LDPE is a common thermoplastic polymer that is well-known for its toughness, flexibility, and resistance to impact and chemicals. LDPE melting point is one of the crucial factors in designing products. This article will provide detailed information on this property and discuss how it affects the products' design and durability.
Let's scroll down for more!
Read more: Temperature ranges for different plastic materials
1. What Is LDPE Melting Point?
LDPE offers low-density and high-flexibility that are perfect for products like shopping bags and plastic films. A Differential Scanning Calorimeter (DSC) can be used to determine the melting temperature of the material. LDPE melting point is from 105 to 115°C, giving it stretchable and moldable properties.
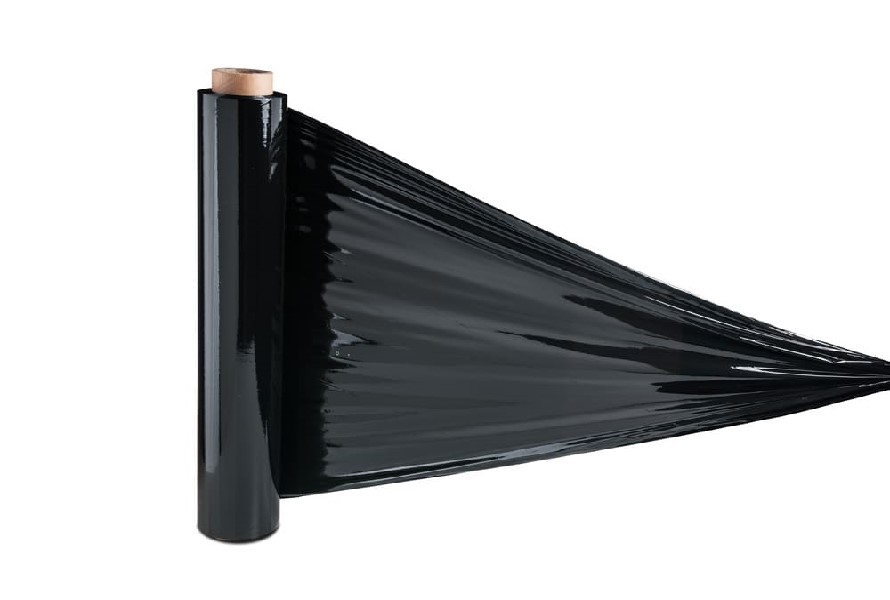
For example, shrink films are made from LDPE, which is heated to almost its melting point—typically approximately 110°C. This procedure generates a tight, safe package for the products.
After that, the film is quickly cooled to stabilize its structure. LDPE film shrinks at temperatures between 90°C and 110°C, forming a snug, protected package.
Read more:
What is LDPE (Low density polyethylene)? Properties & applications
LDPE vs HDPE: Which one is better?
2. How LDPE Melting Point Affects Products
The highly branched structure of LDPE keeps the chains from packing tightly together and reduces crystallinity. This structure also leads to a low LDPE melting point. Here's how it affects the design and durability of products:
2.1. Design
- Design Flexibility: Thanks to the low LDPE melting point, it can be easily molded into thin-walled constructions and complex shapes. Thus, it's a good material for flexible containers with thin gauges and detailed designs, plastic bags, and film wraps.
- Processing Temperatures: A low LDPE melting point helps save energy consumption during manufacturing processes such as blow molding, injection molding, and extrusion.
- Design Constraints: The products' designers should pay attention to the low LDPE melting point to design with limitations to prevent deformation or melting at high temperatures.
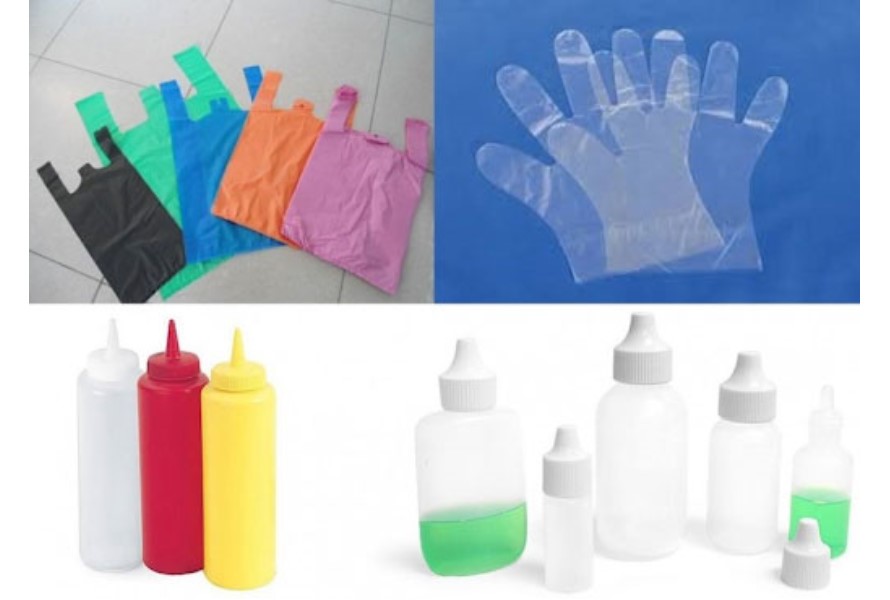
2.2. Durability
- Mechanical Properties: The material's flexibility and toughness enhance its impact resistance. However, the low LDPE melting point may also cause its mechanical qualities to deteriorate more quickly in situations where high temperatures are sustained.
- Temperature Resistance: A low LDPE melting point means low thermal resistance. Therefore, the material might not be ideal for products that can be exposed to high temperatures, such as hot drink containers.
- Environmental Exposure: Even LDPE is resistant to chemicals and moisture; it can oxidize and degrade under UV radiation over time. Thus, it can impair its performance in harsh climatic conditions like heat and sunlight.
Read more: Compare HDPE, MDPE, LDPE, and LLDPE masterbatch
3. Conclusion
The low LDPE melting point might affect the durability and design of products. To guarantee long-term durability and functionality and reduce heat exposure and deformation problems, engineers must take into account the material's thermal constraints and design aspects.
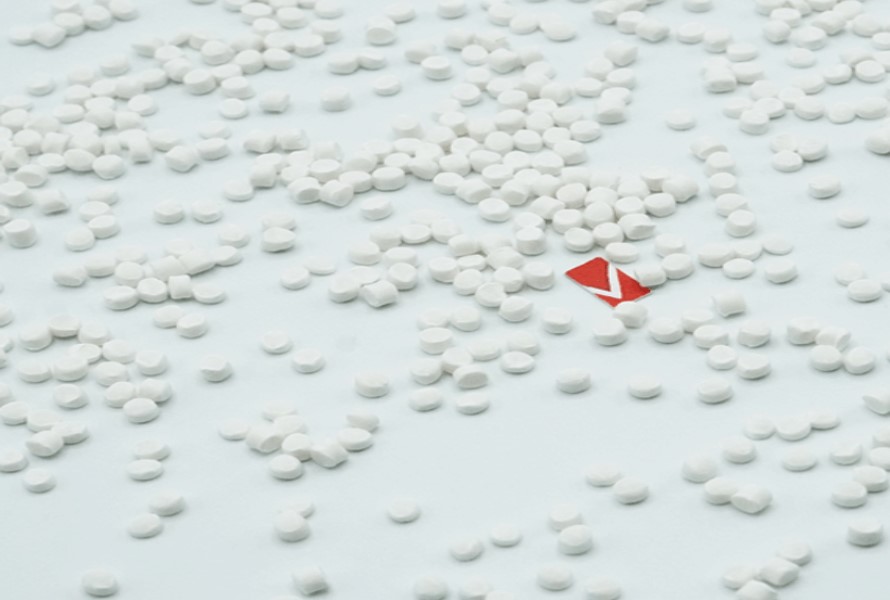
4. About EuroPlas' PE Products
EuroPlas, the world's leading producer and supplier of filler masterbatch, offers a cost-effective solution for plastic manufacturers. Our PE filler masterbatch is a blend of PE resin, CaCO3, and other additives. It provides benefits, including enhanced end-product qualities (brightness and opacity), less shrinkage, and energy savings (due to the heat transmission capacity of CaCO3).
Besides, it improves the stability of the production process. Our product is ideal for injection molding, blown film, shopping bags, T-shirt bags, food packaging, PP woven bags, laminated film, and more.
With 15 years of experience, EuroPlas can provide high-quality, reasonably priced solutions for plastic manufacturers. Don't hesitate to contact us for the best price!