PLA, or Polylactic acid, is a popular thermoplastic monomer made from renewable, organic sources such as sugar cane or corn starch. It receives lots of attention from manufacturers and users due to its qualified features and eco-friendly properties.
How is PLA plastic made? This article will cover its production process, analyze its pros and cons, and explain why it's ideal for your sustainable development.
Let's scroll down for more!
1. What is PLA?
PLA, short for Polylactic acid, is derived from any fermentable sugar, such as corn starch, sugarcane, cassava, and sugar beet pulp. Among them, corn is the most popular option as it is one of the cheapest and most available types of sugar worldwide. PLA stands out among other plastic choices with biomass resources as the raw material. It's the second most produced bioplastic (the first place is thermoplastic starch) and resembles the properties of polyethylene (PE), polypropylene (PP), or polystyrene (PS). And the most important thing is that it is biodegradable.
Read more: PLA masterbatch - the future of the plastic industry.
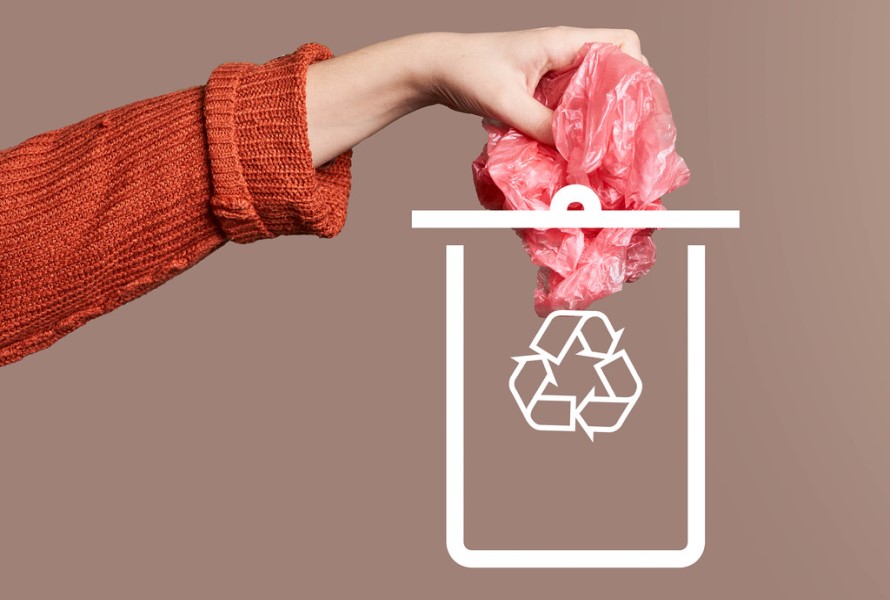
2. How is PLA Plastic Made?
Unlike most plastics made from distilled fossil fuels and polymerized petroleum, PLA uses natural raw materials, such as corn. The material is put through the process of wet milling to isolate and separate the scratch. Then, the manufacturer mixes and heats the starch with enzymes and other chemicals; thus, a type of sugar called dextrose (D-glucose) is released. After that, it is the fermenting process of dextrose to produce lactic acid monomers, which is the main ingredient of polylactic acid.
The next step is to process the lactic acid into PLA material. There are 2 methods. The first one is more common, including condensing the lactic acid into a lactide and then using a polymerization process. This method also adds different catalysts and heat to bind the molecules together. The second way, which is less popular, is to apply the condensation process to the lactic acid directly.
3. PLA Plastic Properties
Density |
1.24 g/cm³ |
Heat Deflection Temperature (HDT) |
126 °F (52 °C) |
Flexural Strength |
80 MPa |
Tensile Strength |
50 MPa |
Shrink Rate |
0.37-0.41% (0.0037-0.0041 in/in) |
Impact Strength (Unnotched) IZOD (J/m) |
96.1 |
UV resistance |
Limited. The material can degrade due to long exposure to sunlight. |
Chemical resistance |
PLA is chemically resistant to some solvents, including alcohol, acetone or isopropyl. |
How strong is PLA plastic? According to the table above, PLA's tensile strength is 50MPa, indicating it's a relatively strong material. Yet, it still has some limitations. For example, it's more brittle than other plastics such as PETG or ABS.
4. PLA Plastic Pros And Cons
4.1. Pros
- PLA is a sustainable bio-based material since it's made from sugar starches.
- PLA has the ideal properties of a thermoplastic to be molded, solidified, and injection molded into various forms and shapes suitable for 3d printing and food packaging.
- The products of PLA are a functional, renewable, and comparable replacement for the use of PET.
- PLA meets the international requirements for biodegradation, meaning a reduced size of the landfills. For example, in an industrial composting facility, it takes only 45–90 days to break down.
- The material is eco-friendly as it emits zero toxic fumes to the environment while being incinerated.
- PLA is FDA-approved, meaning it is safe for food contact.
4.2. Cons
- Relatively low flexural strength
- It's not really heat-resistant
- The material can be more expensive
5. Can PLA Plastic Be Recycled?
In general, the material can be recycled with the condition that it's not mixed with other plastics. The process of recycling PLA can be done in mechanical and chemical ways. Nowadays, only post-industrial PLA scrap is being recycled at an industrial scale.
6. EuroPlas - A Reliable Companion for Your Sustainable Development
EuroPlas is known as a leader in the masterbatch field since the company satisfies a wide range of requirements for unique plastic raw material solutions to optimize production costs and improve the competitiveness of the customers.
Besides, EuroPlas understands the demand for biodegradable plastic for sustainable development and the environment. That's why we've developed a list of high-quality Bioplastic Compounds and Bio Filler to provide our partners with different types of eco-friendly materials.
6.1. BioNext - The Bio Plastic Compound
We have
BioNEXT, a bio compound exclusively developed by EuroPlas. It can be decomposable within 12 months after use, making it a suitable option to save the environment. We guarantee that the end product passes strict quality control management to meet all the requirements. You can use our product in many applications, such as automotive & transport, construction, fibers, electronics, household appliances, and especially food packaging. Here is the list of our available options:
- BiONext 102 and BiONext 152 - the two bio-compounds made of bioplastic and CaCO3. They have high stiffness, high impact strength, and low melt flow index, making them easy to process.
- BiONext 400 - a bio-compound produced based on bioplastic and modified starch powder. It can keep moisture on the surface, resulting in longer food preservation.
- BiONext 500 - a bio-compound based on bioplastic and reinforced CaCO3 powder. It has high stiffness, good elongation, great dispersion, and is easy to process.
- BiONext 600 - a bio-compound based on bioplastic, talc, and other specific additives. It's anti-UV, oxidation, and moisture.
- BiONext 700 - a bio-compound based on bioplastic and specific plasticizers. It can prevent oxidation, thus resulting in longer food preservation.
6.2. Bio Filler
Bio Filler from EuroPlas is a cost-effective material solution for bioplastic products. It's a biodegradable material that improves several properties of end-products, such as stiffness, gloss, etc. It can act as an anti-block and slipping agent in blown film.
- BiOMates 01: It's a mixture of bio-resin, modified CaCO3, and dispersion additives. This biodegradable product can optimize cost for bioplastic end-product processing and play as an anti-blocking and slipping agent for PBAT films.
- BiOMates 02: It's a blend of bio-resin, modified BaSO4, and dispersion additives, helping optimize cost when mixing with several types of bio resins, such as PBAT, PBAT compound, PBAT & PLA blend. It also can increase the film's glossiness.
- BiOMates 03: It combines bio-resin, modified talc, and dispersion additives. It can increase the film glossiness and optimize the cost of bioplastic end-product processing. The product helps produce more transparent film than when using CaCO3. BiOMates 03 also acts as anti-blocking and slipping agents for PBAT films.