Carbon black is an important ingredient that gives black masterbatch its characteristic black color. They contribute to increasing the adhesion, UV resistance as well as the durability of black masterbatch particles. In addition, carbon black is also used as a reinforcing agent for rubber products, car tires. Moreover, carbon black also proves its importance in other industries such as electronics to absorb radar or used as a good conductor, anti-static additive in the automobile manufacturing industry. In this article, EuroPlas will emphasize the core role and how to choose and the benefits of carbon black in the production of black masterbatch. Refer now!
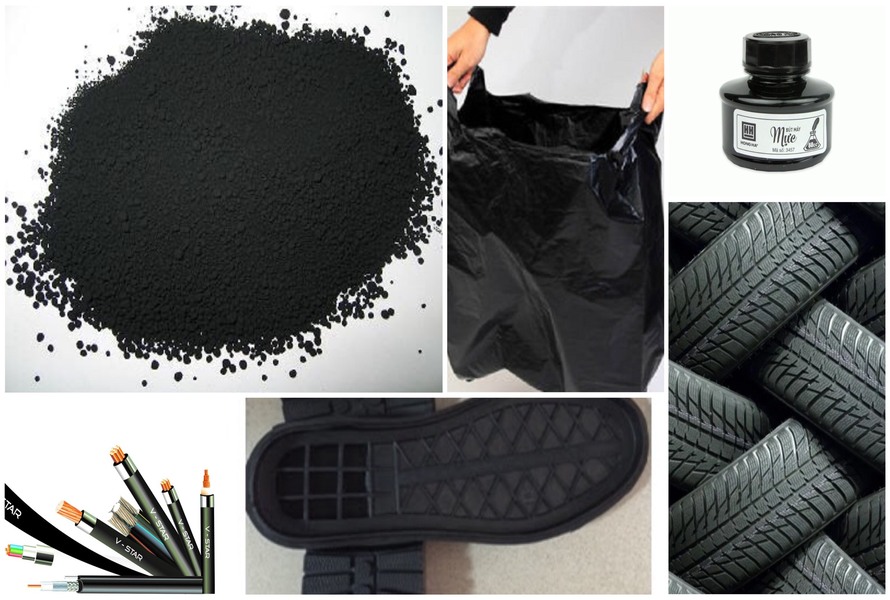
Diverse applications of carbon black in many industries
1. Factors to consider when choosing carbon black.
EuroPlas sends customers the top 3 factors to consider carefully when choosing quality carbon black. Carbon black must ensure: High pigment, low carbon content, good conductivity and electrical resistance.
1.1. Carbon black with high pigment
Basically, carbon black contributes to providing black pigment when combined with virgin resin and other additives. Pigment will directly determine the color and aesthetics of the product. Black masterbatch is required to have an even black color on each particle. Therefore, the color dispersion and pigment of carbon black are strictly tested to ensure quality.
For example, if the color pigment of carbon black is poor, it is difficult to use in the printing industry because the color will be uneven and affect the quality of the entire batch. In the plastics industry, black masterbatch also needs to have a suitable uniform dispersion for applications in electrical and electronic equipment, automotive accessories, agriculture, construction industry and packaging industry. That is why the pigment characteristics are given top priority when evaluating & selecting quality carbon black.
1.2. Low carbon carbon black
This factor needs to be considered very carefully because it is related to the health and safety of workers. The Occupational Safety and Health Administration (OSHA) has issued strict guidelines to ensure that production workers are not at risk of inhaling unsafe doses of carbon in raw form. The basic reason is because carbon black is created from the complete combustion of materials with heavy oil content, such as: Coal tar, ethylene cracking plastic, etc.
In addition, carbon black with high carbon content is classified as a group 2B carcinogen. They will penetrate through the air and directly affect the lungs. Therefore, the production and selection of carbon black are issued with strict regulations on protection.
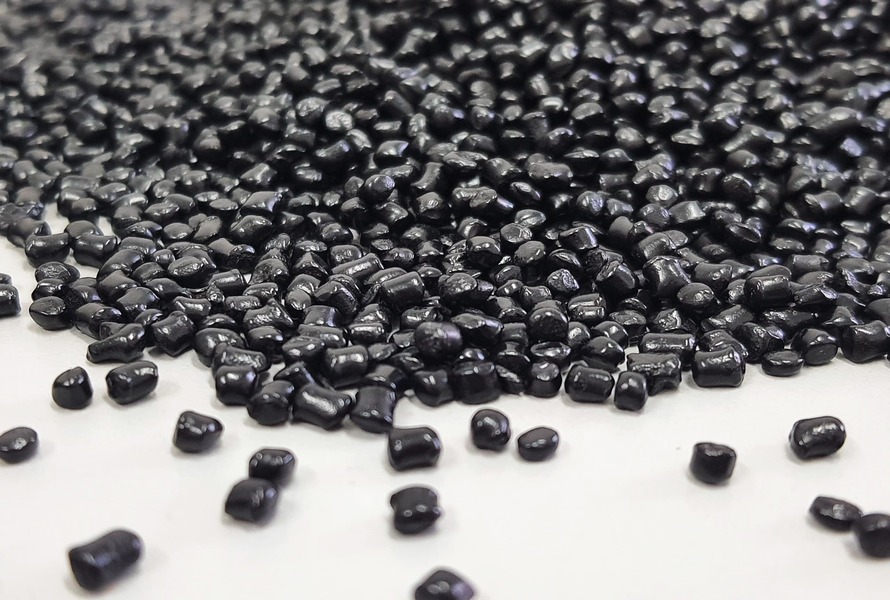
Black Masterbatch produced from carbon black
1.3. Good electrical conductivity and insulation
Carbon black particles are linked together to form chains, and the conduction phenomenon is created by the movement of atoms in the chain. Theoretically, the smaller the carbon black particle size, the more particles per unit volume, which is beneficial to improving electrical conductivity. This is normal in rubber products.
However, when used in conductive plastic products, if the carbon black particles are too small, the dispersion is poor due to the small shear force after plasticization. The performance is reduced and the actual value is lost. Therefore, customers need to evaluate and check the overall size of the carbon black before combining them with other raw materials.
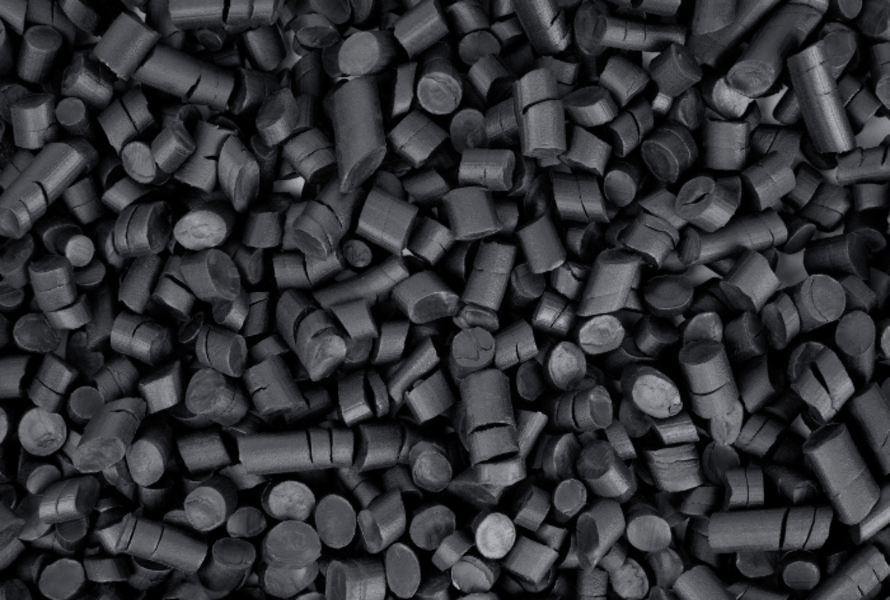
Carbon black provides stable anti-static and conductive properties
2. Common types of carbon black in black masterbatch production
Currently, there are 3 common types of carbon black used in black masterbatch production, namely N330, N326 and N550. EuroPlas will analyze the advantages and practical applications of each type. Specifically as follows:
2.1. Carbon black N330
Carbon black (Carbon black N330) stands out with its mechanical properties as well as diverse applications in many fields. Dispersion, adhesion and durability are 3 factors that are well evaluated in N330 material. Therefore, they are commonly used in the production of plastic films, plastic pipes and engineering plastic products. These are products that emphasize the adhesion and dispersion of the material to form the quality of the final product.
2.2. Carbon black N326
Carbon black N326 is the perfect choice for black masterbatch applications in fields requiring high mechanical strength as well as stable abrasion resistance such as: Automotive equipment, electronic equipment or rubber industry. The dispersion of N326 is also highly appreciated by manufacturers and is similar to N330.
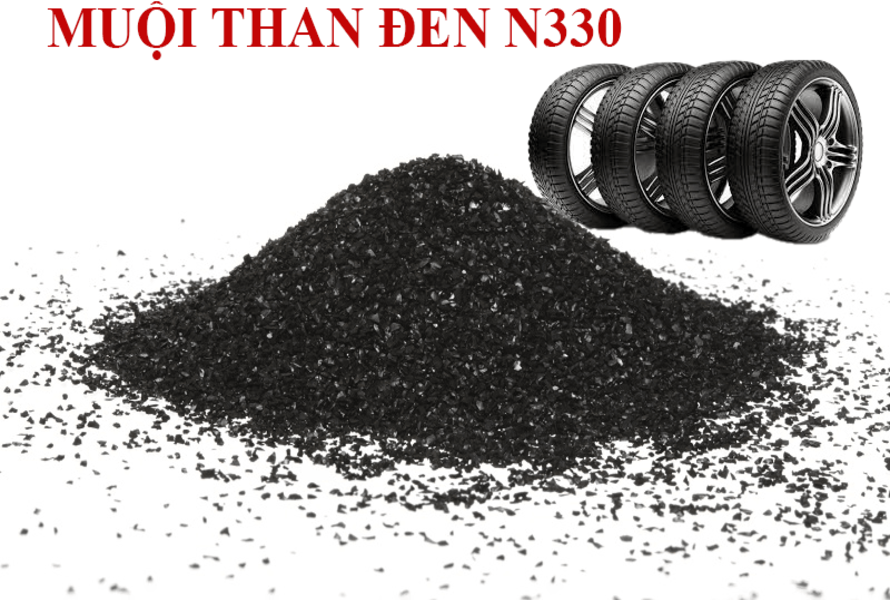
Black carbon black N330
2.3. Carbon black N550
This is the carbon black line with the best dispersion of all 3 types. Therefore, they are suitable for products that emphasize aesthetics and surface smoothness. However, if we consider the mechanical strength, impact resistance and abrasion resistance of black masterbatch plastic fillers, N550 is somewhat inferior to N326 and N330.
In general, all three types of carbon black N330, N326 and N550 have their own advantages and disadvantages. Therefore, they will maximize their performance if combined with quality virgin plastic materials and suitable additives when producing black masterbatch. In addition, customers need to clearly understand the characteristics of their industry and products to choose the most suitable type of carbon black.
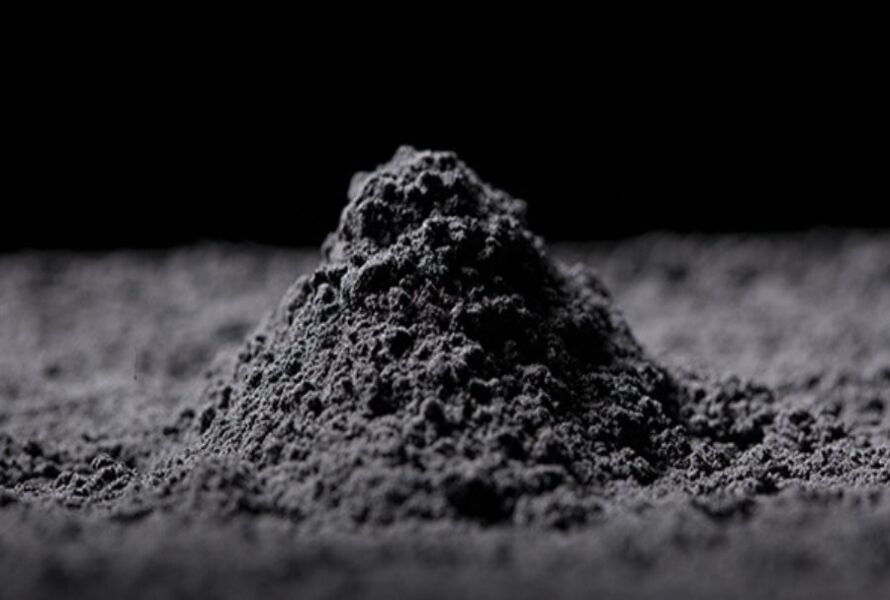
Carbon black N550 has good dispersion
3. Benefits of choosing the right carbon black
EuroPlas has suggested to customers 3 factors to consider before choosing carbon black. Therefore, if customers can choose a quality carbon black, it will maximize its function throughout the production process of finished products. Specifically as follows:
-
Carbon black is outstanding in its ability to create black color for plastic raw materials or final products. Adding carbon black to colored plastic particles helps create good black color for plastic products, so it is an essential ingredient for many applications such as automobiles, insulation products and many other industrial applications.
-
In addition, quality carbon black will have stable adhesion and higher durability when combined with virgin plastic and other additives. Therefore, they can be used in the production of electronic equipment, circuit boards or technical plastic products.
-
In addition, choosing quality carbon black helps manufacturers reduce the cost of producing black masterbatch. This is certainly an advantage of color masterbatches over engineering plastic compounds. Despite the fact that both are in the form of masterbatches, the compounds are significantly more expensive due to their complex manufacturing processes. On the other hand, carbon black masterbatch is easy to produce in large quantities, making it the best choice for coloring processes
-
There are 3 common types of carbon black and they possess different unique characteristics. Therefore, customers need to understand their characteristics to apply them to different industries. For example: N550 carbon black will be suitable for products that require technical factors, while N330 and N328 carbon blacks will be suitable for products that require high mechanical strength.
-
In particular, standard carbon black will ensure stable resistance and conductivity over a long period of time. This is an outstanding advantage that allows them to become important materials in the production of electronic devices and ensures safety during use.
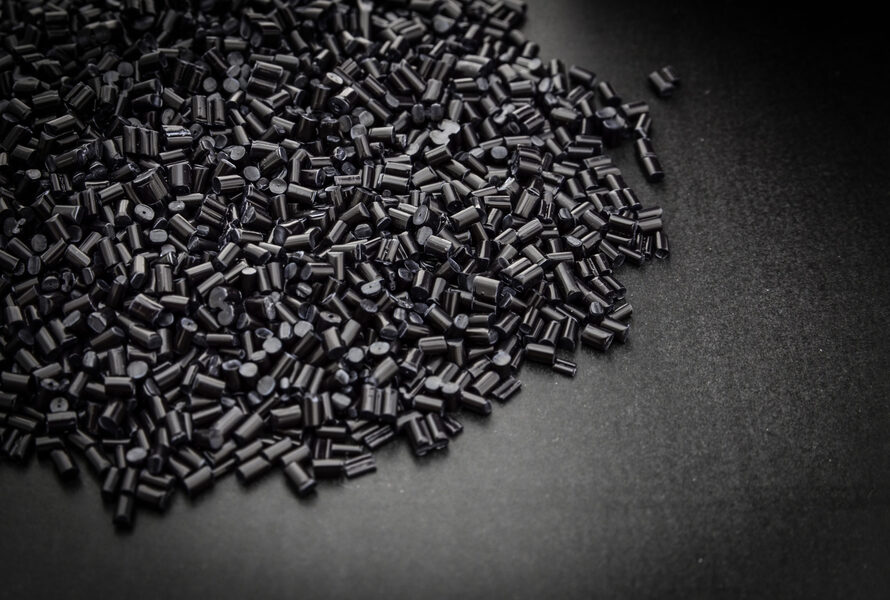
Carbon black contributes to increasing the durability of black masterbatch
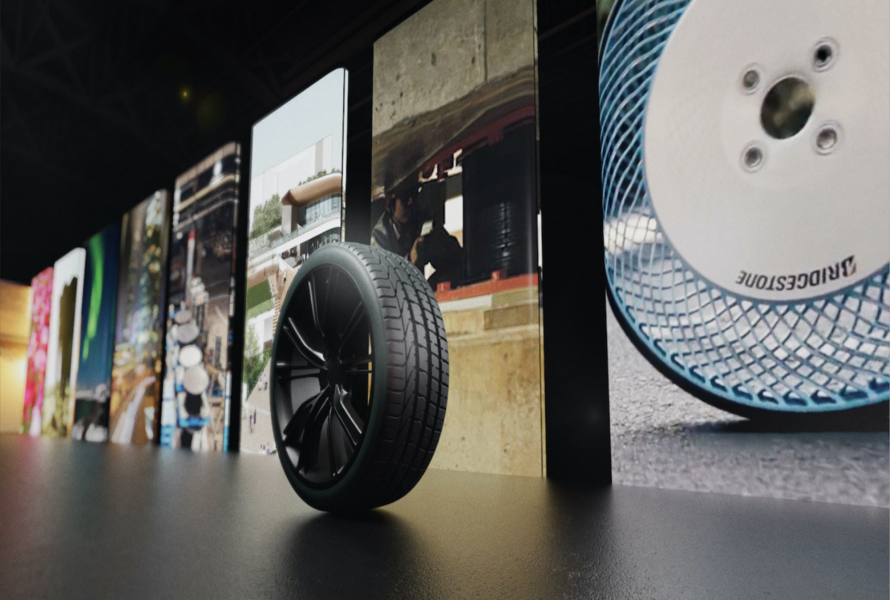
Carbon black used in making tire casings
4. Conclusion
EuroPlas has introduced to customers in detail the importance and practical applications of each type of carbon black. In particular, our team has given 3 factors to note & consider before choosing quality carbon black. EuroPlas hopes that the above knowledge will help customers throughout their production process and don't forget to follow EuroPlas Blog to quickly update knowledge & news about the global plastic raw material market!
5. About EuroPlas black masterbatch products
EuroPlas is proud to be one of the prestigious manufacturers of filler masterbatch in the Vietnamese market. We provide many types of black masterbatch with suitable mechanical properties for different applications.
Black masterbatch at EuroPlas is produced from 3 main components: carbon black, virgin resin and suitable additives. EuroPlas black masterbatch products possess 4 core advantages as follows:
-
Create black color according to the requirements of the finished product
-
Good dispersion High color fastness, good heat resistance
-
Contribute to improving the features of the final product such as UV resistance
-
Diverse color shades depending on customer requirements.
In addition, EuroPlas also strictly inspects the specifications of black masterbatch products as follows:
-
Color: Black
-
Additives: Dispersants, processing aids
-
Processing temperature: 160 - 280°C
-
Particle size: 3 (± 0.3) mm
-
Packaging: 25 kg/PP or PE bag
-
Storage: Keep in dry conditions
-
Recommended usage rate: 2 - 5%