can yield materials with enhanced characteristics. This article delves into the possibilities of combining PBT with other plastics, exploring the benefits, challenges, and applications of these blends.
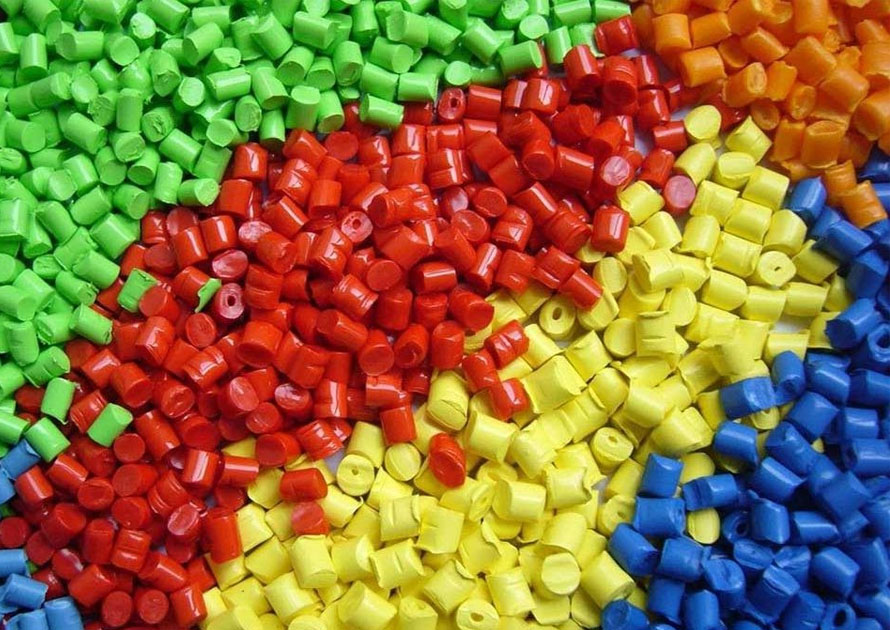
Discover whether PBT resin can be combined with other plastics
1. Overview Of PBT Resin
1.1. What is PBT resin?
Polybutylene Terephthalate (PBT) resin is a high-performance engineering polymer widely utilized for its excellent mechanical and thermal properties.
PBT resin is a semi-crystalline thermoplastic polymer and a member of the polyester family. It offers excellent resistance to solvents and minimal shrinkage during molding. PBT exhibits strong mechanical properties and can withstand temperatures up to 150 °C, or up to 200 °C when reinforced with glass fibers. Flame retardants can be added to PBT to enhance its fire resistance.
PBT resin was initially developed by Imperial Chemical Industries (ICI) in the UK, PBT shares similarities with other thermoplastic polyesters. When compared to polyethylene terephthalate (PET), PBT resin is slightly less strong and rigid but has improved impact resistance and a lower glass transition temperature. Both PBT and PET require UV protection for outdoor use and can be flammable unless treated with specific additives. PBT is synthesized from the polymerization of 1,4-butanediol and terephthalic acid.
It can be seen that PBT resin has some main features as follows:
- Thermoplastic Polymer: PBT resin is a semi-crystalline thermoplastic, making it suitable for various molding applications.
- Chemical Resistance: It resists solvents and chemicals, contributing to its durability in harsh environments.
- Mechanical Strength: PBT resin is mechanically strong, providing excellent structural integrity in finished products.
- Heat Resistance: It can withstand temperatures up to 150 °C, or up to 200 °C with glass fiber reinforcement.
- Low Shrinkage: PBT resin exhibits minimal shrinkage during the molding process, ensuring dimensional stability.
- Flame Retardancy: It can be treated with flame retardants to enhance its fire resistance.
- UV Sensitivity: PBT requires UV protection for outdoor use to prevent degradation.
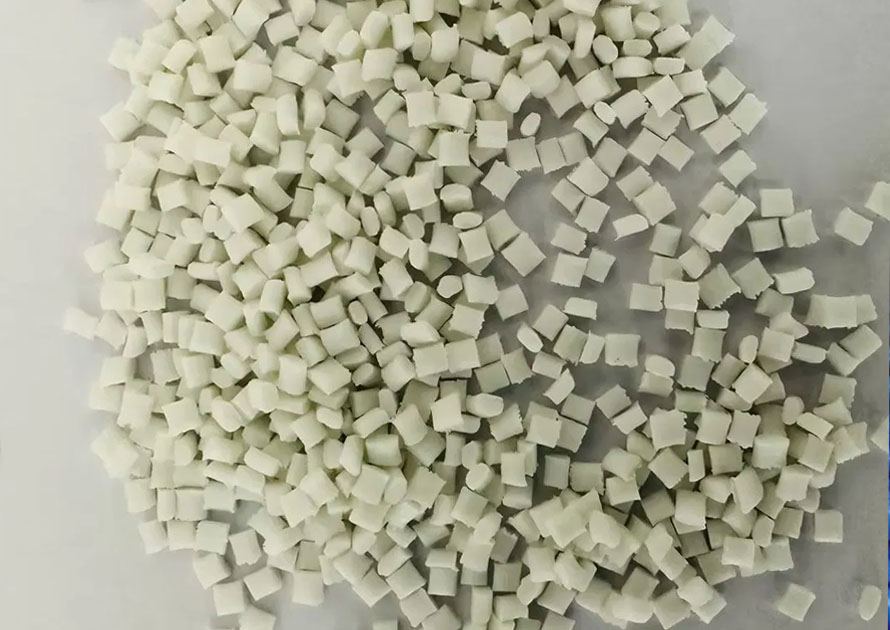
Polybutylene Terephthalate (PBT) resin is a high-performance engineering polymer widely utilized in many different sectors.
Read more:
PC - PBT plastic: definition, properties, applications, and more
Beyond the Basics: The PBT Family You Need to Know
PBT GF30: What is it? Properties, key benefits & uses
1.2. Applications of PBT resin
PBT resin finds diverse applications across multiple industries. In electronics, it serves as a reliable material for enclosures, connectors, and components due to its excellent electrical insulation and dimensional stability. The automotive sector utilizes PBT for parts like plugs, connectors, and even exterior components, benefiting from its durability and resistance to harsh environments. Consumer goods also incorporate PBT, evident in products like showerheads, irons, and toothbrush bristles, where its strength and chemical resistance are valued.
Moreover, PBT resin’s unique properties extend to textiles. Its inherent elasticity and chlorine resistance make it a preferred choice for swimwear fabrics. Recent advancements highlight its superior UV protection compared to similar materials, expanding its potential in outdoor apparel.
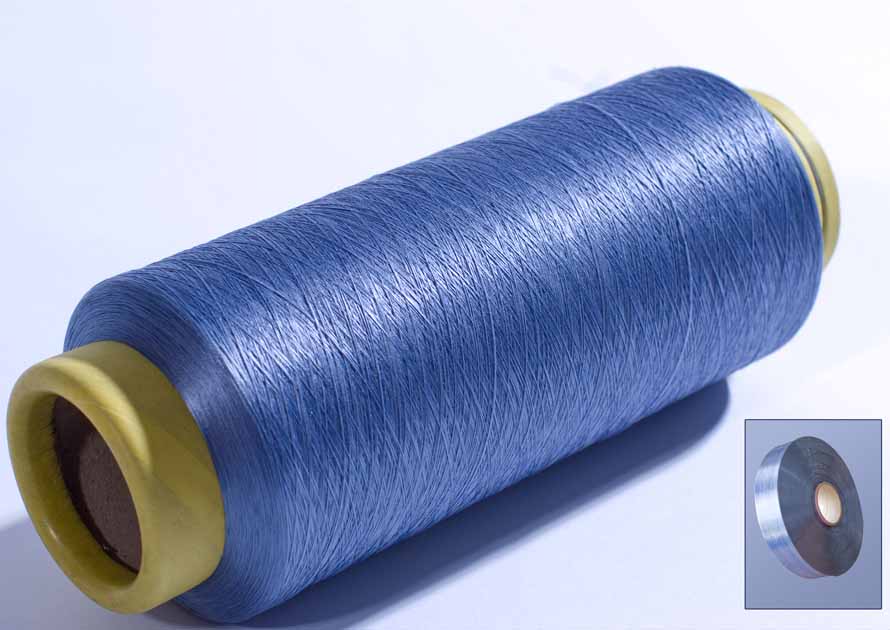
PBT yarns for textiles
For applications demanding fire safety, PBT, particularly when reinforced with glass fibers, can be effectively treated with flame retardants. This characteristic makes it suitable for electrical and electronic components where safety is paramount.
Read more:
Applications Of PBT Compound To All Industries
PBT-GF30 Applications That Are Changing Industries
PBT vs ABS - Differentiation and Comparison
2. Can PBT Resin Mix With Other Plastics?
PBT resin can be mixed with other plastics to create materials with tailored properties, allowing for the combination of desirable characteristics from different resins.
For example, PBT resin can be blended with polycarbonate (PC), acrylonitrile butadiene styrene (ABS), and polyamide (PA). By carefully selecting the blend ratio and processing conditions, manufacturers can achieve materials with enhanced impact resistance, heat resistance, flexibility, or other specific properties.
- PBT resin and PC: PBT mixed with PC plastic creates a material boasting excellent impact resistance, heat tolerance, and chemical stability. This blend shines in demanding applications such as automotive components, electrical connectors, and medical devices, providing enhanced durability and performance in demanding environments.
- PBT resin and ABS: Combining PBT with ABS enhances impact resistance, toughness, and processability. This versatile material excels in applications demanding durability and dimensional stability, such as durable automotive components, robust appliance housings, and reliable electrical enclosures, delivering both functional strength and improved aesthetic appeal.
- PBT resin and PA: Blending PBT with PA plastic results in a material boasting enhanced strength, stiffness, and heat resistance. This combination is ideal for automotive parts, industrial components, and mechanical gears, offering enhanced durability and performance under high-stress and high-temperature conditions.
Additionally, PBT resin can be combined with fillers like glass fibers or flame retardants to further tailor its properties to meet specific industry standards and requirements.
It's crucial to remember that not all polymers work well with PBT resin. Phase separation or material property degradation could result from certain combinations. Therefore, when combining PBT with other resins, considerable thought and testing are necessary.
3. Conclusion
In conclusion, the compatibility of PBT resin with other plastics presents a dynamic landscape of possibilities for material engineers and product designers. By carefully selecting compatible resins and optimizing blend ratios, manufacturers can create novel materials with tailored properties to meet specific performance requirements. The judicious combination of PBT with other resins offers a promising avenue for developing innovative and high-performance materials across various industries, from automotive and electronics to consumer goods.
4. About EuroPlas’ PBT Products
EuroPlas specializes in engineering PBT plastic compounds, meticulously crafted by combining pure PBT resin with a diverse array of additives and reinforcements. These formulations are tailored to meet the exact requirements of various plastic applications. EuroPlas primarily offers two key product lines: glass fiber reinforced PBT (PBT-GF) and flame retardant PBT (PBT-FR).
4.1. PBT-GF compound
The PBT-GF compound boasts enhanced strength and rigidity due to the incorporation of glass fibers. EuroPlas provides a range of PBT-GF options, each distinguished by its unique glass fiber content and fire resistance rating, as classified by the rigorous UL94 standards. These compounds excel in demanding applications within the automotive, electrical, and household appliance sectors, where components such as car parts, motorcycle components, battery turbines, radiator fans, and electrical appliance housings benefit from their exceptional properties.
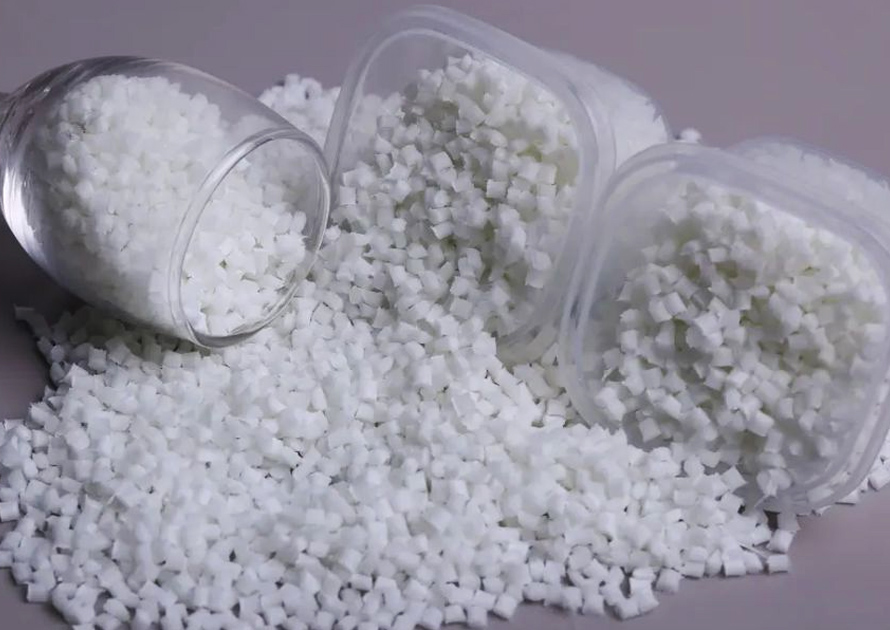
The PBT-GF compound enhanced strength and rigidity due to the incorporation of glass fibers.
4.2. PBT-GF-FR compound
Building on the strengths of PBT-GF, the PBT-GF-FR compound incorporates flame retardant additives alongside glass fibers. This synergistic combination enhances fire safety while preserving the mechanical properties of the compound. EuroPlas’ PBT-GF-FR compounds are tailored to meet the specific needs of applications requiring both fire resistance and structural integrity, making them ideal for components in kitchen equipment, household appliances, electrical engineering, and car interiors.
EuroPlas’ PBT-FR compounds prioritize fire safety without compromising performance. These materials are infused with flame retardants to achieve varying levels of fire resistance, ensuring compliance with industry regulations. Similar to PBT-GF, the PBT-FR range offers diverse formulations to accommodate specific application needs.
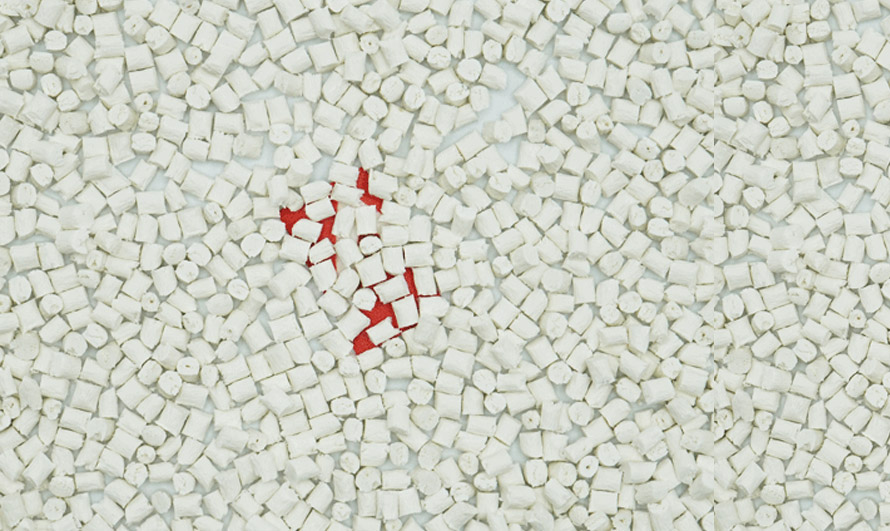
PBT-GF-FR compound incorporates flame retardant additives alongside glass fibers
To explore how our PBT products can meet your specific needs, contact us today for more information.