The utility model pertains to a compound cement bag formed of a woven net made of paper and plastic, of which the center layer is knitted silk made of polypropylene plastics and the inner and outer layers are made of sack paper. Among these, polypropylene is regarded as the most crucial component of the cement plastic bags manufacturing process and affects the packaging's quality. Let’s discover the cement packaging bags material and the comprehensive cement plastic bags manufacturing process in this article.
.jpg)
1. Cement packaging bags material
.jpg)
Cement packaging is a significant factor in cement bags manufacturing process regarding product protection, shelf appearance, cost margins, and sustainability targets. Depending on the preferences and purposes of use, cement bag manufacturers can create it from different materials, but the most common cement packaging bag material is polypropylene plastic. In the next section, let's find out all the information about this material and discover why it is so preferable.
Related: What are Laminating Pouches Made of?
1.1. Cement bag material
Most of the cement bags currently on the market are made from Polypropylene plastic (PP plastic). Thin polypropylene strips are woven in a weft and warp pattern to create PP bags. PP bags, however, may also be non-woven. These bags are made by fusing thin polypropylene strips.
Let's talk about why Polypropylene plastic is often chosen to make cement bags.
Related:
- 4 types of filler masterbatches recommended for packaging industry
- CaCO3 filler in the packaging industry - 5 most common applications
Availability
Jute was used to make packing bags in the past. However, seasonal variations may be seen in jute output. As a consequence, there have been instances when there was a shortage of jute needed to make packing bags.
However, polypropylene polymer is widely accessible all year round. The supply chain will also be long-lasting affected by this. The introduction of Polypropylene plastic material will help the supply chain not be interrupted and thereby, maintain the stability of the supply of cement bags.
Powerful, long-lasting, and resistant to wear and tear
Due to the great tensile strength of polypropylene, it is capable of withstanding the weight of significant amounts of cement without ripping. It is a long-lasting substance due to its durability. As a result, it is feasible to recycle PP cement bags for an extended period of time.
Impermeability to water
When exposed to rain, jute bags quickly get drenched and retain their moisture for a considerable amount of time. Cement is a material that solidifies when it comes into contact with moisture. After it has been set, cement cannot be repaired in any way. In the event that cement comes into contact with moisture while being stored or transported, the cement will be rendered unusable.
Therefore, the material that is used for the packing of cement should be resistant to moisture. Bags made of polypropylene provide a barrier that is watertight and impermeable.
Tear resistance
During the process of shipping cement, the work demands dexterous manipulation of the packing bags. Because polypropylene has an inherent resistance to ripping, handling packed cement is not as difficult as it could otherwise be. The durability of polypropylene packing bags to tear ensures that rats will not chew holes in them while they are stored in warehouses. Polypropylene, when used in this way, protects the inside contents from the risk of leakage as well as deterioration.
Chemical resistance
When cement comes into contact with substances such as alkalis or acids, the product's quality deteriorates. The bags used for packing cement shouldn't disintegrate when they're exposed to chemicals, and they also shouldn't let chemicals make their way inside the bag. Because it is chemically inert, polypropylene is an excellent material for the packing of cement.
Related:
- 5 types of plastic masterbatch are mainly used for packaging production
- Additives in Packaging Industry (5 minutes to Read)
Weatherproof
Cement that has been packaged for shipment might be moved to other areas or at different times of the year. The layer of the packing bag that is exposed to the elements should not be impacted by the shift in temperature. Polypropylene is a weatherproof material. As a result, it is appropriate for use in the packing of cement.
Lightweight
PP cement bags select polypropylene as the packaging material because of the material's low weight. Because of this quality, PP is very simple to work with.
Easy to stack
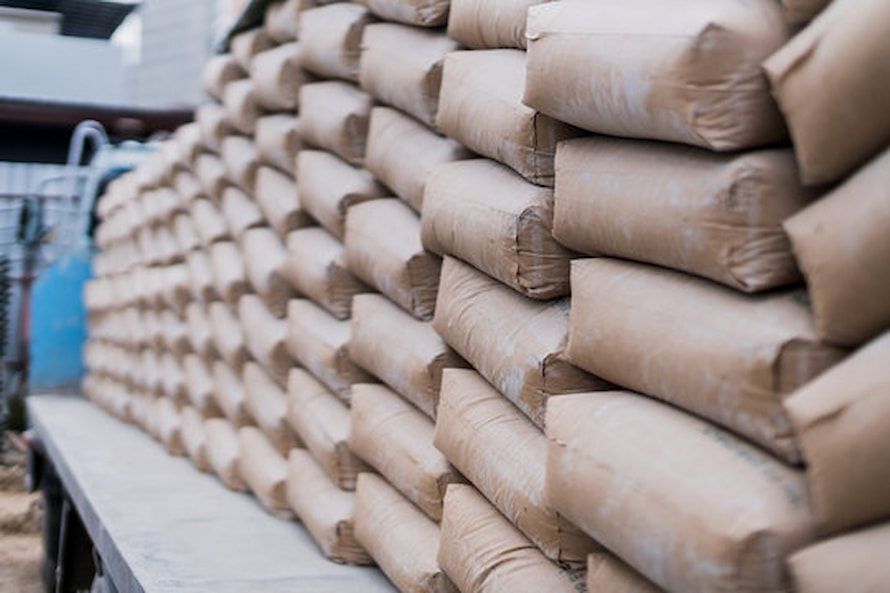
Both anti-static and anti-skid qualities may be found in polypropylene. As a direct result of this, packing bags manufactured from PP are suitable for simple stockpiling in warehouses. PP bags with gusseted bottoms are much simpler to stack.
Affordability
The price of cement bags made from polypropylene (PP) is quite low. There is a wide variety of plastic available for use in packaging. In spite of this, PP is the most affordable of the three.
Customizable
Bags made of polypropylene are quite easy for their manufacturers to personalize. PP bags are simple to color, and manufacturers may make them in a variety of sizes. Printing, lamination, and the inclusion of metalized layers are all options for cement bags made of polypropylene. A business may do a better job selling its goods with the aid of attractive packaging.
Eco-friendly
It is feasible to recycle the polypropylene that was used to make the packing bags since it has a high resistance to breaking down over time. After it has been used several times, a packing bag made of PP may be recycled into other usable plastic objects in an easy way. It's possible that the producers of colorful PP bags may switch to using natural dyes in an effort to reduce their impact on the environment.
1.2. Where to buy these materials?
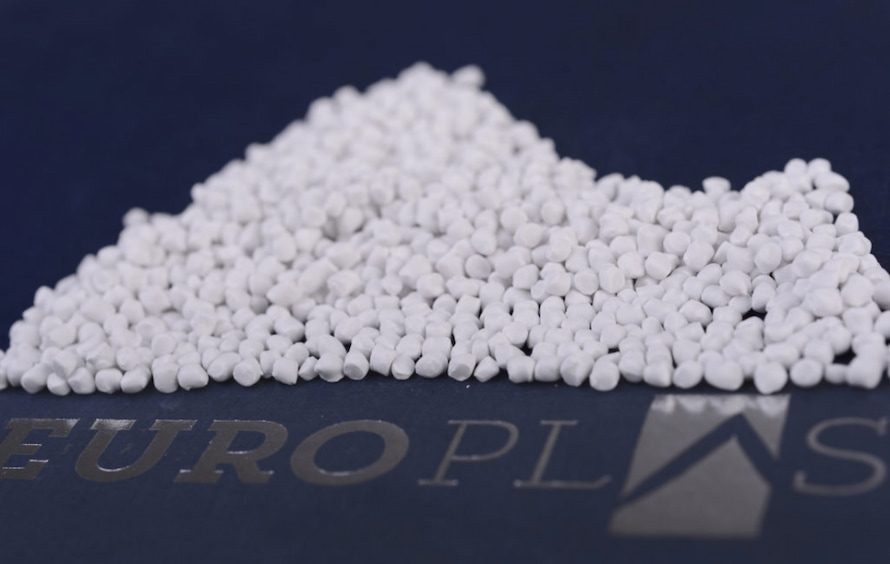
Polypropylene filler masterbatch of the European Plastics Joint Stock Company (EuP) has been trusted by many cement bag manufacturers in Vietnam and around the world. PP filler masterbatch brand EuroPlas is a combination of CaCO3 stone powder, PP base resin, and appropriate additives.
Advantages of PP filler masterbatch from EuroPlas:
- Optimizing production costs
- Contributing to improving some surface features of finished products: increasing hardness, reducing shrinkage,...
- Save fuel thanks to the good thermal conductivity of CaCO3
- Reduce mold cooling time, shorten the production cycle
In particular, PP filler masterbatch is a composite product line, a final material that does not need to be further coordinated, designed specifically for the needs of each customer.
As the world's No. 1 filler masterbatch manufacturer, EuroPlas is proud to offer a unique plastic material solution that helps customers' factories optimize production costs and improve their competitiveness. on the market. EuP is committed to providing the best user experience. Therefore, when choosing our PP filler masterbatch products, customers are completely assured of the product quality and services.
2. Cement plastic bags manufacturing process
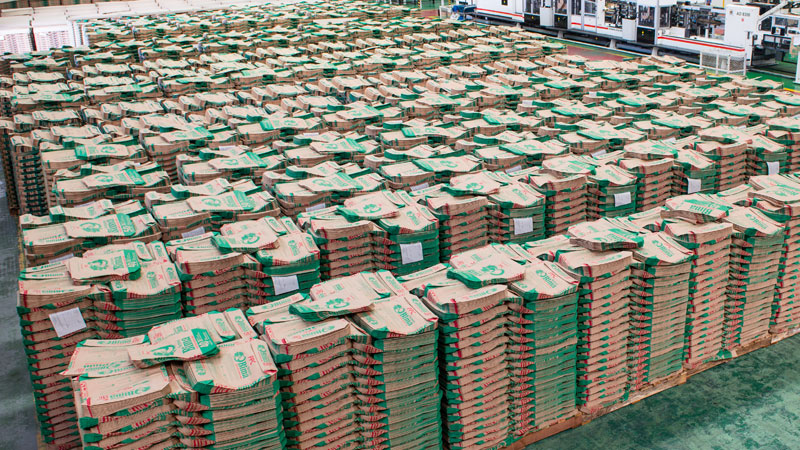
The starting material for the production of PP plastic packaging is plastic masterbatches. Plastic beads mainly used are milky white and transparent colors. If the packaging has colors, it must be mixed with plastic colorants.
Cement plastic bags manufacturing process:
PP yarn –> Woven PP fabric sheet –> Coated PP fabric film –> Printing on PP bags –> Finished products (bottom sewing, mouth sewing, perforating handles).
The cement bag production line is produced under a rather complicated process.
2.1. Make PP yarn
PP plastic granules are loaded into the hopper of the yarn-forming device, by the suction machine put into the extruder, and heated to melt. The screw extruders the liquid plastic to the mold mouth with adjustable length and thickness as required, and plastic film is formed through the forming cooling water bath. Then the film enters the cutter shaft to slit into the required width (2-3 mm), the yarn goes through a heater to be stabilized and then put to the winding machine.
In the process of creating yarn, the fiber wastes and bavia of the plastic film are recovered by suction, cut into small pieces, and returned to the extruder.
2.2. Woven PP fabric sheet
The PP yarn rolls are put into the 06 shuttle circular loom to weave into PP fabric tubes, through the PP fabric winding mechanism.
2.3. Coated PP fabric film
The PP fabric roll is installed by the forklift truck on the film coating machine, the PP fabric sheet is coated with a thickness of 30 PP plastic to increase the bond of moisture-proof fabric. Roll of PP fabric coated and rolled.
2.4. Printing on PP bags
OPP film lamination is the most professional and beautiful bag, gravure printing technology on OPP film, and then grafting this film onto a roll of woven PP fabric.
2.5. Finished product cutting and packing
Non-Printed or Flexo Printed PP Woven Bags: Woven PP rolls are passed through the hip folding system (if any), and the finished product is cut. Then sew first, print later, or sew later, print first. Finished products go through automatic counting conveyor and bales packing.
PP woven bags with gravure printing film in rolls are passed through an automatic system of side folding, edge pressing, cutting, bottom sewing, and packing.
In a nutshell, polypropylene polymer is the material of choice during the cement plastic bags manufacturing process when it comes to the production of packing bags for cement. The storage, transportation, and handling of cement are all activities that benefit from the physical, chemical, and mechanical properties of polypropylene.
If you are looking for a suitable additive for your plastic product, don't hesitate to
contact our team of consultants today for advice and to receive samples!