PEEK is a strong, long-lasting polymer with outstanding workability and processability. Its glass and carbon-reinforced grades are among the hardest polymers at room temperature.
PEEK resin is perfect for a wide range of applications in various industries, including automotive. It's used in running gear, HVAC system, sensors, clutches, brake systems,engine control unit (ECU), and more.
Let's delve into the article to understand why and how this resin is widely chosen for the automotive industry!
Read more: PEEK plastic: Definition and Application
1. How Does PEEK Resin Help In The Automotive Industry?
Automakers are replacing metals with engineered plastics like PEEK to cut emissions and increase fuel economy. According to Grand View Research, with an expected compound annual growth rate (CAGR) of 7.1%, the worldwide automotive PEEK market is forecast to reach $115 million by 2025.
PEEK resin is utilized in high-end automobiles, EVs, and hybrid electric vehicles (HEVs). It enables engineers to combine many parts into integrated designs that minimize weight, part count, and assembly labor.
The resin's unique qualities open a gateway to lighter, more efficient structural parts and power strains. They also allow for more designs that can't be done with metals.
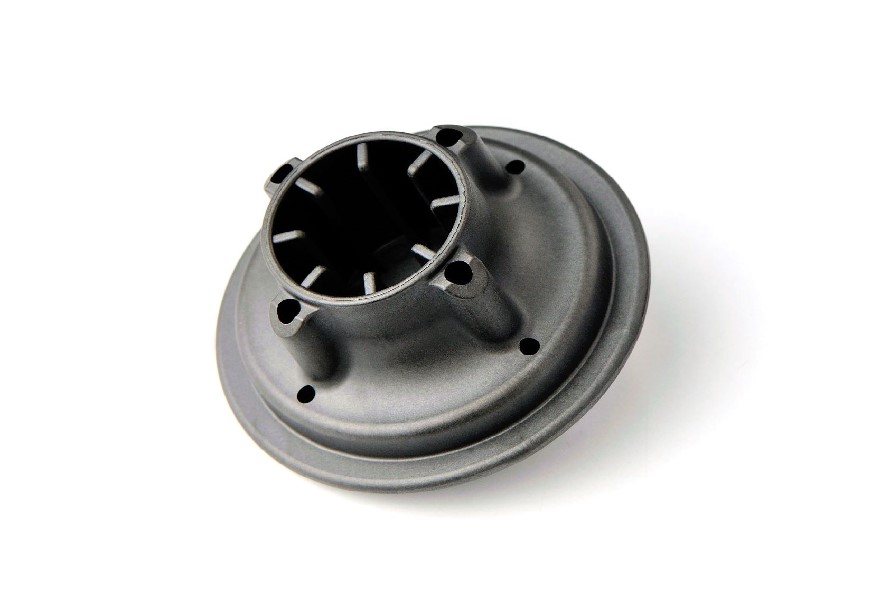
PEEK is an excellent new material option for the automotive sector. It offers great strength, resilience to temperature changes, and resistance to chemicals. It's the ideal material to replace metals in crucial engine and transmission applications.
PEEK resin contributes significantly to the automotive industry. Research reveals that around 50 automotive components are made with this resin. It remarkably helps manufacturers enhance vehicle performance and minimize manufacturing costs. Big automakers such as Mercedes-Benz, BMW, Volkswagen, Volvo, General Motors, Toyota, Chrysler, Renault, and Tesla also use PEEK in their products.
PEEK resin presents in numerous critical automotive details, such as:
- Transmission parts: PEEK can withstand high loads for millions of cycles without losing strength. Thus, it's often used in bearings, clutches, and mechanical links.
- Engine components: The material can endure intense heat and pressure generated by the engines. Its popular applications are wear pads, bushings, seals, gaskets, pumps, and pistons.
- Structural components: PEEK is lighter but offers great durability. Therefore, it's ideal for parts such as cams, gears, suspension arms, and fasteners.
- Electronics details: PEEK provides electrical insulation and environmental protection. It is used in many automotive electronic components, such as control units, sensors, and connection housings.
2. Why Is PEEK Resin Chosen For The Automotive Industry?
PEEK resin offers many benefits to vehicle production and component performance.
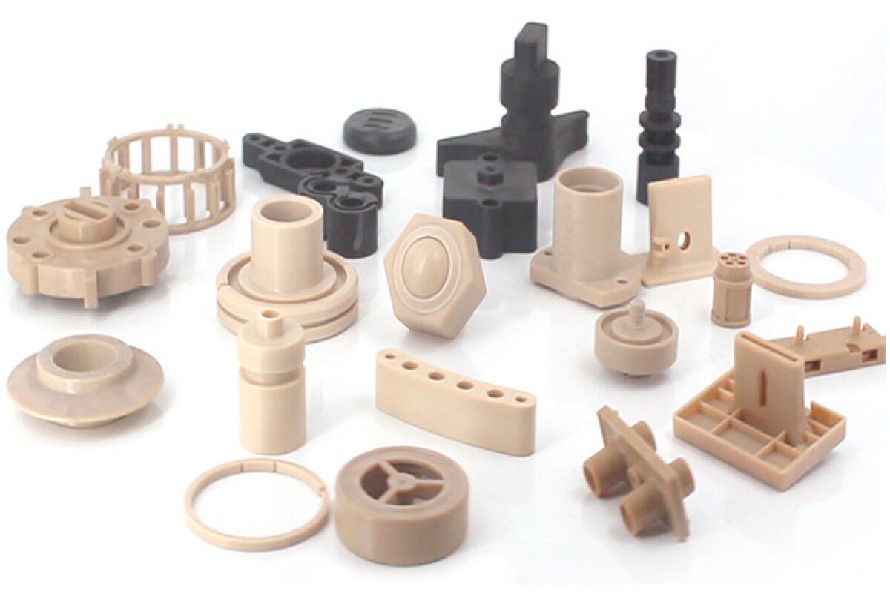
Some of its highlighted advantages are:
- Excellent strength-to-weight ratio
Since PEEK resin has a high strength-to-weight ratio, it can replace heavier metals without compromising structural integrity. Components made from PEEK weigh less than steel or aluminum. Thus, it helps the parts improve its fuel efficiency and meet the emissions standards.
The resin is especially useful for electric cars. It reduces the weight of components, leading to longer battery life.
- Ability to withstand high engine heat
PEEK is a highly heat-resistant plastic that can continuously withstand temperatures up to 250°C. Therefore, it's ideal for engine and transmission components.
Components made from PEEK resin still have outstanding mechanical qualities after being exposed to temperatures exceeding 200°C for an extended period of time. Because PEEK is more heat resistant than other polymers, it may be used in under-the-hood parts where metal isn't appropriate and to ensure engine components can tolerate rising temperatures.
PEEK is a polymer that exhibits exceptional resistance against many automotive and roadside chemicals, including brake fluids, motor oil, coolants, greases, and battery acids. It keeps its structural integrity and surface polish even after being exposed to severe chemicals for hundreds of hours. It ensures a longer service life for fuel system parts, oil pumps, seals, sensors, and gaskets.
- Flexibility in designing and manufacturing
PEEK resin has a special benefit over metal substitutes since it can be molded into intricate shapes and designs. Replacing metal components with PEEK plastic makes the parts lighter and more compact. Its manufacturing flexibility and processability allow for creative part designs that are not achievable with metals. Therefore, it minimizes waste and improves the overall quality of the design.
PEEK's ability to form complicated shapes and resistance to abrasion make it a cost-effective substitute for traditional materials like metals and composites. It requires less maintenance and replacement costs.
3. Conclusion
PEEK resin has many advantages over metals, especially in the production of automotive parts. Its durability and reliability make it a potential material that can transform the automotive industry and propel the advancement of mobility.
4. Explore Engineering Plastic Compounds From EuroPlas
As a leader in the masterbatch industry, EuroPlas offers a wide range of optimal solutions with flexibility, high quality, and all functions in just one material for your business. It allows you to process directly without any material added. The material also can be tailor-made based on the final products' requirements. Our engineering plastic can be used in automobile, electronics manufacturing, interior decoration, and renewable energy.
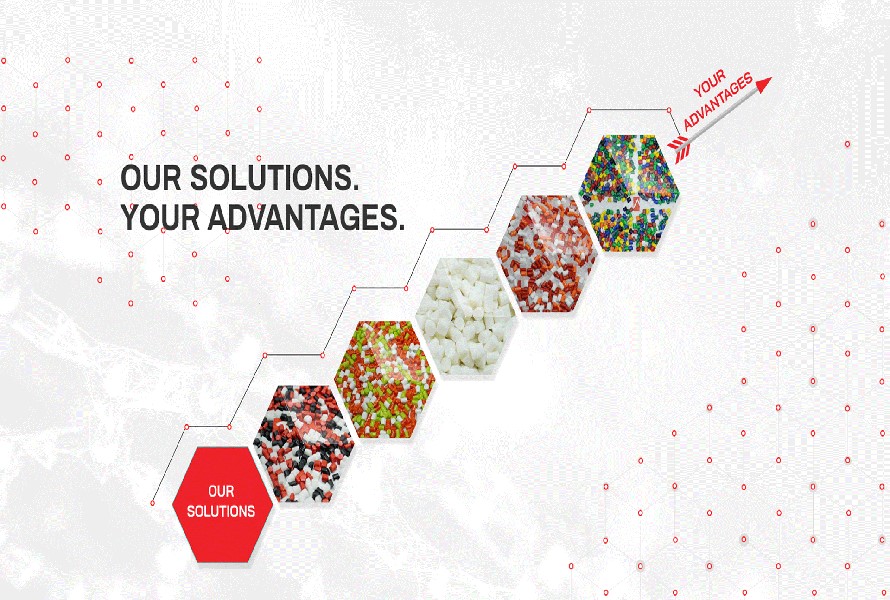
EuroPlas products include PBT GF-FR compound, PA6, PA66 blend compound, PC flame retardant compound, ABS Glass fiber compound, ABS antistatic compound, etc., guaranteeing you high-quality end-products. Here is our list of Engineering Plastic Compounds:
- PBT GF-FR Compound
- PP Engineering Plastic Compounds
- HIPS
- PA (Nylon) engineering plastic compound
- Polycarbonate Engineering Plastic Compound
- ABS Plastic Products
Contact EuroPlas right now for more information on our outstanding products!