I. What are engineering plastics?
1. Engineering plastic definition
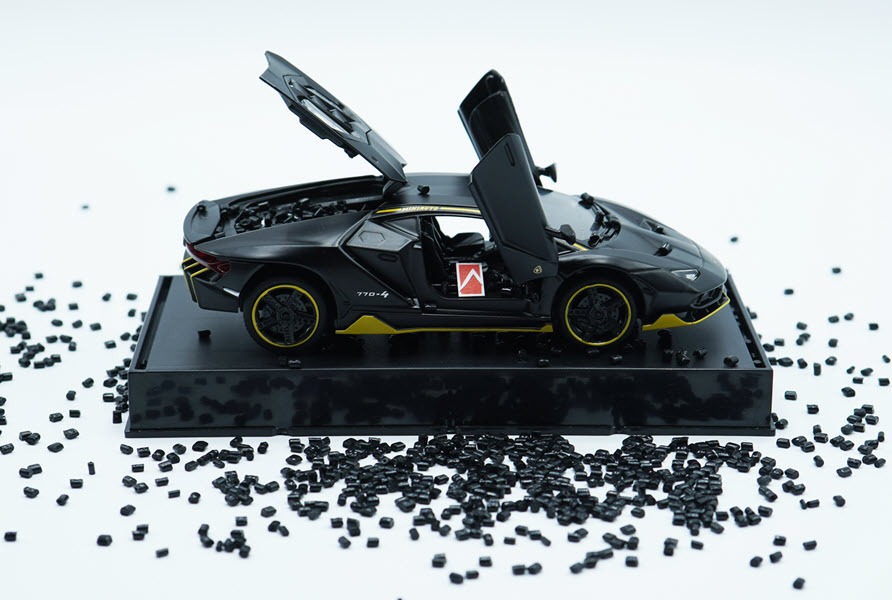
Engineering plastics are plastic materials that have better mechanical, chemical, optical, and thermal properties than standard plastics. In addition, they also have dimensional stability, low flammability, and reduced shrinkage.
When it comes to engineering plastic, it usually refers to thermoplastic materials rather than thermosetting ones. Engineering plastics are easy to process, especially in complicated shapes. Therefore, they tend to be used in structural applications that require high detail such as mechanical parts or automotive interiors, rather than bulk and high-volume products like containers or packaging.
Engineering plastic is a general name, it is not a specific type of plastic with fixed composition and properties. It depends on the specification of the finished product to create a custom-engineered plastic for that product.
Related:
- 5 types of engineering plastic compounds for technical components
- What is compound engineering plastic? Prestigious compound engineering plastic companies in Vietnam
2. Engineering plastic materials properties
Because it is synthesized according to the request of customers, engineering plastic materials have many outstanding properties. It is highly resistant to the objective effects of nature or subjectively caused by man. Therefore, engineering plastics are applied in many areas of life.
The most prominent characteristics of engineering plastics can be mentioned as follows:
- Good mechanical properties
- Excellent machinability and dimensional stability
- Good chemical resistance
- Good wear resistance
- Reduce shrinkage and enhance thermal resistance ability
- Optical properties
- Low flammability
- Water repellent
- Sliding properties
- Electrical properties
Related: Important applications of engineering plastic compound in automotives
In addition, this material has a variety of other properties to assist in the production of finished products with high quality and finishing requirements. Each characteristic will be present in a specific engineering plastic and is suitable for a different end product.
3. Types of engineering plastic
3.1. Polycarbonates (PC)
PC plastic is a group of thermoplastic polymers that contain carbonate groups in their chemical structure. They are easy to machine or mold to the desired shape.
PC has high strength and impact resistance, high dimensional stability, chemical and heat resistance, and especially very high optical properties.
Applications:
Safety helmets, outdoor roofing sheets, aircraft cabin glasses, signal lights, CDs and DVDs, automotive industry, electronics, and eyewear lenses.
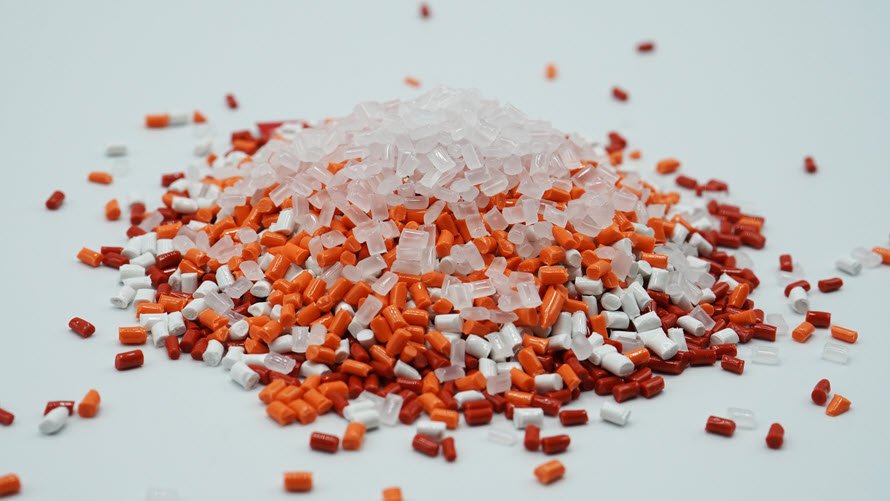
PC engineering plastic
3.2. Acrylonitrile Butadiene Styrene (ABS)
ABS plastic is an amorphous polymer and a thermoplastic. It is formed by the polymerization of acrylonitrile and styrene together with the additive polybutadiene.
ABS offers properties such as heat resistance, fire resistance, chemical resistance, electrical insulation, easy coloring, impervious surface, impact strength, etc.
Applications:
Computer keyboards, control panels, wheel covers, and bumpers,...
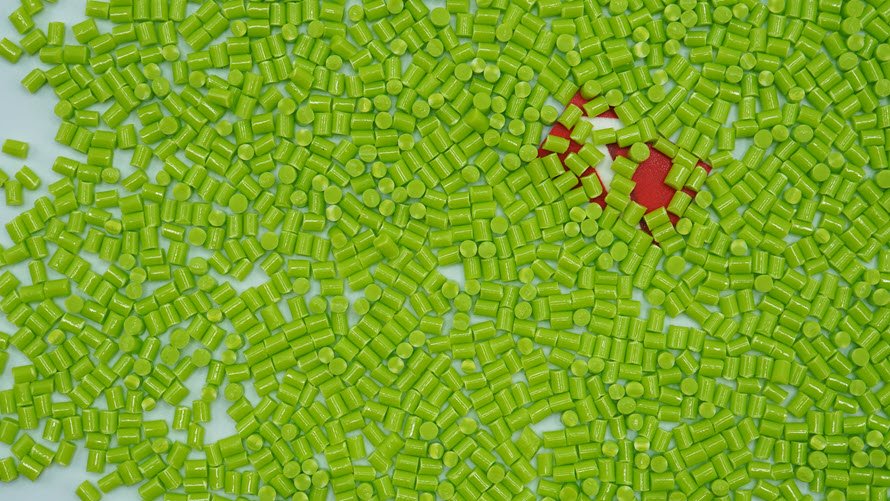
ABS engineering plastic
3.3. Polymethylmethacrylate (PMMA)
PMMA, also known as acrylic, is a hard plastic with highly transparent, very good resistance to ultraviolet radiation and weather. It can be easily colored on demand, molded, cut, drilled, and shaped.
PMMA has high surface strength, temperature performance, chemical resistance, and excellent wear resistance. In particular, with its high optical transparency, it is an excellent substitute for glass in many applications.
Applications:
Car windows, motorcycle windshields, roof covers, TV screens, laptop screens, smartphone screens,...
3.4. Polyphenylene Oxide (PPO)
The list of common engineering plastic materials also includes PPO. This crystalline thermoplastic offers high hardness, impact strength, abrasion resistance, good dimensional stability, and electrical properties.
In addition, PPO can be used to improve water-repellent and high-temperature resistance.
Applications:
Water pumps, welding machine housings, gears, pipes, medical surgical instruments, automotive interiors, electronic components, and mechanical parts,...
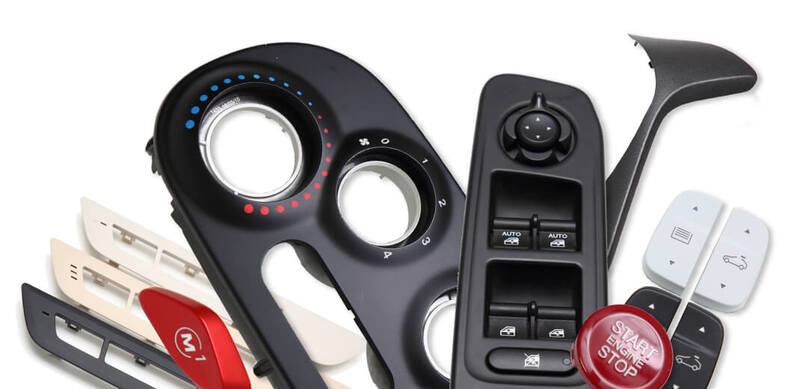
Applications of PPO engineering plastic in automotive interiors
3.5. Polyoxymethylene (POM)
POM plastic is divided into two types, Homo-formaldehyde and Co-formaldehyde. Homo-formaldehyde is obtained by the polymerization of polyoxymethylene. Co-formaldehyde is the copolymerization product of trioxymethylene and a small amount of dioxolane.
The force resistance of POM is good, similar to the hardness and force resistance of the metal. In addition, it has the properties of good electrical insulation, good dimensional stability, good self-lubricating properties, and high rigidity and elasticity.
Applications:
POM is mainly used for gears, screws, auto parts, bearings, electronic devices, pipes and fittings, precision instruments, and construction materials,...
3.6. Polybutylene terephthalate (PBT)
PBT resin is a semi-finished thermoplastic material. It is a member of the polyester polymer family. PBT is produced by the polymerization of terephthalic acid or dimethyl terephthalate.
PBT is less elastic during forming, and heat resistant up to 150°C or 200°C with fiberglass reinforcement. It also can be reinforced with flame retardants to make it non-combustible.
Applications:
Windshield wiper housing, mirror housings, air vents, handles, fans, fuel system components, fuse boxes, engine components, and ignition system components,...
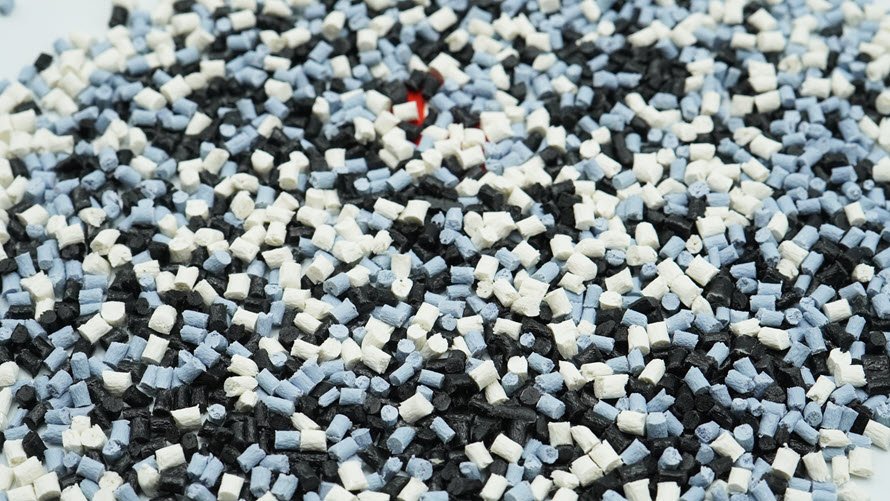
PBT engineering plastic
3.7. Polyamide (PA)
PA plastic, also known as nylons, is the most known and widely used plastic product on the market today. PA is a long polymer chain, containing amide units. These polymers are obtained by polymerization of acid with amides.
PA stands out for its high hardness, good strength, good corrosion resistance, easy processing, high glossiness, non-toxicity, and easy mixing.
Applications:
Pump fans, propellers, bearings, hot and cold air conditioning valves, and automotive power tools. Also, PA is the plastic with the largest consumption rate in the automotive, electrical, and electronic industries,...
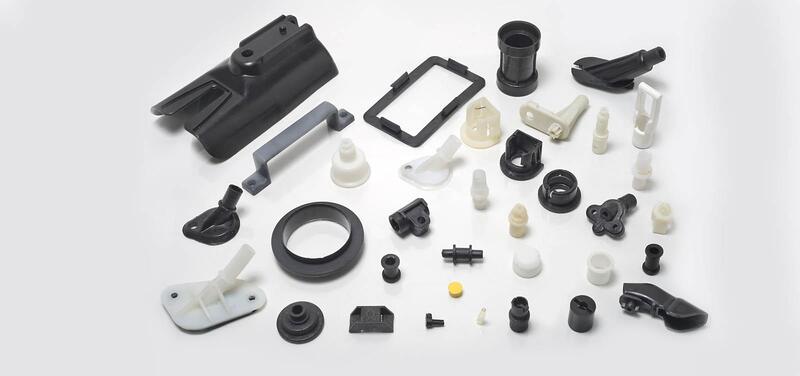
Some applications of PA engineering plastic
3.8. High Impact Polystyrene (HIPS)
HIPS belongs to the group of thermoplastic PS. This plastic is formed from a polymerization reaction. HIPS plastic is usually transparent and easy to shape.
HIPS plastic has properties such as waterproof, hard and brittle, and extremely good electrical insulation. However, it is easy to carry static electricity, and easy to collect dust on the surface.
This type of engineering plastic is odorless, does not contain harmful substances, and does not allow bacteria to grow, so it is often used in the production of food containers.
Applications:
Boxes, candy trays, yogurt jars, yogurt jars, disposable cups, and plates,...
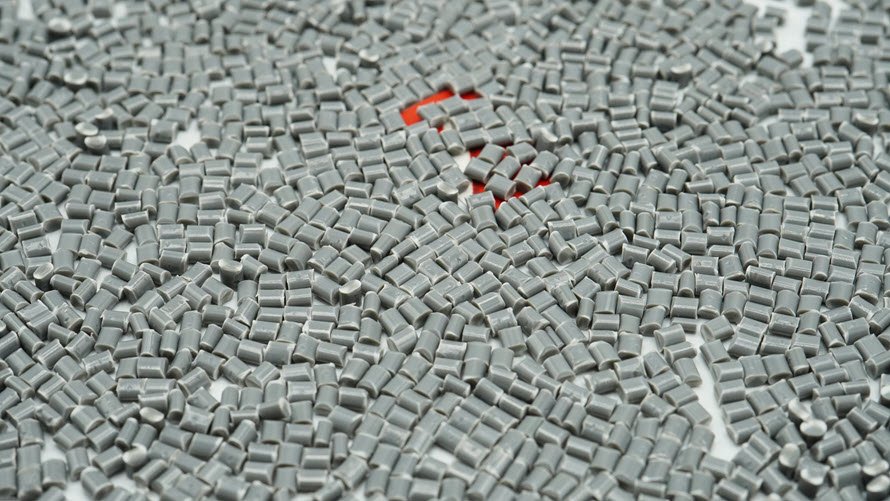
HIPS engineering plastic
3.9. Polypropylene (PP)
PP is a thermoplastic derived from propene gas with the smallest specific gravity so it is very light.
PP is stable and resistant to chemicals and heat. Because PP is odorless and does not cause skin irritation, it is widely used in the food and pharmaceutical industries.
Applications:
Food packaging, electrical appliances, auto parts, construction, garden furniture, artificial lawns, suitcase covers, medical equipment, and plastic bags,...
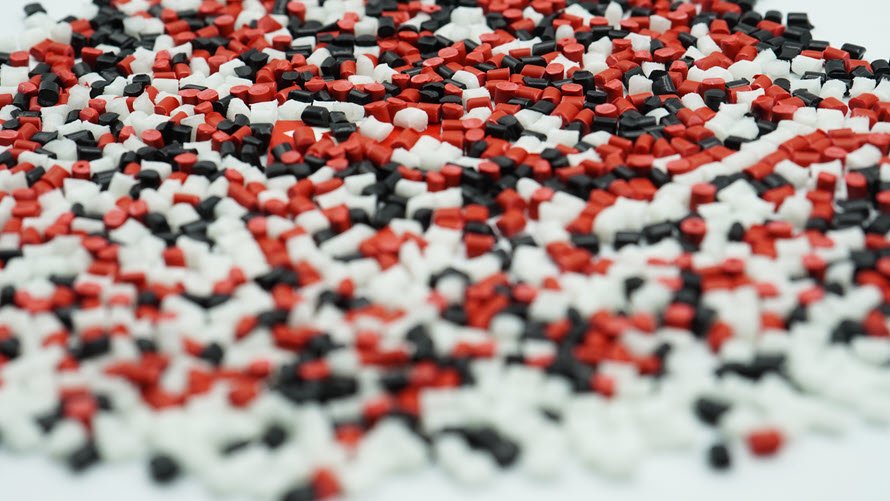
PP engineering plastic
3.10. Polyethylene terephthalate (PET)
PET is a polycondensate of the polymer family made from terephthalic acid and ethylene glycol.
PET is a transparent and lightweight material. It has impact resistance, heat resistance, chemical resistance, and solvent resistance. Besides, it is anti-moisture, anti-alcohol, and dimensionally stable. PET is one of the most recycled thermoplastics today.
Applications:
Plastic bottles, packaging for food and cosmetics, household appliances, gas machines, and seat belts,...
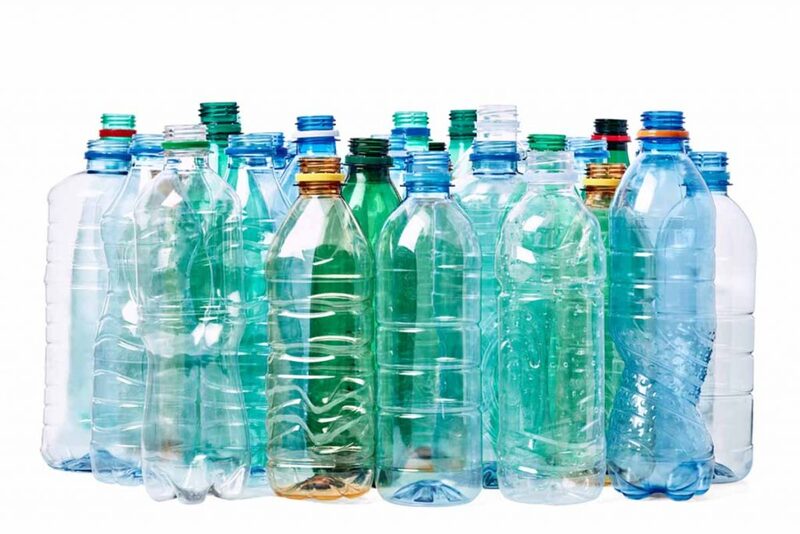
The most popular application of PET plastic
3.11. Polyphenylene sulfide (PPS)
PPS is a special engineering plastic, PPS is usually white and has high crystallinity. Today, PPS is commonly used as a high-performance thermoplastic.
PPS is chemical and heat resistant, it still works well in high-temperature environments from 240°C to 260°C. At high temperatures, PPS retains good mechanical properties, hardness, anti-corrosion properties, good dimensional stability, high energy radiation resistance, UV resistance, flame retardant, and electrical insulation.
Applications:
Sockets, motor housings, fuses, recorders, radios, computer housings, tachometers, printers, and cameras. Especially due to its ability to resist radiation, PPS is used in the production of magnetic therapy devices.
3.12. Polyetherketone (PEK)
PEEK is a very heat-resistant plastic produced by extrusion molding polyetheretherketone resins. The allowable operating temperature of PEEK plastic can be up to 260°C for many hours, even at 310°C for a short time.
PEEK has many mechanical properties like good hardness, corrosion resistance, good friction resistance, dimensional stability, UV resistance, radiation resistance, fire resistance, and low smoke when burning.
Applications:
Surgical equipment, medical machinery, printed circuit boards, connectors, pump parts, and aircraft components,...
II. Engineering plastic compounds from EuP
To produce a plastic product, manufacturers need a formula that mixes virgin resin, additives, filler masterbatch, and some other ingredients to meet the requirements of the end product's properties. Sometimes, this mixing input material does not bring the desired effect and takes time. To address the problem, plastic manufacturers offer engineering plastic materials which is a full-function-in-one-material solution for end-products.
As mentioned above, engineering plastic materials are mainly ordered by plastic product manufacturers to meet end-product performance requirements. Therefore, engineering plastic is an input material with much higher compatibility with the end product when compared to traditional plastic materials.
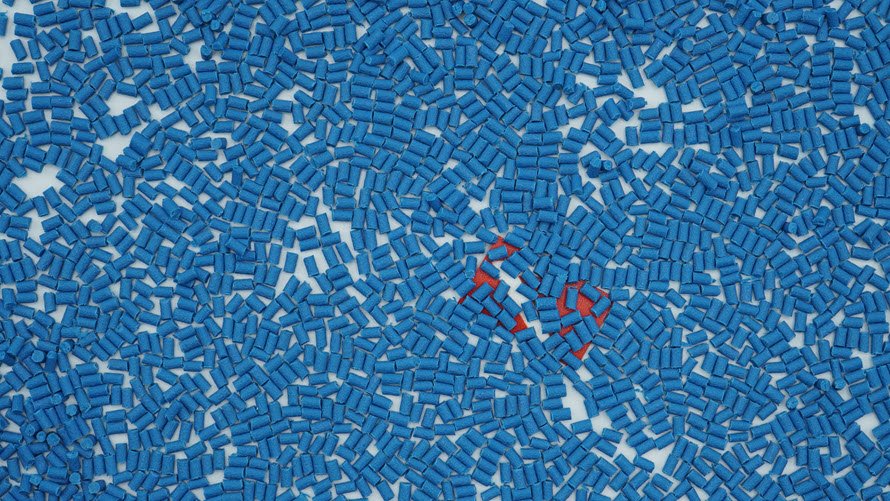
Engineering plastic compound from EuP
European Plastics Joint Stock Company (EuP) is a high-quality engineering plastic supplier which is trusted by thousands of customers around the world. EuP's engineering plastic compounds are diverse in types and properties including:
- PBT GF-FR compound
- PA6 & PA66 blend compound
- PA6 & PA66 glass fiber compound
- PC flame retardant compound
- PC glass fiber compound
- HIPS flame retardant compound
- HIPS conductive compound
- ABS antistatic compound
- ABS glass fiber compound
- PP flame retardant compound
- PP conductive compound
- PP BaSO4 compound
- PP talc compound, etc.
Other than that, there are many other types of engineering plastic with outstanding properties that are researched and manufactured by EuP based on customer requirements to match their product requirements. Contact us for more details, we’re more than happy to help!