According to a report by Market Research Future, the global masterbatch market is projected to reach a value of $15.81 billion by 2028, with a growth rate of 6.6%. These figures demonstrate that masterbatch is one of the key factors contributing to the growth of the global plastics industry. With the benefits it brings, masterbatch will continue to be widely used in the future. In this article, we will explore the definition, manufacturing process, classification, and applications of masterbatch.
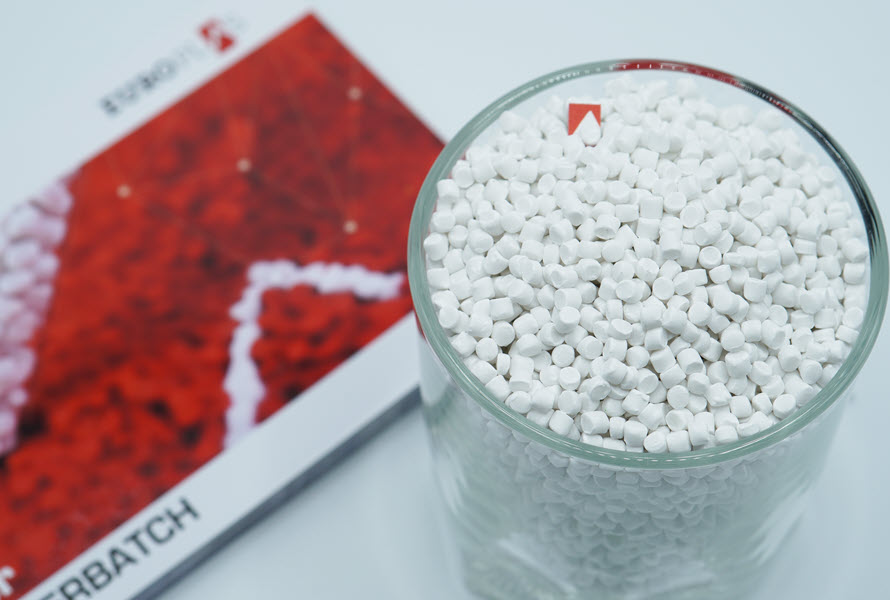
What is masterbatch?
1. What is masterbatch?
Masterbatch, or plastic masterbatch, is concentrated plastic pellets consisting of carrier resin, plastic fillers, colorant for plastic, and other additives. The word “masterbatch” means the main mixture.
Masterbatch is applied in plastic manufacturing for 3 main purposes:
- Reducing the amount of required resin
- Coloring plastic products
- Enhancing functional properties to plastic products
Based on these functions, masterbatches are divided into 3 major categories: color masterbatch, additive masterbatch, and filler masterbatch.
In general, production of masterbatch include 3 steps as follows:
Step 1: Creating a custom formula
Masterbatch manufacturers will identify and weigh the proportion of resin, pigments, additives,... The formula depends on the types of masterbatch they want to produce.
Step 2: Mixing and heating
Afterward, all materials will be mixed together by being heated and melted. The equipment for this process is typically twin screw extruding.
Step 3: Cooling and forming
The materials in the form of molten liquid will be cooled down and cut into small granules.
2. Types of masterbatch
2.1. Color masterbatch
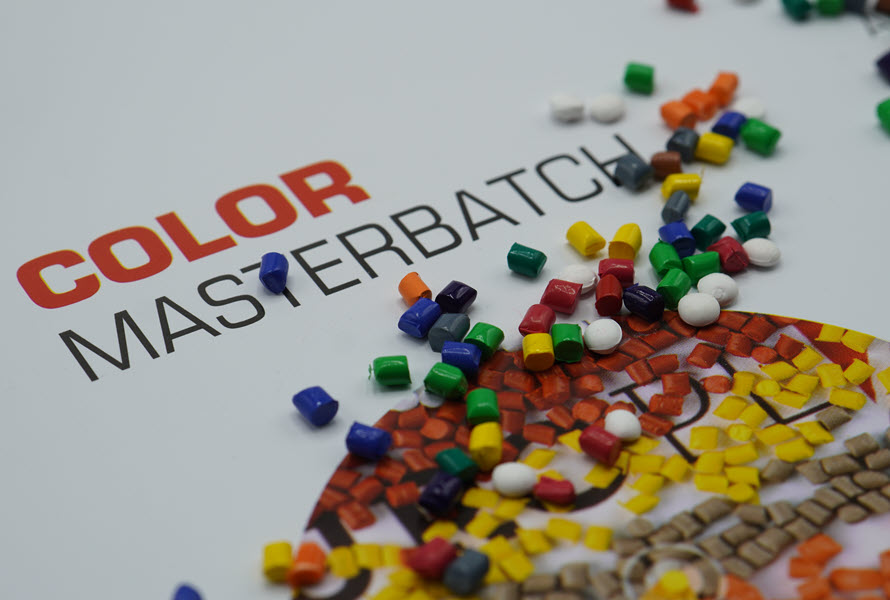
Color masterbatch
Color masterbatch (also known as color concentrates), is plastic concentrated pellets used for the purpose of coloring plastic products.
Typically, there are two main components in color masterbatch that are the colorants and the polymer-specific carrier resin. Other than that, some special formula also contains processing additives such as zinc, oil, wax, etc., and/or fillers.
Color masterbatch is widely used in nearly every aspect of life with a broad range of applications. It creates a colorful and eye-catching appearance for finished products, thus helping them cover the aesthetic requirements.
Step 1: To produce color masterbatch, the manufacturers first mixe industrial pigment, base resin, and other additives according to the well-investigated formula.
Step 2: The compound then will be mixed by a mixer at high speed for about 10 minutes. Afterward, it will be passed through the extruder and be poured into a sheet.
Step 3: Finally, manufacturers will cool the compound, and then pass it through a cutter to cut into masterbatch particles.
The finished color masterbatch is then mixed with primary plastic granules and other additives into a mixture of plastic materials. This mixture will undergo different processing technologies depending on the product shape that customers require (injection molding, extrusion, blowing film ...).
2.2. Additive masterbatch
Additive masterbatch is a combination of organic or inorganic compounds which are added into plastic to enhance specific properties or functionalities for plastic products.
Back to the old day, plastic products are mainly produced from a few basic raw materials. It was not until the advent of plastic additives that add many features like anti-aging, flame retardant, anti-fog, and anti-UV to the base materials. These components meet almost all the finished product requirements.
3. Filler masterbatch
3.1 What is filler masterbatch?
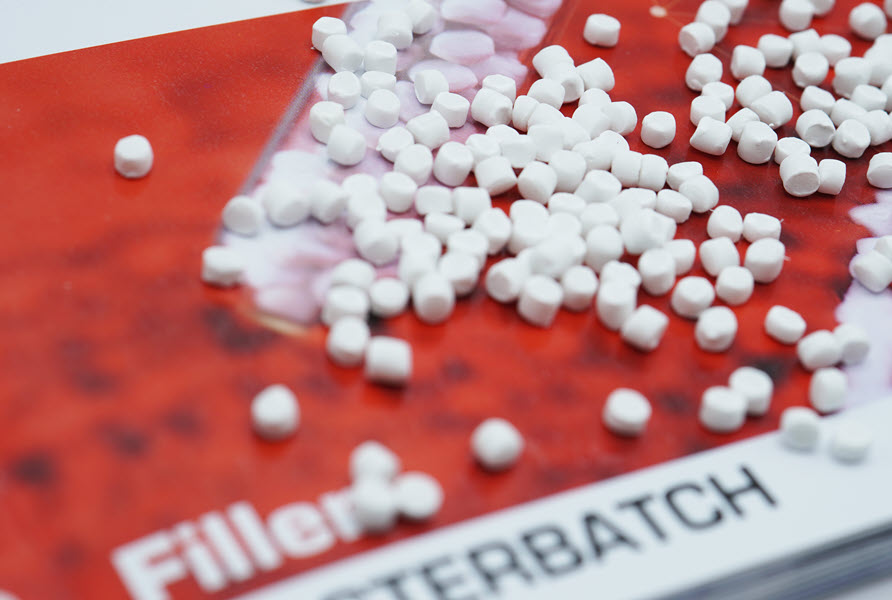
Filler masterbatch is the combination of mineral (CaCO3, NaSO4, BaSO4, Talc,...), carrier resin and other special additives in accordance with customer’s demand.
Filler masterbatch are particles added to plastic production to cut cost as well as supporting in enhancing some properties of end-products. Plastic filler materials are divided into two groups:
- The inorganic (also known as mineral) fillers such as calcium carbonate (limestone), magnesium silicates (talc), calcium sulfate, mica, calcium silicate, barium sulfate and kaolin (China clay).
- The organic plastic fillers such as tree bark flour, nut flours, chicken feathers, and rice hulls.
Normally, the inorganic filler materials are more prefered in industrial production as their simple molecular composition makes them more easily to be processed.
The production of filler masterbatch includes 4 steps:
Step 1: Mineral filler (CaCO3, NaSO4, BaSO4, Talc,...), additives and plastic resin are mixed together by high-speed mixer.
Step 2: The mixture is completely melted at high temperature.
Step 3: That mixture is then cooled and put into a screw extruder, pushed forward and pressed into the mold.
Step 4: The output of the extruder is cut into similar small pieces. They are filler masterbatch applied into plastic manufacture.
3. Applications of masterbatch
Thanks to its tremendous benefits, masterbatch has become an indispensable component in many plastic processing methods.
3.1. Blown film and lamination
Blown film is one of the most popular plastic manufacturing methods worldwide. As it offers end-products great uniform properties regarding the length and width and specifically preferred in the packaging industry.
Filler masterbatch is used in the blown film technology to improve rigidity, control heat, enhance turbidity, and cut down production costs and is a more prominently used technology in the packaging industry.
Besides, blocking in blown film is most frequently phenomenon in polyethylene and polypropylene film processing. Therefore, plastic manufacturers tend to use slip and antiblock masterbatch to address this problem.
3.2. PP raffia/Yarn
Another application of filler masterbatch is PP raffia/yarm. Polypropylene yarn, also known as PP yarn and polyp yarn, is widely acknowledged as the lightest and most practical yarn used in the textile industry.
The sanitary nature of polypropylene yarn prevents allergic responses. The breathing structure expel moisture produced by sweat and other similar sources; it does not retain moisture or water and does not contain dirt or stains.
In terms of returning to nature and reusability, it is also in a better position than many other yarn types.
At the necessary ratios, it is a kind of yarn that can also be given exceptional strength properties. It has qualities like strong durability and unbreakability that were obtained through manufacturing applications.
Due to its technical qualities, it is not only the most popular yarn type for narrow weaving but is also utilized in a variety of other industries, including the production of household textiles, socks, and carpet.
3.3. PP non-woven fabric
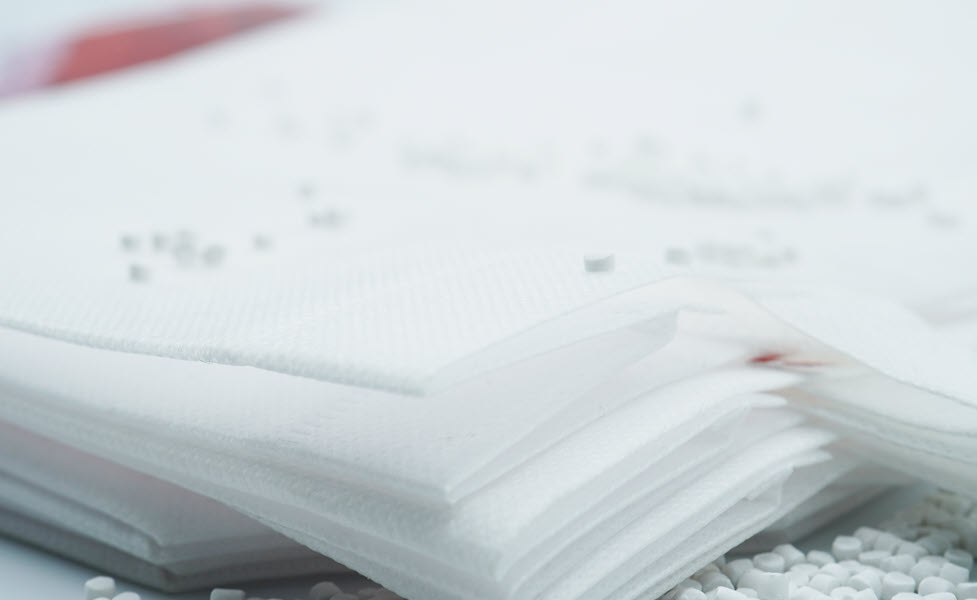
As the name speaks for itself, non-woven fabric is a type of fabric produced without weaving or knitting. With a view to optimizing the production of nonwoven, calcium carbonate filler has been taken into use. Being made of calcium carbonate powder (CaCO3), plastic resins, and other specific additives, calcium carbonate filler is one of the most effective material solutions for nonwoven manufacturing. The application of this material offers end-products several benefits:
- Cost reduction
- Properties enhancement
- Productivity improvement
- Environmental friendliness
3.4. Polyester and Nylon yarn
Polyster yarn
Polyester yarn is a type of synthetic yarn that is frequently marketed as acrylic or novelty yarn. While acrylic yarns are often machine washable, affordable, warm, and robust, they also have a tendency to pill and don't have the same level of breathability as natural fibers. Novelty yarns come in a variety of odd textures, such as faux fur-like yarns and ladder or ribbon yarns with sequins or spangles woven right into the fiber.
When knitters and other fiber artists are allergic to animal fiber, polyester yarn is sometimes used as a replacement for wool due to its warmth and durability. Additionally, it is frequently used to knit household items and garments for infants and children, both of which call for regular washing.
Nylon yarn
Nylon yarn is a synthetic material that may be designed to have the appearance and texture of many different natural fibers. When silk became harder to come by, nylon was initially developed as a replacement. In comparison to natural fiber strands, nylon is robust, somewhat elastic, and typically less expensive. For novice knitters, it could be a suitable material option because it is typically simple to work with.
Yarns made from natural fibers, like wool, may be highly costly. This is particularly true if the yarn is organic and needs to be imported. It may be used to make a variety of clothes, accessories, and even home décor items in place of these natural fiber yarns.
Numerous strands may protrude from one base thread in certain nylon yarn that is intended to resemble fur. It could take longer to master this kind of yarn than others and be more challenging to work with. Locally, knitting lessons are typically given, and books and websites that teach knitting patterns and techniques are also accessible.
3.5. Extrusion
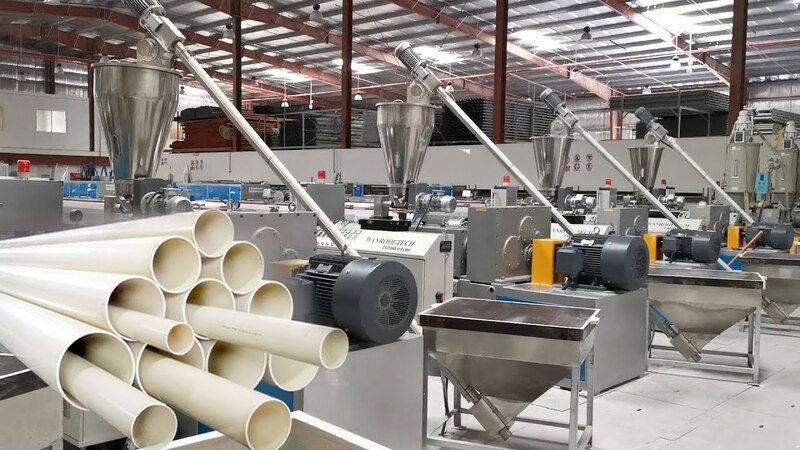
Extrusion is also used for the manufacturing of plastic components for electronic gadgets and is one of the important techniques in filler masterbatch manufacturing. The process is used to manufacture bulk volumes of desired product and as a result has a high demand for manufacturing appliance components and packaging. The application of extrusion technology improves the rigidity and bearing capacity of finished products such as PVC pipes, straws, and gutters.
3.6. Injection molding
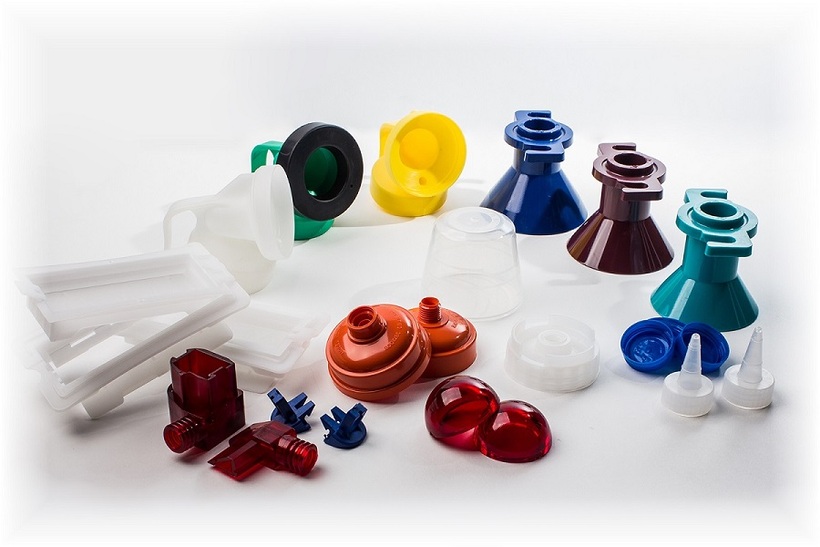
Injection molding offers certain advantages for filler masterbatch. Some of them are:
- The manufacturing lead time decreases due to good thermal conductivity of CaCO3
- It offers increased stability during the product forming process
- It saves energy due to a decrease in manufacturing lead time
3.7. Thermoforming
Basically, thermoforming is a general term that refers to the process of transforming a plastic sheet into a 3-dimensional shape by using heat, vacuum, and pressure.
The use of filler masterbatch in thermoforming offers end-products several advantages.
- Cost reduction: calcium carbonate filler which has a cheap price partly replaces virgin resins.
- Properties enhancement: By adding filler masterbatch in thermoforming, end-products are equipped with better mechanical properties such as tear resistance, anti-friction and anti-slipping property, dimensional stability, rigidity, impact strength and printability.
- Productivity improvement: CaCO3 is a good thermal conductive. Therefore, using filler masterbatch in thermoforming reduces processing temperature and shortens the products cycle, thus saving energy consumption as well as increasing productivity.
Environmental friendliness: compared to fossil resin, which releases a great amount of carbon footprint during its manufacturing process, the production of filler masterbatch is far more environmentally friendly.
4. EuroPlas - The world's largest filler masterbatch manufacturer
European Plastic Company (EuroPlas) is the world's largest filler masterbatch manufacturer headquartered in Vietnam. EuroPlas filler masterbatch products are quality-tested products that have satisfied thousands of customers in more than 85 countries around the world. This product is a cost-effective solution and helps you enhance many of the properties of the final product such as brightness, opacity and reduced shrinkage.
If you would like to know more details about our filler masterbatch product in particular, as well as our other masterbatches, please
fill out this form or contact us via email/phone number. We are happy to answer all your product questions and concerns!