Vacuum forming involves the use of heat and vacuum pressure that are used to act on the sheets of plastic that will be formed into certain designs. Depending on the choice of clear plastic, the quality of the final item, its clarity, and even its lifespan can vary greatly. This article speaks of the best clear plastics to use in vacuum forming.
Read more: Vacuum forming plastic - The ultimate guide
1. Top Clear Plastics For Vacuum Forming
1.1. Polyester
Polyester, especially PET, is a clear plastic commonly used in vacuum forming because of its good clarity, as well as good toughness. It has a medium heat resistance and a certain level of shrinkage in the forming process of fur production. It can, therefore, be used for products that do not need high heat resistance, however, the forming conditions should be properly controlled.
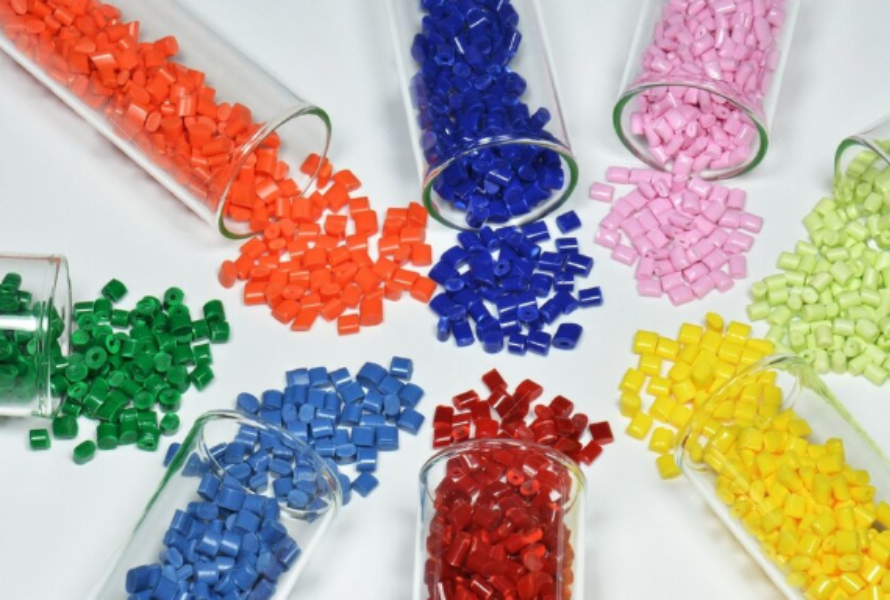
Polyester's combination of clarity, rigidity, and thermoformability make it a popular clear plastic for a variety of vacuum-formed products.
1.2. Polypropylene
Polypropylene (PP) as a clear plastic used in vacuum forming is another remarkable material taking into account its valuable properties: low melting point – 160-170C, which enables it to shape easily and create multiple forms. PP is also light in weight and rigid with chemical & impact resistance which is quite appropriate for vacuum forming.
1.3. HDPE
High-density polyethylene (HDPE) is a clear plastic, very rigid and impact-resistant plastic that is very effective for vacuum forming. Moreover, the molecular structure of HDPE is more crystalline and therefore it is harder to stretch and form as compared to LDPE. This increased rigidity is a disadvantage but it offers more stiffness and structural strength in the final vacuum formed part.
1.4. LDPE
LDPE is generally a flexible and pliable clear plastic material that has good chemical resistance. However, its clarity is significantly lower compared to other film types. Hence, LDPE is normally unsuitable for vacuum-formed products if the main focus is placed on the aesthetics of the final product.
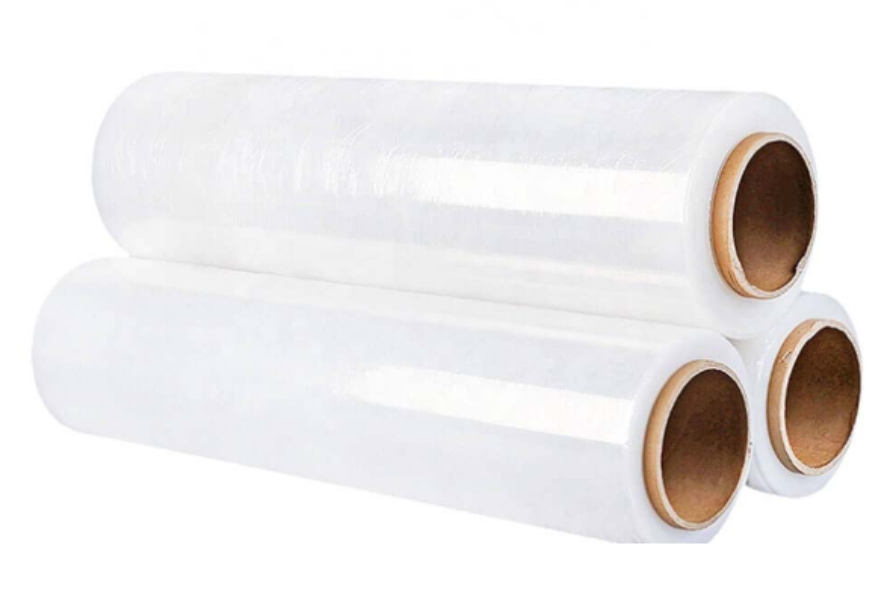
LDPE (Low-Density Polyethylene) is another clear plastic material that can be used for vacuum-forming applications.
1.5. Polystyrene
Polystyrene or PS is reasonably priced and easy to form and process; this clear plastic has good clarity also. But, it has relatively low impact resistance which might be a problem in areas where items are subjected to heavy blows. The vacuum-formed product using this clear plastic might be easy to use especially if the application will not demand high-strength properties.
1.6. ABS
ABS is another highly utilized thermoplastic due to its good impact strength and relatively high rigidity about comparative thicknesses for a vacuum-forming material. Although the fact is that its transparency is not very high and makes only a moderate level, this clear plastic can be rather an optimal balance between optical and mechanical characteristics.
1.7. Acrylic
PMMA or Acrylic is a clear plastic that is specifically suitable for vacuum forming because of the material’s high light transmission and transparency. This clear plastic also has high rigidity and impact strength and is acknowledged for its good thermoformability. Acrylic is commonly used in products that are vacuum formed where clarity is a major consideration.
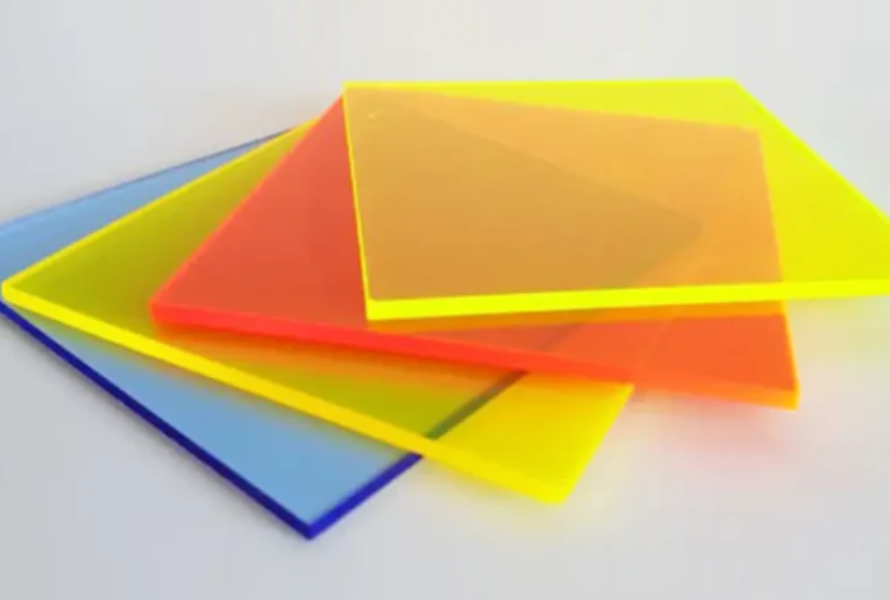
Acrylic is a suitable clear plastic for vacuum-forming applications, which requires high transparency.
1.8. Polycarbonate
Polycarbonate or PC is known to be a highly impact-resistant and heat-tolerant clear plastic that also makes a great choice for vacuum forming. It also has a good light transmission, therefore making it suitable for products that are expected to endure high stress and at the same time deserve to be aesthetic.
1.9. Kydex
Kydex on the other hand is a type of thermoplastic that is highly rigid, very durable, and is characterized by high clarity and a glossy surface. Due to the highly effective chemicals and impact resistance, this clear plastic becomes ideal for vacuum-formed end products that are likely to encounter difficult operating conditions or be used frequently.
2. Factors To Consider When Choosing Clear Plastics
2.1. Optical clarity
The clarity for many vacuum-formed products is dependent on the optical quality of the plastic. Some of the clear plastics that can be used are acrylic, polycarbonate, and some grades of PETG while other materials such as polypropylene as well as polyethylene are relatively opaque as compared to the former.
2.2.Impact resistance
Impact resistance is another property that defines the ability of clear plastics to resist impact or shock before being used in certain applications. The impact strength of clear plastic is high in polycarbonate and ABS while the materials such as polystyrene show comparatively low impact strength.
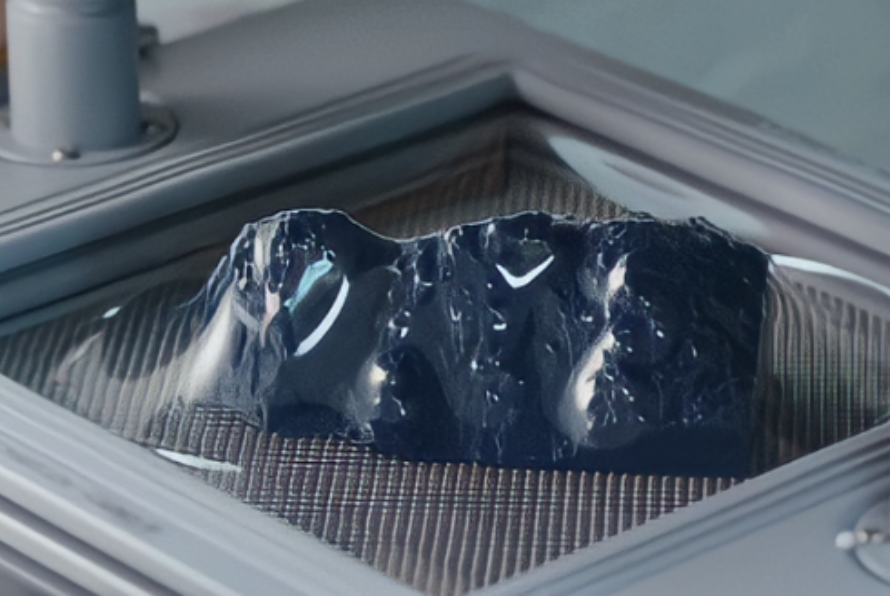
Depending on the application, the clear plastic may need to withstand impacts or stresses, so impact resistance is an important property.
2.3. Thermal properties
The heat tolerance and the coefficient of thermal expansion of the plastic are components that influence its adoption for vacuum forming. Some types of clear plastics that shrink and deform at higher temperatures or chemically degrade when heated include ABS and PVC, while others that do not shrink or degrade when heated include polycarbonate and acrylic.
2.4. Chemical resistance
In some cases, such as in the environment where it may be exposed to chemicals, solvents, and other products, the resistance of the plastic may be a relevant factor. For instance, Polypropylene and HDPE, have a very high chemical resistance whereas some other clear plastics are somewhat susceptible to certain chemicals.
2.5. Dimensional stability
This characteristic is useful for applications that require a high degree of dimensional stability in the clear plastic part after forming. Nonshrinkable materials that include Acrylic and ABS plastics are best suited for vacuum forming as they do not warp easily.
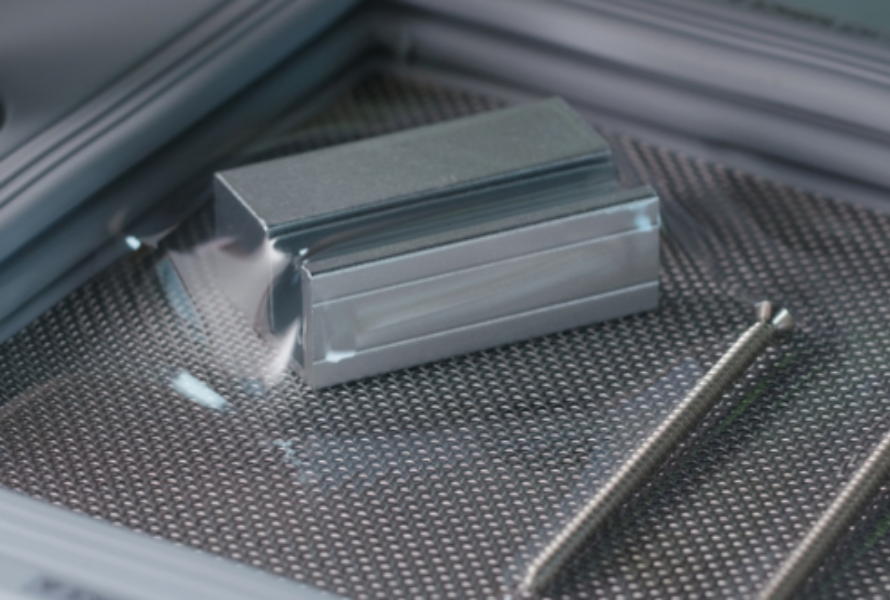
Dimensional stability is an important factor to consider when choosing clear plastics for vacuum forming applications.
2.6. Cost and availability
The cost and availability of clear plastic can also pose some challenges, especially to companies that deal with large volumes of production. Cheaper options such as polystyrene and high-density polyethylene may be applicable depending on the setting, while other materials like Kydex may be costly.
3. Conclusion
Where to buy the best clear plastic for vacuum forming that will suit your project is determined by the degree of transparency required, the expected impact or the temperature conditions of the area of applying the clear plastic, and the affordability.
Conducting a comparison of samples of these materials and undertaking tests will enable you to make the right decision. Finally, understanding the material characteristics of clear plastic and the requirements of the project will help one choose the right plastic for the vacuum forming process.
4. About EuroPlas
As a successful masterbatch supplier company, EuroPlas offers a wide range of solutions related to clear plastic in vacuum forming, that are bendable, of the highest color quality, and include all the desired functions in one material.
4.1. PP Compound
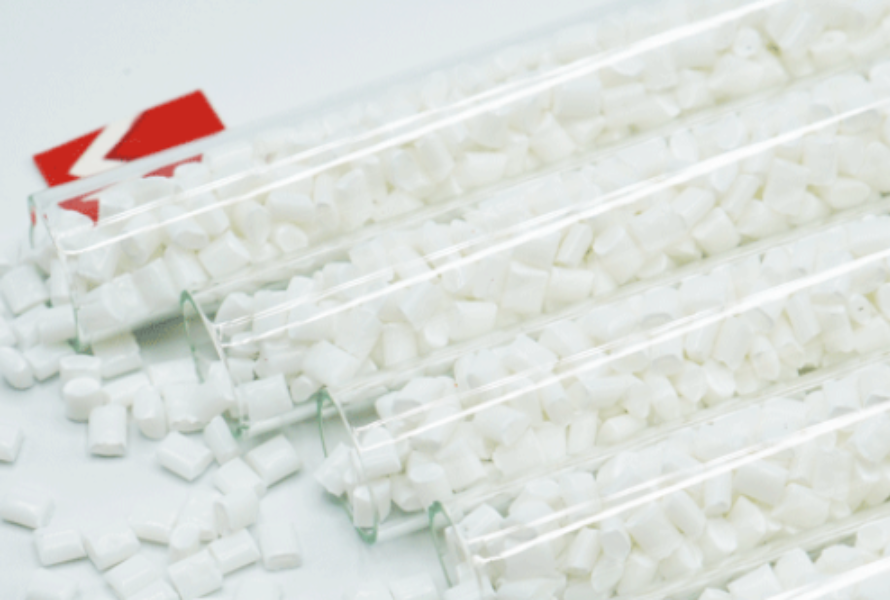
EuroPlas’s PP products include:
- PP flame retardant compound: PP flame retardant compound is a mixture of polypropylene (PP) resin and halogen/non-halogen flame retardant.
- PP conductive compound: PP conductive compound is made of PP resin and carbon black conductive.
- PP BaSO4 compound: PP BaSO4 compound is polypropylene treated with BaSO4 to reduce shrinkage and deformation in high-temperature settings and enhance formability and heat, chemical, and impact resistance.
- PP talc compound: PP talc compound consists of talc powder and appropriate additives such as dispersant and bonding additives according to end-product requirements.
- PP glass bead compound: PP glass bead compound combines PP resin, glass beads, and additives. The glass beads offer transparency, compressive resistance, and thermal stability due to their shape, and can improve the material's mechanical performance under load.
- PP glass fiber compound: PP glass fiber compound is made of PP base resin, glass fiber, and other additives. It gives the final products increased flexural modulus and tensile strength.
4.2. ABS Compound
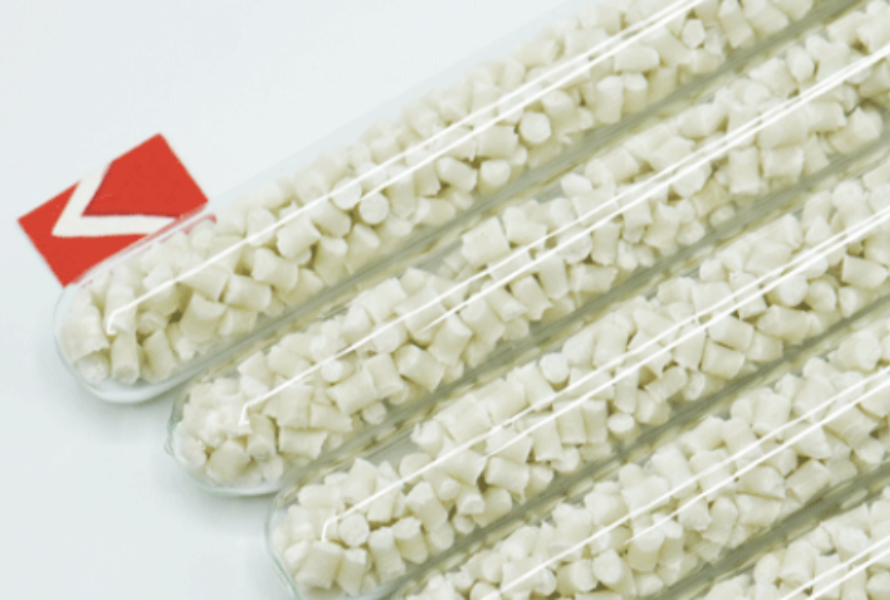
EuroPlas’s ABS products include:
- ABS Glass fiber compound: ABS glass fiber compound is a composite material made by adding glass fiber as a reinforcement to ABS resin. This combination results in a material with improved mechanical properties such as higher strength, stiffness, and dimensional stability.
- ABS Antistatic compound: ABS-antistatic compound is an ABS-based material that dissipates static electricity. It's made by adding antistatic additives to ABS resin, providing conductivity while preserving the resin's mechanical and processing properties.
- ABS flame retardant compound: ABS flame retardant compound is a combination of ABS that has been modified with flame retardant additives to increase its fire resistance.
Contact us right now for more details about these clear plastics.